For as much capacity lithium-ion batteries have, their useful lifespan is generally measured in the hundreds of cycles. This degradation is caused by the electrodes themselves degrading, including the graphite anode in certain battery configurations fracturing. For a few years it’s been known that pulsed current (PC) charging can prevent much of this damage compared to constant current (CC) charging. The mechanism behind this was the subject of a recent research article by [Jia Guo] and colleagues as published in Advanced Energy Materials.
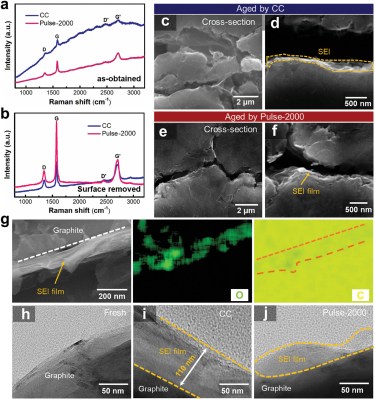
The authors examined the damage to the electrodes after multiple CC and PC cycles using Raman and X-ray absorption spectroscopy along with lifecycle measurements for CC and PC charging at 100 Hz (Pulse-100) and 2 kHz (Pulse-2000). Matching the results from the lifecycle measurements, the electrodes in the Pulse-2000 sample were in a much better state, indicating that the mechanical stress from pulse current charging is far less than that from constant current charging. A higher frequency with the PC shows increased improvements, though as noted by the authors, it’s not known yet at which frequencies diminishing returns will be observed.
The use of PC vs CC is not a new thing, with the state-of-the-art in electric vehicle battery charging technology being covered in a 2020 review article by [Xinrong Huang] and colleagues as published in Energies. A big question with the many different EV PC charging modes is what the optimum charging method is to maximize the useful lifespan of the battery pack. This also applies to lithium-metal batteries, with a 2017 research article by [Zi Li] and colleagues in Science Advances providing a molecular basis for how PC charging suppresses the formation of dendrites .
What this demonstrates quite well is that the battery chemistry itself is an important part, but the way that the cells are charged and discharged can be just as influential, with the 2 kHz PC charging in the research by [Jia Guo] and colleagues demonstrating a doubling of its cycle life over CC charging. Considering the amount of Li-ion batteries being installed in everything from smartphones and toys to cars, having these last double as long would be very beneficial.
Thanks to [Thomas Yoon] for the tip.
This reminds me a little bit of https://www.rctalk.com/dyna-pro-digital-discharger/
PC also works on lead acid. Really extends the battery’s life.
Also helps break up sulfation and can restore batteries that won’t charge with normal chargers. I’ve got an Optimate 4+ that I’ve had for a long time and the amount of batteries it’s brought back to life is crazy.
So why don’t all chargers do this? Seems relatively easy to implement.
>>”So why don’t all chargers do this? Seems relatively easy to implement”
The manufacturers of your battery operated devices want you to replace them as soon as possible. They’re constantly pushing towards non-repairability and more frequent replacement. They don’t even care about the environmental costs of those practices, never mind caring about your convenience or your bank account.
They want the lifespan of your batteries to be shorter, not longer, so it seems likely that pulsed charging will have to be legislated if it’s ever to be the norm in consumer devices.
+1 – yep, planned obsolescence. It’s why the glue them in.. My prev mobile phone lasted through three entire batteries (which were easy to replace) of very hard use, the new one is going to be a perfectly good phone when it’s very hard to change battery quits…
Thought that doesn’t explain why most of the 18650 charges there aren’t using Pulse-2000, nor does it explain why charges for solar batteries aren’t either..
If this research is right (and widely excepted) it does indeed seem insane for charges not to be doing it…
planned obsolescence paranoia bs. The reason why it´s not implemented is very pragmatic: dumb charging circuits are cheaper. The planned obsolescence is 99% a myth.
Depending of course what device, cost isnt always the reason. Changing from the trusted and tried often is.
