The handheld screw driver is a wonderful tool. We’re often tempted to reach for its beefier replacement, the power drill/driver. But the manually operated screw driver has an extremely direct feedback mechanism; the only person to blame when the screw strips or is over-torqued is you. This is a near-perfect tool and when you pull the right screwdriver from the stone you will truly be the ruler of the fastener universe.
A Bit of Screw Driver History:
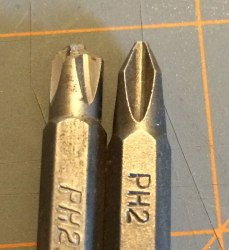
In order to buy a good set of screw drivers, it is important to understand the pros and cons of the geometry behind it. With a bit of understanding, it’s possible to look at a screw driver and tell if it was built to turn screws or if it was built to sell cheap.
Screw heads were initially all slotted. This isn’t 100 percent historically accurate, but when it comes to understanding why the set at the big box store contains the drivers it does, it helps. (There were a lot of square headed screws back in the day, we still use them, but not as much.)
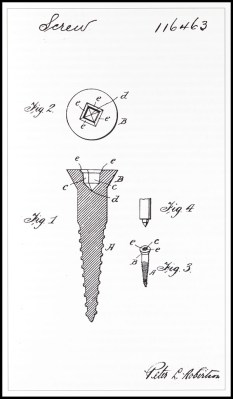
Flat head screws could be made with a slitting saw, hack saw, or file. The flat-head screw, at the time, was the cheapest to make and had pretty good torque transfer capabilities. It also needed hand alignment, a careful operator, and would almost certainly strip out and destroy itself when used with a power tool.
These shortcomings along with the arrival of the industrial age brought along many inventions from necessity, the most popular being the Phillips screw head. There were a lot of simultaneous invention going on, and it’s not clear who the first to invent was, or who stole what from who. However, the Philips screw let people on assembly lines turn a screw by hand or with a power tool and succeed most of the time. It had some huge downsides, for example, it would cam out really easily. This was not an original design intent, but the Phillips company said, “to hell with it!” and marketed it as a feature to prevent over-torquing anyway.
The traditional flathead and the Phillips won over pretty much everyone everywhere. Globally, there were some variations on the concept. For example, the Japanese use JST standard or Posidriv screws instead of Philips. These do not cam out and let the user destroy a screw if they desire. Which might show a cultural difference in thinking. That aside, it means that most of the screws intended for a user to turn with a screw driver are going to be flat-headed or Philips regardless of how awful flat headed screws or Philips screws are.
However, since the Phillips screw unequivocally sucks at its primary job (turning a screw into something without exploding), lots and lots of inventors set-out to design a better mouse-trap of a fastener. Unfortunately, they all did a really good job and no single useful standard has come out.
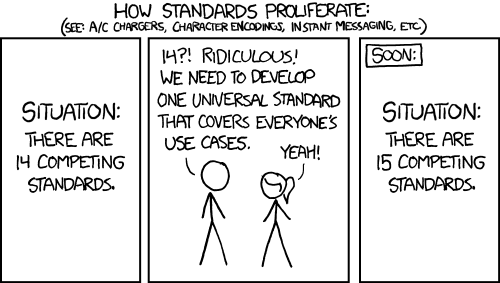
Though, you can break them down into three categories. One is the category of fastener that’s designed to transmit as much torque as the user wants without destroying itself. The second is a fastener that’s meant to flummox the user as much as it possibly can. We know these as security screws, and they are hated. The last category is the rare fastener that’s designed with the actual fastening as a useful secondary consideration. For example, aerospace actually has a Philips-type screw that’s designed to ruin itself if over torqued. I’d also throw thumbscrews in this category. They’re usually awful screws, but you don’t need a tool!
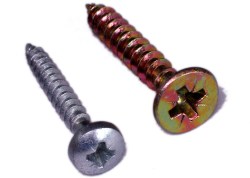
Now that all this history is out of the way, we can make a few determinations. If the Philips screw cams out when too much torque is applied, we need a Phillips screw driver with a precisely ground head and sharp geometry to bite into the metal. Another example determination we can make is that not all plus shaped screws are Philips screws. They do have pretty easy markings though, for example, most of the stripped out screws on an unfortunate piece of test equipment I tried to take apart had a little X intersecting the head pattern. This X indicated that the screws were in fact Posidriv screws, and no amount of cursing would make them properly compatible with a #2 Philips. Flat head screws are to be used for decoration. Hex headed machine screws are to be used with a ball headed driver when torque is low and flat headed driver when torque is high. I won’t go on and on, but I guess I’m making a case for doing research on the fastener. It tells you a lot.
