For all of the semiconductor industry’s legendary reputation for cleanliness, the actual processes that go into making chips use some of the nastiest stuff imaginable. Silicon oxide is comes from nothing but boring old sand, and once it’s turned into ultrapure crystals and sliced into wafers, it still doesn’t do much. Making it into working circuits requires dopants like phosphorous and boron to give the silicon the proper semiconductor properties. But even then, a doped wafer doesn’t do much until an insulating layer of silicon dioxide is added and the unwanted bits are etched away. That’s a tall order, though; silicon dioxide is notoriously tough stuff, largely unreactive and therefore resistant to most chemicals. Only one substance will do the job: hydrofluoric acid, or HFA.
HFA has a bad reputation, and deservedly so, notwithstanding its somewhat overwrought treatment by Hollywood. It’s corrosive to just about everything, it’s extremely toxic, and if enough of it gets on your skin it’ll kill you slowly and leave you in agony the entire time. But it’s also absolutely necessary to make everything from pharmaceuticals to cookware, and it takes some big chemistry to do it safely and cheaply.
Going With The Flow
Understanding the industrial importance and production of hydrogen fluoride requires a close look at the fluoride side of the molecule. Like chlorine and bromine, fluorine is one of the halogens, and as such has a high electronegativity, or the tendency to attract shared electrons in chemical bonds. As the most electronegative element, fluorine is very reactive, so much so that it forms bonds with almost every other element on the periodic table.
Fluorine compounds fall into two broad categories: organic and inorganic. Both categories have a wide range of industrial uses. Organic fluorides are compounds where fluorine is bound to carbon; while this is technically a covalent bond where electrons are shared between two atoms, fluorine’s pull on the carbon electrons is so strong that it gives the C-F bond ionic characteristics. This tends to make organic fluorides, like polytetrafluoroethylene (PTFE, or Teflon), very stable compounds, leading to their industrial usefulness. Stability is a double-edged sword, though; fluorocarbon solvents and refrigerants like Freon can persist for decades in the upper atmosphere, and perfluorooctanoic acid (PFOA) is classified as a persistent organic pollutant or “forever chemical” with toxic properties.
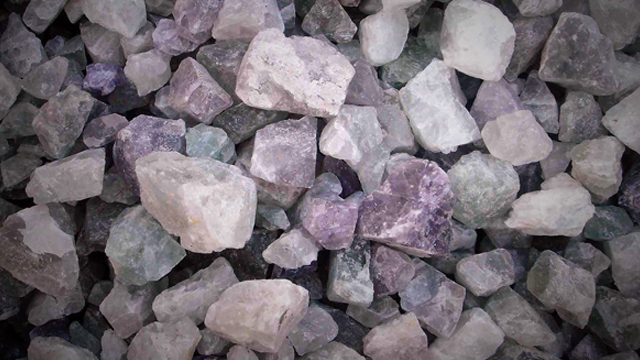
For as many uses as organic fluorides have, and for as much of them as we produce, the vast majority of global fluoride production is in the form of inorganic fluorides, and the majority of that is dedicated to the production of metal. Fluoride compounds such as calcium fluoride, also known as fluorite or fluorspar, have been used as a flux in steelmaking for centuries; fluorine takes its name from the Latin fluor, to flow. Thanks to its reactivity, the fluorine in fluorspar binds to impurities in the steel mix, floating it to the surface as a slag that can be removed. About half of the world’s fluorspar production goes into steelmaking, with most of the rest going into aluminum production in the form of synthetic cryolite, a compound of sodium, fluorine, and aluminum that is used as an electrolyte to lower the melting point of alumina in bauxite ore.
Inorganic fluorides also play a huge role in the petroleum industry, where fluorine serves as a catalyst for alkylation, the process of adding alkyl groups to smaller, lighter hydrocarbons. Alkylation is used to turn the four-carbon compound isobutane into alkenes such as propylene and butylene, which are precursors to plastics such as polypropylene and butadiene, the “B” in ABS. Inorganic fluorides are also making a splash in the battery industry, with lithium hexafluorophosphate (LiPF6) becoming more important as an electrolyte for lithium batteries.
None of these compounds, though, would exist if it weren’t for the two million tons of hydrogen fluoride we turn out each year, in the form of anhydrous hydrogen fluoride (AHF). AHF is a gas at room temperature, but when chilled slightly it condenses into HF, a liquid that’s miscible in water. Aqueous solutions of HF are called hydrofluoric acid, and are generally the form used for industrial processes to produce most of the organic and inorganic fluorides listed above. Hydrofluoric acid is also broadly used as a cleaner, solvent, and etchant in industrial processes, particularly in the manufacture of integrated circuits.
