They might call it Levity, but there’s nothing funny about Rapid Liquid Print’s new silicone 3D printer. It has to be seen to be believed, and luckily [3D Printing Nerd] gives us lots of beauty shots in this short video, embedded below.
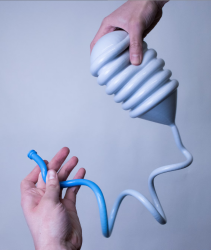
Printing a liquid, even a somewhat-viscous one like platinum-cure silicone, presents certain obvious challenges. The Levity solves them with buoyancy: the prints are deposited not onto a bed, but into a gel, meaning they are fully supported as the silicone cures. The fact that the liquid doesn’t cure instantly has a side benefit: the layers bleed into one another, which means this technique should (in theory) be stronger in all directions than FDM printing. We have no data to back that up, but what you can see for yourself that the layer-blending creates a very smooth appearance in the finished prints.
If you watch the video, it really looks like magic, the way prints appear in the gel. The gel is apparently a commercially-available hydrogel, which is good since the build volume looks to need ̶a̶b̶o̶u̶t̶ ̶5̶0̶0̶ ̶L̶ at least 125 L of the stuff. The two-part silicone is also industry-standard and off-the-shelf, though no doubt the exact ratios and are tweaked for purpose. There’s no magic, just a really neat technology.
If you want one, you can sign up for the waiting list at Rapid Liquid Print’s website, but be prepared to wait; units ship next year, and there’s already a list.
Alternatively, since there is no magic here, we’d love to see someone take it on themselves, the way once equally exotic SLS printers have entered the DIY world. There was a time when resin printers were new and exotic and hobbyists had to roll their own, too. None of this is to say we don’t respect the dickens out of the Rapid Liquid Print team and their achievement–it’s just that imitation is the sincerest form of flattery.
Cool tech and nice write-up!
I suppose you mean it is more isotropic than FDM (instead of less)?
Indeed, the structure of the sentence is clear, and thus logically it must be. But I stumbled on that one too.
And fixed. Thanks all.
Definitely meant more isotropic. Or maybe less anisotropic.
Hmmm, I think it’s correct as written, at least if I understand the printing process. Isotropic would imply that the structure is the same along rigid/set lines. But if the layers blend and ooze, then the structure is less “iso” ??
Then again it’s strength that’s mentioned. Perhaps less isotropic in form but stronger in all directions (vs weak along layer lines) so more isotropic in strength?
Isotropic means the same (iso) in all directions (tropic). So less isotropic means more difference between directions, whereas more isotropic means more the same in all directions, which is obviously what is trying to be explained. So it should definitely be MORE isotropic.
Not to be the one… but… Isotropic means same in all directions, as such there can be no “more” (or less for that manner). Different levels of anisotropy on the other hands maybe make more sense…
Nice article by the way
Yes, indeed I did.
I had initially written about structure, then edited it to be about strength, and apparently forgot to switch that word.
That’s the sort of quality you’ll never get from an LLM!
The Form 3 supports Silicone but its expensive.
https://formlabs.com/store/materials/silicone-40a-resin/?srsltid=AfmBOopznaU22ij7KZd-gJmMnn_OHzGkGmEHHiKW5hLdVl9NfYqk1loA
This printer is looking to be more expensive imo, possibly by a lot. Material costs will be cheaper though, so at scale it could work out and the type of versatility is different.
Wonderful idea and even better execution. I could see this replacing some industrial processing needs. I’d love to learn more about the strength of materials made this way, it’d be nice to have a mini version of this :) 500L is a lot of gel to spill
This doesn’t look like 0.5 cubic meters at all. Apparently, the video author got “half-a-meter cube” (50x50x50cm) confused with “half-a-cubic-meter” (0.5m^3).
The build volume is 50x50x50cm (data from the website), which is “only” 125L of hydrogel :)
That box in the video doesn’t look like 50x50x50cm. More like 100x100x100cm or so. But that’s 1,000L. So maybe the box is 79.3700526×79.3700526×79.3700526cm?
Or just 80x80x80cm, which would be 512L, which is 500L when you round it. ;)
A 50cmx50cmx50cm build volume could easily become a 80cm-on-a-side box if the print head needs 15cm of clearance on each side… although that seems like a lot of clearance and you probably wouldn’t need anywhere near that much on the Z axis.
Yeah, true. So the build volume could be 50x50x50cm, but the box might be 80x80x80cm with 15cm dead space on every side, requiring 512L of gel.
I can imagine that the dead space is necessary to prevent distortion of the printing needle (Head? What would you call it?) due to the drag of the gel against the box’s surface. I can imagine that the forces on the needle could become significant when it moves close to the edge of the box, possibly even affecting the calibration.
