A common saying is that every disaster is caused by a chain of events, some of which can stretch back by years. Airplane disasters and near-disasters are no exception here, with all too often a small mechanical issue worsening until suddenly everything goes south. In the best case the flight crew is still able to work through the problems and figure out a way to put the aircraft down on firm soil in a single piece. This was the situation that the crew of Qantas Flight 32 (QF32) found themselves forced to deal with, as detailed in a recent article by [Kyra Dempsey], aka [Admiral Cloudberg].
When QF32 started its flight from London Heathrow in early November of 2010, everything seemed normal, but a mere four minutes after take-off from a layover at Singapore on its way to its final destination of Sydney, the #2 engine on the left wing of the Airbus A380 essentially exploded, launching shrapnel through the wing and fuselage. Although the A380 has four engines (numbered 1-4 from the left wing tip) and normally a single engine failure is not a major deal, the loss of systems that got destroyed in the explosion left the crew scrambling to diagnose the damage and implement a solution.
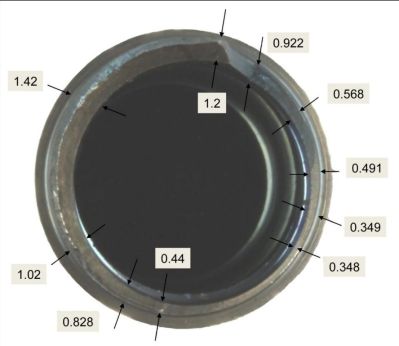
Fortunately, the shrapnel had not done too much damage. The flight crew was able to stabilize the aircraft and circle back to Singapore for a successful emergency landing. When the ATSB (Australian Transport Safety Bureau) examined the destroyed #2 engine, they traced the fault back to a single lubrication oil feed line for bearings inside the engine that had sprung a leak (full ATSB report). The leaking oil auto-ignited, destroying seals that let hot turbine gas in where it didn’t belong. The gas made quick work of cutting through parts of the engine, which resulted in the turbine spinning out of control until a disc shattered into many, very fast-traveling pieces of shrapnel.
As for why the oil leak occurred? The wall thickness of the oil pipe was very irregular, with a fatigue crack coinciding with the thinnest wall section. The pressurized oil had exploited this weakness and in the process very nearly turned QF32 into a TWA-800 or Alaska Airlines Flight 261 level disaster. During the subsequent inspection of all other Rolls-Royce Trent 900 engines, a number were found to also have a similar flaw in the same piece of pipe. The pipes were quickly replaced.
It’s a really good article – like it!
One intriguing bit about the animation is the use of non-metric measurements applied to an engine designed by a British company (Rolls Royce) that only uses metric measurements. This means that the spec for the engine thrust was converted from Newtons to imperial and then the imperial measurements were redacted to obscure their origins.
In fact, of course, if we go to the Wikipedia page for the Trent 800, we find that the thrust is given in kN first (413.4kN) and then imperial measurements second, in brackets.
https://en.wikipedia.org/wiki/Rolls-Royce_Trent_800
I guess the question is, what’s the need to redact metric? Is it a big problem to include both, so that 100% of the world’s population can understand the topic instead of just 4%?
Totally agree! Although to be honest, it’s 4.23% as of July 2023
https://www.worldometers.info/world-population/us-population/#:~:text=the%20United%20States%202023%20population,(and%20dependencies)%20by%20population.
Seems the rejection of the imperial system in December 1773, at Boston, was a bit half-hearted!
I still think USA should have finished their migration to metric. They were among the first to push for it over a century ago and yet we’re the biggest country in the world still not using metric exclusively.
I’m so tired of having 2 sets of tools.
Plenty of other countries can understand imperial measurements as well as metric. Generally the UK and (ex)Commonwealth countries grow up learning both. Our measuring tapes have metric down one edge, and imperial down the other, and a socket set will include both imperial and metric sockets.
I’m happy with both, but if I have to do any maths I’ll convert everything to metric and then calculate.
I guess there is always a risk of people looking at the wrong number and assuming the wrong unit. If you black all numbers out you can eliminate this risk.
Because that’s their intended audience.
You might as well complain why they aren’t speaking in Mandarin Chinese since there’s more people who speak Chinese as their first language than there are those who speak US English.
Sure, but inevitably, US English videos reach a global audience, because such a high proportion of people use English as a first or second language: e.g. the Anglosphere (obviously), Europe, Africa, India, Pakistan..
I just found it a bit odd that they used imperial for that but called out temperatures in centigrade.
Aviation has a crazy mix of units even to Americans. i.e. wind in knots, temperature in Centigrade, pressure in inches of Mercury. There is no sense in complaining about it, we’re all pretty much equally confused at the start of flight training.