It Takes Acid to Make Acid
Fluorine is a fairly abundant element, making up 13% of the 13th most abundant in the Earth’s crust by mass. Because it reacts with so many elements, there are a lot of fluoride-containing minerals, like fluorspar, which is the main feedstock for industrial-scale hydrogen fluoride production.
Like many big chemistry processes, the reaction that produces hydrogen fluoride is quite simple. The details, however, require some careful chemical engineering and strict process control, along with a lot of specialized equipment:
Fluorspar is treated with sulfuric acid, creating hydrogen fluoride and calcium sulfate, which in hydrated form is known as gypsum. But before any of that can happen, fluorspar has to be mined and preprocessed. Most fluorspar deposits have a fairly low concentration of the mineral trapped in unwanted rock material, or gangue. To increase the relative concentration of fluorspar to gangue, raw ore goes through a process called beneficiation, where it’s crushed into a fine powder and mixed with water and surfactants. Air is pumped into the mixture, creating bubbles that the gangue adheres to while the fluorspar sinks. The enriched fluorspar goes through several rounds of froth flotation and drying until it gets to the proper concentration — about 97.5% pure fluorspar for acid production feedstock. Fluorspar used for flux in steelmaking or to make cryolite only needs to be between 60% and 84% pure.
Anhydrous hydrogen fluoride production starts in a prereactor, which is charged with dry acid-grade fluorspar. Sulfuric acid, which is produced from sulfur recovered from natural gas processing, is pumped in, along with oleum, or fuming sulfuric acid (SO3). The combined reactants are pumped into a rotary kiln, which is indirectly heated with steam. The kiln needs to be heated because the reaction of sulfuric acid and calcium fluoride is strongly endothermic; the heat drives the reaction to completion.
Raw hydrogen fluoride gas leaves the rotary kiln and passes through a series of filtration and purification steps. The goal here is to remove any fluorspar particulates and sulfuric acid aerosols in the gas, as well as to dehydrate the raw gas as much as possible with condensers and distillation. Anhydrous hydrogen fluoride can then be stored as a gas, or more commonly, diluted with water to form hydrofluoric acid at a variety of concentrations tailored to downstream processes.
Like everything destined for the semiconductor fab plant, the hydrofluoric acid used for etching silicon wafers has to be as close to contaminant-free as possible. Electronics-grade hydrofluoric acid is made by diluting AHF with ultrapure water to a final concentration of about 50%. Total cationic contamination has to be less than 10 parts per billion, meaning that each liter must have less than 10 micrograms of anything other than hydrogen, oxygen, and fluorine.
A Healthy Apatite
Another major source of hydrofluoric acid is as a byproduct of phosphoric acid production. Phosphates are a major plant macronutrient — it’s the “P” in the familiar “NPK” rating on fertilizers — and in a world with 8 billion mouths to feed, mountains of phosphate fertilizers are made every year. Phosphoric acid is the chief feedstock for fertilizer manufacturing, along with being important as a food additive, in lubrication and metal treatments, and of course as a dopant and etchant in semiconductor manufacturing.
Phosphoric acid is manufactured from phosphate-containing minerals such as calcium hydroxyapatite (Ca5(PO4)3OH), the same mineral that makes bones and dental enamel hard, and fluorapatite (Ca5(PO4)3F). Both minerals, together known simply as apatites, are found in phosphate rocks all over the world; commercially viable deposits are few and far between, though.
Extracting the apatite ores involves typical mining processes followed by similar beneficiation steps used in fluorspar manufacture. Phosphoric acid can be created from sufficiently enriched apatite by treating it with sulfuric acid:
It’s a very similar reaction to that used in AHF production, but the desired product is the phosphoric acid (H3PO4), which goes through extensive filtration and purification processes. The gaseous HF that’s produced is just a waste product, albeit one valuable enough to be recovered. This is accomplished with a wet scrubber, which treats the HF-containing flue gasses with a fine spray of water. The HF readily dissolves in water, making it easy to recover. The aqueous solution goes through further filtration and distillation processes to reach the final desired purity and strength.
Poisons While It Burns
The descriptions of the chemical processes used to liberate fluorine from minerals are greatly simplified, of course, and almost nothing about handling AHF and hydrofluoric acid on industrial scales is trivial. Hydrofluoric acid, while chemically classified as a weak acid thanks to its inability to dissociate completely into H+ and F– ions in solution, is anything but weak in practical terms. Hydrofluoric acid is corrosive in the extreme, quickly destroying most metals, many plastics, and even glass. Only certain polymers, like certain polyethylenes and fluoropolymers like Teflon, are resistant to HFA; unfortunately, materials like these are difficult to use in industrial settings, especially where high temperatures and pressures are needed. Certain nickel alloys like Monel are resistant to hydrofluoric acid, meaning that a lot of the reaction vessels and piping are used in hydrogen fluoride plants.
