We had a chance to talk to Matthew Hertel of PocketNC at the Bay Area Maker Faire this year. During the conversation, he answered some questions I’d had about the project since I saw it on Kickstarter, and told a cool story while he was at it.
When the Pocket NC 5-axis Tabletop CNC Mill KickStarter came out, I immediately chocked it up as a failure out of the gate. I figured that there would never be a single delivered unit. It just seemed too impossible. The price was too low for a machine with that many large machined aluminum pieces. It had real linear guides. It had a real spindle and housed a beagle bone black running linuxCNC. It just couldn’t be that cheap. Ends up, I’m quite happy to be wrong. Pocket NC is doing well, delivering their first units, and taking new orders.
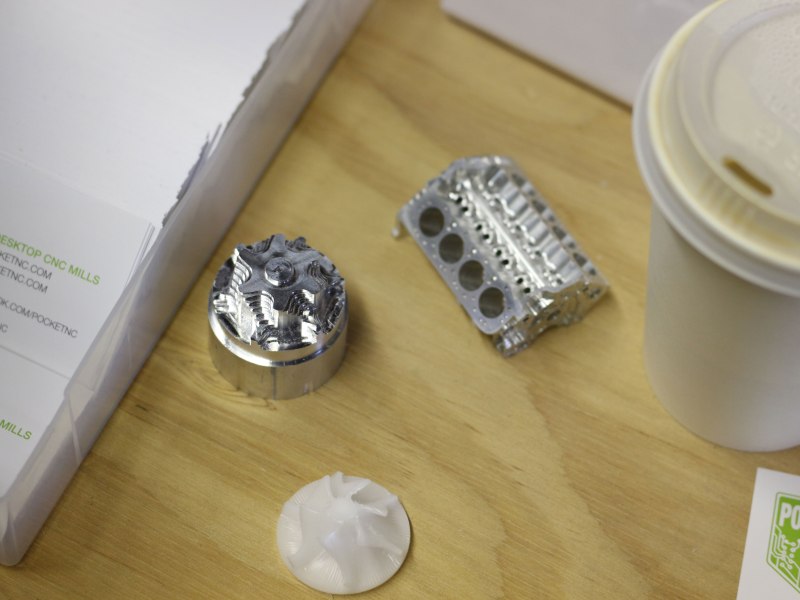
It’s easy to get jaded with the Kickstarter and IndieGoGo scams that are out there. Or even the disappointing behavior of projects that could be legitimate. People often do failure analysis of companies, but it is also worth investigating what people did right when they are successful.
A while back there was a company called Lumen Labs. Lumen Labs promised the cheapest gantry CNC on the market. In Lumen Labs defense, they really did have an amazing product. It was the largest, cheapest, most precise CNC mill for the money, and if they had only sold what their shop could produce they would have been fine. However, they set no order limit, soon orders for thousands of bots were rolling in. What seemed like good fortune was their death knell. Since they didn’t take into account the actual cost of their machining times and the machines they were being machined on; they didn’t have the real price of the build. Their margin was negative. With no way to expand but to buy more machines and get more people, they quickly ate through all of their capital. Today Lumen Labs is a blank page on the Internet and a few favorable reviews on the Make Blog.
Pocket NC, however, made none of these mistakes. Matt and Michelle run the business as a husband and wife team. Neither of them are lightweights, Michelle having spent some time as a mechanical engineer in aerospace and Matt having similar accolades. Matt came up with most of the design, but he credits Michelle with the success of the business. She insisted they estimate their costs and potential overruns as precisely as possible. Only once they knew in minutia the cost of every component, machining step, and potential set-back could they accurately price their machine for a successful Kickstarter campaign.
The first step, and this is one many campaigns don’t get to before launch, was to complete the design. The device was thoroughly iterated until they had a real 5-Axis machine. Next came the important bit. They constructed a few Pocket NCs and timed every step. They knew how long it took to do the machining, wiring, testing and assembly down to the second. Using this information they further optimized the design and repeated the process. This method of iteration left them with not only a sound mechanical design, but a thorough understanding of the cost of their machine.
