If anything ends up on the beds of hobbyist-grade laser cutters more often than birch plywood, it’s probably sheets of acrylic. There’s something strangely satisfying about watching a laser beam trace over a sheet of the crystal-clear stuff, vaporizing a hairs-breadth line while it goes, and (hopefully) leaving a flame-polished cut in its wake.
Acrylic, more properly known as poly(methyl methacrylate) or PMMA, is a wonder material that helped win a war before being developed for peacetime use. It has some interesting chemistry and properties that position it well for use in the home shop as everything from simple enclosures to laser-cut parts like gears and sprockets.
Free Radicals
Like many of the polymers that the world is built on, PMMA was first commercialized in the early 20th century. The plastic’s root go back much further, though. Acrylic acids, including methacrylic acid, were first synthesized in the mid-19th century. Methyl methacrylate (MMA), the monomer from which PMMA is built, was first synthesized later in that century, and the first successful polymerization was carried out in 1874.
The key to polymerizing methyl methacrylate is the double bond between the two carbons. That bond is part of a functional group called a vinyl group, where the name for other plastics like polyvinyl chloride comes from. In the case of PMMA, the MMA monomers react together in the presence of an initiator compound, like benzoyl peroxide – yes, that benzoyl peroxide. The initiator’s job is to provide lots of free radicals, or unpaired electrons. The free radicals greedily sop up the extra electron in the double bond, reducing it to a single bond and linking an MMA monomer to the initiator. But the resulting molecule is itself a free radical, which can reduce the double bond of nearby MMA monomers, resulting in another free radical. Eventually, the chain reaction runs out of steam, but not before long chains of PMMA are created.
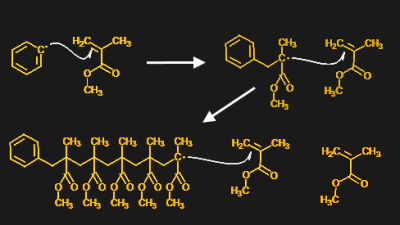
Battle of the Plastics
It would be more than 50 years after the initial polymerization reaction was discovered before PMMA was turned into a commercial product. In the early 1930s, British and German chemists were working independently on PMMA. The British team of Hill and Crawford, working for Imperial Chemical Industries, perfected a method for producing an “acrylic glass” which the company would later market as Perspex. Perspex was lighter, stronger and clearer than regular glass, and as a thermoplastic was able to be pressure or vacuum formed into complex shapes. It was eagerly adopted by civilian aircraft manufacturers to save weight and make their planes more aerodynamic. Military aircraft designers would also take advantage of the properties of Perspex in the run-up to World War II.
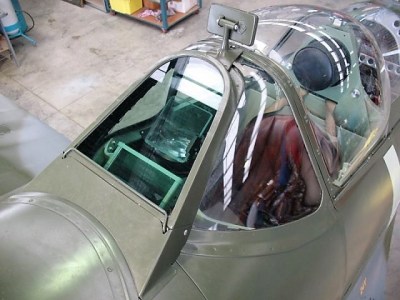
On the German side, chemist Otto Rohm, co-founder of industrial giant Rohm & Haas, took a different approach to his process. He saw the value of a composite of regular glass and PMMA, with a layer of the polymer laminated between two sheets of glass. He thought that if he could run the polymerization reaction between two sheets of glass, the PMMA would glue the whole sandwich together into a solid sheet. Sadly, he couldn’t make it work – the glass always peeled away from the PMMA. But it left him with perfect sheets of acrylic glass, with all the same properties of Perspex. He dubbed his product Plexiglas, and it would find just as many civilian and military applications as Perspex.
Having proved itself in the crucible of war, PMMA was poised to take advantage of the post-war boom in consumer products. Acrylics found their way into everything from kitchen utensils to car dashboards, and as aqueous suspensions, PMMA revolutionized the coatings industry by essentially allowing a durable plastic coating to be painted onto a surface. PMMA was also found to be largely biocompatible and became a popular main bone cement for orthopedic prostheses, such as artificial hips and knees.
