If you are in the habit of seeking out abandoned railways, you may have stood in the shadow of more than one Victorian iron bridge. Massive in construction, these structures have proved to be extremely robust, with many of them still in excellent condition even after years of neglect.
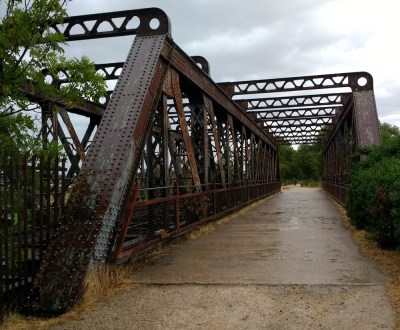
When you examine them closely, an immediate difference emerges between them and any modern counterparts, unlike almost all similar metalwork created today they contain no welded joints. Arc welders like reliable electrical supplies were many decades away when they were constructed, so instead they are held together with hundreds of massive rivets. They would have been prefabricated in sections and transported to the site, where they would have been assembled by a riveting gang with a portable forge.
So for an audience in 2018, what is a rivet? If you’ve immediately thought of a pop rivet then it shares the function of joining two sheets of material by pulling them tightly together, but differs completely in its construction. These rivets start life as pieces of steel bar formed into pins with one end formed into a mushroom-style dome, probably in a hot drop-forging process.
A rivet is heated to red-hot, then placed through pre-aligned holes in the sheets to be joined, and its straight end is hammered to a mushroom shape to match the domed end. The rivet then cools down and contracts, putting it under tension and drawing the two sheets together very tightly. Tightly enough in fact that it can form a seal against water or high-pressure steam, as shown by iron rivets being used in the construction of ships, or high-pressure boilers. How is this possible? Let’s take a look!
How Rivets are Formed
The above simple description of the process leaves out a few details. Rivet snap and set tools — heavy solid steel formers to fit both the straight and mushroom shaped ends of the rivet — are used on both ends of the rivet, on the mushroom end to hold it in place while it is being hammered, and at the straight end to hammer the sheets together with the snap and form a smooth new mushroom shape with the set. Thus a typical riveting gang such as that working on a railway bridge would have included two people working on the rivet itself, one on either end. Sometimes the person holding the set on the mushroom end would have to crawl into confined spaces such as inside a boiler to perform this task.
In the Victorian era the work would have been all done by hand, the rivet shaped by repeated blows to the set by a hammer, but from the early 20th century onwards a typical riveting gang would have used a hand-held pneumatic riveting gun. If you think of the tool Rosie the Riveter was often depicted as holding, you’re in the right place. However as the video below from 1949 shows, the scene would have otherwise changed little from the Victorian era, with the operator of a small forge tossing glowing rivets up to a worker who catches them in mid-air before placing them in the hole to be forged.
https://www.youtube.com/watch?v=CVjS1DsqYvo
Swapping Rivets for Welders or Bolts
In 2018, you are only likely to encounter this type of iron rivet being used in heritage restoration work or in work that is intended to emulate it (The aviation industry uses rivets, but not quite the same as the ones you’d find in boilers or railway bridges!). Even then, as for example with the boiler on the new-build steam locomotive Tornado which was welded rather than riveted, it is by no means a given that rivets will be used. You can see a video of a modern-day riveting gang installing a boiler patch at LNWR Heritage in Crewe though, typical of this kind of riveting work. It’s ironic that even one of the most iconic riveters was pictured at a time when the practice was dying out, Rosie the Riveter’s portrait appeared while American shipyards were embracing the welder. Structural steel with mating holes is still used today, but high-strength bolts of a quality unavailable during the height of riveting have completely taken the place of rivets.
Speaking personally as a Hackaday scribe, my dad had occasional need to rivet as a blacksmith. Done by hand with the set positioned in the hardy hole of an anvil it was a more difficult job for an enthusiastic teen than you might expect, and I remember more than one attempt that emerged with distinct play in the resulting joint. I suspect I hadn’t managed to keep my rivet hot enough and thus its contraction had been less than it should have been. The rivets we were using were smaller than the ones in the videos after all. Perhaps if there had been handy online tutorials back in the day I’d have had more success.
Header image: Simon Lee [CC BY-SA 2.0].
Most modern aircraft still use rivets. They are aluminium, and squeezed, without heating them.
Some rivets are pulled (pop like rivets).
