Polish YouTuber WorkshopFromScratch finally got fed up with tripping over piles of garden detritus and decided to have a go at building a woodchipper (Video, embedded below). Since they had a ‘small’ 1.5kW gearmotor just lying idle (as you do) it was an obvious fit for a machine that needs torque rather than supersonic speed. The video is a fabulous 20-minute journey through the workshop showing just about every conceivable metalworking tool being used at some point.
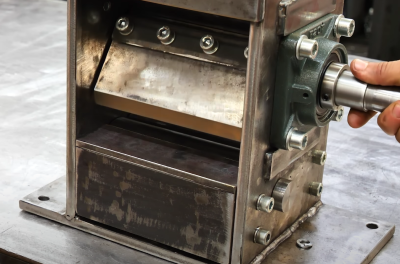
One interesting point is the bottom roller, which sits between a pair of removable guides, which should help the thing self-feed without jamming. Whether that was necessary is not for us to judge, but it can’t hurt. The frame looks like it was constructed from at least 1/4″ thick steel, which is expensive if you don’t happen to have a supply to hand. There’s lots to see, everything from thin sheet metalworking, which was plasma cut, constructing the feed and exhaust guides, to box sections being skilfully welded at some interesting angles to make a cart to move the thing. They tell us the blades were constructed from some seriously thick slabs of C45 grade steel, but currently are not hardened. This is planned for the future, but we suspect not something that is easily achieved in the home workshop!
If this channel is familiar, then you might remember the earlier stump grinder they built. If you are drowning in sawdust, but have a log burner, then you’ll appreciate this sawdust briquette machine.
All you need to make $300 machine is a $10000 workshop 🤡
you could do that? really?
And $1000 of parts and materials
Boom!
A woodchipper with no serial numbers and no paper trail? Only murderers who want to surreptitiously get rid of bodies would use such a thing! I hope congress soon passes legislation to ban ghost chippers like this one.
Don’t worry. Only the parts with a serial number need to be registered. And by themselves they are completely safe.
I suppose you could then 3D print the other parts that hold everything together…
Whaddaya mean with Pervertly save?
Haven’t you ever seen a malicious serial number lurking around in the deep of the night?
Smart killers use pigs. You can’t eat a woodchipper when you’re done with it.
Well, that’s where the wood chipper chipper comes into play!
haha squared
Alright Brick Top?
Cuppa tea?
Not so smart using pigs as body disposers. They will devour everything bar teeth which will identify the victim.
Haven’t you ever seen Snatched, everyone who saw it, knows you have to pull the teeth, nails and shave the hair before feeding bodies to pigs.
The hog of the forsaken got no reason to cry.
Got to chew the angels falling from on high
Professional machine shops outsource their heat treatment.
It’s a specialty and at the highest levels, involves crazy dangerous things (molten cyanide salt baths!)
He’s going to want to get those blades hardened and tempered ASAP. Wood is amazingly abrasive.
In the end, he will buy better edge hardened and ground cutters.
Either cuss himself for using an odd size or call himself a genius for using an available one.
That’s assuming he’s got enough wood to justify his own chipper.
This will work great if he’s only got one accomplice to get rid of. Might need to feed the head in pieces.
I’ve heard that replaceable carbide cutters is the way to go for planers, the same might be true here? Or is this more about crushing and ripping?
These are more impact driven which is better for high speed steel. Also, steel is easier to sharpen with common equipment. Usually a chipper knife eventually gets killed by a rock or embedded metal before they wear out. Steel allow you to sharpen out of a few hits where carbide shatters. We are not looking for surface finish here so toughness outweights sharpness life. Steel actually gets sharper than carbide but loses that edge faster. Chipper blades do not have a razor edge because they could not hold them long. They are blunter than you would want a finish planer blade for toughness.
IIRC cyanide is just for the carburizing salt baths; aka those which screw with your composition by adding carbon. Admittedly that’s better than the kinds which are oxidizing and screw with your composition by removing carbon.
Using homemade knives as an example of a steel blade where the heat treatment is critical, even quite advanced powder metallurgy steels can be heat treated in a home shop with minimal equipment and no dangerous chemicals. You have to take a high temperature oven through a sequence of temperatures for a sequence of times, so a computerized one is generally chosen. I’ve seen “quenching” done with blocks of aluminum and compressed air as well as with oil. Some steels encourage you to perform a cryogenic treatment afterwards but it’s usually optional. Those steels described as tool steels seem to generally have simpler heat treatment processes than the ones intended for knife blades.