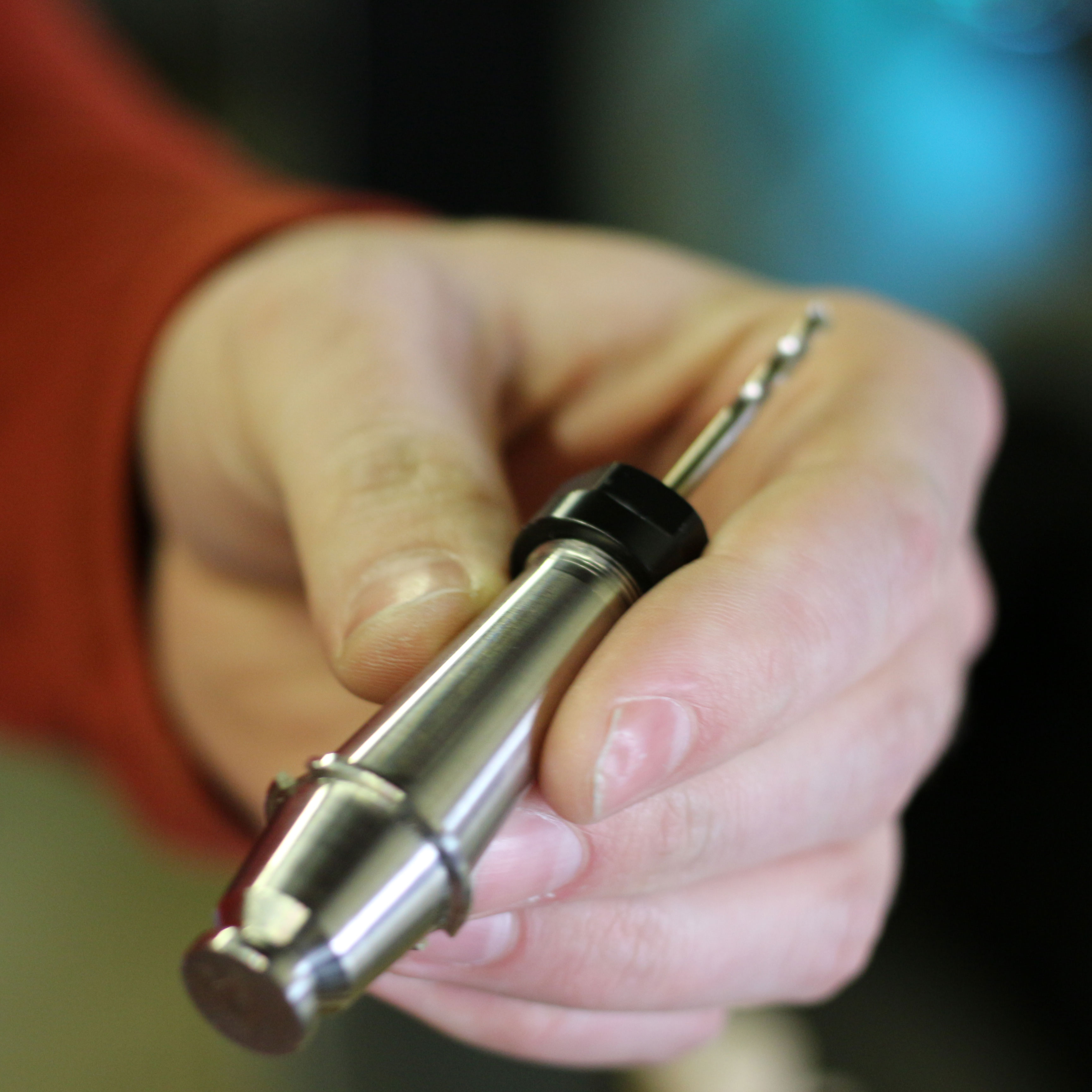
I remember finding it odd, when the campaign launched, that they had set a maximum on the amount of machines they would sell. Isn’t the point of a Kickstarter campaign to raise many boatloads of money and sail into a golden sunset on a shimmering ocean of cash? Remember Lumen Labs?