Cut It, Bend It, Glue It
For the home gamer, PMMA offers a lot of flexibility in designing and building projects. While PMMA filament for 3D-printers is not unknown, it doesn’t have nearly the followings that PLA and ABS have. PMMA mostly shows up as stock for laser cutters and engravers. Given its optical clarity, it may seem odd that a laser can cut PMMA, but the polymer actually absorbs the infrared wavelengths emitted by CO2 lasers quite strongly, enough to burn right through it. There are many online guides to laser cutting acrylic, but the general rule is to get rid of the vaporized PMMA as rapidly as possible, preferably through a downdraft table. Not only is the gas released toxic as hell – think formaldehyde, carbon monoxide, and the original monomer, MMA – it’s also flammable. Leaving it around to burn will only cause problems. Some laser cutters also use a gas assist, gently blowing the vapors away with a gentle stream of nitrogen or compressed air, to help get an optically clear, flame-polished cut.
PMMA’s susceptibility to organic solvents may be a weak point for some applications, but it makes for easy assembly of acrylic parts. Solvent welding with acetone, dichloromethane (DCM), or trichloromethane (chloroform) is a quick and easy way to bond acrylic pieces together. The solvent, which is often mixed with a small amount of MMA, flows into joints by capillary action and dissolves the two pieces together, forming one solid piece of plastic.
[Featured image: Trotec Laser, Inc.]
The common wisdom for GlowForge laser cutters is to use “cast” acrylic. However, other sources say that cast and extruded acrylic are safe with respect to vaporized components from the laser cutting (cf. PMMA.dk information). Can you clarify?
The issue of cast vs extruded in the laser arena is due to cast can be “engraved” leaving a frosted appearance. Extruded will have a more “melted” appearance.
Nonsense, have you ever tried or are you just spreading rumours?
Extruded has some properties that make it better for lasercutting: it is much more consistent in thickness. You really hate it if one half of your workpiece is not cut all the way trough because it was 0.5mm thicker.
The downside of extruded is that is has a little more inherent tension in it, which may deform your piece when you cut it out of the sheet. But you are getting internal tensions anyway as you’re using heat to cut (vaporise) material.
Just one of many articles. And yes, I have been using lasers for over 30 years in home and in industrial settings.
http://www.pmma.dk/acryl_stobt_kontra_ekstruderet.aspx?Lang=en-GB
That history is interesting. I always though Plexiglas was a US brandname and Perspex a European one. In the US Plexiglas is often used generically kind of like how Kleenex is used for facial tissues. So how did the German name become the popular one in the US? Did the company that made Plexiglas continue to prosper and marketed it to the US after the war? Did the US just take it kind of like Aspirin? Or did the US just take all the people involved with it’s invention kind of like operation paper clip?
It was a patent thin. Developed in ’33 it was protected at first. After that it became a brand.
https://de.wikipedia.org/wiki/Plexiglas#Entwicklung_von_Produkten_und_Anwendungen
German Wikipedia to the rescue!
Dental technician here. We use PMMA for making dentures. Mostly we pack it manually into moulds or injection-mould it, but there are increasing applications for CAD/CAM milling in the dental industry.
Could I have water-clear dentures?
Yes. I’m a dentist and make clear duplicate dentures when I am making a new denture based on the old one. I then fill the clear denture with impression material and take a mold with the clear denture in place ready to go to the lab as where the pink denture wit white teeth is made.
Don’t forget bake laser cut parts to get rid internal stress or crazing will develop soon.
And before you try to vacuform it. The key is to heat very slowly so the water in it doesn’t boil.
I really want to make an aircraft like canopy for a project I’m working on, but getting a sheet that big (and thick) hot enough is going to be a real challenge. Would love to see an article on how others do it.
I would use a double boiler method. Use cookie sheets or large enough container, the bottom one filled with oil. The oil would boil around 300°C. You could heat this with a propane heater or burners pretty easily. The oil should disperse the heat well, and keep it from overheating…
Boiling oil. What could possibly go wrong? #facepalm
I saw something at an air show (sailplanes). Nichrome wire oven draped over a mold results were imperfect surface, lots and lots of sanding and polishing to get a smooth optic.