Point is, I think you can reasonably harden a few things at home. Is there something about these which can’t work as well?
Hardening is easy, tempering back is hard. As you say, computer controlled temperature and slope, not many degrees below initial hardening temperature.
There are people who can eyeball the temp, there are many more who think they can eyeball the temp.
I think the professionally heat treated versions of such blades have a final edge hardening. Which is tricky. Inductive spot heater etc.
You might even find some with welded on edge’s. Those might not be for wood chippers, rather plastic spru re-grinders.
Not even touching the sharpening. My experience with such blades is with plastic though. Small business, you end up doing everything.
I don’t do it myself, but the knifemakers often just use a toaster oven with a good thermostat for tempering. To get a harder edge than the rest of the steel, they often just differentially harden and/or temper the edge compared to the rest. One version of that is to insulate all except the edge in clay before quenching, which obviously changes the cooling rates and can be quite visible on the blade. (see “hamon”) Or, though they aren’t welding on edges, they sometimes make a blade sandwich where the center steel is harder than the side steels given the same heat treatment. (see “san mai”)
The sorts of things you can do at home may not scale, but they address some of the same problems as some of the professional solutions.
Great execution, not my favorite design. The commercial versions I’ve used set the chip size with a back stop plate then grind away at the branch with standard planing blades, using the weight of the motor and spindle to first lift up on to the branch then eating down slowly. Which given his build style would have been very do able.
Exactly this, normally a big flywheel disk with lots of momentum holds the blades. Much less likely to experience a dead stop jam up.
I own a commercial wood chipper and have a couple thoughts.
1. They use a heavy flywheel and a certifugal clutch. That design also saves the engine/motor from impact loads because it is belt driven. The centrifugal clutch also allows the flywheel to overrun or underrun the engine a bit. Better to slip the clutch than over torque the engine crank. The sprocket and chain transfer more shock loads to the motor. Like 300 lb flywheel on mine with a 25 hp motor and thats the small end of commercial machines. Momentum is what they are looking for here. Then you dont need a very grunty motor. Mine works a lot like a meat slicer in that the wheel is perpendicular to the feed and the blades slice the pices just like a food processor disk.
2. Just buy some chipper blades, they are steel not carbide (easy to sharpen and they are looking for impact toughness that carbide is not so good at). The blades are cheaper than you could make them and heat treat them. Last time I bought a set of three knives they were like $100 dollars and can be sharpened at least 10 times before replacement.
But does it have the torque to pull in an average sized person and reduce them to a pile of easily transportable pulp? If not, I’m not interested.
Well just make some kind of a guard so that young college students don’t just jump in. You wouldn’t want to have a real doozie of a day.
Yeah, you don’t want kids hugging them selves head first into a wood chipper :D
Only room for their feet and legs in the feeder.
Feet first requires commitment, or a little help.
IIRC cyanide is just for the carburizing salt baths; aka those which screw with your composition by adding carbon. Admittedly that’s better than the kinds which are oxidizing and screw with your composition by removing carbon.
Using homemade knives as an example of a steel blade where the heat treatment is critical, even quite advanced powder metallurgy steels can be heat treated in a home shop with minimal equipment and no dangerous chemicals. You have to take a high temperature oven through a sequence of temperatures for a sequence of times, so a computerized one is generally chosen. I’ve seen “quenching” done with blocks of aluminum and compressed air as well as with oil. Some steels encourage you to perform a cryogenic treatment afterwards but it’s usually optional. Those steels described as tool steels seem to generally have simpler heat treatment processes than the ones intended for knife blades.
Point is, I think you can reasonably harden a few things at home. Is there something about these which can’t work as well?
comment glitch!
I like the low speed high torque aspect of the thing – much quieter.
This shouts
“Honey have you cleaned up the yard yet?” “Don’t worry, I’m working on it”
to me. Ha!
Please update your last will and testament and take out some liability insurance for when those inadequate bearings/cases fail and your chipper head inadvertently flys out and kills or maims you or an innocent bystander. Chipping wood has high dynamic loads and harmonics that sucker will give you a bad surprise one day soon.