Michelle had carefully calculated the cost of each machine and the maximum amount of machines they could make with the capital on hand. Rather than falling victim to Lumen Labs downfall — finding themselves backed into a corner where they couldn’t escape without finding more capital, raising the price, outsourcing (which is always risky), and dropping quality — Pocket NC would be guaranteed capable of producing the machines estimated.
In the end a house was sold, a couple moved across the country, and at one point a year may have been spent living in a parent’s basement. However, business is good, they’ve survived where other’s haven’t, and Pocket NC is taking orders for more mills.
> backed into a corner
I see what you did there…
I somehow missed the PocketNC. It seems to be a pretty cool machine, though out of my budget right now. Seems like a great buy for a hackerspace.
I’m impressed to hear how much planing they put into their project before hitting KS. We need more of that out of hardware KD campaigns. And capping orders seems like a great plan.
I agree with the statement that more kickstarters need to do this. The “worlds first $X printer” is one of my biggest pet peevs, they do not account for anything outside of the BOM. Time is actually your highest BOM cost for many of these projects.
Even tho I can’t personally afford a Pocket NC nor the CAM suit to use it, I absolutely love the design and I’m really glad to hear it has been a success :)
When I was looking into CNC it was on my short list all be it more on the wishlist side. Then I started pricing out the CAM suites that could really handle a 5Axis. Which was also about the time cat decided to bless us with her super friendly nature. Which in itself wouldn’t have been so bad if she hadn’t had a massively infected eyeball, which she would rub on you like she was trying to pop it. She became a very expensive free one eyed cat.
I have a cnc machine, it doesn’t bring me love like my cat, I thought it would, but then I learned speeds and feeds, surface feet per minute, bit flex, and much more fun stuff that… isn’t fun and makes me look at the machine with contempt sometimes before starting a cut.
I had the exact same problem. After building my own large scale CNC machine (4 axis + lathe…), reading 20 some odd books on speeds and feeds + machining tricks, I realized I may have bitten off more than I could chew. I have a LOT of respect for professional machinists now. A LOT of respect.
and now that you have a tabletop cnc you can use it to make a pocket sized cnc
This is how gray goo gets started.
I heard you like CNC’s so I CNC’ed a CNC inside your CNC so you can CNC while you CNC.
(Good Gawd! That actually works!)
you forgot the “Yo, Dawg!” part…
Reminds me of the song…CC Rider.
You didn’t think that a $4000 cnc with a 5 inch cutting area could possibly exceed the cost of parts??? In that case, it’s possible that you’re trying too hard to peg enterprises as crooked (aka witch hunting). That has been my suspicion about Hackaday since you first started doing those crass hit pieces on these little start-ups before they’ve even done anything wrong.
No. As a working professional, I pegged it as very unlikely that a brand new company could keep a profitable margin on the manufacture and design of such a machine. I say this because it is a very hard thing for even experienced companies to manage. I never accused anyone as crooked or evil. I simply saw them as attempting a very hard thing to do and succeed. To be honest, if I had the money at the time, I would have backed them as I was very excited for the project. Perhaps you’re looking for a villain when there is none… isn’t this called witch hunting?
Is this a hit piece in your eyes? Is there some previous hit piece on Pocket NC on HaD? Did you wake up on the wrong side of the bed this morning?
I can’t believe how angry some HaD readers get about stuff that only seems to exist in their own minds.
I like to think we don’t run hit pieces. We’re certainly not out to doom a small company that is just getting started.
When there are obvious laws of physics which need to be accounted for in the performance claimed from new products I expect the company to address these. When they don’t it’s appropriate to start the conversation “how is this possbile?”.
