There are more free 3D models online than one can shake a stick at, but what about paid models? Hosting models somewhere and putting a buy button in front of the download is certainly a solved problem, but after spending some time buying and printing a variety of non-free 3D models online, it’s clear that there are shortcomings in the current system.
What the problems are and how to address them depends a little on the different ways models get sold, but one thing is clear: poorly-designed 3D models are bad for consumers, and bad for the future of pay-to-download in general.
Different Ways Models Get Sold
There are quite a few different ways 3D models get sold online. Online sales are great for digital models because models are not physical goods, and serving a thousand buyers is no different from serving ten. A user technically pays for a license to use the model rather than purchasing it outright, and terms vary depending on the creators and providers.
Direct Sales (Pay per Model)
Direct sales work just like free 3D models, but with a price tag stuck in front of the download. Sites like Cults3D and MyMiniFactory allow creators to set prices on non-free models. Sales numbers are a bit hard to determine, but popular models have hundreds or a few thousand downloads.
A standout success is a site like Hero Forge, which allows users to create custom tabletop gaming miniatures with a web-based interface. Users can pay to download the STL of their creation, or pay for a printed version. Hero Forge is a proprietary system, but a highly successful one judging by their recent Kickstarter campaign.
Indirect Sales (Pay for Access to Models)
Indirect selling is when customers pay for access, rather than buying models individually. Successful creators make models in a niche area of interest, and people pay for ongoing access to the creator’s library of work.
Patreon is a common way for 3D model creators to manage monthly subscribers and provide access to files. Tabletop gaming is a common niche, and some of the bigger players have thousands of monthly subscribers.
Another way indirect sales are done is via crowdfunding campaign. Money is raised to create a specific set of models, and backers receive access to the resulting files. Again, tabletop gaming miniatures and terrain are over-represented in this area.
Kits Where Customers Print Their Own Parts
This approach sells 3D models as part of a product. Sold with or without additional hardware like electrical parts or fasteners, a purchaser buys a kit and prints their own plastic parts. As a result, the kit has fewer pieces, is easier to produce, cheaper to ship, and generally costs less than if the seller had to provide everything.
Examples of this business model include the (NERF-compatible) Bulwark Blaster, and the OpenScan (open-source 3D scanner.) In both cases, the project is built around 3D-printed parts and a solid bill of materials. Generally, the buyer is purchasing a single-use license for the printed parts.
Where Are The Problems?
In an ideal world, 3D printers reliably create any arbitrary shape without having issues with overhangs, bridges, distortions, or supports. One could purchase a 3D model and get exactly what’s expected. Sadly, we’re not there yet.
Good-quality 3D models must be designed specifically for 3D printing, and this is especially true if money is involved because in the current system, buyers accept all the risk.
No Test Drives, No Fitting Rooms, No Refunds
The world of non-free 3D models is a lot like a clothing store without a fitting room, or a showroom without test drives. “No refunds” is a common term of service and sale, and when combined with an inability to try before one buys, results can be unfortunate if a model is of poor quality.
Models With Poor DFM (Design for Manufacture) Exist
3D printers, like any tool, are good at some things, passable at others, and bad at the rest. That means models intended for 3D printing should be designed with the strengths and weaknesses of 3D printers in mind. A model that has been designed in such a way can be said to have good design for manufacture (DFM).
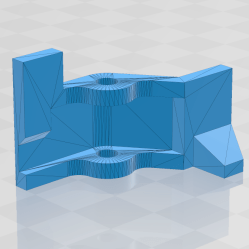
If a model has not been designed with 3D printing in mind, it can make life difficult for the person trying to print it. The trouble is that it’s not always possible to identify troublesome models by screenshots alone. Here are two examples.
The first is a simple latch from a larger assembly intended for FDM (filament-based) printing, shown here. The problem is subtle: the way it has been designed makes it virtually impossible to print reliably without needing supports, no matter the orientation. (It also had other problems, but more on that later.)
Adding supports means additional post-processing and a poor surface finish where the supports connect. If supports are placed on the latch’s presentation side, the part will be ugly. If supports go on a non-presentation side (where the hinge is) it invites fitment problems.
