If legend is to be believed, three disparate social forces in early 20th-century America – the temperance movement, the rise of car culture, and the Scots-Irish culture of the South – collided with unexpected results. The temperance movement managed to get Prohibition written into the Constitution, which rankled the rebellious spirit of the descendants of the Scots-Irish who settled the South. In response, some of them took to the backwoods with stills and sacks of corn, creating moonshine by the barrel for personal use and profit. And to avoid the consequences of this, they used their mechanical ingenuity to modify their Fords, Chevrolets, and Dodges to provide the speed needed to outrun the law.
Though that story may be somewhat apocryphal, at least one of those threads is still woven into the American story. The moonshiner’s hotrod morphed into NASCAR, one of the nation’s most-watched spectator sports, and informed much of the car culture of the 20th century in general. Unfortunately, that led in part to our current fossil fuel predicament and its attendant environmental consequences, which are now being addressed by replacing at least some of the gasoline we burn with the same “white lightning” those old moonshiners made. The cost-benefit analysis of ethanol as a fuel is open to debate, as is the wisdom of using food for motor fuel, but one thing’s for sure: turning corn into ethanol in industrially useful quantities isn’t easy, and it requires some Big Chemistry to get it done.
Heavy on the Starch
As with fossil fuels, manufacturing ethanol for motor fuel starts with a steady supply of an appropriate feedstock. But unlike the drilling rigs and pump jacks that pull the geochemically modified remains of half-billion-year-old phytoplankton from deep within the Earth, ethanol’s feedstock is almost entirely harvested from the vast swathes of corn that carpet the Midwest US (Other grains and even non-grain plants are used as feedstock in other parts of the world, but we’re going to stick with corn for this discussion. Also, other parts of the world refer to any grain crop as corn, but in this case, corn refers specifically to maize.)
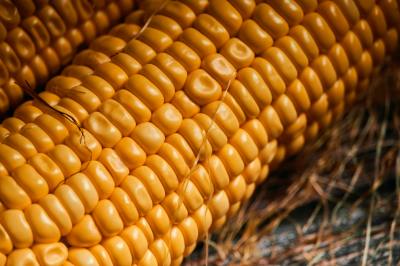
The corn used for ethanol production is not the same as the corn-on-the-cob at a summer barbecue or that comes in plastic bags of frozen Niblets. Those products use sweet corn bred specifically to pack extra simple sugars and less starch into their kernels, which is harvested while the corn plant is still alive and the kernels are still tender. Field corn, on the other hand, is bred to produce as much starch as possible, and is left in the field until the stalks are dead and the kernels have converted almost all of their sugar into starch. This leaves the kernels dry and hard as a rock, and often with a dimple in their top face that gives them their other name, dent corn.
Each kernel of corn is a fruit, at least botanically, with all the genetic information needed to create a new corn plant. That’s carried in the germ of the kernel, a relatively small part of the kernel that contains the embryo, a bit of oil, and some enzymes. The bulk of the kernel is taken up by the endosperm, the energy reserve used by the embryo to germinate, and as a food source until photosynthesis kicks in. That energy reserve is mainly composed of starch, which will power the fermentation process to come.
Starch is mainly composed of two different but related polysaccharides, amylose and amylopectin. Both are polymers of the simple six-carbon sugar glucose, but with slightly different arrangements. Amylose is composed of long, straight chains of glucose molecules bound together in what’s called an α-1,4 glycosidic bond, which just means that the hydroxyl group on the first carbon of the first glucose is bound to the hydroxyl on the fourth carbon of the second glucose through an oxygen atom:
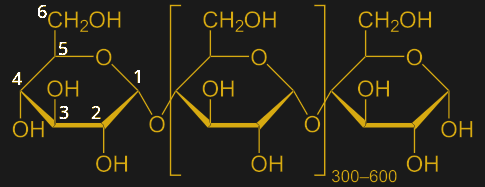
Amylose chains can be up to about 500 or so glucose subunits long. Amylopectin, on the other hand, has shorter straight chains but also branches formed between the number one and number six carbon, an α-1,6 glycosidic bond. The branches appear about every 25 residues or so, making amylopectin much more tangled and complex than amylose. Amylopectin makes up about 75% of the starch in a kernel.