Isn’t there something to do with compression, tension, torsion, etc. forces where rivets are better than say welds in wings or I’m guessing screws also? I might be wrong… just a thought.
I recall boat manufacturers using screws to align the pieces then unscrew as they place rivets in as I guess rivets are cheaper than screws with maybe a smoother surface also if exposed.
Yep, riveting is pretty great- unlike welding, which is mostly just an “edge treatment”, two pieces of metal can be held together with rivets that extend several inches from the edge, which is really hard to do with welding, especially when you don’t want there to be an extra thickness between the sheets.
Welding is still used in the airplane industry, though, on stuff like landing gear.
Welding aluminium is not easy – the temper of the alloy is unpredictably affected by the heat. Welded aluminium structure is extensively tested for inclusions, cracks, material properties etc…
Rivets are often used in structure under compression because the rivet swells to fill the hole, and therefore the whole cross section is effective in compression. A bolt, no matter how tight tolerance in the hole, will never entirely fill the hole, so is not normally considered effective in compression.
Rivets are pretty much never used for out of plane tension applications though.
Makes sense, thanks. Kind of duh moment also since the structure wouldn’t be easy to heat treat I’m thinking if welded to be aircraft aluminum quality now I think what you noted more.
Another big issue with welding in aero is inspectability. Like Alex noted, aluminum welding is fraught with issues that can cause poor weld quality, and so most aerospace welding requirements (AWS D17.1 for ex) demand visual inspection, surface inspection, and volumetric inspection.
Volumetric inspection usually takes the form of X-ray, which is basically impossible to do on anything other than a butt weld.
Since weld material is weaker than parent material, the weld cross section has to be much thicker. Then you don’t want the rest of the part to be as thick as the weld so you have to machine it down.
Basically welding usually makes for expensive, difficult to make parts in aerospace.
There are many reasons why newest aircraft increasingly use glueing instead of welding (like Boeing 787 or Airbus A-380).
I assumed the like for silicone came from when my Dad was in the USAF or Reserves. I know he mentioned one or more improvements they made to the KC-135’s for survivability.
Welding aluminium s relatively hard, it changes the properties of the metal and is hard to inspect / repair. Also a crack can propagate along a weld, whereas it will (hopefully) stop at the next rivet-hole.
nice article, video is blocked till you open it in you tube.
ditto
Small rivets are pretty much impossible to hot-set, they just cool down too fast.
But steel rivets up to 1/4″ can be readily set by a hydraulic squeezer, and you can make one for about £90.
https://bodgesoc.blogspot.com/2014/04/hydraulicrivetsqueezer.html
Back in the day, they had bigger ones: https://www.practicalmachinist.com/vb/antique-machinery-and-history/hydraulic-riveter-111732/
They still do. Don’t get much use, but they are out there, maintained, and made to special order but a couple of firms.
Interesting stuff in both your links. It’s somehow reassuring to know people with that knowledge are still around. Gives me a feeling there’s still some grownups around, somehow, so if the idiots populating the place today ever mess it up too bad, we can all call for society’s dads to come put it right again.
It’s not true of course, but it’s reassuring!
Something I don’t think I see in the article: Part of the robustness of riveted joints comes from the swelling of the shank when the end is peened. The mechanical force on the ends shortens and fattens the shank in the process, so not only do you have a mechanical “head” on each side, but the shank ideally fills the entire cavity and thus reduces corrosion and movement in the joint. (I’m reminded of the article here on HaD about how properly crimped connections deform the strands in a wire, crushing out oxygen and reducing corrosion.)
A few years ago, I did sections for micrographs of rivets at one of my jobs to prove a procedure. The surveyor insisted that a properly done rivet should completely fill the hole with zero clearance in the section, we argued that a properly driven rivet must have a little clearance, because as it cools and contracts in length, the diameter will also contract, the Poisson ratio notwithstanding. Presented calculations and ended up running samples of fresh rivets and cutouts. The only ones that were complete diametric fill had fractured from being driven black brittle, and had overdriven heads (so were never maintaining the tension to draw the material together). The good ones all had a few hundredths of a millimeter clearance. Some of the ‘best’ actually had rejectable amounts of fire scale in the interface and offset of 1/4 or more of the hole diameter (early rivets in assembly get pulled around as later ones are done).
In practice, if it doesn’t leak, and it rings tight (UT these days, rather than a tap with a hammer), it is ok, theoretical consideration notwithstanding.