For example why doesnt car manufacturen X dothis? Well they have this charger already that works. Then this new research pops up so they wanna see if that holds true first.
I mean, one of the big Hurdles of EV adoption is the battery degradation fear. Takong that fear away surely is something people want?
So manufacturers want devices to last as long as possible? Come on, stop lying. Designing for a target lifespan is literally planned obsolescence.
planned obsolescence is not paranoia – it is a well established and documented business practice, for decades.
And moving it to the battery component has also been well documented.
Everything from your electric toothbrush to your mobile phone – invariably the first thing to go is the battery, that has been designed to be hard to replace..
If cars were the same you’d have to buy a new one when the battery died. Wait a second, that IS what we are moving to!
However, I agree with some of the comments re they already have a working charger, so why change as they don’t have the expense of changing a battery, the customer does.
But we have know pulses work well on lead acid batteries for quite a few decades, which is why you can get charges that do that for them. It seems silly that the default for lithium wasn’t the same from day 1..
Between ‘planned obsolescence’ and ‘future proofing’, planned obsolescence is better.
Future proofing is spending too much money today on the hope that an expensive new tech will be the winner in a few years. Just buy the winning tech in a few years, when it’s cheap.
Everything manufactured has a design lifespan. Everything. Even old things that have outlived that lifespan. Steel rusts about a thou/year under most conditions. Swiss watches don’t last forever. Springs have lifespans.
Have you looked into the history of lightbulbs?
The Romans over engineered many of their buildings and they have lasted long after their empire fell apart. Future proofing electronic devices and over engineering makes them more expensive and heavier, and usually isn’t appreciated by a significantly large enough of the market to make it worthwhile. Look at Instantpots. Once everyone had one that wanted one, how many more could they sell?
Yes, the incandescent light bulb manufacturers managed to make bright bulbs that broke their filaments within a tight window. Light bulbs that last longer consume more watts per lumen.
Probably a matter of keeping EMI emissions down. Charging pulses make a lot of RF noise and on most commerical products that are digital based, it’s a struggle to keep emissions below agency requirements even without charging noise being generated. Notice how many devices with larger batteries have a charger with an inline ferrite.
Spread spectrum frequencies can resolve the RF issues a lot.
“The manufacturers of your battery operated devices want you to replace them as soon as possible. ”
Grand collusion by every maker and user of lithium-ion batteries. Lead-acid couldn’t get away with it.
Universities exist and not all necessarily participate in the evil manufacturer conspiracies.
Universities thrive on grant money from manufacturers.
My alma mater gets most of its money from selling degrees to rich foreign kids.
That would make sense if battery chargers were made by battery manufacturers, but that’s hardly the case. Battery charger manufacturers stand to gain from innovations in charging strategy successes, which is why most automatic battery chargers for lead-acid, for example, include a desulfation mode, which oddly enough they usually don’t mention. But the “your battery will get more of a performance boost with my charger than with others” is probably the prevailing strategy. If they do the above, then adding the strategy in this article makes sense too. Perhaps it’s not well known or established enough, or perhaps it’s already bring implemented but hasn’t become mainstream yet 🤔
The problem is that for most devices using lithium-ion batteries, the charger and battery are both integrated into the device, or at the very least are made by the same company (e.g. cordless tool batteries), and the device manufacturer has no interest in a battery that lasts forever. For example, people usually “upgrade” their phone when the battery dies. Those sales would be lost or delayed if the battery lasted twice as long. Now if the 18650 had become the next AA, this would never have happened of course, but that ship has sailed.
Hear!Hear!
lacrosse bc-700 do this for decade
Because chargers are often made simple and cheap? It’s not necessary to cry planned obsolescence when cost cutting is enough. Often they don’t even build the charger to let you choose to charge at less than the maximum possible rate unless they are made for multiple types of battery/cell and know that the maximum rate would be too much for some batteries/cells that are going to go into it. If it was the charger in an EV, it would monitor lots of stuff including temperature, but for a $2 18650 cell in a $10 charger, you’re getting CC-CV and you’re thankful if you can choose what the constant current value is.