Okay, What Else?
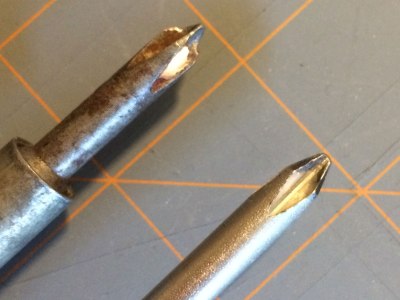
A screw driver, at the end of the day, is a consumable. The cheaper the screw driver, the faster it will be consumed. What drives the price up on the screw drivers is the hardening and tempering on the driving element, as well as the precision with which it was ground. A Snap-On screw driver will last many years; an import store special cannot offer the same promise.
Any feature built into the handle of the screw driver is likely to be a gimmick. I find that the simple hard plastic grip screw drivers offer the best control, even in greasy conditions, over the strange rubberized contraptions some companies try to foist as a must-have feature. Also, the rubber tends to develop a truly awful odor after they’ve sat in a tool box for a few years. I am, however, excepting rated insulated handles from this list.
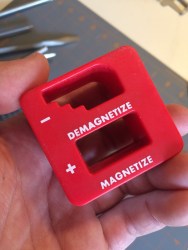
Magnetic tips are nice. I find it’s more useful to own a simple tip magnetizer and demagnetizer so you can add or subtract the feature as needed. I also like to use a school glue stick applied to the end of the screw if I really need to finagle a fastener into a difficult spot. It tends to hold more reliably than the alternative.
I’ve heard that some people like ratcheting screw drivers. I think these people have problems, but when they do work, they do work.
At the end of the day it’s the bit that touches the screw that’s important, not the stuff behind it. Look for things that have sharp grinding on the geometry of the screw driver. You shouldn’t see any rough, wavy edges with tiny chunks taken out of them. A screw driver should definitely mention that it had been hardened. Also, many of the coatings do help prolong the life of a screw driver. I find that chrome plating that go all the way to the tip are usually useless and will chip off unattractively within the first few minutes of usage.
Help! I’ve Made It This Far In Life But I’ve Never Purchased a Screw Driver. What Should I Get?
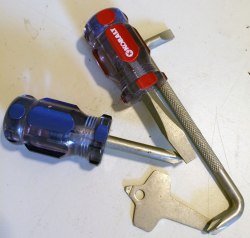
Expect to spend somewhere between 20 and 40 US dollars on a decent set. Don’t be lured in by a lot of accessories.
In my opinion, the most complete set for everyday use is as follows. One set of the three common flat-head screw drivers. Under ANSI, these are #1, #2, and pry bar. Results may vary in different countries. For Phillips the sizes are the small one that doesn’t fit anything (#1) , #2, and cheater bar (#3). I’d also recommend getting one of each of the #0 sizes. These will fit almost every screw found on a laptop or small electronics.