Slurry Time
Ethanol production begins with harvesting corn using combine harvesters. These massive machines cut down dozens of rows of corn at a time, separating the ears from the stalks and feeding them into a threshing drum, where the kernels are freed from the cob. Winnowing fans and sieves separate the chaff and debris from the kernels, which are stored in a tank onboard the combine until they can be transferred to a grain truck for transport to a grain bin for storage and further drying.
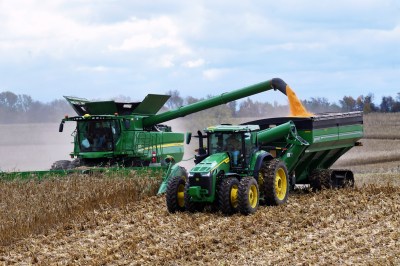
Once the corn is properly dried, open-top hopper trucks or train cars transport it to the distillery. The first stop is the scale house, where the cargo is weighed and a small sample of grain is taken from deep within the hopper by a remote-controlled vacuum arm. The sample is transported directly to the scale house for a quick quality assessment, mainly based on moisture content but also the physical state of the kernels. Loads that are too wet, too dirty, or have too many fractured kernels are rejected.
Loads that pass QC are dumped through gates at the bottom of the hoppers into a pit that connects to storage silos via a series of augers and conveyors. Most ethanol plants keep a substantial stock of corn, enough to run the plant for several days in case of any supply disruption. Ethanol plants operate mainly in batch mode, with each batch taking several days to complete, so a large stock ensures the efficiency of continuous operation.
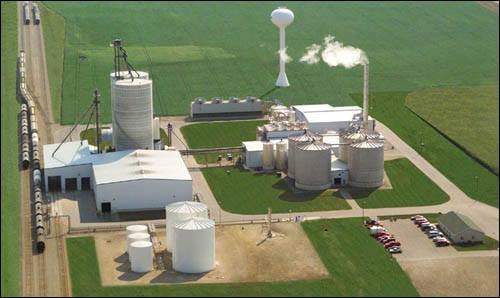
To start a batch of ethanol, corn kernels need to be milled into a fine flour. Corn is fed to a hammer mill, where large steel weights swinging on a flywheel smash the tough pericarp that protects the endosperm and the germ. The starch granules are also smashed to bits, exposing as much surface area as possible. The milled corn is then mixed with clean water to form a slurry, which can be pumped around the plant easily.
The first stop for the slurry is large cooking vats, which use steam to gently heat the mixture and break the starch into smaller chains. The heat also gelatinizes the starch, in a process that’s similar to what happens when a sauce is thickened with a corn starch slurry in the kitchen. The gelatinized starch undergoes liquefaction under heat and mildly acidic conditions, maintained by injecting sulfuric acid or ammonia as needed. These conditions begin hydrolysis of some of the α-1,4 glycosidic bonds, breaking the amylose and amylopectin chains down into shorter fragments called dextrin. An enzyme, α-amylase, is also added at this point to catalyze the α-1,4 bonds to create free glucose monomers. The α-1,6 bonds are cleaved by another enzyme, α-amyloglucosidase.
The Yeast Get Busy
The result of all this chemical and enzymatic action is a glucose-rich mixture ready for fermentation. The slurry is pumped to large reactor vessels where a combination of yeasts is added. Saccharomyces cerevisiae, or brewer’s yeast, is the most common, but other organisms can be used too. The culture is supplemented with ammonia sulfate or urea to provide the nitrogen the growing yeast requires, along with antibiotics to prevent bacterial overgrowth of the culture.
Fermentation occurs at around 30 degrees C over two to three days, while the yeast gorge themselves on the glucose-rich slurry. The glucose is transported into the yeast, where each glucose molecule is enzymatically split into two three-carbon pyruvate molecules. The pyruvates are then broken down into two molecules of acetaldehyde and two of CO2. The two acetaldehyde molecules then undergo a reduction reaction that creates two ethanol molecules. The yeast benefits from all this work by converting two molecules of ADP into two molecules of ATP, which captures the chemical energy in the glucose molecule into a form that can be used to power its metabolic processes, including making more yeast to take advantage of the bounty of glucose.
