Our metallurgical history is a little bit like a game of Rock, Paper, Scissors, only without the paper; we’re always looking for something hard enough to cut whatever the current hardest metal is. We started with copper, the first metal to be mined and refined. But then we needed something to cut copper, so we ended up with alloys like bronze, which demanded harder metals like iron, and eventually this arms race of cutting led us to steel, the king of metals.
But even a king needs someone to keep him in check, and while steel can be used to make tools hard enough to cut itself, there’s something even better for the job: tungsten, or more specifically tungsten carbide. We produced almost 120,000 tonnes of tungsten in 2022, much of which was directed to the manufacture of tungsten carbide tooling. Tungsten has the highest melting point known, 3,422 °C, and is an extremely dense, hard, and tough metal. Its properties make it an indispensible industrial metal, and it’s next up in our “Mining and Refining” series.
Build a Mountain, Make Some Tungsten
Tungsten is a rare metal, making up only a fraction of a percent of the Earth’s crust, about 1.25 parts per million. It has never been found in its elemental form in nature; instead, it appears as several mineral-bearing ores. The physical and chemical properties of tungsten, which make it such a useful metal, also ensure that the formation of these ores is limited to geologies where tremendous heat and pressure are exerted, such as where sections of continental crust collide to build mountain ranges. These orogenic belts, located mainly around the Pacific basin but also across the Alpine-Himalayan belt that stretches from southern Spain to Indonesia, are the main source of tungsten ore.
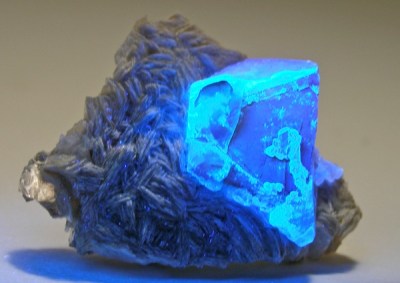
The two main ores of tungsten are scheelite, which is calcium tungstate (CaWO4), and wolframite, which is a combination of iron tungstate (FeWO4) and manganese tungstate (MnWO4). About 70% of the world’s tungsten reserve of 3.2 million tonnes is locked up in wolframite, which is often found in granitic formations and is often associated with quartz. Scheelite is also often found in quartz veins and tends to be found along with commercially important amounts of tin, as well as sometimes with gold. Both tungstate minerals also tend to be found near molybdenate minerals, making molybdenum another valuable byproduct of tungsten mining.
Scheelite, or rather the calcium tungstate crystals within the ore, have interesting properties that make them valuable aside from being a source of tungsten. Calcium tungstate is a scintillator, which means it will fluoresce at a specific wavelength when excited by ionizing radiation, such as X-rays. This made the material very valuable for manufacturing intensifying screens, which were used with traditional film-based radiography to reduce the dose of radiation received by the patient. Large crystals of calcium tungstate, which can be produced synthetically using the Czochralski process, have also been used as scintillators in nuclear medicine procedures.
Mining Up
Because of the relative rarity of tungsten ores and the geological processes that tend to sequester it, a lot of overburden has to be removed to gain access. Open-pit mining techniques are often used, at least when exploiting a new find, but once the ratio of waste to payable ore gets too high, underground mining becomes favored, since it allows miners to work along ore veins and ignore the waste rock that encases them. Because tungsten ores are associated with mountain-building geology, many underground tungsten mining operations actually mine up into the core of mountains rather than down. This was the case with the Pine Creek Mine in the Sierra Nevada mountains outside Bishop, California, where miners had a 3,000′ elevator ride up from the mine entrance to work the scheelite veins. That one mine produced most of the tungsten used in the United States for nearly 60 years before closing in 2001.