I generally find that the screw driver that fits is the one that looks like it’s just a bit too large for the bit. Along with these I’d recommend picking up one bit driver and a set of bits. This will cover you for all the innovation that’s occurred in the past years.
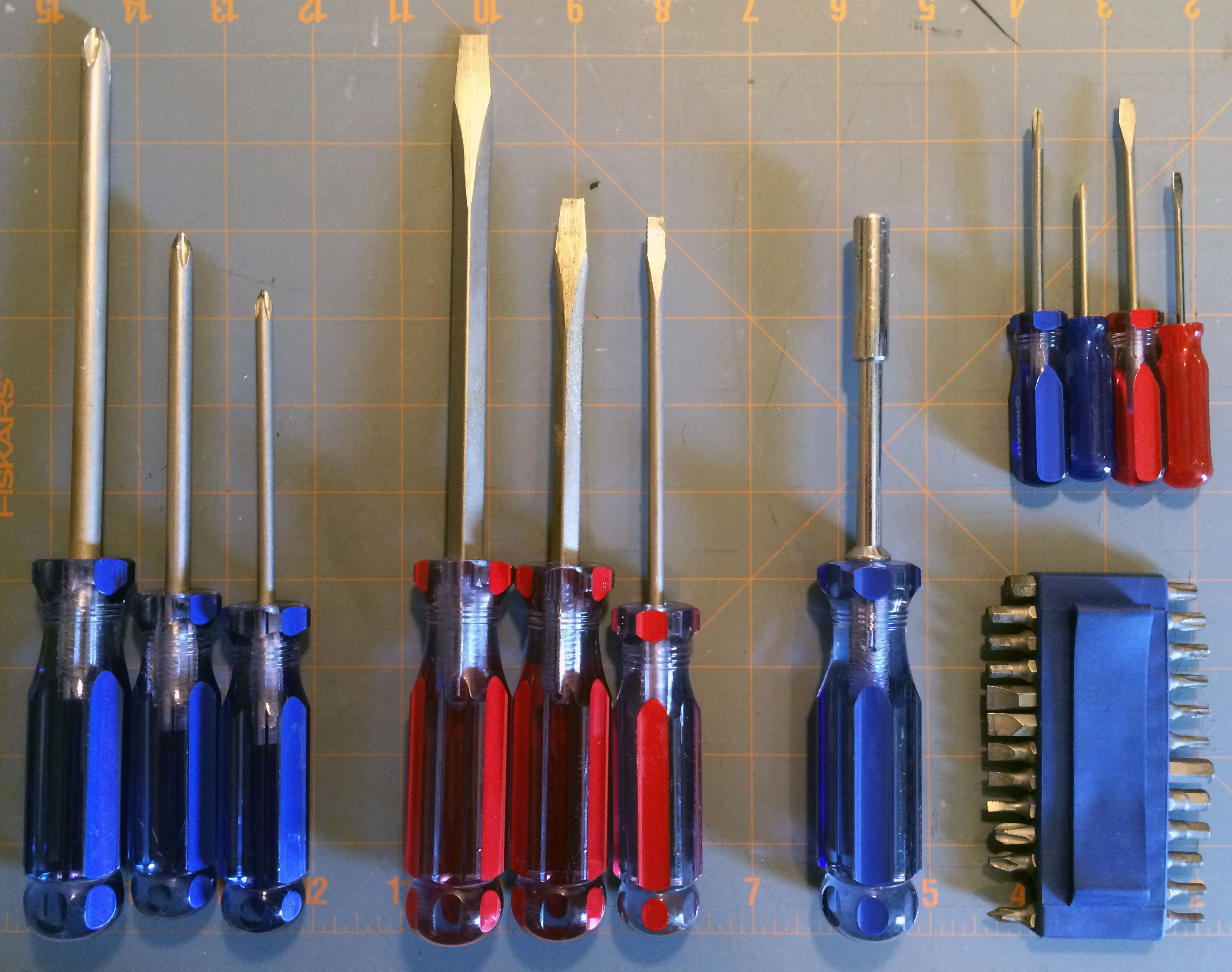
The cheapest set is a simple 4-way combination screw driver, the two #0 size screw drivers, and a set of bits (since they fit into the combination screw driver). The only downside to this set is that the combination screw driver will occasionally be too large to fit inside a recessed hole.
Lastly, a nice set of very small screw drivers is nice. From experience, though, usually small sets are a scam to trick hackers out of money. Don’t cheap out on these and get the dollar store set. If you do, the little flat blade will immediately bend and the tiny Philips will strip out the screw you’re working on. Moody tools and Wiha sell a nice set.
Hopefully that was useful. I’m sure we have a few screw driver experts and historians out there. I’d love to hear more in the comments.
Edit: As some have pointed out in the comments. The technically correct term for a “flat head” screwdriver is “slotted.” Huh, guess I’ve been saying it wrong all this time. Thanks everyone!
Referring to slotted screws and drivers as ‘flat head’ in an article like this is doing everyone a disservice, since ‘flat head’ refers to a screw profile as well.
+1 I am actively trying to purge “flat head”, the name I learned as a child for “slotted”, from my vocabulary in this context. As a result of working on a pinball project with way too many fiddly types of screw requirements, I’m trying to learn and use all the correct definitions of screws and screw parts. Took me a minute to parse your use of flat head as a synonym for slotted, as you wouldn’t expect that in an otherwise deep dive.
You’re right. I learned me some real bad english growing up in East Tennessee. It shows up every now and again. I will try to get my terminology right in the future.
From my youth: a flat-BLADED “goodubbie”.
It’s not just Southerners. Up here near Massachusetts seems like all the carpenters call it a ‘flathead’, and so did I.
Until this article. I’m surprised at the ‘semantics nazis’ this week, but I shouldn’t be!
Does anyone have a good animated gif of a screwdriver? ;)
absolutely. screw heads come in deiiferent flavors such as flat, pan, round, oval, etc. screw driving mechanisms come in different flavors too such as sotted, phillips, clutch, torx, robertson, etc. don’t confuse the two. to define a screw, you need to define the head shape as well as the drive mechanism. you also need to describe the threads, but that’s a different article all together.
