[David Brown]’s entry for The Hackaday Prize is a design for a tool that normally exists only as an expensive piece of industrial equipment; out of the reach of normal experimenters, in other words. That tool is a 6-axis micro manipulator and is essentially a small robotic actuator that is capable of very small, very precise movements. It uses 3D printed parts and low-cost components.
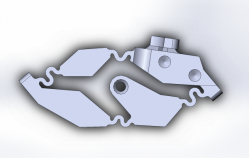
The manipulator consists of six identical actuators, each consisting of a single piece of SLS 3D printed nylon with a custom PCB to control a motor and read positional feedback. The motor moves the central pivot point of the 3D printed assembly, which in turn deflects the entire piece by a small amount. By anchoring one point and attaching the other, a small amount of highly controllable movement can be achieved. Six actuators in total form a Gough-Stewart Platform for moving the toolhead.
Interestingly, this 6-Axis Micro Manipulator is a sort of side project. [David] is interested in creating his own digital UV exposer, which requires using UV laser diodes with fiber optic pig tails attached. In an industrial setting these are created by empirically determining the optimal position of a fiber optic with regards to the laser diode by manipulating it with a micro manipulator, then holding it steady while it is cemented in place. Seeing a distinct lack of micro manipulators in anything outside of lab or industrial settings, and recognizing that there would be applications outside of his own needs, [David] resolved to build one.
Interesting. I hope there will be a followup posting when this is working.
A lot of great entries lately but when is someone going to make a voice coil actuated magnetically levitated stage? (hint! hint!) ;)
Hope for follow-up and many more details…
I liked your project =)
You could also look at spring steel (plastics are dimensionally unstable with temperature), and 3 Digital Dial Indicators with serial data output (about $12/pc on ebay for +-0.01mm with a 12.7mm range).
Some great advice on compliant Flexures:
http://dspace.mit.edu/handle/1721.1/39879#files-area
Variable resisters may be a bit of a disappointment for what you are trying to achieve.
;-)
Thanks,
Yes if i had access to EDM machine then metal would be the way to go, but plastic is much lower cost, and more accessible. It should be possible to fabricate the parts using FFF in nylon filament (experiments needed).
I dont need repetability, just the ability to move very small distances and hold position for 30 seconds whilst the UV cure glue does its thing. So variable resistors are fine for re-setting to the nominal mid-home position and getting a rough feed back of distance moved, as the number of steps will be counted to keep a record of the position.
Note that Cross-strip flexure hinges are often just spot welded or clamped onto mild steels…
If the specific unhardened-state alloy is too hard on C5 Carbide tooling, than chemical etching or water-jet also works. One could also just laminate mirror part copies if kerf proves an issue for a notch hinge.
I still don´t personally understand how the recorded-position is repeatable if the Kinematics changed.
After all, I am only a guy that gets to buy pricey toys form Starrett =)
However, I look forward to seeing how the design performs, and will ponder about the design a bit more.
*nods* mMMM. *sigh*
https://ibb.co/hCcevF
I too want to find a method to position fiber in front of laser diodes and would be very interested in further details. Same requirements for repeatability – only needed while the resin dries.
single stepper with linear rail can have 0.002mm accuracy
https://youtu.be/o4PX10Hz9x4
https://en.wikipedia.org/wiki/Waldo_(short_story)
“I don’t like you.”
hxxp://www.dailymotion.com/video/x2jignc
Ain’t I the lil match maker though. *insert lame emotion here*
What are some use cases for this aside from positioning UV fibers?
Pretty much any case where the cost of high precision actuators such as piezo stacks or alternative fabrication materials are too high, or where equal behaviour could be achieved with much larger apparatus, but where there is a overall access / size constraint.
Right but what are some examples? I’m not normally moving around such small sized stuff so I have no idea what it might be used for. But I want to learn. Grin
Manipulating cells or tissue specimens (like sucking out the nucleus from a cell with a capillary). Aligning micro-optics. Positioning microscale objects (like beads on a surface). Aligning electrical micro-wires or tiny SMD components. Applying adhesives or solders very precisely. Positioning force or temperature sensors at the microscale.
Note that these allow controlling both rotation and xyz position. Very useful.
Ho fine does the positioning need to be? I have a couple mechanical stages from old Zeiss microscopes. Would they work? https://goo.gl/photos/dDnFVV7AWKDMNkvx7
Based on the diameter of the fiber (105um) positioning needs to be in the region of 5-10um. One of the main issues is to also get the angular position as well. In order to get the end of the fibre aligned and positioned you need 5-axis of movement, the 6th is rotation about the beam axis which is irrelevent.