I hope I explain it understandable enough. :)
Hmm. It doesn’t look like a 50cm box, but you’re right about the build volume. I’ll change it to “at least 125 L” since I think there might be some dead space in there that would be filled with gel.
No they are .5 meter, and 1 meter. They are huge. They are my favorite new vendor at work
It looks huge, I’d like to work with one but this is clearly an entirely industrial market product.
I swear I’ve seen something like this before, printing in jell, but I thought it was expanding foam or something other than silicone. Maybe it was the same company.
There’s an entirely different system that does essentially voxel prints via light in a gel, maybe you’re thinking of that?
I wonder how well something less viscus would work. Printing in rapid drying liquid latex for instance. Maybe printing in cyanoacrylate on a bed of baking soda, so it would print almost like an SLS printer.
This isn’t very viscous, and they are taking advantage of that for layer cohesion. Are you sure someone hasn’t done that with superglue though? Sounds very familiar.
As mentioned in the video, I’m sure they “made it look easy” but I can’t help but think that a DIY hacker community could take this idea on and churn out a garage-made version of this.
I’ve seen DIY clay printers, for example, but I don’t think I’ve seen anything like this. Does anyone know of anyone who has attempted to make something like this? I don’t have the bandwidth to experiment but I could probably manage the time to at least build something if it were open-sourced, and I’d love to have the capability to print with silicone (directly; I’m aware of FDM mold-making).
I’d absolutely love one of these Levity printers but I’m sure it’s well out of my budget, hence my desire to build. I also noticed they mention patents on their website though, so maybe that might discourage us hackers from attempting to roll our own.
They will. We let the venture capitalists front the r/d and then copy it soon after release. Then about a year later the mass market chinese version will appear. Its just early in the cycle still. ;)
Pretty sure that’s why their opening gambit is full-on industrial size production machines. It’ll slow direct copies and keep it off the radar until the checks clear.
This is definitely garage-doable, the key component has actually the slicer, followed by the needed silicone ratio for ideal curing in a hydrogel. It’s summer, roll out the back yard labs and start the engineers!
i’m really glad they printed everything with a flared base, that’s very responsible of them.
Oh my.
My first thought as well haha
No Joke…
Must resist making GPL Richard Stallman ‘branded’ fleshlight liner joke…
Don’t push ‘Comment’…Just hit back…
Plenty of jokes in this subject.
Each worse than the others.
Slipped.
this definitely revolutionizes the diy sex toy scene. now if i can convince radiology to scan my booty and send me the pointcloud, i can make something that hits the spot every time.
And you can literally go f**k yourself :-D
Still cost of consumables especially against resin.
Not really, hydrogel isn’t expensive and it’s pretty reusable, and the silicone is much less expensive than resin.
Also there’s no supports to remove and the type of suspension and curing has improved isotropy compared even to resin prints, so there is less post processing.
Where resin wins is resolution and speed, that hasn’t changed.
Regular caulk would not cure in that scenario, it does need access to air. This is using a conventional water based gel though, and conventional liquid silicone, for exactly what you describe. Only their slicer (proprietary) is novel in this case but the printer itself is a monster.
No silicone requires air itself. Condensation or tin cure silicones need water to cure, and air contains plenty of water for the purpose. A hydrogel will be a perfect environment to cure those silicones in.
Or you can use a platinum cure silicone which contains its own catalyst when mixed and will cure even if completely sealed.
…and indeed “platinum cure” came up in the video a lot.
I imagine that this process could also work with liquid epoxy resin as long as you could get a gel and resin of compatible density.
You would end up with some weird thing somewhere in between FDM and resin 3D printing.
No supports required, and you might still be able to use UV setting resin, if the gel allows that frequency through.
However you would need a large tank of gloop.
“None of this is to say we don’t respect the dickens out of the Rapid Liquid Print team and their achievement–it’s just that imitation is the sincerest form of flattery.”
If I may be a bit pedantic, this isn’t really a compliment. The full saying is “imitation is the sincerest form of flattery that mediocrity can pay to greatness”.
If I may also be pedantic, I would point out that in the context of the full quote the Liquid Rapid Print is being referenced as “greatness”, which is indeed a compliment. The full context isn’t much of compliment to us hackers, though. I’ll take mediocrity if it lets me copy this sweet idea, though.
Genuinely curious as to what they got away with patenting given that it feels like at least some prior art has existed for over a decade in academia. https://www.dezeen.com/2013/07/23/sci-arc-student-develops-freeform-3d-printing-with-undo-function/
The cited work involved light cured resin, NOT silicone. That alone could be enough. Many patents include aspects that build upon prior art, you cant determine the validity of patent from a birds eye view, you must examine the SPECIFIC claims of a patent to determine if they are novel, unique, and eligible for protection.
This thing’s big brother!
https://spritesmods.com/?art=jello3dprinter
This may be helpful
https://techxplore.com/news/2025-05-origami-materials.html