And as if hydrofluoric acid’s corrosivity weren’t enough, it’s also extremely toxic. Hydrofluoric acid burns in the lab or plant are very dangerous; as soon as the acid breaks down the integrity of the epidermis, the fluoride ions begin to bind to anything they can find, with particular affinity for calcium and magnesium ions in tissues. These ions are vital for the electrochemical reactions of the nervous system, meaning that with enough of a dose, fluorine ions can quickly stop your heart. Immediate washing followed by rapid medical intervention is required to avoid a gruesome and painful death.
It’s also a byproduct when you spill Chlorine Trifluoride (CF3), as noted by Derek Lowe in his infamous post “Sand won’t save you this time” (https://www.science.org/content/blog-post/sand-won-t-save-you-time).
To quote:
” it’s bad enough when your reagent ignites wet sand, but the clouds of hot hydrofluoric acid are your special door prize if you’re foolhardy enough to hang around and watch the fireworks.”
Hard pass on both for me. :)
This is the chemistry blog I have been looking for!
Fluorine chemistry just seems like utter chaos to me.
I just saw a video talking about HFA as a byproduct of combustion in an apparently infamous prototype rocket engine from the 60’s. The Rocketdyne Tripropellant. With only a passing interest in chemistry, this thing sounds like an absolutely horrifying concept…
It oxidizes high temperature fluorine and hydrogen with molten lithium.
https://www.youtube.com/watch?v=KX-0Xw6kkrc
The dangers we play with.
https://youtu.be/qfAw4YvI_u0
Best fuel ever! They said that it dissolves flesh, but surely they mean that it dissolves bone, while leaving a puddle of flesh.
“It oxidizes high temperature fluorine and hydrogen with molten lithium.” Except fluorine is normally an oxidizing agent, so it doesn’t get oxidized; it gets *reduced* (when it participates in a reaction as an oxidizing agent). And lithium is a reducing agent (and gets oxidized when it acts as such).
For anyone that hasn’t seen that article before, comment #3 has an entertaining tale to tell.
WHen I was fresh out of engineering school, with a shiny diploma in EE/semiconductor fabrication, I spent a year in an academic fabrication lab (class 100 with downflow tables) and was always very surprised by how casually some materials, like HF, Methylene chloride, benzene, and the like, were handled. About the only thing that really put fear into most (at least the brighter ones) of the staff was the silane gas feed for the furnace.
Then again, my SO at the time worked in materials at Corning, and she had some Really interesting stories…..
AFAIK Methylene chloride is just dichloromethane? Where is the problem with this? Much more benign than HF and a useful extraction solvent. It is not corrosive.
It has required control and recovery for many, many years. Leaving open washes full of it (litre quantities) was then, at best, poor practice, as was using it to spot-clean hands/skin (took the photoresist RIGHT off. Cavalier handling of the source bottles led to several people getting it on their bare hands). No monitoring was done at the time, but the vapours were well known to be harmful, skin contact was known to be harmful, and typical of the lax practice. This is why professional lab managers exist.
Remembers me of a friend, who was once working in screen printing and did this at home a few years later for fun. He was quite liberal with the methylene chloride for cleaning screens and hands. But in the mean time, the most damage to his body came from another chemical anyway: too much ethanol. That nearly led to his early death.
+1
HFA was the nastiest product I known … before parsing the excellent (and scary) “Things I Won’t Work With” articles serie by Derek Lowe on that website.
His piece on Dioxygen Difluoride (AKA “Satan’s Kimchi”) is an absolute gem
https://www.science.org/content/blog-post/things-i-won-t-work-dioxygen-difluoride
I watched a live demo of flourine being combined with metallic Caesium. Just for kicks and giggles. That was quite violent.
I used to work on a site that made and shipped HFA out in huge quantities. It’s bad – do not go anywhere near it.
There was a time when I was interested in making Si transistors at home. The realization that would need to use HF helped cured me of that. Fortunately, thin-film transistors are still on the table!
What? The forum that laughs at safety concerns with a hearty-HA!
I have already seen several videos about home made semiconductors. There were several glass etchants used, which have only a low concentration of HF or fluorides. I seems, that they can be be handled somewhat savely. Of course you should know what you do.
