Drawn along in the wake of the 3d printing/home shop revolution has been the accessibility of traditional subtractive CNC equipment, especially routers and mills. Speaking of, want a desktop mill? Try a Bantam Tools (née Othermachine) Desktop Milling Machine or a Carvey or a Carbide 3D Nomad. Tiny but many-axis general purpose mill? Maybe a Pocket NC. Router for the shop? Perhaps a Shapeoko, or an X-Carve, or a ShopBot, or a… you get the picture. [Rundong]’s MatchSticks device is a CNC tool for the shop and it might be classified as a milling machine, but it doesn’t quite work the way a more traditional machine tool does. It computer controls the woodworker too.
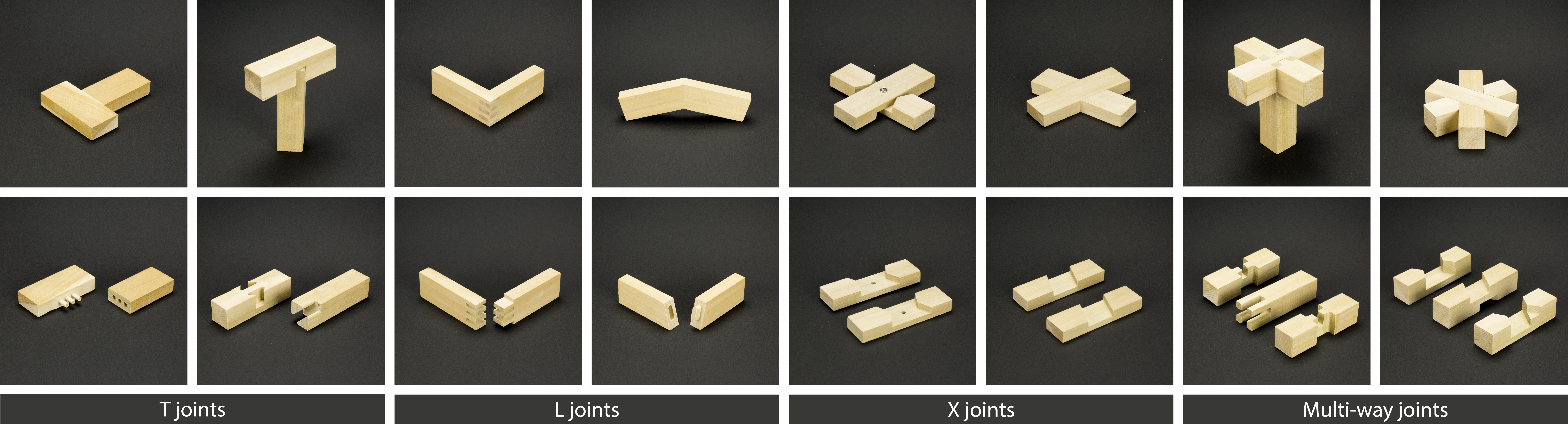
At a glance MatchSticks probably looks most similar to a Pocket NC with a big Makita router sticking out the side. There’s an obvious X-axis spoilboard with holes for fixturing material, mounted to a gantry for Z-axis travel. Below the big friendly handle on top is the router attached to its own Y-axis carriage. The only oddity might be the tablet bolted to the other side. And come to think of it the surprisingly small size for such an overbuilt machine. What would it be useful for? MatchSticks doesn’t work by processing an entire piece of stock at once (that what you’re for, adaptable human woodworker) it’s really a tool for doing the complex part of the job – joinery – and explaining to the human how to do the rest.
The full MatchSticks creation flow goes like this:
- Choose a design to make on the included interface and specify the parameters you want (size, etc).
- The MatchSticks tool will suggest what material stocks you need, and then ask you to cut them to size and prepare them using other tools.
- For any parts which require CNC work the tool will help guide the user to fixture the stock to its bed, then do the cutting itself.
- Once everything is ready for final assembly the MatchSticks will once again provide friendly instructions for where to pound the mallet.
In this way [rundong], [sarah], [jeremy], [ethan], and [eric] were able to build a much smaller machine tool without sacrificing much practical functionality. It’s almost software-like in it’s focus on a singular purpose. Why reinvent what the table saw can do when the user probably already has access to a table saw that will cut stock better? MatchSticks is an entire machine bent around one goal, making the hard stuff easier.
It’s worth noting that MatchSticks was designed as an exploration into computer/human interaction for the ACM Conference on Human Factors in Computing Systems so it’s not a commercial product quite yet (we’re eagerly waiting!). For a much more in depth look at the project and its goals and learnings the full research paper is available here. Their intro video is down after the break.
Thanks [ethan] for the tip!
Love the references to the mills, routers etc. I was just looking for such a thing (cutting front panels would be the main use).