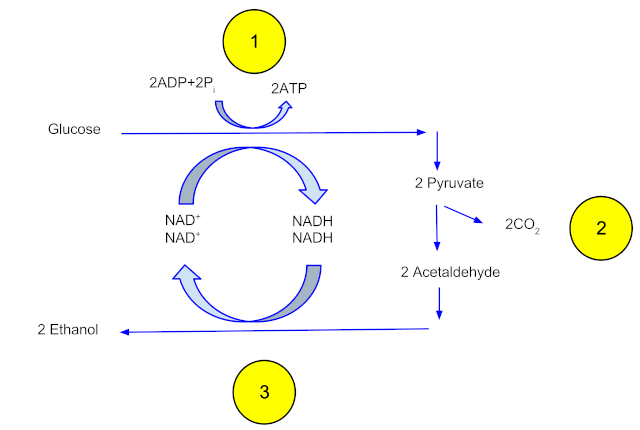
After the population of yeast grows to the point where they use up all the glucose, the mix in the reactors, which contains about 12-15% ethanol and is referred to as beer, is pumped into a series of three distillation towers. The beer is carefully heated to the boiling point of ethanol, 78 °C. The ethanol vapors rise through the tower to a condenser, where they change back into the liquid phase and trickle down into collecting trays lining the tower. The liquid distillate is piped to the next two towers, where the same process occurs and the distillate becomes increasingly purer. At the end of the final distillation, the mixture is about 95% pure ethanol, or 190 proof. That’s the limit of purity for fractional distillation, thanks to the tendency of water and ethanol to form an azeotrope, a mixture of two or more liquids that boils at a constant temperature. To drive off the rest of the water, the distillate is pumped into large tanks containing zeolite, a molecular sieve. The zeolite beads have pores large enough to admit water molecules, but too small to admit ethanol. The water partitions into the zeolite, leaving 99% to 100% pure (198 to 200 proof) ethanol behind. The ethanol is mixed with a denaturant, usually 5% gasoline, to make it undrinkable, and pumped into storage tanks to await shipping.
Nothing Goes to Waste
The muck at the bottom of the distillation towers, referred to as whole stillage, still has a lot of valuable material and does not go to waste. The liquid is first pumped into centrifuges to separate the remaining grain solids from the liquid. The solids, called wet distiller’s grain or WDG, go to a rotary dryer, where hot air drives off most of the remaining moisture. The final product is dried distiller’s grain with solubles, or DDGS, a high-protein product used to enrich animal feed. The liquid phase from the centrifuge is called thin stillage, which contains the valuable corn oil from the germ. That’s recovered and sold as an animal feed additive, too.
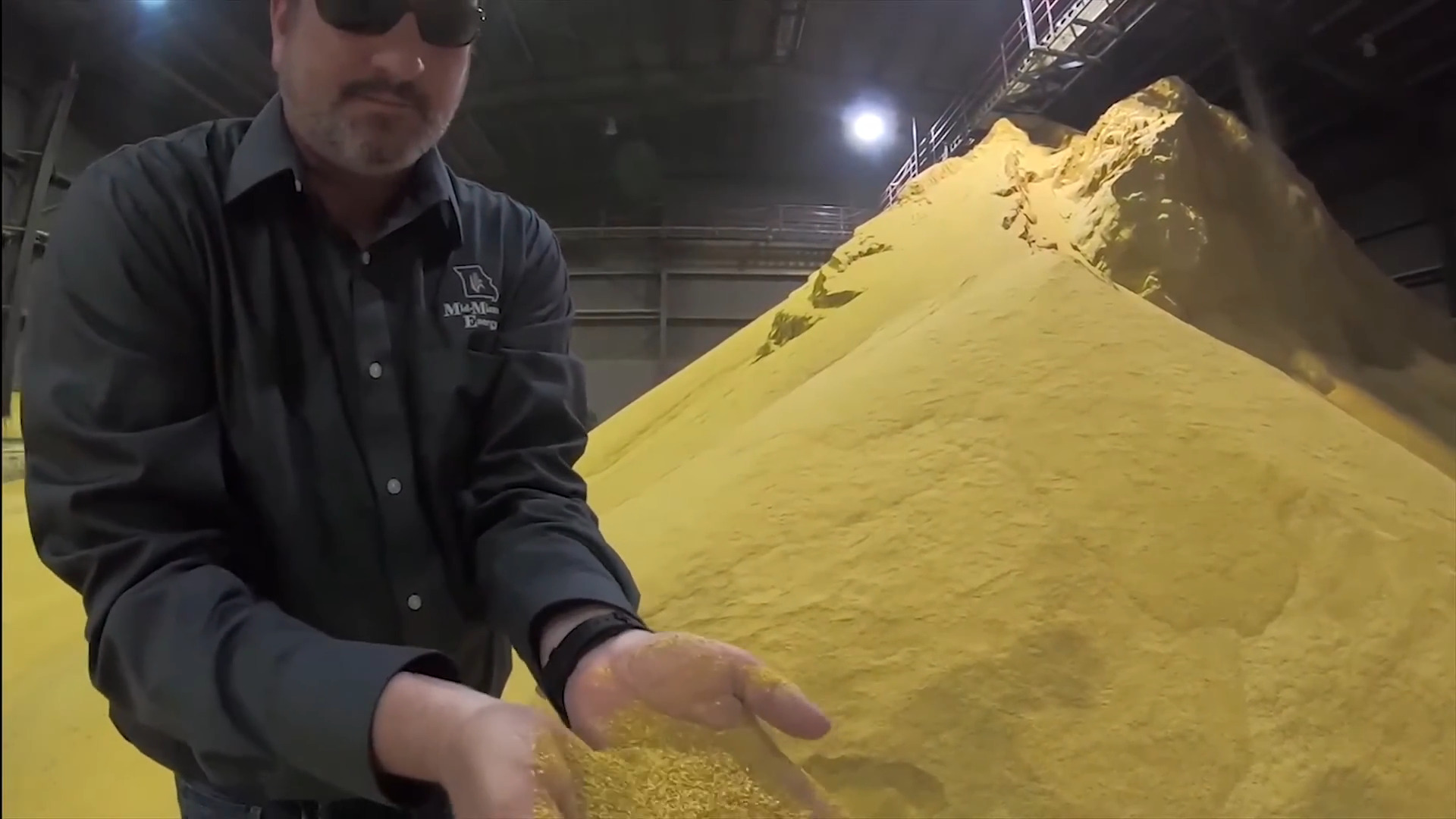
