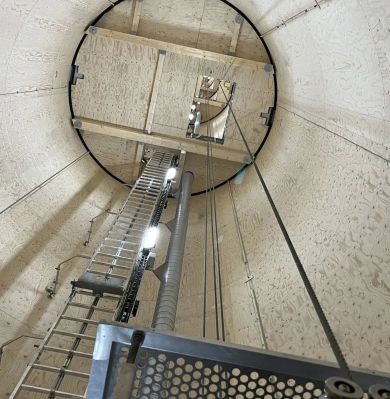
Modern-day wind turbines are constructed using mostly concrete and steel, topped by the fiberglass composite blades mounted to the nacelle that houses the gearbox and generator, along with much of the control systems. With the ever increasing sizes of these turbines transporting the components to the installation location is a harrowing task, something which Swedish company Modvion claims to improve upon with its wooden tower elements that come mostly packaged flat, for on-site assembly. The BBC recently took a look at the first of these partially wooden wind turbine towers. At 105 meters tall, it features a standard V90-2.0MW turbine and blades.
Rather than using concrete slabs at the base with steel tower segments on top, or a fully steel tower like with most wind turbines, Modvion uses segments of layered wood which it calls ‘the module‘. These are assembled out of 144 layers of 3 mm thick spruce, with ring segments assembled on-site. This means that multiple of these modules can be stacked onto a standard truck with no concerns that come with oversized transports. According to Modvion these wooden towers should last about the same number of years as their steel counterparts.
Where some of the claims made by Modvion fall somewhat flat is that it solves the whole wind turbine transport problem, as their solution does not fix the most daunting issue of transporting wind turbine blades. They also claim that using wood instead of steel makes their wind turbine tower section ‘carbon negative’ due to capturing carbon in the wood, with the same wood ‘reusable’ after decommissioning by reusing it for buildings. This would reduce wind power’s already small carbon footprint.
The issue here is of course that the steel in most wind turbine towers can be almost fully recycled and reused, whether to make new wind turbine towers or something else. Melting steel can also be done using zero-carbon energy sources, with the world’s steel industries gradually shifting to such ‘green steel’. Although Modvion seems very upbeat about the prospects of their wooden towers, it remains to be seen whether it doesn’t turn into another Spruce Goose.
Papier maché
From an engineering perspective, no. Not only is that a completely different material, but functionally it has no where near the engineering properties of what they are describing which seems legitimate.
The largest wooden building in the world houses a statue of The Buddha in Nara, Japan and is almost 1300 years old. It’s almost entirely just solid hardwood, and over 160 ft tall. If you ever get a chance to go and check it out, I highly recommend it. Studied part of the scuplture there for my Japanese degree a long time ago.
Wood, when engineered correctly, is perfectly capable of lasting a long time. The question is, if their wood is toxic…
Thank you for your reply (sincerely).
I was just being flippant.
Np, I figured. I’ve always wondered if you get tired of typing out your name..it’s even longer than mine. I used to just go by Drew but someone started using that.
Prime example how to do over correction properly…
I’d suggest that actually the two materials could be very similar, once you make them to similar thicknesses – both are layers of long plant fibres, probably in varied orientations bonded together with a glue. And at the thinnest end the toddlers art project might well be vastly superior to a zero ply plywood…
Many variables that can change how the two compare though – how deep does the glue penetrate, does the wood used have longer wider fibre meshes or much stronger fibres in the mix, just which glue did you use? etc…
The highest wooden habitable structure is the HAUT skyscraper in Amsterdam at 73m (or 269ft in freedom units): https://nl.m.wikipedia.org/wiki/HAUT
There are higher wooden structures but these are mainly lattice towers.
waht aboiut this fella
https://www.fs.usda.gov/inside-fs/delivering-mission/apply/worlds-tallest-timber-building-opens
I find it hard to believe this wood is actually just “wood”.
I used to work with an engineered wood composite that was used for the interior form of transformer substation coils, made of a European Red oak reinforced material called lignostone, which was primarily fortified with phenolic resin in different concentrations. The dust from that stuff is cancerous.
I looked into their page to see what the stuff is actually made out of, and they seem to suggest just normal wood glue but they never state outright what holds the stuff together. Lignostone is it proprietary material made by one company, and it’s not exactly easy to recycle that stuff.
I would be very hesitant to think this stuff is made with normal glues…
Most likely the structure is like glass fiber but instead of a glass fiber mat and epoxy, you have some kind of a cellulose mat and PVA. The PVA glue will be the bulk of the material.
PVA or “normal wood glue”, polyvinyl acetate, is a synthetic plastic made out of fossil fuels. It can be made out of (bio) ethanol with some difficulty, so it’s more commonly made out of ethylene gas separated from natural gas.
Thanks for this insight. After working with that stuff I mentioned which looked exactly like plywood, I have like a permanent paranoia about any kind of engineered wood now.
The stuff I mentioned does however make an incredible workbench, since it’s designed to soak up a special oil inside the transformers that’s like pure cancer oil, it sucks up oil and grease nicely. As long as I don’t cut it it’s safe. Expensive stuff though, The bench I made from it that’s like two inch thick was an offcut that the shop gave to me and couldn’t sell.
There’s a really good blog called Transmaterials I used to follow, that would go into a lot of exotic engineered building materials like glass filled concrete block you could see through, bioengineered building materials and stuff like that. https://transmaterial.net/
No. It’s a laminate. It’s in the article. Wood, glue, wood, glue, repeat.
Now imagine the carbon bonus if you make nuclear reactors out of wood.
Genetically engineered plants that grow into large buildings, forming various materials with various micro structures, self reparable. The control machinery is living, self regenerative wetware. Just drop the fuel rods at the entrance, and pick the slightly radioactive ashes.