Platinum is also impervious to hydrofluoric acid. I worked for a while in a glassmaker’s research lab, and we used platinum crucibles the size of a pint-glass to make bespoke samples, as they could be thoroughly cleaned using the acid to prevent cross-contamination. Each one cost more than my house, and they were collected and weighed every night to prevent anyone gradually shaving bits off.
Pointing out an incorrect statement:
> Fluorine is a fairly abundant element, making up 13% of the Earth’s crust by mass.
According to https://en.wikipedia.org/wiki/Abundance_of_elements_in_Earth%27s_crust and the CRC handbook its more like 0.06%
Yes, my mistake — it’s the 13th most abundant.
I would like to point out 2 further mistakes
1. Regarding organic fluoro-compounds, it is a C-F bond, not C-Fl. Flavorium is far to unstable to make many compounds.
2. Isobutane is a 4 Carbon Alkane, not 3.
Fixed, thanks
Also, “Certain nickel alloys like Monel are resistant to hydrofluoric acid, meaning that a lot of the reaction vessels and piping are used in hydrogen fluoride plants.” – surely this should say that a lot of said vessels and piping are made of Monel, or something?
Did you mean Flerovium?
Nasty nasty stuff, but fascinating.
Recently had the opportunity to visit a semiconductor foundry where we were treated to a demo in their failure analysis lab.
Decapping a part for analysis used a combination of heated acids, one of which was hydrofluoric, and it took literally less than 30 seconds for the part to be stripped of encapsulation, ready to wash and further process.
AFAIK the decapping (removing the epoxi) is done with hot nitric acid and then you have to depassivate the chip (remove the glass layers) to be able to measure electrical signals. I think that needs HF.
Fun fact: The IRFNA ( inhibited red fuming nitric acid) as rocket propellant (oxidizer) was doped with HF (0,5%). That had the function as a corrosion INHIBITOR for the tanks (stainless steel?) That formed a stable fluoride layer, which protected the metal against the nitic acid.
An excellent article – very well written and bang on correct with some of the lesser-appreciated details of the manufacturing process.
I spent a while working on HF3, the former ICI HF production plant based in the NW of England, and fondly remember the burn at the back of the throat that ppm levels of HF gave when breathed in. Trying to keep the reciprocating prefeeder (basically something like a big industrial bread mixer, except that its charge was fluorospar, sulphuric acid and oleum) 100% gas tight was always a bit of a challenge…
The plant operators described HF as “an abhorrence of nature”, and they were right. Working on a plant like that required treating it with the utmost respect. Left long enough, it would even leave significant corrosion damage on high nickel alloy components, such as those made from Hastalloy or Monel B.
One of the largest customers didn’t fall into any of the categories listed here, but I’m not going to mention gaseous centrifugation…
It’s a credit to the plant operators, design engineers and maintenance folk that HF was successfully and *safely* manufactured for 50+ years on that site with capacities in excess of 30,000 tonnes per year. Sadly, that operation closed in 2015 and much of the knowledge surrounding the process has gone with it. Great to see an article like this to keep some of the details higher profile than they otherwise would be.
Well done. Keep the high quality technical articles coming.
(A chemical engineer that used to love working on big stuff who now works on small stuff instead since there’s not much big stuff left).
Useful article, but in fact there is little use of pure HF in semiconductor manufacturing today
Almost all the etch processes are plasma based, though they do use lots of fluorine in gases such as fluorocarbons, SF6, NF3 and WF6 for tungsten deposition. This does mean the effluent gases from the processes need a lot of scrubbing though.
Where bucket chemistry is still used, it’s likely to be buffered 10% HF, which is a bit safer.
Personally it was the Pirana etch that gave me the real willies!
Where’s the “don’t try this at home” disclaimer?
“Silicon oxide is nothing but boring old sand, and once it’s turned into ultrapure crystals and sliced into wafers, it still doesn’t do much.” Here, it sounds a lot like you’re talking about SiO2 which in crystalline form is quartz. But then you go on without a segue to talk about phosphorus and boron doping – which implies you are actually talking about silicon, not silicon dioxide, because there’s no reason to dope silicon dioxide. Then you specifically mention SiO2 again (“notoriously tough stuff, largely unreactive and therefore resistant to most chemicals”). It sounds like the author isn’t sure whether he’s talking Si or SiO2; does he know the difference? Just to clarify, pure HF doesn’t etch Si, but will etch SiO2. However, HF mixed with HNO3 and acetic acid will etch Si.
Guess I could have been clearer. Fixed the intro a bit.
Thanks for updating everything, and thanks for agreat read.