The final valuable product that’s recovered is the carbon dioxide. Fermentation produces a lot of CO2, about 17 pounds per bushel of feedstock. The gas is tapped off the tops of the fermentation vessels by CO2 scrubbers and run through a series of compressors and coolers, which turn it into liquid carbon dioxide. This is sold off by the tanker-full to chemical companies, food and beverage manufacturers, who use it to carbonate soft drinks, and municipal water treatment plants, where it’s used to balance the pH of wastewater.
There are currently 187 fuel ethanol plants in the United States, most of which are located in the Midwest’s corn belt, for obvious reasons. Together, these plants produced more than 16 billion gallons of ethanol in 2024. Since each bushel of corn yields about 3 gallons of ethanol, that translates to an astonishing 5 billion bushels of corn used for fuel production, or about a third of the total US corn production.
Serious questions:
How much electricity does this process use?
Are any ethanol plants operated net-energy positive…. meaning, once the plant is bootstrapped, can they produce the electricity and heat needed for distillation from the fuel they produce?
Has anyone considered co-location of nuclear reactors and distillation plants where waste heat could be put to good use?
Nope. The EROEI of corn ethanol is barely above 1 and if it was run back to produce electricity, it would be cleanly below 1.
Corn ethanol is just one way to greenwash fossil fuels and turn them into corporate farming subsidies.
https://link.springer.com/article/10.1007/s10668-010-9255-7
“Our results show that the average EROI calculated from the meta-error analysis was 1.07 ± 0.2, meaning that we are unable to assert whether the EROI of corn ethanol is greater than one. (…) In light of this work, we conclude that production of corn ethanol within the United States is unsustainable and requires energy subsidies from the larger oil economy.”
It’s right in TFS.
There are other valuable products of corn distillation.
Counting all the costs while ignoring some of the benefits is just a lie.