Oppo phone corporation which owns OnePlus, Realme, Oppo and Vivo phones use SuperVOOC/DashCharge/SuperDart charging system that uses pulse current charging and few other tricks to pump loads of power into battery while also providing 800 to 1600 charge cycles. Funniest or saddest thing is that people STILL buy new device because they are bored from using their currently owned phone.
So … You Take a normal CC charger and chop IT Up with a 2 kHz and 50% dutycycle PWM? Wouldnt that result in to Low a voltage? Or would the charger Just crank up the voltage to meet the needed current?
They take the batteries up to full charge. They have a choice of doubling the charge time or doubling the instantaneous current; I think the first citation doubled the charge time. Both methods should be tested in the same experiment to compare the effects that may come from temperature and other factors.
Oops, looks like I’m wrong. They doubled the instantaneous current.
People always yelling about how pwm chargers damaged their calls, but in the end its actually batter than cc?
Are you sure you’re not talking about PWM solar charge controllers? The PWM there has nothing to do with how a li-ion cell is charged.
But PWM could be the next item to study. Is 50/50 the optimal or perhaps some other ratio.
This was kind of what I was thinking about: a lot of chargers are switching buck regulators, and maybe removing the output capacitance that is there to reduce output ripple, would result in pulse charging that’s less expensive than a stock CC charger, although that’s going to be a varying duty cycle as the current changes with the state of charge (and changes a lot when you first start up and the error amplifier is trying to deal with the surge current.)
I suspect the smoothed output is an integral part of the feedback used to regulate the output voltage. Without that, the total current may be wildly off target.
Well, it was the old argument from cc chargers like tp4057 to pulse charger mx1879. But speak to solar controller, i find a Chinese company has created a chip called MPPT-1 2022, that actually do the dc-dc down conversion and provide kind of real mppt behaviour with less than 1 buck!
Presumably this also extends the charging time. On a simplistic level a 50% duty cycle would double the charging time (admission: commenting without reading the paper!)
Compared to CC charging at 1C, they pulse charged at 2C and 50 % duty cycle to get the same charge rate and charging time.
As most chargers ‘limit’ current to 1C, 2C etc. according to te cell they’re intended for I’d suspect the pulse charger has a higher current limit which would mitigate the lower average ‘on time’.
I could of course be compeltely wrong and will probably kick myself later when I get time to read the paper properly.
You should have read the paper. Or at least skimmed through it and looked at the graphs like I did. It shows that it pulses a current of 2C at 50% duty cycle. Charging time remains the same. We already know a lower charging current (or lowering it once the battery warms up) increases lifespan of the battery. But this technique has the same effective charging current.
I wouldn’t be surprised if one of the main reasons we have to limit CC charging to 1C is due to the depletion effects described in the paper, and so peak current can go higher as long as the relaxation periods are present to keep the cells healthy.
It’s mostly to keep the cell voltage below a certain limit.
You have to remember that the cell is a long rolled up foil sandwich with resistance along the way. It doesn’t charge quite evenly across the entire electrode if you push really high currents through it. The thinner the foil, the more you can pack in, but the slower you have to charge.
For pulsed charging, there’s the additional trouble of the cell having inductance, because it is a spiral, and also capacitance so it leaks AC through and not all of the current contributes to charging it at higher frequencies.
Though more modern cells expose the edge of the foil along the way and fold it on itself across layers to mitigate that effect. For instance in electric cars, so they can push hundreds of kilowatts through it. Still, at very high currents there will be a voltage difference between the edge and the middle of the cell.
Why aren’t all charging systems using it is a good question but the obvious question in that regard is the duty cycle of Pulse-2000? If it’s 50% like shown in the above first image then it’ll mean at least 2x the charge time. Others have shown that slower charging than max 1C charging is better for the battery life and others have shown it’s better to charge more regularly but a smaller percent(30-40%) SoC instead of fewer but deeper discharge/charge cycles. Heating and the expansion that brings seems to be a contributing factor and Pulse-2000 is going to reduce that heating unless the duty cycle is quite high compared to what’s shown(50/50).