I agree, although growing up I was always taught that those kind of screws were called “common” screws. Guess thats another term to throw in to the terminology bucket.
+1. I agree although growing up I was always told that those types of screws were called “common screws” instead of flat head. Only ones with an actual flat head were called flat head screws, didn’t matter what bit they used.
For those of us who are trying to unlearn “flat head,” I like “flat blade.”
What an idiot about your Robertson comment. I didn’t have to read any further to know you have no clue what you’re talking about. Go worship at the foot of your Ford.
I’m well versed at using the term “flat head” as well. I worked at a tech repair shop for a couple of years and I always heard the term flat-head. From my experience even automobile mechanics (my friends atleast) use the term flat-head as well. If I asked them to toss me a slotted screw driver I’m not even sure they would know what I mean. lol
Nonetheless, good article on screwdrivers.
I’m surprised that the fabled, “Jeweler’s Screwdrivers” were not mentioned, at least in that context. I change watch batteries, and often use what might be, in another environment, a
“-1” Phillips for those very small screws holding some watch backs in place. And, inside some watches, there are even smaller screws. You know, like a real Jeweler has to work with while servicing a mechanical watch.
Some watches, after the insult of 4 or 6 screws holding the back in place, have two more inside, holding a battery clamp in place. I can’t begin to guess the number of screws I’ve launched into that “BLACK HOLE”, while trying to put one of them back in place.
Phillips sizes get smaller with additional zeroes. A 00 is smaller than 0.
Maybe it’s just the fact that I’ve grown up with metric units for everything, but having “sizes” where “size 0” is a non-zero width seems bizarre. Why not just specify the diameter of the driver?
” I can’t begin to guess the number of screws I’ve launched into that “BLACK HOLE”, while trying to put one of them back in place.”
Get yerself a plastic lunch tray (yeah, like from a cafeteria). Line it with a towel or a piece of soft cloth. Do your disassembly on that tray. Screws don’t bounce off towels or cloth.
And those Wiha drivers are sweet. Expensive, but sweet.
Best advice i was ever given was start with the biggest screw driver and work your way down till you find the one that fits tightly.
Its all to easy to start from the smallest and end up with a stripped screw.
Use Torx everywhere!
I love the Torx. I have saved so many from HDD disassembly.
Often nice screws, but mostly useless for other projects if not metric.
This!
When it comes to using a impact driver or drill/driver for construction or in the woodshop, I definitely prefer either Torx or Posidriv. Actually, I think the Posidriv is a bit better at not stripping out (in a situation where I generally want the screw and tool to win out over the material). Using regular Phillips head screws with a drill/driver sucks.
This is where Robertson comes in for Canada
Indeed. If you’ve never used Robertson screws in your life, you don’t know what you’re missing.
Yeah, this… Once you have realised that all major screw types (including woodscrews) are available in Torx and that torx screws require no axial force on screwing (or more importantly, unscrewing) using anything else seems ridiculous. Both for power and handtool use, anything smaller than M6 should be torx, anything larger either hex head or socket head.
Ahem, and M6 itself?
For M-6/MI-6, use a James screw. I’m told it’s a hell of a screw and it’s certainly the only one that gives that trademark bond, a James Bond.
Traditionally, there’s only been a male bit, but I hear they’re working on a female Bond, which would be an even more interesting screw for my applications
I try to use Torx everywhere but everywhere I look I see Philips screws.
Good article, I have a couple screwdrivers recommendations:
Best ratchet drive I’ve ever used, it has a simply amazing action and feel to it compared with other crappy ones I have:
https://www.amazon.com/Megapro-211R2C36RD-13-Ratcheting-Driver/dp/B004VJY1EC?ie=UTF8&ascsubtag=SH672&linkCode=xm2&tag=thesweethome-20
Autoloaders are also great when you need to change bits often and don’t want to lose bits, it stores 6 bits in a chamber in the handle and you can switch between them easily.
https://www.amazon.com/Hi-Tech-Electronic-HTP-2000-Autoloader-Screwdriver/dp/B002FQ6BGY
“Believe it or not the “Robertson” screw came out before the Phillips. Robertson just hated money and didn’t want to license his patents. So it’s only now that they’re in common use again.”
I don’t know for others countries but here in Canada we have been using it for decades. The Robertson head is the standard construction screw except for gypse panel where the Phillips seem to be the standard.
In the US (at least where I’m at) square screws are also used frequently in construction.
I have them holding the concrete board on under my kitchen tile, and they are standard for any kind of deck screw.