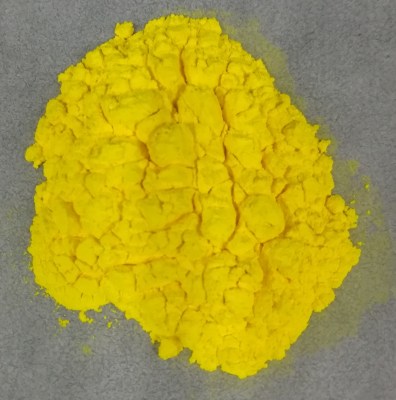
Because the amount of tungsten in either ore is so low — a tonne of tungsten ore contains only about four kilograms of either scheelite or wolframite — tungsten mines have to concentrate it considerably before it can be refined. This beneficiation is usually performed right at the mine site, starting with the usual crushing and grinding steps. Jaw crushers and ball mills turn the ore into a fine powder, which is classified by a series of sieves to achieve the correct grain size. The powdered ore is then transferred to a digester, where hot sodium hydroxide reacts with the tungstate minerals to form sodium tungstate, liberating it from the gangue, or waste rock.
The liquid sodium tungstate then moves on to a series of purification steps using a combination of hydrometallurgical processes. The exact steps taken depend on the source ore and tungsten concentration, but include filtration, extraction with organic solvents like decanol or even kerosene, or precipitation with salt solutions such as calcium chloride. The goal is to form increasing pure solutions that can be treated with hot hydrochloric acid to form tungstic acid, a hydrated form of tungsten trioxide (WO3). Tungstic acid, a vibrant yellow compound that was once used as a fabric dye, is washed repeatedly until as pure as possible before being dissolved with ammonium hydroxide. This solution is filtered and then heated, driving off the ammonia and water to leave behind ammonium paratungstate (APT), a salt with a complex chemical formula:
APT, a free-flowing white crystalline salt, is convenient to handle and contains a lot of tungsten — twelve atoms per molecule. APT is the main raw material produced at most tungsten mines, and is generally shipped out to refineries for further processing into metallic tungsten and fabrication of metal products, such as wire, sheet stock, and billets, not to mention the all-important tungsten carbides.
The first step in releasing metallic tungsten is to decompose APT into various tungsten oxides using high temperatures:
Tungsten oxide is then heated in a reducing atmosphere of hydrogen gas to form elemental tungsten:
Depending on the requirements for the finished metal, the tungsten oxide is sometimes doped with silicon, aluminum, or potassium before undergoing reduction. Reduction is performed in refractory vessels called boats, which are usually made of Monel, in tube furnaces called pusher furnaces. The tubes are filled with hydrogen gas and heated to about 850 °C, which reduces the oxide powder for about 20 minutes.
The resulting fine powder of metallic tungsten is washed, dried, and sifted before going to ingot production, or consolidation. Here the powdered metal is placed in thick-walled molds and put into a hydraulic press, which forms the metal into an ingot. The ingot is referred to as “green” at this point and needs to be handled carefully so it doesn’t break apart during sintering, a two-step process where the ingot is first heated to 650 °C in a furnace, then up to 3,000 °C by passing an electric current through it in a water-cooled tube filled with hydrogen. The result is a solid ingot of tungsten, ready to be worked into products.
Hot and Hard
Even though the age of the vacuum tube is long gone and the world has largely turned away from incandescent lighting, tungsten wire is still an important end product. A single ingot of tungsten can be drawn into almost 1,300 kilometers of wire, depending on the gauge. The drawing process starts with hot-rolling the ingot into a cylindrical shape and swaging to reduce its diameter. One end of the tungsten rod is tapered by dipping it into molten potassium nitrate, which dissolves the rod enough for it to fit into a die. Up to 50 passes through smaller and smaller dies, the smallest of which are made from diamond, may be required to get the wire to the proper size.
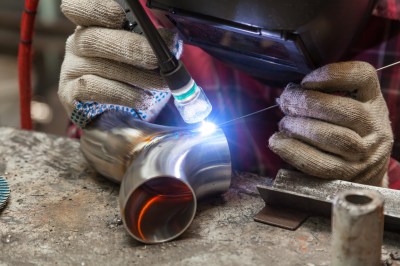
Another important industrial use for tungsten is welding electrodes. The high melting point of tungsten makes it perfect for TIG welding — the “T” is for tungsten, after all — which uses a high electric current to create a super hot plasma that melts the base metal and filler. Tungsten electrodes may look like pieces of thick wire, but they’re actually formed in much the same way as tungsten ingots are. Powdered tungsten is mixed with various additives, especially rare earth oxides like lanthanum and thorium, before being pressed and sintered into solid rods. The rare earth oxides serve to reduce the energy needed to remove electrons from the electrode, which makes it easier to strike an arc and makes the electrode last longer.