The tone of the site has changed in a big way. The content feels more like Buzzfeed or other sensational headline factory that posts 200 times a day than Classic HAD. The OC makes a good point IMO since the whole article premise is that the project must be a scam, and the reveal is that they did a good job. Under the old editorial model of HAD this would be reversed.
This is only one of many basic rules of writing that are broken all the time on this site. Where I once read 3 out of 4 pieces on the blog now it’s more like 1 in 20 because trudging through poorly written, unilateral views from writers who have poor understanding outside their own experiences isn’t enjoyable. Reading project posts is much more satisfying because there is less agenda on the part of the writer.
I have ten years exp. in B2B and B2C writing on complex topics, it’s easy to get into a bubble where you can’t see your overall editorial picture. As a long time reader I can say the current evolution of the site isn’t attractive and that opinion is widely shared among the people I know who read the site regularly.
I am definitely biased, but having worked for Hackaday then and now. In my opinion, It’s definitely better now. I think there may be a case of rose colored glasses.
Here’s the first ever post on Hackaday, a monument to journalism: http://hackaday.com/2004/09/05/radioshack-phone-dialer-red-box/
Perhaps this stunning breakdown of an article on Arduino I/O speed? http://hackaday.com/2010/01/06/arduino-io-speed-breakdown/
Okay, so what about the way we covered things like Makerfaire. Here’s an in depth interview and post from Hackaday’s visit to CES: http://hackaday.com/2010/01/07/ces-parrots-ar-drone/
Another: http://hackaday.com/2010/01/07/ces-roboard-robotic-hand/
Compared to what we have now. This post, for example. Or this one: http://hackaday.com/2016/06/03/1575-bottle-of-beer-on-the-led-wall/
You have to remember the law of averages. HaD publishes more articles in a day now, than they did in some weeks. More great articles, and more shit.
I find the style, tone, or agenda of some articles much more abrasive than I remember HaD being, and perhaps that needs some work. I believe its just that there are more cooks working in the kitchen than there used to be, and that’s not entirely bad.
I do agree with you though. I recently called out a writer (Jenny List, ‘Free Radio on my Phone’) for posting a piece that sounded exactly like the copy-pasta the National Association of Broadcasters has been posting all over the internet, about the importance of having working FM receivers in our cell phones. That kind of agenda laden op-ed stinks, and you can instantly see it for what it is.
Jenny is a life long professional who specializes in high end audio and radio. Why wouldn’t she naturally tend towards wanting a radio in her phone? We get to pick our topics. It would be like getting mad at me for evaluating the manufacturability of a CNC machine. (I’m a working design engineer who also writes; why wouldn’t I be able to make that evaluation?)
Hackaday is generally credulous to a fault, in my opinion. Certainly they dont run witch hunts!
Which scam KS did you run?
If it was a Ferrous or titanium alloy, that would make sense (it would probably add an extra zero to the cost), but aluminium is a poor choice ( https://en.wikipedia.org/wiki/Fatigue_limit ).
Selling a device that will fail after a specific amount of use just seems wrong to me. But maybe I am living in the past, and not part of the disposable generation.
Sherline Machines are very long lived. They’re all aluminum. So are airplanes, trucks, engines, etc. It has already been proven to be a good working material and the actual sliding parts (bearings) in the Pocket NC are all steel. Aluminum is an excellent choice.
There are a lot of machinery out there with aluminium parts and in no way does aluminum=disposable!
Everything is disposable, the difference is the failure mode.
The Aluminium=Disposable mentality comes from the iPhone followers. They see the “unibody” frames of the “disposable” phones and laptop and they relate them for some reason. Well, what can we do? You are right, aluminium is a great choice. The simple fact that the resistance to corrosion that it has is enormous.
I’m happy to live in the “disposable world” of flight where most aircraft that have been built are inherently limited in lifespan by fatigue. A structural element in a machine tool that is seeing stresses high enough to drive material selection based on fatigue life has bigger issues than eventual failure- it is going to flex and chatter horribly.