These issues can be solved with post-processing, but that’s not the point. The point is that it would be better to design the part in a way that avoids such problems in the first place.
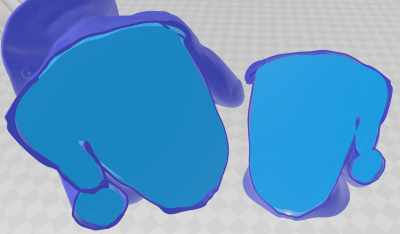
Another example is shown here. This model was advertised as being compatible with SLA (resin-based) printing. FDM and SLA printers are good at very different things, so it was encouraging to see a model specifically designed for SLA.
Unfortunately this turned out to not be the case. The model was not a solid figure. There are gaps between the outer layer (the figure’s jacket) and inner layer (the body) because they were modeled separately, and left as-is.
Not only do these gaps trap uncured resin, but the areas around the gaps are very thin, which invites print failures. In short, this model’s design choices ensure that the outside layers — the presentation surfaces — are the most likely to fail. These issues were not visible until after the model was paid for.
These problems and others like them demonstrate poor DFM that is not evident from screenshots and renders, and as mentioned earlier, pay-to-download is currently the land of No Refunds and Buyer Beware.
Why Bad Quality Models Are A Big Problem
The problem bad models cause is this: by the time a model has proven to be troublesome (or impossible, or wasteful) to print, a buyer has invested considerably more than the purchase price. All a bad model accomplishes is to alienate a person who was willing to mash a BUY button.
Having a buyer accept all the risk, only to have their expense of money and effort rendered worthless should be considered a worst-case scenario for any platform that is trying to grow.
Ways To Improve
It may be tempting to try to solve the issue of no returns or refunds with a system that can control access to downloaded files, but anything in this direction starts to look a lot like DRM, which is doubtful as a way forward.
It is possible to increase confidence about model quality and purchase without changing much about the underlying platforms as they currently exist. Here are some things that can be done.
Demonstrate Model Quality with Photos and Documentation
Documentation and photos (of the printed results, not just renders of the model) are an effective way to let a buyer know more about a model. Documentation doesn’t have to be long, but it should talk about design elements, assembly, or areas of special attention. An example is this model of a 3D printable vise by Christophe Laimer. It’s a free model, but excellent documentation in a way that builds confidence in the model’s quality.
Models that require additional hardware should have a clear bill of materials along with specifications and sources. That latch model I used as an example of poor DFM? It required a mystery spring of unspecified dimensions and no source; another issue not discovered until too late.
If a designer doesn’t clearly demonstrate that they have printed their own design successfully, don’t buy it.
Provide “Test Drive” Pieces
Designers of kits or other assemblies for sale can offer free access to small number of parts as a way of saying “if you can print these models and assemble them, you’re good to go because my product is designed using the same principles.” If customers cannot return purchases, this can at least provide a form of test drive.
Perform Automatic Quality Checks on Models
Professional print places like 3D Hubs perform an analysis of uploaded objects as part of their quote process, and warn about model features like thin walls, intricate details that could be lost, or the potential for hard-to-remove supports. Services responsible for hosting and selling models could increase buyer confidence by performing similar checks on models for sale, and showing the analysis along with the model and price.
What is Your Experience With Paid Models?
Have you bought models online, or do you sell your own designs? What’s been your experience, and what would you change about how it all works? Let us know your feelings in the comments.
Bold of you to assume I would ever pay for a 3D model.
Sometimes you have to pay, either with your time or money. And why design something the 5th time, spend hours on it instead of paying 3$?
Because designing parts is half the fun 😁
I often roll my own even if I can find what I need on Thingiverse because I often enjoy the journey more than the destination.
“In an ideal world, 3D printers reliably create any arbitrary shape without having issues with overhangs, bridges, distortions, or supports. One could purchase a 3D model and get exactly what’s expected. Sadly, we’re not there yet.”