Don’t know what people are using for framing any more since most of that is pre-fab now. Back when my house was built they used nails.
Not for framing, they are used for flooring almost exclusively up here.
They are the de facto head for electrical uses (breakers, sockets, switches, etc). Much better than the classic slotted terminals we used to have!
The ones I *really* love are “electricians screws”… with the combination slot and phillips on the same head. See them everywhere from circuit breakers, power outlets, etc. Supposed to work with slotted, pozidrive or phillips drivers, but doesn’t work for any of them!
The rotten things popped into existence about ten years back because dumb**** electricians are so lazy they can’t select the right driver for the job, they just reach into a toolbag and pull out the first damn thing with a handle and a long metal rod attached to it.
Ban them. The screws that is… not the electricians (although maybe…)
There are special screwdrivers for these screws
http://www.1-2-do.com/wissen/userfiles/image/sd_plusminus.jpg
That enraged me so much.
Robertson got fucked over by a British company that tried to play a shell game and receive a very liberal license on his design. He freaked out and spent pretty much his whole fortune buying back the rights to his own design (!).
He refused to let Ford manufacture them, wanting exclusive control… So Ford passed and went for the Phillips head design.
Robertson drive is superior to Phillips for any kind of application where you don’t want cam-out. It’s just as good as hex and torx, without the complexity of torx, and it retains the screw better than hex.
Would it be safe to say that he got screwed?
Oh yea he really did, and not only did Ford pass on Robertson he was so incensed that anyone would go against the great Henry he said any suppliers that used Robertson screws in anything they made would not be able to supply to Ford, he basically froze Robertson out of the largest screw market in the world! If there was any justice or logic in the world the Robertson screw would be the standard screw of the world. (What, I like the Robertson screw, hey if it was good enough for Mrs. Robertson…)
PL Robertson
https://en.wikipedia.org/wiki/P._L._Robertson
A this screw Head is Light years better than Philips
You might remember these similar, but much more popular ones:
https://upload.wikimedia.org/wikipedia/commons/0/07/Inbus-Schraube.jpg
Mr. Robertsons genius isn’t entirely lost :-)
Hahaha. Win.
Pretty good article!
Finding good quality is indeed the challenge and to date the most reliable indication of quality I could find is, well, the brand. Costs easily $10 for a single driver, but that one will last longer than a 10-pack of cheapo-chinese stuff. And it won’t do the worst a screw driver can do: damage the screw head even if properly used.
These typical 15 pcs. sets for $2 are better used as a paperweight. They do more damage than good to screws.
Very true! But I did find a good cheapo set; the bits are excellent but the case was a warped, unlockable mess.
I can recommend the brand Wera screwdrivers. Currently I use these http://i.ebayimg.com/images/i/331754875255-0-1/s-l1000.jpg
Yes! I love this set!
Flat head screwdrivers can be further categorised, ones where the sides of the blade are parallel and within the profile of the shaft and ones where the blade is inexplicably flared to be wider where it meets the shaft the only purpose of which is to stop you from using it down small holes.
Stanley sell and market sets with both types so there is apparently a difference.
Klein calls that a cabinate tip.
On the handles: My favorites are the Craftsman red and blue handle sets. All the slot heads are red and all the Phillips are Blue. I’ve got various others around but I always grab the wrong one from the bag because the handles all look alike from a distance
Craftsman handles stink. Oh, they have an OK grip, and the shafts don’t seem to tear out, but search the term Craftsman with “cellulose acetate butyrate” and you’ll see what you’re in for. My Craftsman set is so old that all of them are the red handles on clear–I have no idea when they started color coding them.
Same deal with the vintage “Excelite nut drivers” or “Excelite handle with interchangeable nut drivers” sets. Some tools I misplace and have to search for a very long time to find, the Excelites require only my nose. Awful, awful smell, but distinctly limited to plastic tool handles so identification of it is quite easy.
On the other hand, I’d wear a cologne made of the smell of vintage electrical tape (essentially the smell of vintage cloth-based band-aids).
Two equally distinct smells, likely not too far away from each other on the Periodic Table of Stink, but one is sickening and the other oddly pleasant to my nose. Go figure.
Philips #1 can be used to unscrew posidriv #2 without damaging it. :P
My Wiha screwdriver set is the best. Has torx and hex as well.
Ha, I was looking for someone to bring Wiha up, the best screwdrivers there is. They proud of their drivers, but there’s a reason for that pride. I have yet to replace a single driver, and some of them are over 10 years of age, still look and feel brand new!