It reminds me to the ghost gun milling machine
can’t wait for this design to be popular andsee people freaking out
It reminds me of this – https://www.youtube.com/watch?v=_rIIYaPYcE0
Dear God, this looks like it’s still in Beta. The UI is absolutely horrible. Seek infiltrated from actual woodworks asap.
Dear Ron, it looks like your still trolling…..
its an ACM/university project, so yeah it probably is in beta (POC)?
For a long time, I’ve had the idea that a small, horizontal CNC router would make for slick mortise and tenon joinery. I’m probably not the only one. It’s cool to see it realized. The software that guides the user and supports a variety of joints is an interesting twist.
It’s like a CNC pantorouter.
This^^ I’ve got a buddy that bought one of those pantorouter kits. Very neat for the time.
Wow, I hadn’t seen these. You’re right it does look like a CNC version. Very cool tool!
Matthias Wandel is a genius with wood. His youtube channel is worth checking out. He’s been featured many times on HaD.
Pantorouters were around and popular long before [Matthias]. I had the pleasure of helping move a 1300lb combination pantorouter / milling machine a couple years back.
Interesting, but not nearly a full featured product yet. The HandiBot (by ShopBot) is much more robust atm, and from what I recall has an open source API to dev with.
*looks up some of these desktop mill names*
*sees bre pettis*
oh no not you again…
… please explain?
bre pettis – an American entrepreneur, video blogger and creative artist. Pettis is best known as the co-founder and former CEO of MakerBot Industries, a 3D printer company now owned by Stratasy
Yeah, thanks … I was aware of the facts. I was just wondering if other people perceive him as … um… “overexposed” like Elon Musk = very charismatic/visible in the media but rather mediocre as CEOs/leader and thus less successful than they could be if they would focus on their products/services…
Naw that’s not my reason. I just remember building makerbot on open hardware/software and then selling out and locking it all down. As such I wouldn’t be inclined to trust a desktop mill sold by him either
Him building maker bot not me (stupid phone)
Is this an open source design? If so where can I get the blue prints?
As a part-time woodworker, I’ve created many jigs to ensure that I can get safe, accurate, repeatable results and to save time when creating larger projects. I built a template-based dovetail jig for cutting through-dovetails, and have built several jigs for creating mortise and tenon joints, including an x-y template-following router, similar to the Pantorouter (but nowhere near that level of ingenuity and execution, and I agree that Matthias Wandel is a genius in this realm, and the Pantorouter is a beautiful and useful machine). I believe that there’s a missed opportunity for a dedicated CNC joinery machine in the woodshop, and the folks behind the Matchsticks device have seized on that. CNC routers, including the Handibot, are not well-suited for executing common joinery tasks in a (though they can certainly be adapted for such as a quick search of YouTube confirms). They’re bigger than you need for many joints, and the cutting axis and stock-holding surface isn’t arranged for cutting dovetails, box joints, or tenons. If you read the paper that is published by the Matchsticks creators, they make this reasoning behind their design very clear (they even acknowledge the Pantorouter as their nearest non-CNC cousin). And, contrary to the comment from one HaD reader, they appear to have put careful consideration into the UI, which to me is the crux of whether an automated joinery tool would be useful. I’ve thought about building a CNC tool for joinery, but I know that I wouldn’t use it if it wasn’t easy to set up and run for different joints and stock sizes – the typical CAD to CNC workflow would offset the benefits of automation in most one-off projects. Since I don’t have the capability to build a really friendly interface to control a CNC machine, I haven’t pursued it any further. What strikes me about the Matchsticks project is that the importance of the UI is well-understood and they’re clearly on the right track. It’s even been usability-tested with a small group of woodworkers, and there’s good inital confirmation that they’re on the right track. I hope that they take the next step and bring this product to market. I also wish that people who take the time to comment on posts like this would also take the time to read the information that’s been provided. Thanks to the HaD and especially to Kerry for finding and sharing this excellent project.
I agree. You covered alot of the points I would have made. Devices like this are interesting in democratizing access to advanced capability tools for those who ARENT inclined to dig deep into CNC territory. (I personally find it interesting, but I can see why people would rather invest mental energy in other areas of woodworking and production) Very interesting option for small businesses who are trying to nail economies of scale.
Vaguely connected concept you may be interested in:
https://www.youtube.com/watch?v=QKlrY33asnE&index=14&list=PLJtitKU0CAehkEO_2bwU6kU59_HvQMb30
Sorry linked the playlist not the video:
https://youtu.be/QKlrY33asnE
Rolling your own joints used to be a Pain
Thanks for the write-up Kerry Scharfglass!
Now that’s different! Could put it to good use in the shop. Thanks for the read.