Those valuable products could be obtained otherwise, or the corn itself would be more valuable.
Sure, and the energy cost of obtaining those products by alternative ways should be in the accounting.
But that doesn’t advance the agenda, so ignored.
Like (parking/shop revenue) at airports…
Or counting fuel taxes as subsidies on gasoline…
Tired, derpy lies.
Farmers want the high protean feed associated with fermentation waste.
It’s not just for Vegemite.
The products also are less valuable than the corn.
Well, if for example you wish to make yeast proteins for animal feed, you can grow yeast much more efficiently and faster in aerobic than anaerobic conditions where it can consume the corn sugars more efficiently – but it won’t create ethanol, only CO2.
After all, about 90-95% of the energy in the corn is converted to ethanol in the process of fermentation – because the anaerobic conditions don’t allow the yeast to complete the metabolic process. That’s the point for making alcohol.
However, if you wanted to make yeast for animal feed, you would definitely NOT want to make ethanol because you could grow 10-20 times the amount of yeast with the same input of corn, or conversely spend just 5-10% of the feedstock for the same output of yeast proteins. That translates to vastly reduced logistics and material costs, and you don’t need the distilleries etc. to do it.
If your point is to just upcycle corn for better cow feed, you’re better off without all the complexities surrounding the ethanol.
the EROEI for gasoline is also clearly below 1, it’s only economically viable because oil refineries get the fuel they need to run for free. for the same reason, fuel ethanol stills are frequently powered by burning agricultural waste.
Gasoline is refined oil. Corn ethanol is also (mostly) refined oil and natural gas. Burning agricultural wastes only accounts for a small fraction of the energy demand in production.
If you look at it from that perspective, refining oil to gasoline is much simpler and more efficient than refining it to corn ethanol.
And, the agricultural waste also exists because of a huge input of petrochemical fertilizers and energy in farming and transport, so that too is a form of “refined oil” if you think about it.
But the main problem is that anything with an EROI less than 3:1 is considered a net energy sink for the society, because it needs to cycle back into its own means of production with losses along the way. Even if you make some optimistic hand-waving over the energy return of corn ethanol and the co-products, you can get to about 1.7:1 which is not enough to make it sensible.
Gasoline exists because we can’t burn oil directly in our cars. Corn ethanol exists because big agricorporations cannot get government subsidies without having some sort of an excuse.
Also, blending ethanol to fuels causes acetaldehyde pollution, which is a major contributor to lung cancer and asthma these days.
In the case of sugarcane derived ethanol, the EROEI was found to be as high as 6:1. The main source of energy tho power the distillery is sugarcane bagasse, and the plants are usually net energy positive, meaning that they export electricity to the grid when the boilers are running.
Rather than calculating it all, just look at how many of the conversion plants are sitting on natural gas pipelines/power lines etc. If they were at all efficient, wouldn’t they just burn their own product as a thermal source for distillation? Even oil refineries do this.
I worked closely aligned with some of the research on this for a very long time and the standard answer was “No, it’s not really energy positive but there are other benefits …”
The trick is that while it’s possible to produce net energy with corn ethanol, in the average case you don’t because it’s not the optimal case.
Money, not efficiency, is what decides where the plants go and what they use for energy. As long as they can turn a profit, nobody cares that they’re hooked up to the gas line and transporting corn in from across the country spending enormous amounts of fuel.
except ethanol isnt a fossil fuel.
Neither is hydrogen, but if you make it out of cracking natural gas… what’s the difference?
In sugarcane ethanol distilleries, the norm is to be net energy positive. The plant incorporates a main cogeneration boiler, fed by cane bagasse, that supplies steam for process heat and electricity via steam turbines.
I can visualise what a pound is. Just double it and add 10%. But a bushell??
1 bushel corn (US) equeals 25,4012 kg
and
1 bushel (US) equals to 35,239 l
Just picture riding on the bus from hell, which works in any metric.
Two pecks!
Simple.
1 bushel corn (US) equeals 25,4012 kg
and
1 bushel (US) equals to 35,239 l
“The beer is carefully heated to the boiling point of ethanol, 78 °C. ” ….. at which point, nothing useful will happen unless it were 96.5% ethanol. More likely it will need to be heated to about 90 degrees C if it’s 15% ethanol, with the temperature increasing slightly as time goes on.