I took out hundreds of screws today by hand. totally possible, but I can see why those electric screwdrivers are popular :P Good article though, always fun to examine something we take for granted.
Does anyone know where I can get a set of long good quality Philips screw drivers?
I fix these motor controllers that have a bunch of small rusted metric screws that hold the cover to the heat sink:
http://www.wolftronix.com/amc325_0044/images/IMG_6083.jpg
The ones I have are made in china and can take out about 4-5 rusted screws before they go bad.
Thanks,
Wolf
Take “quality” screw driver which isn’t quite long enough.
Find steel pipe/tube with ID which is a near friction fit of the driver shaft OD.
Need angle grinder & welder.
Hopefully you see where I’m going with this.
I work in a profession that isn’t writing. I, in fact use the tools in this article EVERY SINGLE DAY as part of my job that I have been doing a long time. Oh, and my job requires specs for the very fasteners used, very, very specific specs, including torque. I don’t have time to point out everything wrong with this article, but all I can do is shake my head…. Please do your own research… Don’t rely on some guy who seems in writing at least to have a background in mechanical engineering, yet seems to know very little practical knowledge of fasteners or the tools used on them other than how to search Wikipedia. You’ll thank me when you’re older…
I will say that those skinny handled hard plastic craftsman screw drivers are shit. Complete shit. If you want your hands to hurt after about five minutes of use and to spend more time fishing for tools than torquing screws, go ahead, buy a set.
A larger handle that has a slight amount of give or cushion to it gives you far more control. When you are loosening a screw that is too tight, you want to transfer as much power as you can into it right up front, else the tool bit slips and strips. Think about how an impact driver works…. A screw driver that you can get a good, non-slip grip on is what you need…. That’s why the craftsman PROFESSIONAL line, which you probably can’t afford has softer, larger diameter handles.
This is more fodder for those poor unknowing souls who shop at sparkfun and ada fruit and think they are getting a good deal….
You didn’t have the time to point out everything wrong with the article, yet you had plenty of time to vent and suggest that the non-professional (us) aren’t worthy of the knowledge you don’t have time to share. Why bother commenting at all?
+1
What do you propose the comment author be paid for his or her time in service of researching and writing what the original article should have included originally? Why contribute time to a community that shows no respect? I fully understand the OP’s point of view and point out that your response has little merit and is meant as intentional vitriol.
At best he offered a differing opinion from the article wrapped in a lot of posturing. I am very open to the idea that I can make errors, and I like it when people point them out so I can change my knowlege and fix the article. Take the flat head vs. slotted discussion. It’s a mistake I didn’t even know I was making! Neat.
I enjoyed the article. I don’t throw away bad screwdrivers i grind them into: Awls, Ice-picks, scribes, & etc.
Totally agree about the quality of content on this site going downhill fast. There was a time when I would use the values in a HAD article as confidently as I would use an official data sheet.
This is another Buzzfeed-type article from this writer who I doubt even has a workbench. I am a graduate school educated professional writer and can say that it’s not easy to do quality work at the rate HAD is pushing out right now. It looks like it’s a click game and traffic metrics are all that counts. There are some really simplistic mistakes in fact as well as in structure in this piece. It’s no wonder some of the impressive guest writers have not returned when this site has become so crappy content-wise. Thanks for your input since the comments are often much more informative than some articles and include missing or corrected information.
Considering past criticism of self-help crap that was foisted on the wrong audience led to me being scolded by this writer for my “machismo”, I expect to be banned or attacked by other member of the do-nothing-write-something armchair engineer crowd for giving actual honest feedback so these are likely my last days visiting HAD which is sad.
Flathead v.Slotted?!?
Are you really threatening to leave because an article on tools pushed you over the edge? Sounds like you may have a few screws loose.
I write my articles on a workbench I built myself… for the record.
Nah. That’s either earthquakes or the 3D printers shaking the whole workspace.
Hah! It’s pretty sturdy… compared to workbenches I’ve built in the past. I am improving my woodworking game slowly:)
@notarealemail
Both are possible in my house and the pacific northwest:)
You are dead on the money. I worked in a shipyard and one submarines (ex-sub-sailor here) and the drudgery of this article really irks me. Klein makes some mighty-fine tools, and I could add a number of other suppliers, but I won’t. Don’t even get me started on gun-smithing screwdrivers, which usually offer the absolute best fit on any screw since the tiniest slip-up means a mark or damage on a multi-hundred dollar firearm stock. Aside from that, conventional Philips head screwdrivers can be “resurfaced using a regular mill-cut file and some patience. Any real mechanic will hack his own tools for the job… IE: heating the shaft or shank of a screwdriver as per the needs of the job.