A lengthy piece about a historical non-electronic topic? This feels like a Jenny List article… and it is!
Since when was hackaday limited to electronics?
I think he meant it as a good thing. I’m always glad to see one of these articles between a dozen about badge hacking and people building retrocomputers from 74xx chips
I riveted the holster for a Bluetooth keyboard to the side of my CNC. (Which runs Linux and open-source FPGA code).
So you can mix and match.
And I don’t mean pop-rivets, I mean solid copper rivets set by a hydraulic squeezer. Just because I had them all to hand.
Variety is good. Remember the general forum rule that once we devolve into discussing what does and does not belong on the forum, we do not belong on the forum.
More discussions about ear wax. :-p
Indeed so. But historical? My dad’s a blacksmith, this is present day! :)
If you’ve got half a brain it gets you thinking… like, “Oh, it’s the rivet shrinking that pulls it together firmly, now what if we exploit the memory effect in plastics…..”
Plastics expand roughly an order of magnitude more than metal. I’m not telling you you should never rivet plastics, but it makes more sense to friction weld or mold them in one piece. Injection molding works wonders on plastic.
Ohhhkay, I’ll just leave you to friction weld, mold, or injection mold your PCBs onto things then.
I actually did this to repair my sunglasses. I lost the screw for one side, so I took a length of PLA filament, ran very hot (85C) water over it, pulled the filament until it necked down to smaller than the size I needed (~0.5mm or so), then trimmed it so it was about 3mm in length (with one end a little larger than the other, acting as a head so it wouldn’t fall through the hole). I assembled my glasses frame, put my little PLA rivet in the hole, then ran hot water over it. It swelled back up on each end, filled the hole (but not too tightly), and is still functional to this day over a year of use. PLA is remarkably strong, actually.
Ironically, most of the Rosie Riveters you see (actual) pictures of are riveting aircraft.
I drive over riveted bridges every day. The youngest of which is nearly 100. Never ceases to amaze me.
“If you are in the habit of seeking out abandoned railways, you may have stood in the shadow of more than one Victorian iron bridge. ”
Victorian? I’m sure it was used later than that.
Construction age. We don’t call the pyramids or the Leaning Tower modern structures even though they attract hundreds of thousands annually.
Of course, Rosie had to be a riveter! She just wouldn’t look as tough holding a welding rod.
Not sure what you are getting at there are photo of women welding on WW II production lines Probably more women named Rose than Wendy, at that time, so Wendy the welder wasn’t the best propaganda line.
Exactly that. Rosie had to be -strong- and tough. Holding something about as heavy as a cast iron fry pan and hot as an oven wouldn’t do much for the cause. Holding a freaking heavy riveting tool and being on either side of such force as to properly form a thick chunk of steel? That’s freaking tough!
Rosie wasn’t an icon to romance the Era, she was a call to action, and she had to be -legendary-.
Clickspring is using a lot of cold-peened rivets in his Antikythera mechanism build
The most important thing about rivets wasn’t mentioned in the write up, nor shown in the illustrations, and old silent film. The reason rivets are so effective is the shank of the rivets expand to tightly fill the space they are in. Any one who has work on a sickle bar can tell you how tightly a rivet cold worked using a hammer is difficult to remove. no doubt a hydraulic press is used to set the rivets in the factory, but tools marks reveal when what you are working on has previously been repaired in the farm shop.Even pop rivets expand to a degree, but they are for sheet metal,not structural metal assembly, so that’s comparing apples to oranges.
Wrocław, Poland. 100+ years old, 112/18m still standing strong.
http://www.polskaniezwykla.pl/pictures/original/272587.jpg
St Pancras station is a rather glorious riveted structure too. https://en.wikipedia.org/wiki/St_Pancras_railway_station
The good news: they had earplugs back then.
The bad news: they were also red-hot rivets.
Yep, the person “bucking the rivet” was a “rivet bucker”, the tool was a rivet buck.
I have a few copper rivets and riveting tools that I use occasionally to fasten leather.
Although hollow copper rivets are quicker to use, I also use the solid rivets with a copper washer.
Hence the phrase “bucking the trend”? :)
My Father-in-Law (95) was a Coppersmith in both Naval and civilian life. He has or had rivets in pretty much every brewing copper and still in the UK. Riveting the 3/8″ plates on a still was a four man job – one to heat the rivets, one to *catch* and place them, and two with hammers, one inside the vessel.