I for one am waiting for Biotechnica to put out chooh2. Then we can really get going ;)
Jokes aside. For all dystopia in the world of Cyberpunk. I saw that lore bit on chooh and I instantly went, wow thats actually very green and renewable.
Hope we get something like it irl. Without the whole rubber and plastic damaging effect ethanol has.
https://en.wikipedia.org/wiki/Synthetic_fuel
The link between stock car racing and moonshine may have been a bit exaggerated, but you’ll still find a few bottles of undocumented alcohol in the break room cabinet at many NASCAR shops. Or would up until the time still covered under the statutes of limitations….
I have always wondered why we don’t make ethanol from recycled paper, it seems to me that we would just need to add cellulase to the process to get the same result. I’m sure someone here knows (seriously, this is one of the smartest places on the net) so could you tell me why this isn’t done?
Using cellulase is more costly because you have to produce the enzyme in large quantities, and it is produced mainly by organisms that eat wood – like fungi – which grow relatively slowly. Some sources say the cost of the cellulase enzyme alone is 50% of the cost of converting cellulose to fermentable sugars.
Wood ethanol was commonly made in the past as a side product of the sulfate process in paper making. The sugars were produced by acid hydrolysis instead.
Thanks.
Enzymatic conversion of cellulose to sugar isnt very efficient. Fortunately, The advancing field of Supercritical Water Oxidation Reactors is making great strides. This is not only applicable to paper waste but also to other cellulosic waste like the stalks and other non edible portions of agricultural crops.
Once these processes have been perfected and scaled the resulting sugars will not only be useful for fuelstock, but also as feedstock for modified yeast and/or bacteria producing an array of useful products from medicine to plastic to alternative foodstuffs. RealDeal and Perfect day are already making animal free milk and cheese from modified yeast. SCWO may someday allow companies like these to repurpose agriwaste and eliminate both the feed cost and environmental impact of dairy farming.
OOPS
Correction.
I meant to type Supercritical Water Hydrolysis (SCWH) not Supercritical Water Oxidation (SCWO). SCWO has a ton of interesting applications as well but does not result in sugar production as it typically employs higher temperatures, pressures, and exposure times than SCWH,
Cool. Sounds like SCWH will be quite an advance once perfected, thanks.
SCWH scares the crap out of me because I’ve seen what a boiler explosion can do, and SCWH generally runs even hotter and higher pressure. But it’s in the same league as the Haber-Bosch process and, although many people died before that got tamed, it’s pretty well understood now and widespread as heck. SCWH might not be so scary now.
Boiler explosions are a concern with batch processing, which is more commonly employed in SCWO than SCWH due to low residence times requirements. Continuous flow SCWH pumps fluidized feedstock into one port of a Y shaped Inconel or Hasteloy pipe, Injecting supercritical water at 380c (716F) at 230 bar (~3336psi) into another port, then harvesting the exhaust from the third port. The total residence time varies from 0.004 seconds to 1.15 seconds depending on input material type and consistency. This rapid reaction allows system to use thick wall small ID pipes with significant safety factors designed in. Scaling up is accomplished by parallel reactor pathways. This reduces cost in construction and maintenance over the service life as well as limiting disaster potential.
While commendable in principle, I wonder how tasty the milk and cheese are when the yeast is fed with pure sugar feedstock with nothing besides the essential nutrients to survive.
After all, you can taste the difference between a free range egg and a factory farm egg by the fact that the factory farm chicken were fed nothing but soy, corn, and some fish paste for protein, while the free range chicken also fed on actual grass and insects found outside.
the yeast is just producing casein and whey
The lactose, fats, minerals, vitamins, and water must be added from there.
The resulting products flavor and consistency has less to do with what the yeast is fed and more to do with the ingredients blended with their proteins.
The same kind of corn is also turned in fuel for diesel engines as well. There’s a refinery that makes the stuff also out west. Oh and it wasn’t just at the beginning of the 20C, that same group also was making cheap whiskey during the beginnings of this country. Take a look at the meaning behind the term “Shay’s Rebellion”.