Most of the aviation units make perfect sense.
Temperature in C, of course. And speeds in nautical miles (i.e. knots), as that is tied to the circumference of the earth.
Altitude in feet can be argued both ways, but ultimately it’s just a number assignment and change for the sake of change doesn’t buy much in this department.
The only thing that stands out as truly anachronistic is the inches of Mercury for air pressure. Or the PSI readings on some gauges.
And there are of course those manufacturers who still use inch-pound units when they specify their parts. Though for them it’s often a legacy problem, as they are using stuff that was originally certified back in the dark ages, and doing a units conversion is simply not economically feasible.
Another example of why aviation is accurately described as hours and hours of boredom, interspersed with brief moments of stark terror.
“Fortunately, the shrapnel had not done too much damage.“
Dig into the Australian report it’s an interesting read.
A cannon ball sized chunk of the rotor punched through the wing spar.
They all are very lucky to be alive.
The oil tube was the root cause. It started a fire the cut through the tie shaft connecting the compressor section to the turbine section. The turbine section overspeed caused a rotor to fail.
RR made a software change to catch a shaft failure in the future.
Is Esmiol your real name?
Quite rare and linked to a pelicular region in France…
Yes couldn’t believe that statement. Obviously little research done. I found the article very light weight.
Have you read the book written by the pilot? It is an excellent read for anyone interested in aviation. As is the ATSB Report.
If it wasn’t for the fact that the flight crew just happened to be the A Team on the A380 at the time plus had two check captains on board for routine checks plus an outstanding CSM who kept everyone calm, they would have ended up in the ocean. It was an outstanding example of CRM practice, particularly in a dire situation and is held up as one of the finest examples of airmanship ever.
Oh, and the fuselage WAS penetrated but the lower altitude meant the passenger cabin was not compromised and it was a miracle that no one was injured when shrapnel peppered the fuselage. However,many systems were put out of action.
I flew on that aircraft one week prior to this incident and remain super thankful for the timing.
They got lucky. If any of the broken fans pieces went through the fuselage, the plane was cut in two and it was game over.
While fuselage penetration is possible and has happened, the nacelle casing around the fan is typically wrapped in a thick sleeve of anti-penetration materials including Kevlar, and subjected to ‘blade liberation’ tests, to reduce that likelihood to a vanishingly small value. A single blade, if it can escape its webbing, would punch a clean hole through the walls, seats, floors, cabling, hydraulics, or people in its path for sure, but still not “cut in two” the whole plane. Redundant A/B routing of the critical wiring and hydraulics lines also minimize the chances of critical losses there.
Meh, they would have lost cabin pressure when there is a hole in the fuselage, but it does not have to be more catastrophic then that. Of course depending on what other stuff gets damaged.
Do you still remember Aloha Flight 243?
Yes, that’s a good example of explosive decompression damage.
https://en.wikipedia.org/wiki/United_Airlines_Flight_232 would be a good example of turbine destroying three critical hydraulic systems.
I believe the harrier has or had a tricky time with the lift fan. Losing a fan blade in one direction would leave the pilot feeling a bit ill. One of those single point of failure type accidents.
no? that’s just nonsense
I’m intrigued how they cut that thin-walled pipe so cleanly that they could measure it like that. Any ideas? Water jet?
Probably a precision metallography abrasive saw. Very common in the world of metallographic examination, less so outside of that.
water jet, lapidary saw, wire edm: I can think of a bunch of ways to cut really nice cross sections. They can also cut and polish. But this might be the face of the broken pipe, unmodified. It looks to me like it might be threaded and the differences in thickness may be a function of the thread depth as it spirals around the pipe, although if that were the case I would expect they’d say so.
Probably looked a bit like this: https://www.youtube.com/watch?v=KHU7PBIezB0
The engine case is supposed to contain most…problems.
So the question is: why were these pipes manufactured so poorly? Their wall thicknesses are not only too thin, but very clearly lopsided. I can’t imagine any machinist looking at that and thinking it could possible be ok. Is it possible these are counterfeit parts that made their way into the supply chain?
It’s possible.
https://www.bloomberg.com/news/features/2023-10-11/fake-parts-found-on-boeing-airbus-jets-plague-airlines
This explains the conflaguration of american measuring systems extremely well. For those who don’t understand I will include the obligatory SARC;) https://www.youtube.com/watch?v=JYqfVE-fykk
It’s been left out of the articles and comments so far, but this story is one of the key stories told in chapter 6 of “The Perfectionists” by Simon Winchester (https://www.amazon.com/Perfectionists-Precision-Engineers-Created-Modern-ebook/dp/B072BFJB3Z/), which I originally learned about from a “Books Every Engineer Should Read” article on here. An excellent book which I can highly recommend.