[James] is designing an open-source 3D printed keyboard switch, with the end goal of building a keyboard with as many printed parts as possible. Since keyswitches are meant to be pressed quite often, the DIY switches ought to be tested just as rigorously as their commercial counterparts are at the factory. Maybe even more so.
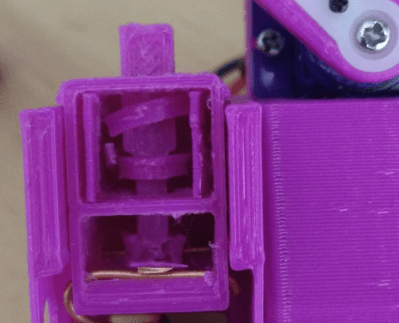
Rather than wear out his fingers with millions of actuations, [James] built a robot to test switches until they fail. All he has to do is plug a switch in, and the servo-driven finger slowly presses the slider down until the contacts close, which lights the LED.
The system waits 100ms for the contacts to stop any tiny vibrations before releasing the slider. That Arduino on the side tracks the contact and release points and sends them to the PC to be graphed. If the switch fails to actuate or release, the tester stops altogether.
We love that this auto-tester works just fine for commercial switches, too — the bit that holds the switch is separate and attaches with screws, so you could have one for every footprint variant. [James] recently did his first test of a printed switch and it survived an astonishing 13,907 presses before the printed coil spring snapped.
One could argue that this doubles as a servo tester. If you want a dedicated device for that, this one can test up to sixteen at a time.
Via @Microchip_Makes
I doubt the servo will last long enough to damage the switch :-D
Yeah, exactly my thought lol. It’ll last longer than a crummo 3d-printed switch, but a real one? The IBM model F capacitive switches I’m banging on this moment is rated in the billions of cycles… Hope you have a lot of time and a veeeery well-made servo.
A better design would have been to just put a continuous-rotation motor and a big round cam with bumps along its perimeter above it, all mounted on some good sealed bearings. Reciprocating motion isn’t gonna be as reliable.
but then you dont need an arduino ;-) or even a 555 :lol:
You do if you want to count cycles! Unless you’re going the semi masochist way and doing it all in discrete logic.
You use an app on your phone to listen for click-clacks.
Hey presto you’ve got your switch tester.
One could modify a dollar store calculator or a pedometer as a counter.
For a calculator, press 1+ and each step on the ‘=’ would increment the count. The 2 wires to the ‘=’ could be connected outside.
You just electrically connect up the key/switch to the switch you are testing.
yup.. or a solenoid actuator
Some keykaps are so resilient, that off-the-shelf parts used for test equipment will wear faster.
Solenoid actuators actually have fairly high failure rates. I second the cam on a motor technique.
+1
Your cam design might actually be able to test the limits of your billions of cycles switch but how long is that going to take? Do you really have a lifetime to devote to that project? And why does it matter? I doubt your finger is rated for billions of button pressing cycles anyway.
I’ve been thinking about building a custom keyboard lately. I want one with a dedicated compose button. Buying a whole set of good quality switches though is a lot of money just to get a keyboard with one more button than any of the free ones friends and family have dumped on me over the years.
~14,000 presses isn’t much compared to factory produced but if it’s easy to print and replace that might be good enough to consider actually using. I’m skeptical but interested too. I’d hardly call that “crummo”.
The back of my envelope says that you’d get the space and etaoin etc starting to fail after about 20 hours of 60 wpm typing. So basically in a week of normal keyboarding and twice in the last 48 hours of a critical project or deadline for your thesis.
I don’t know how much I type but that still might last me a while.
Also, clearly he built this tool so that he would be able to measure his progress as he iterates his design. ~14,000 is the starting point, not necessarily the end goal.
Besides, if he shares his design in the end, if the plastic spring is still the main limiting factor we can always substitute a traditional metal one.
Solenoids …. you could wack those keeps virtually forever with a proper solenoid its litearlly just an electromagnet + moving rod/armature ( in the case of rotary solenoids).
yet the article says the switch failed! the switch uses a plastic spring?? hard to imagine.
it’s a 3d printed switch..
Every switch fails. The point is to measure its life prior to its death.
Just spin a dc motor with a cam wheel
This sounds kind of like Samsung and the infamous we folded the phone 1 million times thing. If you don’t press the buttons just like humans (variable impact forces, angels, etc) your test only proves that it can be pressed 1 million times with that servo.
I was thinking the same thing, I only gingerly touch and hold my keyboards key’s at all times in all situations, banging in autocad commands, rage posting on a forum, playing the hard part of a game, always.
There’s a old video on YT about DEC making their series of personal computer’s, their keyboard test had rubber tipped steel rods just wailing on them driven by pneumatic cylinders.
Pneumatic cylinders are amazing. Hardly anything mechanical is that reliable at those levels of force. Motors aren’t really that great till you get to reasonably high quality ones, and they don’t fail gracefully at all.
And basic things like gears and pulleys have all kinds of ways to cause trouble, but compressed air seems pretty trustworthy.
Until maintenance puts some weird oil in the lubricators, causing all the seals to fail.
“But brakes are a hydraulic system, what’s wrong with DOT-4 ?”
Oh yes, I forgot about the law that requires anyone who does maintenance to have a stash of weird oils. One would hope they would be more responsible with them!
Any well thought out testing would include the occasional spray of coffee, spit out due to a equally well thought out HaD comment.
The idea is that, in ideal scenarios, you should get around one million folds. That’s more they any human would likely achieve in the total lifetime of the device. So let’s just say you only get around 500,000 folds in real world use. That is a lot of folds. You still wouldn’t be able to realistically fold the phone that many times in normal use, within the lifespan of the phones usefulness. Other factors like failed batteries and underwhelming processor performance will shelve the phone long before the day comes that your screen breaks.
Did you not have access to the internet when that phone was released? Within days reviewers and individuals were reporting IN MASS that the phones screen was cracking, breaking, dead pixels. It did not take 500,000 folds to break it was taking a few dozen in some cases. So the idea that oh well half of super ideal test conditions is probably what we’ll get fell so flat on it’s face that Samsung pulled the entire product line and refused to sell it to people. It couldn’t be a bigger example of failure to properly make test cases.
They probably built a fixture that perfectly mechanically supported each half and rotated it in the exact arc… fairly slowly…. they probably didn’t (correctly) model holding it by one side and thumbing it upward with force on one side of the hinge and letting it crash against the stop.
n=1. not a really good base to take conclusions from. take at least 20 examples before drawing any conclusion. if you go all the way, you may as well go the last mile
Why the obsession with purely 3D-printed designs? What has metallurgy ever done to you?
how many times do we have to cut our fingers, down with metal!
However, when there are commonplace high toughness plastics and homeshop convenient ceramics, you’ll cut your fingers on those too. It’s like trying to invent something that has the same properties as water and then being surprised that it’s wet.
Nice idea, but the data is not likely very useful in practice. I put together a pneumatic switch tester myself (did not expect a servo to survive the test), and ran some switches for over a million cycles. Unfortunately, I did not experience even one failure. “In the wild,” switches are exposed to real world dust and dirt, so they were failing after a couple hundred thousand cycles.