This may help (or be a good start at least) – PDF
http://acversailles.free.fr/documentation/08~Documentation_Generale_M_Suire/Cellule/Verrieres/Fabriquer_une_verriere/Blowing_your_own.pdf
I take it placing a sheet over a mold and going over it with a heat gun wouldn’t work?
Having a large oven or playing with very hot oil (as referred to in previous replies) don’t seem like things I want to do :(
I suspect that the localized heat source from a gun would likely make it difficult to get an even stretch/shaping across the entire work piece.
The vacuum will tend to pull things the most, wherever the plastic is warmest.
@komradebob There is an abundance of information on the topic freely available. Basically the acrylic manufacturers (Aristech is one example) put as much info as possible on how to form it and what temperature profiles to use etc. Go to Aristechs website and check out the “Technical Library” link on their homepage. There’s enough info to setup your own manufacturing facility. It’s much easier to sell if your customers know how to work with it :) Curbell Plastics also has info. I’m sure there are others as well.
Also, + 1 to what Robert Mateja said. If you want to see the internal stress of a clear acrylic part, you can improvise a polariscope by using the polarized light from your monitor and a sheet of linear polarizing film. Hold the film in front of your face, oriented so that the light from your monitor is blocked. Now hold the part in question between the film and the monitor… The stress in the part affects the polarization (birefringence) and it shows up as whitish cloudy transitions in acrylic. If you look at polycarbonate safety glasses, you can see the stress lines with some color near the stress points, especially if you give them a little twist.
Convenient. I’ve got an item that was cast in an acryllic block a long time ago and would like to retrieve the item intact.
Is there an easy way to get it out with little risk to damage? All I find are how-to’s on ‘casting’, never removing.
I guess it would really depend on what it is that is inside as to whether it would be better to use either a thermal, mechanical or chemical method to remove the acrylic.
It’s his testicles. I’m thinking removing them intact is going to be quite the challenge. What do you think.
Hmm. It’s an old derringer pistol.
I’d probably go mechanical to remove most of it, then acetone to get the remaining.
Go over the outlines very carefully with a bandsaw to remove most of the material.
Then soak it in alcohol for a long time – this will cause the remaining acrylic to crack, and much of it will crumble away. (You can google this effect.)
Then soak the remains in Chloroethane, also known as “methyl ethyl chloride”, which is available in liquid form as an acrylic solvent. It’s used to “weld” acrylic pieces together, go on youtube and look for “acrylic welding” to see how it’s used.
(Be careful! Chloroethane is a neurotoxin absorbed through the skin, and the vapor is nasty as well. I say this and I don’t give warnings about casual chemicals such as acetone.)
https://en.wikipedia.org/wiki/Chloroethane
He’d want to cut pretty wide to start with. What’s the refractive index of PMMA? Wouldn’t want to be fooled on the derringer’s position and end up sawing into it.
Many thanks for the comments. This will be enough information to get me started :) I might just mill some material off and then do the alcohol/methyl ethyl route.
Windex cracks acrylic as well.
Are acrylic fumes toxic?
quoted from article “Not only is the gas released toxic as hell – think formaldehyde, carbon monoxide, and the original monomer, MMA – it’s also flammable.”
so yes.
Well, except that the article is wrong. Very wrong. It’d be almost irresponsibly so, if it weren’t for the fact that FUD on this topic is all over the Internet. Too many armchair scientists, not enough reading/comprehension of peer-reviewed journals and regulatory agency white papers, imnsho.
The vast majority of the (very little) gas released from laser-cutting acrylic is released as MMA. Ever seen an SDS for MMA? Liquid at room temperature, and if you pour it on your skin or stick your arm in a vat of it you should really rinse that off with water right away or your skin might get irritated. Get it in your eyes? To the eyewash station with you! But you would have to stick your head over a big vat of burning acrylic for a while to encounter enough of it to irritate your eyes or lungs. (Or under the vat, I guess – since MMA is denser than air. Though, seriously – don’t do that.)