They double the peak charge current to get the same charge time. This unfortunately doubles the average I squared R conduction loss heating, so it would be disadvantageous in hotter environments or insufficiently cooled battery packs. Not so bad for my electric car here in Canada, though!
It shows that it pulses a current of 2C at 50% duty cycle. Charging time remains the same.
“having these last double as long would be very beneficial.”
– only to the customer unfortunately.
I am not sure of this. I see iphones as being very expensive yet they sell lots of new ones and there are still a lot of old ones out there. They get newer features that people want and they drop OS support for them. I like to think that if they come up with a better way to charge batteries so they last longer, it will be sold as a feature, at lest until the tech is put on a chip and everybody has it, and I do not think it will be long before it is a common feature in charging/management chips.
Most battery powered devices are thrown away because the batteries go dead, and can’t be charged. Pulse Charging can rejuvenate the dead batteries, and make the device useful again. Oh, that would reduce your need to buy new cell phones, and other battery powered stuff. We can’t have that!
And to the planet too. But no one care anyway.
Any chance we can just hack a 2K square wave onto the output of our current chargers? (I’m thinking 18650’s here). A 555 ought to do it.
Not sure it’d work. First because to get the same charging speed, you need to crank up the current to 2C instead of 1C. And since default charging algorithm is CV then CC, it means there’s a feedback circuit that’s measuring the battery voltage and current input. If you chop the output, that circuit will only see half the value on average which might be catastrophic for the feedback loop.
Instead, I think a programmable charger can be tweaked to only measure current & voltage during the on state of the PWM (ideally, at the end of the pulse so the transient is done)
CC then CV
Wasnt pulse charging also popular for NiCd?
I had Iron Curtain era handheld CB (Tukan 1) as a kid, as old as I was at the time. https://unitraklub.pl/opis/24161 Was very surprised to discover charger was just a transformer with single diode going straight to raw NICd cells.
Hi Rasz, was this a yellow coloured plastic transfomer housing for the adaptor ;-?
Those toy chargers work fine, as long as you keep the temperature in control.
As well from the transformer adapter as of the batteries to charge.
In the end NiCads are much more robust than the ‘new’ developped more environment friendlier newbee batteries. Again, it is because of human dump waste behaviour that NiCads went out of sight.
But they are still pritty well used in for example emergency light armatures ;-?
It is not rocket science, but for the majority it still is,
Back in the mid 1970’s there was a NiCd battery pack charger schematic published in Soaring magazine (!) that provided pulse charging for wet cell nickel cadmium battery packs commonly used in sailplanes. It used rectified AC and, for each 60Hz cycle, would measure the battery pack voltage and, if it was below an adjustable value, would momentarily put a heavy load on the pack (a few milliseconds) followed by a longer charging pulse. A LED would flash during the charging pulse. When used, the LED would light steadily then dim and ultimately become an occasional flash as it would keep the pack in float charge.
All done with a SCR and a few transistors and discreet parts. Always struck me as a truly elegant design!
Why didn’t chargers use pulse mode from the beginning – and why don’t they all do so now? Lots of non-conspiratorial reasons. Pulse charging takes more circuitry – expensive, lossy, large, and more likely to fail, especially in the past (use lots of transistors). Pulses have high frequency content, resulting in audio and video noise and other interference issues. Increased current during the pulses require lower impedance parts to supply same, which has its own costs and side effects. As an electrical engineer, I appreciate the benefits of pulse charging (cf above mention of a March 1971 design) as well as why it is not always used.
Meanwhile, my 2015 Surface Pro 3, 2008 Prius (over 350Mm), and 1987 Norelco shaver are still running fine though admittedly I replaced the shaver’s NiCds in 2003.