“…that translates to an astonishing 5 billion bushels of corn used for fuel production, or about a third of the total US corn production.
“Astonishing” is not a good enough word.
I can find nothing in any of the arithmetic in the article (forget “Maths”; all it takes is simple “2 + 2 = …”) which would–or CAN–justify such a fact, particularly in light of of the fact that so much of the world is starving…INCLUDING first-world, second-world, …’n-th world citizens.
And forget the crap about this being ‘necessary’ for fuel purposes. The US is in the grips of an individual who uses the tag-line, “Drill, baby, drill!” to whip up his followers. And it will be done.
That is not for the lack of food. Half of all food produced is lost as waste because of overproduction and spoilage.
The original rationale for accepting the poor corn Energy Return on Energy Invested (EROEI) was as a gasoline substitute while moving to renewable energy sources. That’s been highjacked by farm states looking for another price support, but it wasn’t a bad idea.
The apparently positive EROEI for sugar ethanol in Brazil is illusionary. The growers are indirectly mining soil, moving on when a field is played out.
Given that hybrid and fully electric automobiles and light trucks are now widely available in the US, gasoline substitution has outlived its purpose.
Diesel substitution is still worthwhile. Too bad that the vast majority of US ag land is unsuitable for oil palm, and SEA growers are burning down forest to make room for more acreage.
Hybrids relying on internal combustion engines are more efficient than IC alone, but are still largely dependent on a fading petrochemical resource.
Full electric vehicles still suffer range issues, slow “refueling”, lithium volatility, and an environmental benefit beyond “NIMBY Pollution” thats only as good as the cleanliness of our grid which is still heavily reliant on nonrenewable resources.
We live in a country with a fully developed and widespread infrastructure for liquid fuel delivery. While ethanol only has ~56% the energy density of gasoline. Direct ethanol fuel cells already reach 40-55% efficiency with the potential to reach as high as 97%. Even if those potentials are never met, the current technology already overtakes the poor efficiency of internal combustion engines as well as IC Hybrids.
While not as energy dense by weight, ethanol beats hydrogens energy density by volume, doesnt require pressurized storage vessels, and has a significantly lower risk in accidents. Ethanol still has great potential in the automotive/transport field.
But if you cover that cornfield in solar panels, you collect a lot more energy than the corn was going to.
Fuel cells check arge a battery,hand you can charge batteries at night without using time, or quickly enough round here, on the road.
Grow something under your panels, even if it is grass, and the soil improves.
Why cover good agricultural land with solar panels when theres plenty of land unsuitable for crops that could be used? Solar is a great option for stationary (home and business) power, as well as limited range vehicles. It is NOT a great option for long distance or heavy load vehicles.
A Chevy Bolt has a 60KWh battery and a 259 mi range. Its fast charge only adds 100 miles after a 30 minute charge.
As to your fuel cells charge batteries, Thats not entirely accurate. Fuel cell vehicles rely on their battery only in conditions where operating the fuel cell is impractical or inefficient such as initial start up, and stop and go traffic. As a result, Fuel cell vehicles do not require nearly as large a battery as an EV does,.
The toyota Mirai only uses a 1.2KWh battery, but its Fuel cell can output 114-128KW. The Toyota Mirai XLE can travel about 402 miles on a full tank of hydrogen. It takes between 3 and 5 minutes to refill its tank. The problem is the US doesnt have a robust hydrogen infrastructure in place.
Ethanol fuel cells would not require any new fueling infrastructure as the existing petrol stations are capable of dispensing ethanol just as easily as petrol.
Personally I think corn should feed people and livestock. But once SCWH conversion of agriwaste, cardboard, waste paper, etc has been perfected and scaled to industrial volumes, the production of trash ethanol as feedstock for fuel cell vehicles will solve many of the issues of EVs.
Electric vehicles cannot be produced for everyone, there simply isnt enough raw material for the batteries. Gasoline and other alternative ICE fuels will be around for a long long time. EV are pipedreams, made to sooth the aching conscience of rich people.
There is enough raw materials, but not enough money to extract them, at least in any hurry.
When actively commuting by bicycle, I made a thing for my messenger bag that said “powered by clean burning ethanol.”
I still think that is the best use of fermentation.