So, is it toxic? Well, everything is toxic, it just depends on quantities, blah blah blah, so the question is really whether you can produce sufficient quantities of the stuff while laser cutting to be toxic. The answer to that is going to be “no” for anyone not doing industrial-level quantities of it (and probably still no for many who do).
Put another way: you’d think that if a laser cutter could produce dangerous fumes, folks who flame-polish acrylic with a hydrogen torch in open air without full-face respirators would have to be *nuts*, right? Let alone with no breathing protection at all… and certainly no self-respecting commercial plastics business would endorse that sort of thing.
https://www.youtube.com/watch?v=Mmd56UMHDK0
(To get into the weeds of it a bit: folks who work in acrylic production plants are exposed to 25-50ppm of airborne MMA throughout an 8h work day on average, with some peaks throughout the day in the hundreds of ppm, not counting spills and such. The “no effect” level for sustained exposure to it per EPA is 50ppm. As a point of reference to those values, it’s also useful to know that the level at which it can be clearly smelled is around 0.1ppm. All this is in the EPA AEGL document for MMA.)
The amount of formaldehyde produced is a tiny fraction of what already is a pretty small amount of gas to begin with. Carbon monoxide, even less. More importantly: know what else creates formaldehyde and carbon monoxide when you burn it? And almost certainly in larger quantities than laser cutting acrylic does, to boot? Wood.
https://www.epa.gov/burnwise/wood-smoke-and-your-health
Among many other things. Ever use any adhesives? Not white glue or anything. Ya know, the good stuff. Could you smell them? Big ol’ whiff of formaldehyde. Ever been around a smoker, or are one yourself? Have some formaldehyde! Really, burning literally *any* organic substance is going to create formaldehyde. And CO, for that matter. You’ll get a bigger dose of both from accidentally burning your toast in the morning than you will from a laser cutter.
Now, If you’re cutting acrylic with that plastic film stuff still on it, all bets are off — that stuff *seriously* stinks to high heaven when you burn it. Really, most burning plastic gives me a headache, but that stuff is particularly noxious. Peel it off first, for goodness’ sake.
All said and done, I have zero qualms with the “if you can smell it, ventilate it/wear a mask” school of thought for just about anything. As long as they don’t criticize me for not wearing a respirator to a campfire, I won’t ever criticize that line of thought for being cautious to a fault. But needless FUD helps no one.
ps. For any fellow org-chem geeks, if you want to know WAY too much about the byproducts of burning acrylic, here, have fun: https://safetylit.org/citations/index.php?fuseaction=citations.viewdetails&citationIds%5B%5D=citjournalarticle_375852_38 – abstract/citation; the Google Scholar link from there will get you to a PDF of the full text.
I do a lot of engraving on cast acrylic. I am wondering can it cause some healthy issues
I like to use PMMA, but, for any protecting use, DON’T try PMMA, it’s a kind of exploding sharpnels when it fails, and with age, UV and stress, if it’s not very thick, it will fail.
PMMA is a “dry” plastic, for a cockpit or any carter or protection device, I’d rather use a more “fat” plastic, like Polycarbonate, Polyethylene or polystyrene choc (HIPS) that supports better impacts than PMMA.
Whenever you cut PMMA, you must bake it afterwards at low temp (less than 100 ° C) for some hours until all small and big tensions that have been made by the cutting have melted together again, unless it’s been water cut (that’s smooth enough —except for the first impact of the water jet— not to make any tension).
If you don’t bake it, and spread some acetone on it (like you want to clean it a little ;o), il will make some very fancy cracks everywhere in less than a second. I like to do it on purpose sometimes, kind of a punky effect, then I bake it to keep it in one piece).
If yo want a soft finish without hand water sanding for hours, try the oxyacetylene blower, with blue flame, around 2800 ° C, it give’s a very shiny finish aspect immediately… but you need to be very careful just to melt it fast, unless it’ll start to burn and bubble all over.