We (professional mechanics) often have The Nice Set, a cheaper set, and then the “buy at Harbor Freight specifically to mod/hack/destroy” set. (Or in my case, about a half dozen sets). Ratcheting screwdrivers are a godsend, especially offset bar-handled min-drivers for tight quarters. T-handle ratcheting drivers are also very useful, especially when working in “off-grid” locations such as the middle of a long snowboard run and adjusting your friend’s bindings on the board he rented. Then of course there’s Spinner screwdrivers (Klein all the way!)- when working with conduit runs or regular 120/240/277 voltage runs, you NEED these or you will have dead forearms. Side note: next time you are at a salvage yard and somebody asks for a screw-driver, hand them a spinner. Hilarity ensues as they stare at it.
In other words: do your homework. The #1 Philips badmouthed in the article is perhaps one of the most heavily used by anybody who works on classic ATX (or variant) computers.; # 2 in construction, #3 in shipyards and large mechanical/industrial capacity. Don’t let a writer with obviously limited experience in handtools provide guidance on the tools, other than taking it with a hefty sample of NaCl.
Slow news day??
What do you mean? Hackaday is the only place where you can get the best and most riveting discourse on subjects that matter, like screwdrivers.
Riveting! Now that’s a subject I’d like to know more about.
PS: i enjoyed this article, more please!
Why some screwdrivers stink up your whole toolbox:
http://dwarmstr.blogspot.com/2013/02/why-toolboxes-and-tool-handles-stink.html
What about the white mold that grows on such plastic? I have stripped the handle in acetone and it still grows back. I feel that lacquer or shellac would wear off rather quickly. I don’t like to handle flaky or mold-slimy handles. A humid summer seems to bring it on, perhaps the desiccant inside is a good idea. Those can only capture so much H2O, after that they are saturated. They need to be baked out to be able to capture more moisture.
Also worth noting, hand impact drivers are great for removing stuck or partially stripped screws. Looks like a fat screwdriver, but when you hammer the end it turns a little bit.
Fun fact for those of you with newer Hondas:. If you change your own oil, you’ll probably have taken some tin snips to the useless metal skid plate panel under the oil pan by now because the 4 Phillips screws holding it on were over torqued from the dealership and stripped out.
Those aren’t Phillips. They’re JIS.
Not just newer Hondas. Pretty much all Japanese motorcycles since the 60’s use JIS screws. This is why so many older Japanese motorcycles have stripped screw heads all over the bike.
I haven’t seen it mentioned that slotted screwdrivers are meant to be ground to fit the screw head you are working on today… basic knowledge.
Out of all the screwdrivers I have – including that really worthless craftsman set pictured, Klein has been the best. The tips do not wear.
I also have a cheap set of insulated Chinese made screwdrivers that show no wear after years of use in electrical situations.
It’s actually a more worthless Kobalt set:) Made to imitate the Craftsman set. I just take good care of my tools so I can’t seem to wear them out enough to buy a new set:/ Hacker problems, haha.
+100 for Kline and Wiha. Between the two of them, you’ll not go wrong and you’ll pass most of them along to your grandkids (or some other lucky schmuck if you’re child-free)
After working for an electrical contractor for an extended period, I must say my Klein screwdrivers are the only ones that i now own. The increased price was offset by the gasoline saved on running to Sears to replace broken tips every weekend????
Yeah, I remember running to Sears for replacements. Around 1970, I was a shop mechanic and had one long skinny Craftsman that was great for adjusting carburetors. I broke the tip doing something stupid, ground it back into usefulness and eventually took it back on on of my regular migrations for replacement.
Well the sales fellow shook his head and said, “Sorry no, can’t replace it — it’s been modified.” Then with a sparkle in his eye walked over to a vice mounted on a bench, clamped it down and reefed on it. He held up the broken screwdriver, smiled and said, “Now I can replace it.”
Thanks for reminding me …
Regarding the term “flat-head” I’ll weigh in. My father who was an airplane mechanic taught me the term “straight-blade screwdriver” to refer to the driver used in slotted screw heads. This seems more correct because it is a blade-like, is straight, and that end of the screwdriver doesn’t really resemble a head. (Isn’t a head round, even if it’s flat on top?) In reference to the screw itself, slotted screws can be flat or round when you look at them from the side. Phillips, Robertson, hex, Torx and nearly every other variety can be flat or round, and there’s also “pan-head”, sort of an elliptical profile. And in nearly all other screw-and-driver contexts when we refer to the head, it’s in reference to the head of the screw, not the driver. But no worries. Words are not sacred cows and I’ve learned to cope. But I’ll still say “straight-blade” in reference to the driver or “slotted” in reference to the screw.