The toughness and high melting point of tungsten also make it suitable for cutting tools, especially in the form of tungsten carbide (WC). Tungsten carbide is made either by reacting powdered tungsten metal with graphite at high temperatures, or by blowing a mixture of hot carbon monoxide and carbon dioxide through a bed of tungsten trioxide. Either way, the tungsten and carbon bind to each other, creating a material that’s twice as stiff and twice as dense as steel, with a melting point of about 2,800 °C. Tungsten carbide can be mixed with various binders and additives and pressed into complex shapes that can be sintered into solid cutting tools tough enough to withstand the punishing requirements of CNC cutting.
Also used in (now) old light bulbs https://en.wikipedia.org/wiki/Incandescent_light_bulb
“Even though the age of the vacuum tube is long gone and the world has largely turned away from incandescent lighting, tungsten wire is still an important end product.”
Indeed.
Of course, it’s a bit less than perfectly accurate when we say incandescents have been discontinued – mainly what was discontinued was standard screw-in bulbs. Halogen lamps are just an incandescent that can run at a higher temperature without burning out too soon, and is therefore a bit more efficient. And we still have plain non-halogen filament bulbs in automotive use, or for heat, or in other carve-outs that weren’t discontinued. They’re cheap, and the efficiency doesn’t matter as much in other uses.
My mothers home town has a wolframium mine that was very active during WW2. The demand fell after the war and the mine was closed
Very nice.
The melting point of carbon is 3642 °C.
My date could take the heat.
I think my comment disappeared, but anyway – Carbon sublimates at that temperature rather than melting, unless you put it under very high pressure. Tungsten filaments at the same (incandescent bulb) temperatures last longer than carbon, especially with the benefit of a bit of inert gas or in a halogen bulb.
“world’s tungsten reserve of 3.2 million tonnes” and “We produced almost 120,000 tonnes of tungsten in 2022”. So that means we only have less than 27 years to go before exhausting tungsten reserve ???
Correct, same with oil. There is a major economic factor in that nobody wants to fund discovering more of a mineral that is still relatively cheap
Golden metal resources a British company has a new large discovery in Nevada.
Is the largest undeveloped resource in the USA
> miners had a 3,000′ elevator ride up from the mine entrance
It took me a while to understand that. IMO “3,000 feet” would be much easier for those coming from metric world. (I assume that metric hacker can handle feet and pounds just fine, it’s just the unusual notation that’s confusing.)
There’s no winning with local notations without getting very inconvenient. Sometimes I see numbers given like 100,234 instead of 100.234 and have to figure out whether they meant a hundred or a hundred thousand. Or if the word is a billion, is it a thousand million or is it more? Even with numbers like 1.00234E5 there’s always the chance that it gets garbled by text formatting or mistyped and misinterpreted.
1′ is standard notation for 1 foot.
1″ is standard notation for 1 inch.
I realize not everyone in a metric county will have encountered this notation, but it is used in every place I just looked.
Engineering books
Carpentry plans
Building plans
Old electronic board layouts
Repair manuals
Maps
SAE tools are also labeled with this notation.
11/32″ wrench
20′ tape measure
The labels on the tape also use this notation
Even the dumb decimal imperial stuff like 0.032″ drill bits
(as Graham Chapman) “Toongsten carbide drills? What the bloody ‘ell’s toongsten carbide drills?”
Fascinating article. The video at the end showing how tungsten carbide inserts are made was great, also.
I’ve used thousands of those inserts, and seeing the automated process was so enlightening. Well done! :-)
The obvious solution is for the U.S. to say goodbye to their SAE fractional inch units and embrace metric like literally the rest of the entire world has! Lol