Please excuse my shouting, but I have to do it. “THIS IDEA HAS BEEN AROUND FOR OVER 40 YEARS!!!”. Yeah, virtually all batteries can benefit from pulsed charging. It’s actually a bit more complicated than that. There is a large charging pulse where current is pushed into the battery at 10X the charging rate, then there is what’s called a burp discharge pulse at 1/10th the charging current. The BDP is a small brief little discharge current that helps assimilate the charge carriers. So, it goes like this Charge Pulse (Big), Burp Discharge Pulse (small), and a small rest period. It was originally used in NiCad batteries, and was noted for being able to rejuvenate batteries. This also worked on Lead Acid batteries as well. I had a Lead Acid charger that used pulse charging, and was able to bring a totally dead sulfated Lead Acid battery back to life. The really big reason why this technology faded away was that it was too good. It would make batteries last 10-100 times longer. The battery industry wants batteries that fail after a known period of time so they can sell you more. These chargers save batteries, and prevent you from buying new ones. THAT’S WHY! If cell phones, and other battery using equipment were to use this charging technique, our cell phones, and other battery powered equipment would last 10-100 times longer. Oh! We can’t have that!
Yep, I agree with James Reed Feeney,
MOREOVER I’d like to reffer, what you plug in your cellphone for example,
is NoT a charger, merely a mains voltage safety down transformer !
ALL those expensive devices have their charge controller inside,
they just need a low DC-voltage applied for ;-?
And yes, it is possible that battery manufacturers want to sell more often.
But in the end: it are the users that decide how to apply their appliances !
And that is where it often fails.
And I can write books about this.
Refilling a car only when it is really empty on reservoir, . . .
Running with tyres over or under inflated, . . .
Cooking always a half full water kettle, . . .
It all ends up in premature wear and costly replacements, . . .
It is like selling medication to counter migraine, and writing on the leaflet:
can provoke headache, . . .
Hmm, if pulsed charging helps battery life, I wonder if pulsed discharging (ie, usage) would also help?
Most devices already but Buck/Boost converters in front of battery, so they are pulsed loads.
Nope, because than you create also pulsed discharge spikes !
LoL, folks, I to think that planned obsolescence is a Hoax !
The circuit for pulsed charging gets complicater and thus more expensive .
But, why nobody seems to realise themselfs: every car Lead acid battery is already yet pulsed charged !
See, you have a three phase alternator, followed by a 3ph rectifier, and than the battery, that acts as a
smoothing super capacitor aswell ;-? I don’t think this needs more explanation, Harry Belgium.
And yes, ALL batteries benefit from a controlled pulsed charging.
You can even pulse a Constant Current source, and those circuits exist for decades.
And ALL cellphones, do have yet a very unique and complex internal battery charging management.
It are the users that destroy their batteries premature ! Period.
One common thing that destroys batts and CAPs is a too high ambient Temp.
Whether that’s in Celsius or Fahrenheit ! CAPs don’t like heat,
so are Batts just huge super caps.
Second is too often deep discharges.
As with most people shouldn’t have kids, nor should they drive a car, etc . . .
The world would be a lot better off, with more technical inclined education & insights of use ;-?
And now, all comments will start to raise, LoL
PS moderator, feel free to take parts out of this my comment, just please try to keep the escence ?
And my last on this topic : Harry says :
The best battery chargers, are the ones that act on each cell individually, period.
Another problem with batteries is that it are allmost always a combination of cells,
to achieve a certain end voltage. And here comes the problem of uneven distributed
charges due to each cells’ individual capacities, that degrade over time, . . .
Allmost all problemsome battery packs, let’s say from a cordless drill, or vacuum cleaner, etc. . .
End up, with one cell that is unbalanced, overcharges -because of the others- and in the end fails,
pulls the overall voltage down, and the next weak cell follows, etc . . .
Every technical inclined will see my point ;-?
And I really don’t think any battery manufacturer does this on purpose.
To select each individual battery pack, and charge them all individually
would turn way too expensive and labour intensive.
ONE MAJOR WWW environmental more friendlier design would be, that each battery pack would be made of individually easy replaceable battery cells. Whether it are NiCad, NiMh, Li-ion, LiPo, etc . . .