When you think of tracked robots, you might think of bomb disposal robots or others used in military applications. You probably haven’t seen anything quite like this, however—it’s a “reconfigurable continuous track robot” from researchers [Tal Kislasi] and [David Zarrouk (via IEEE Spectrum).
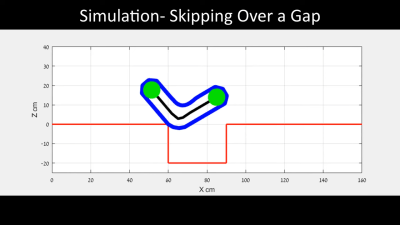
The robot looks simple, like some kind of tracked worm. As its motors turn, the track moves along as you would expect, propelling the robot along the ground. Its special feature, though, is that the track can bend itself up and down, just like a snake might as it rises up to survey a given area.
The little tracked robot can thus tilt itself up to climb steps, and even bend itself over small obstacles. It can even try and hold itself up high as it inches along to try and bridge its way over a gap.
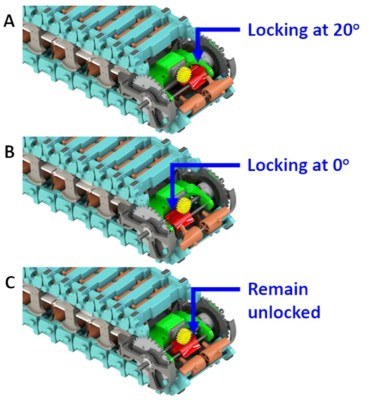
How does it achieve this? Well, the robot is able to selectively lock the individual links of its outer track in various orientations. As the links pass over the front of the robot, a small actuator is used to lock each link in a 20-degree orientation, or a straight orientation, or leave them loose.
The ability to lock multiple links into a continuous rigid structure allows the robot to rise up from the ground, form itself into a stiff beam, or conform to the ground as desired. A mechanism at the back of the robot unlatches the links as they pass by so the robot retains flexibility as it moves along.
It’s a nifty design, and one we’d like to see implemented on a more advanced tracked robot. We’ve explained the benefits of tracked drivetrains before, too.
Fantastic !!! Clearly great thinking. What would the version that can turn look like?
Two tracks that can turn independently and sync back up to go straight again. No different from tanks or any other two wheeled robot.
“We Didn’t Run Out Of Television Screens And Planes, We Ran Out Of Food.”
This is really cool. I feel like a track system that ran with some sort of cable connecting the track units together, the way ski lifts run, would allow for the track to be held to the system that supports and drives the tracks, so then you could articulate the support system and get a similar result, but maybe with fewer moving parts. Ski lift systems have the cable held on top and bottom with a lateral connection to the gondolas, to ensure the cable can’t drop. A tracked system doing this would need to have some ability to alter its length, but could, for instance, run in a sinewave with continuous curvature along the body of the machine. Can you imagine something like this slithering up stairs?
Look at him go.
Love it! Soo clever. Just one fly in the ointment. Tracks get used in muddy or sandy/griity places. How long will it function in abrasive porridge?
Spent my youth repairing dumb tracks…..
I was similarly thinking that this wouldn’t be very robust.
Perhaps some mechanical simplification (at expense of cost) would be possible by fitting an actuator to each tread block?
I feel like this is only an exercise in minimizing control, rather than anything useful.
As such, it is an interesting exercise.
But you wouldn’t actually want the fragile, disposable parts of your vehicle to be the single points of failure.
On the other hand, you turn every track link into an actuator, via a single control mechanism at the front. I find it to be an amazingly simple solution, compared to say having a line of actuators down the body to generate the same movement.