Flatpack design? From Sweden? Gasp!
Article forgot to mention the model… it’s a Schmarkflgargenflul.
I might have too many vowels, though.
And not nearly enough diacritics ;)
Vindkraftverksträtorn?
(‘Wind turbine wood tower’ in Swedish)
I know; I found that a delicious coincidence too. Wonder if they ship out with a happy wordless line-art one-sheet assembly guide.
This will do wonders for the price of plywood. Maybe invest in glue?
A real trick would be to genetically engineer bamboo to grow into a 100M tower.
Even though forest regeneration may well provide sufficient “additional” raw materials, the jury is out regarding the long-tern effect on biodiversity. To contemplate such usage during a time of global temperature increases and changing climate seems irresponsible, IMO.
https://www.ncbi.nlm.nih.gov/pmc/articles/PMC7067718/
…. or plant some of those giant redwoods in windy locations to make ‘living’ wind turbines.
“A real trick would be to genetically engineer bamboo to grow into a 100M tower.”
And that’s how you get Triffids! 😱
Here I was thinking they solved the actual problem of fiberglass blades, not created another one… Now there’s resin packed wood for the main structure instead of easily recycled steel. Ah well, ACCELERATE
cement for the bottom 1/3 of the tower and steel for the top 2/3 is a good combo imo, the cement section acts as a damp proof course, though i have seen cracks everywhere in a prototype tower. I would hope that the turbines would be built in such a way as the mechanical components could be refurbished when worn out.
I have seen the towers being transported on a trailer, and they take up little space, the widest sections at the bottom are made in two halves and the steel sections are much narrower due to being closer to the top, so they are the full circle.
a towers environmental impact would be greatly reduced if its life could be extended to 50 or one hundred years, but i understand that designs change and that may not be economical. the future may be one without neodymium magnets for instance.
Cement or concrete is practically un-recycleable. Given that wind turbines are commonly abandoned after the subsidy term runs out and the turbine becomes non-profitable to maintain, it also becomes a logistics problem to break it apart and carry it away to landfill after 12-15 years.
Last time I checked the concrete I have seen degrading seems to be breaking down into sand and rocks and returning to where it came from. Seems like a pretty complete cycle to me. Also, wood seems to rot into dirt and releases its CO2. Steel seems to rust away to oxides. Seems like nature has figured out recycling pretty well.
Oh and by the way, around here concrete gets broken up to become aggregate in new concrete. Every concrete company around accepts broken concrete for free or even pays for it.
I’d be curious about the glue they are using.
It seems like you can turn basically anything with some tensile strength into a pretty decent composite; as long as you don’t mind the result being mostly epoxy resin. Useful if you really need a composite; but not really a triumph of natural materials or even especially sustainable vs. metal parts.
If they are getting good performance out of wood with better-behaved glues, though, things become a lot more interesting in that regard.
> but not really a triumph of natural materials
Like “transparent wood”, which is 80% plastic and 20% bleached cellulose fiber.
So that when they burn down they burn down completely. 🤦
The stats on how many of these units fail catastrophically before the end of their planned lifespan is alarming.
I would point out that a company has already figured out how to recycle fiberglass, it’s just cheaper to not do it.
Using wood is not carbon negative. If it was cutting down the rainforests and making lumber of it would be carbon negative as well. You cant have it both ways. The tree took in the carbon and made wood. Eventually that wood will degrade and return the carbon. What you do with the wood in the meantime only delays that. Manufacturing and working with lumber uses energy just as steel production does. I thought environmentalists thought loggers were evil, are they now heroes? I can’t keep track of what we are told to support or not support at this point ;)
A composite structure is a fiber impregnated with a binder. The aerospace industry will be shocked to find out that wood composite propellers are an advancement now. I guess anything supposedly green can get funded now.
Cutting down a tree in itself is something you would have to do for a healthy forest anyway and carbon wise still works out in the right direction as long as you don’t just straight up burn the wood and it was cut down as part of forest management not deforesting – The forest now its thinned has more healthy young fast growing carbon sinks and a more mixed healthier ecology and whatever that cut down tree is used for (including just leaving it on the forest floor for the insects etc) will hold carbon for a significant time with much of its carbon remaining captive even after the tree itself is gone – everything that broke down the tree didn’t just turn it all into CO2 again, lots of it becomes part of some other lifecycle more long term and eventually might well end up stored ‘permanently’ as part of the soil etc and if it was used in construction of something for people that wood quite possibly lasts century in service, or gets dumped in a landfill when its service is done – where it might even end up so buried it doesn’t break down further.
So your Loggers probably are ‘evil’ – as that term generally seems to be used now only to imply deforesting to a mass scale of ecological vandalism for profit and then probably not even trying to create a sustainable forest for their kids/grandkids, instead turning that now flat land into something else for even more short term profit… But a well managed forest can provide a great deal of wood in the processes of remaining a healthy ecosystem and sinking carbon – the sustainable forests won’t sink carbon as quickly as a newly restored forest, not even close, but they do hold a great deal and continue to sink some carbon.
And the advancement here isn’t the concept of wood composites, its the scale of this structure and the load it has to take that is the impressive part – in the same way the ever growing blades of a windturbine are not made in new novel materials but have been a steady advancement…
NB I’m not sold this is actually a good idea yet, as steel is proven and enduring in the elements and we know how to keep it protected for century with a little maintenance. So for a wind turbine that is already of minimal carbon impact switching to wood to make it better is quite a risk. However if these tubes do stand the test of time well enough…
By the way, next week I am going to invent carbon fiber composites which are lighter and capture even more carbon than wood. I hear that they can make propellers too. As soon as someone talks about “carbon capture”, my bullometer peaks.