I wouldn’t do aluminum either but the biggest drivers are things like a low modulus of elasticity and a high coeffecient of thermal expansion.
If the stress is very low then the number of cycles is very high. For example DC-3s that were built during WWII are still flying cargo runs in Alaska today. Cessna 172s and Piper PA-28s built in the 1960s are still flying today.
Copper also has a fatigue limit. How often do you see a wire break from it in your home?
If they used 430 stainless steel the cost for the actual material would be a lot less than AL6061 but the machining would be more difficult.
Precision milling requires the machine to be extremely stiff. High stiffness implies very little strain in the structure. At very small strains, aluminum is good for many billions of cycles, which means thousands of hours of 20,000 RPM milling. Detailed below, the stress is so low in this design that it’s out past the tested limits of cyclic fatigue.
Let’s look at the likely strain. According to their specs, Pocket NC’s bit deflects between 0.3 and 1.0 microns per Newton. That’s actually a bit wimpy, but that’s hardly a surprise, because stiffness costs money.
You can think of that deflection as the sum of the deflection due to each component in the path from the workpiece to the bit. Most deflection will come from the bearings or ball screws and so forth, all of which are made of steel, and particularly steel chosen for its hardness (stiffness). The remainder, perhaps 0.1 microns per Newton, will come from deflection of the structure.
I don’t have a pocket NC in front of me to measure, but I’d guess the path from workpiece to bit through the machine is on the order of 40 cm. Typical cutting forces will be around 10-50 Newtons. So at most we’re talking about 5 microns of deflection over 40 cm, which is 12 ppm. I just buried a bunch of FEA into a single glib sentence, so you know there are ways bad design could lead to early fatigue, but barring those we can still make some general statements.
12 ppm strain in 6061-T6 aluminum (69 GPa Young’s modulus) is around 850 kPa. If we look at the stress/cycle curve on page 13 of https://www.osti.gov/scitech/servlets/purl/10157028/, we see that 6061-T6 can do 1 billion cycles of way more stress than this. On the prior page, 1 billion cycles endurance was tested at 20 to 48 MPa, dependending on the load. The stress in the Pocket NC is between one and two orders of magnitude less.
The bottom line is that milling machines are dominated by stiffness, and cost is dominated by the time spent shaping the parts. In that design space, 6061-T6 aluminum is an excellent choice. Steel would be worse, as it would have corrosion issues and cost more to cut to shape.
That is one very impressive little machine! I’ve never heard of PocketNC before this, but now I really want to find a way to justify buying one.
I remember seeing that someone had bailed out of the lowest priced reward tier during their kickstarter. It was soooo hard to not click that link…
It would have only been a second mortgage on my remaining kidney… but then again, 5-axis on my desktop…
Having been handed my hat in way too many technology innovations, I want to see how this holds up under real-world use first. Those metal chips appearing to be going into the stage mechanisms made me cringe.
I can confirm that it exists, we have one at the Ultimaker office.
It has not seen much use yet, due to CAM difficulty, and difficulty of attaching your stock material to the bed.
I’ve been following Matt and Michell for a while now and couldn’t wait for the KS to launch. I was one of the first round backers. What they been able to achieve on in terms of sustainable development, both business and engineering, shows an all too rare degree of professionalism in startup-landia.
Pocket NC 5xAxis machines are very impressive and wholly unequaled at this price point. For most people Fusion360 is practically free and does the 3+2 CAM needed for the machine. There is a substantial learning curve, which will be quite steep if you are new to CNC machine tools and CAM. Software UI/workflow could use some work, but I’ve been spoiled.
I’ve machined precise small aluminum parts with oil mist coolant, and dry machined wood, wax, and plastics.
For the sake of semi full disclosure, at the time of the launch, I also was working as a mechanical engineer for another desktop CNC machine company.
I lol’d about fatigue limits for the AL6061 frame. For rigidity and minimal deflection to maintain machine accuracy, the frame has very large cross sections where cutting loads would result in high stress. As a result the stress in any zone that would fatigue is well bellow the 3x rule of thumb.