He’s now deaf, of course.
This was a fun read. I am a bit of a bridge nerd myself.
Something else that riveted joints (don’t) do to great benefit is transmit fractures very well. If two plates are welded and one of them fails, the fracture will usually be propagated on to the next plate since they’re essentially one piece. Riveted pieces may allow one plate to fail without continuing it – acting as a crack interruptor in a sense – and limiting damage. Aircraft designers are well aware of this, but there are other interruptors that are included in most designs.
The transition from (slow) riveted shipbuilding to (quickly assembled) welded seams with the WWII Liberty Ships highlighted this problem as they would concentrate stress, then fail about the middle all at once. This still happens with oceangoing vessels, river barges and other large structures on occasion.
https://metallurgyandmaterials.files.wordpress.com/2015/12/liberty-ship-failure.jpg?w=640
I posted a picture and article link regarding “liberty ship brittle fracture” to show what happend when rivets were replaced with welding. For some reason the moderators deleted it.
I guess they needed more room for snarky, trolling comments, and bad puns and jokes.
Thanks Hackaday!
I dunno, there’s one directly above your post that might well be the same thing. Maybe it was for redundancy. Although even then they shouldn’t remove posts without a better reason than that. Bit of redundancy never killed anybody.
Counter-example: bloated bureaucracy.
Air stream still uses buck rivets in their rv’s, and my Scamp rv is put together with pop rivets. Not quite the same as the article but similar concept.
Truck frames still has riveted parts on them, one of my first jobs after school was to replace one side of a Scania frame after an accident, as I remember, we heated the rivets with an acetylene torch, and used a pneumatic hammer and a bucking tool.
It was in the late 80’s, I was 17, and the frame replacement was a 24/7 operation ao I did nights to earn some extra cash.
Interestingly, the Golden Gate Bridge in San Francisco is replacing their riveted struts with single piece struts laser cut to appear the same as the original riveted pieces. At reasonable closeness, you can easily discern the old from new from the complete lack of rivets.
My understanding is they reproduced the old riveted struts and stress tested them in a laboratory for earthquake(?) resistance. They tended to buckle under certain circumstance as opposed to the equivalent single piece units. Since the bridge is a major tourist attraction, they opted to retrofit the bridge.
I didn’t think to take pictures of it, but there is an area under the bridge on the South side you can look at the new laser cut struts as well as one of the failed riveted test struts. This page also discusses it a bit of detail: http://goldengate.org/exhibits/seismic-retrofits-and-historic-preservation.php
If it were me I’d probably glue on some pretend rivet heads. They’re as iconic as any other bit.
Same thing with castings, they used to do lot of beautiful castings. The main reason was not because people really liked the process of doing it but because there were few machines that could otherwise produce these parts. It is still true to some of the processes but it is really energy and labor intensive and it makes more sense to mill/turn/lasercut or any other machining to produce same parts. Also the worlds economy has changed since 1900 and it might not make sense anymore to do metal casting for a product, because nobody would buy it at the price which once can do casting.
Sydney Harbour Bridge : over 6 million rivets.
How do you buck rivets anyway? Surely you’re not just holding the round end in place with a pair of tongs or the like, just with muscle power? Wouldn’t it give a little, every time the bloke on the other end hit it with a bloody great hammer? I can understand holding it in place so it doesn’t fall out, but not against a hammer blow.
Did the give not matter, as subsequent blows effectively shortened the length of the straight part?
Well the plan is to have a rivet buck of significant mass, like at least as heavy as the hammer, then inertia helps.
Rivets were partly to blame for the DeHaviland Comet failures. They’d come up with a faster method of punching the rivets through the aluminum sheet rather than drilling and deburring both sides of every hole. Unfortunately the punching process created small tears and cracks around the holes, which when stress cracking from around the too sharp window corners reached a rivet hole, the fuselage would rip apart along lines of rivets.
There were plenty of other design faults, but had they stuck with the slower but safe riveting method, they might have gotten by with nothing more than having a few windows blow out VS the whole plane going to pieces.
in 19th century on large structures such as ships how did they drill holes for rivets to exactly match and align. did they have portable drillls on site?
Excellent information in this Post..keep it up.Thanks for sharing
When I was an apprentice in the 70s we had to make a rachet drill brace for cutting holes in rsjs
Citb off the job training for Mechanical engineers
Now I understand Ray Stanz’s line about cold-riveted beams with cores of pure selenium