Oh another thing — if you trash the head of a Phillips or Robertson screw trying to remove it, here’s a trick: take a dremel and turn it into a slotted screw head. Hopefully you can remove it without the straight-blade screwdriver stripping it.
Damn. That’s such a stupid simple solution I’m not surprised at all I never thought of it. Haha. Great trick!
That’s what we always called them around here too… straight screwdrivers.
When a Philips head screw is rusted in, a very useful tool is an ‘impact driver’. Place the driver in the screw and then hit the handle with a hammer. An internal ramp twists the screw at the instant it’s being driven into contact with the screw head. It works beautifully, and is the only thing that I found that could extract Philips-head bolts from a motorcycle crankcase.
BTW, one of the nice things about Robertson screws is that you can place one on the screwdriver and drive it with one hand. Very handy if you are working at the top of a ladder.
Hit the offending screw with a quick shot of Kroil first. Wait 5 minutes. Apply impact driver. Smile.
Robertson is the best screw. The only one where you can hold the screwdriver pointing downwards (one hand free), and the screw will not fall off of it, even without magnetization. I buy them whenever I can.
Here is a good pic:
https://en.wikipedia.org/wiki/List_of_screw_drives#/media/File:Robertson_screw.jpg
https://upload.wikimedia.org/wikipedia/commons/thumb/f/fe/Robertson_screw.jpg/561px-Robertson_screw.jpg
I’m surprised at the lack of Europeans gloating about the ubiquity of Pozidriv screws here. Maybe you all don’t know how good you’ve got it?
The Phillips head is so lousy — I curse every time I have to use one now. In contrast, I smile every time I feel the Pozidriv lock in on a screw. It’s as if they were made to work together. It’s a fundamental quality-of-life issue, like good cheese.
PZ4Lyfe!
Pozidriv was jointly patented by the Phillips Screw Company and American Screw Company so technically it is a Phillips (done right.)
I’m surprised no one here has mentioned laser tip screw drivers. http://www.toolstation.com/shop/Hand+Tools/d10/Screwdrivers/sd80/Wera+Kraftform+Plus+Lasertip+Screwdriver/p93334
because of the ridges on the tip you get a lot of grip (much more than normal)
using them actually feels kind of weird because of the amount they grip the screw
By far the best screwdrivers in my toolbox are my late father’s old flat-heads with wooden handles. Simply indestructable and very comfortable to work with. Wish i also had some Philips screwdrivers like that.
And agree 100% on the small set tip: don’t buy the cheap ones; they’re all rubbish. I’ve inherited a professonial set that’s 50+ years old and still in excellent working order.
Lemme throw my two cents in I guess. Slotted screwdrivers ARE called flathead screwdrivers in the Southern States in USA. I grew up in a machine shop in Houston, we modified engines, guns, instruments, and everyone in the shop would ask for a flathead if they wanted a slotted. And funny enough, we always knew the difference between a flathead screw and a flathead screwdriver. Even the buzzy old fart in the corner fine tuning his mini steam engine. Jenny’s are called pliers, and cops are called constables. SO WHAT. Learn your regional as well as your technicals, because you may need to work with a local who is very important to your project, and will not feel like investing anymore into the snotty guy who can’t even run a decent flathead.
Also, speaking of the crappy old flathead screwdriver, there are tapered and hollow-ground and flat ground. All flathead screwdrivers are not the same, and basically, in our shop, the tapered were for gate hinges and opening paint cans. Hollow ground are precision fit to the screw, and very effectively transfer torque to the head.
I did not grow up an electrical engineer, and when I meet them in my friends hacker space, I tend to giggle at their ideas of good tools, but I keep my mouth shut. I learned about good cheap nippers from them, so yeah, we all got stuff to learn from everyone, even those poor saps who think a straight bladed screwdriver should be called a flathead.
Seems to me that screws in imperial sizes are bought with Robertson heads when rest of the world with metric screw sizes are mostly using torx.
Bosch Ixus and a proper pair of Proxxon bits is the weapon of choice for me
BTW I hate security screws. They just slow you down.
Yikes, I’d never considered the difference between pozi and philips in any great detail before, but now you mention it I have had instances of damaging screws, and perhaps I now know why.
Honestly the different types of screwdriver heads confuse the hell out of me. I mean I know what they all look like but I have no idea what they are actually called. Always a huge head ache