It’s important to note that 3+2 is vastly different than simultaneous 5 axis when it comes to the actual CAM and way the part is cut. 3+2 locks the A and B axes while XYZ are free to move, the AB axes are simply indexing. I know that a lot of this is due to the CAM suite, as 360 doesn’t offer full 5 axis simultaneous yet. IIRC, it didn’t even offer 3+2 when they launched the KS, it was only 4th capable and they were waiting for Autodesk to “be there yet”. Coming from a machining background, I have difficulty seeing where this will fill a niche that exists.
True, it is indexing for now, but indexing at the angular resolution the axis, which is some 0.025 degree. I’d love to see full 5-axis in F360, it sure would allow for much nicer finishing strategies, I hear it’s “in the works” Which is hilarious. IIRC, HSMWorks basic package is only 3 +1 or +2 and 5axis is premium.
Wow.. Full on product lust.
Its SOOO Cute.. It looks SOOO well made! The people making it sound soooo neat! Wow.
Wish I had 4K to spend on such a device.
Software to program it is a non-trivial issue though.
Color me impressed.
OK, now I want to know what HaD thinks of the Allforge.
I really have to question the new spindle design. They were using nice little NSK spindles but they seem to have rolled their own now, I assume to save money. I would like to see a cross section of the spindle, it just does not seem like a great design, especially with the stickout of some of the tools.
I thought the same thing at first! But after seeing the machine at Maker Faire I was blown away… The new spindle has way more clamping force on the tool because it uses the ER11 collet system and the tool holders have a solid grab as well. I think they went to this system because it has way WAY more benefits over the old system!!!
A friend got his PCN on time as advertised. The funny thing is at the same time we are learning the software side of a Bridgeport J head CNC conversion we did. The Pocked NC has been an interesting distraction from the centroid. It’s been a good learning experience.
Simple said the PNC is beautifully made. The Hardware is A class, clean machining, great parts and wonderful assembly. The software Xming, PuTTY SSH client and MachineKit not so much. Putting a side Fusion 360 year subscription open source is how they delivered the PNC for the price.
Where PNC are proven at designing building and delivering a GREAT product. They really need help in there instructional material. They lost sight who there customer is “Hobby” and didn’t spend time in HOW DOSE THIS WORK factor. The 3 videos on there site is WAY to complicated for a first time “get it up and running” project. This is not for the faint of hart, you will need to stick with this to make it produce something of value.
WARNING: Setting up a CAM file is MUCH harder then slicing a STL, MUCH harder.
IMO: This is just a toy, beautiful but still a toy. I have no idea what to use it for. It’s just to small. For the money buy a used cnc mill and don’t worry about the other 2 axis.
Resin casting high precision plastic parts! http://hackaday.com/2016/02/09/learn-resin-casting-techniques-duplicating-plastic-parts/
I agree, you don’t need the extra axes. I have a 4 axis and still haven’t used the fourth axis.
Wow.. Full on product lust.
Completing the product and timing the build process is a great thing to see that ALL kickstarters should be required to do before launching. While mine wasn’t successful, i did complete the product long before the kickstarter and timed the build process and costs so I could make sure I’d be able to deliver rewards in a timely manner.
Thanks for the article. Estimating the complete costs is common sense (although easily overlooked or botched). Limiting the order amount was something I hadn’t thought about. It makes a lot of sense, though. I’ve bookmarked this page for future reference if I decide to launch something on kickstarter.
First time to this forum…I’ll never be back.
Another company that was successful on kickstarter was 5axismaker. But pocketNC got the mindshare and 5axismaker didn’t. Even though 5axismaker is lot bigger than pocketnc and at comparable price. One disadvantage is 5axismaker is a british company. 5axismaker.com
why is being british a disadvantage? is it the import tax
Is it better to spend the money in the PocketNC or in aliexpress machines?