Every workshop generates waste, whether it be wood shavings, scrap metal, or fabric scraps, and sometimes that waste seems too good to throw away. [Igor Nikolic]’s hackerspace had a ruined circular saw blade in the trash, and rather than let it go to waste he took it to the forge and fashioned a bowl from it. Then because another blade came his way and he wasn’t quite happy with the first one, he made another.
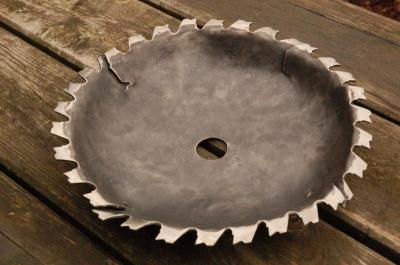
Saw blades are not promising material for forge work, being made of a very high-quality hardened steel they do not take well to hammering even when hot. So his first task was to anneal his blade in a kiln, heating it up and then letting it cool slowly to soften it.
Working the blade into a bowl shape was done on a home-made ball anvil. The blade was marked to provide guide rings as an aid to forming, and the bowl shape was progressively built out from the center. The first bowl was a little irregular, in his second try he’d got into his stride. Both bowls were mounted, one on a cut acrylic base, the other on a set of feet.
A project such as this can only be done with a huge amount of work, for which owners of larger forges will typically use a power hammer. [Igor] admits that a swage block (a specialized anvil for forming such curved shapes) would have made his life easier, but we think he’s done a pretty good job.
If you’ve been paying attention to recent Hackaday articles you may have noticed the start of our series on blacksmithing. We’re indebted to [Igor] for the genesis of that piece, for he was operating the portable forge that features in it.
Saw blades do have really nice metal. Just yesterday I made a 2″ roundover router bit out of one (for routering foam)
They make phenomenal (and angry-looking!) cymbals.
Give a new dimension to “cut my life into pieces”!
The bowl has a crack, a huge hole in the middle, and still incredibly sharp edges. I am trying to imagine what to use it for.
No more carelessly reaching for another handful of snacks, I guess.
This is why I enjoy r/diwhy.
You have ruined my life.
I have just spent an hour there, and I feel that most of my brain has left my body.
The large one is used to hold nespresso coffee cups in the office, and when it runs out, fruit. Hole is not a problem at all. The smaller one has a closed bottom, and is now a jewelry tray. Both were gifted, and recipients love them as they have a incredibly industrial look, but are actually very pleasant to hold and handle. The surface is very smooth, and the hammering gives it a very organic texture. They are coated with beeswax, are nice to the touch and they feel incredibly solid.
The saw teeth are not too bad in terms of handling, as all of the carbide cutting edges fall ff in the furnace, and I sanded the sharp edges, so that they are skin friendly. However, you still do not want to have one fall off the table and on your foot, or be thrown at you during an argument ;)
There’s an opportunity here to figure out what happened to those carbide cutting tips. Certainly they fell off, but then what happened to them? Can you find them in your forge? They might be a little magnetic, because of the cobalt, so if your forge is anything like mine, with a fire-mortar lining, you might be able to fish them out with a strong magnet.
A form of folk artwork, I suppose. I’m a different stroke for different folks,sort of person, but I would have it toss it on the scrap iron pile.
Well, as the saying goes, one mans garbage is another mans gold. And, sure, this is not the kind of esthetics that appeals to everyone. But if you are into industrial styling, this is just perfect on a table as a fruit bowl or so. I have people begging me to make them one as well, and have trouble finding enough discarded saw-blades :) Luckily, somebody just gifted me 20+ really old blades, so there will be a bunch more coming!
No doubt in the right shop you will be able to sell them all. Some time back a kid wanted
A couple of points: the saw blade did not need to be annealed before working, unless it was going to be worked cold, like copper or silver (which is generally not done with iron). A saw blade that was annealed would be no different to work than one that one that was not.
Secondly, a blacksmith should be cognizant of what they are working on. Everyone knows the dangers of heating beryllium copper, or galvanized metal, but tungsten carbide, and more importantly the sintering compound used to bind it present heavy metal hazards for inhalation, and putting something like that in a forge without removing the carbide cutting tips is asking for trouble. This kind of exposure is cumulative, and it is worth every effort to work safely.
The blade he used had carbide cutting edges attached to the tips of the teeth, and those teeth are clearly missing in the final product.
http://www.lni.wa.gov/safety/hazardalerts/951a.asp
http://nj.gov/health/eoh/rtkweb/documents/fs/1960.pdf
That is probably only relevant for workers working regularly with powdered tungsten carbide. It is difficult to imagine, that the solid chunks on the saw blade could do other damage than mechanical.
Especially nice is the following advice in the PDF: “Where possible, automatically pump liquid Tungsten Carbide from drums or other storage containers to process container.”
When the melting point is probably in the range of 4000°C.
I don’t always pump liquid tungsten carbide, but when I do, I pump it automatically from drums to the process container.
Haha. Beer reference.
Yes, it’s a little stupid to be concerned about the tungsten carbide. I was talking about the sintering compound.
from the PDFs:
“Cobalt, which is a routine ingredient of tungsten carbide and other hard metals, may be released into air during the manufacture, finishing, grinding, filing, sharpening, brazing, welding, or sandblasting of hard metal.”
and
“The recommended airborne exposure limit for cemented Tungsten Carbide containing greater than 2% Cobalt as a binder is .05 mg/cubic meter (as Cobalt) averaged over a 10 hour workshift.”
Note “brazing, welding”, which are both done at temperatures considerably lower than 4000 celsius, and the exhaust of a coal/coke or propane forge, especially with amateur blacksmiths, is seldom contained in a flue. You inhale what your forge exhales, to a greater or lesser degree. There is enough pulmonary hazard from the fine particulates from a forge: there’s no reason to make it worse with cumulative heavy metals.
The experimenter and the maker expose themselves to hazards that philatelists and skiers are not susceptible to, and a little extra caution is often warranted.
really old idea but still neat. most of the ones i see and have use an old plow disc cleaned up.
They also make wonderful axes and hatches when heat treated cut and ground.
J.T.
Kokopelli knives