For a relatively immature technology not a surprise. The buyers take on a lot of responsibility. Kind of like early personal computing. Some “free hardware”, vetting, and good documentation would have been helpful.
almost every model I have downloaded and tried to print has major issues.
I also feel like if someone wants to actually SELL models for download, that they should be tested and tweaked for the most popular printers on the market and marked as such. and come with profiles and SEVERAL types of filament that are known to work.
The print should finish, even if the person makes minor mistakes in the execution.
There are a few models that I have downloaded and printed that are VERY forgiving, but alas these are the exception not the rule. Usually they are stupid simple.
One of the biggest problems I have run into is the fact that the printer will run off and do another part of the print, and by the time it comes back to add something on the other side, the plastic has cooled and layer adhesion is shit for that part. Most designers aren’t actually good at designing for printers that will execute the gcode in a different order, or might just be VERY slow, or in the opposite case VERY FAST. The execution in the slicer is not good enough to tell when it needs to turn the heat down for small circumferences, and when it should be up for larger areas to obtain proper adhesion.
eg: I have one of the fastest printers on the market, yet I have to slow it down for many models that are not designed with such a printer in mind.
bridging is another one of those “its very different on every machine” parts of a design that should literally just be left out of almost any design that is made for general distribution.
I’d rather glue together a part or otherwise fasten it, than waste a crap ton of time and plastic because the og design is crap. Cut the design into multiple pieces.
A simple guide of what sort of standards your printer should be able to achieve would go a long way to hinder confusion. but nobody does that.
another issue is that ‘profiles’ for a lot of these printers are just flat out junk, and need tweaking.
I basically have a profile for each part I print, it’s like setting up the machine from scratch, every time i want to print something new. Even at that, I often find myself sooner or later just saying “this design is junk” and designing something myself that will actually print and stand in for the exact same use case.
ie: all-in-all the problem should solve itself over time as more people become more highly educated in the industry, but I don’t expect that to happen with all of the fragmentation and hobby level designers out there that just don’t cut the mustard when it comes to ease of use and functionality over form.
You are quite right on a printer tolerance suggestion for each model being something that would be very useful, and some models would be better off in parts (especially for FDM). Though I’d argue in most cases it should be the end user choosing where and how to chop up a print to meet their needs – you don’t want my model cut into bits designed for the tiny 10x10x8cm build volume if you have one of those much bigger printers, nor do you want every element cut into parts for the easiest/most detailed/quickest/strongest print for every possible printer permutation (also remember resin printers are a thing and able to create parts in ways even the finest nozzled most highly tuned FDM could not) – You at best want one of the preceding thousands of options and the modeller can’t be expected to provide the perfect file for every single possible need unless you really want to pay them $1000 per file or something equally stupid for the hours they would have to waste doing so..
However most of the issues you are moaning about sound like a problem with the slicer or printer settings not the model you are trying to print at all. So its nothing the model designer can do about it – your setup is the problem.
If your printer really is able to run that fast it will print anything at all that fast just fine (that’s what part cooling fans, the massively potent hotends etc are for – though you always need to have a good initial calibration and then probably will need to tweak some settings based on the filament you are using if you really want great results – I’ve have fillaments supplied that are slightly under or over sized even from the big names, need 10 degrees less or more heat (probably because of the colour) despite being the same plastic).
If you are having issues with layers adhesion you probably need a slightly hotter setting on the extruder, or to be running a little slower so your hot end can keep up with all the plastic you are pushing though it.. Generally speaking you can come back to print that is now room temperature and just resume (done that many many times – pause the print because the old spool is dead (automatically stops) and feed in the new one (I use up lots of smaller otherwise waste spools any time I am prototyping so finish and colour don’t matter)) – there will usually be some evidence you paused that long – as the already printed layers will have shrunk as they cooled but the adhesion at that point should not be a real issue (if using the same types of plastic – not all filaments will stick to a different one well).
so just to explain where the settings in the printer DON’T MATTER… When you turn the heat up small radius corners and what not end up curling, while larger stretches of the model end up being too cool. The ‘part cooling’ bit, doesn’t work when the printer is setup to run quickly because the hotend doesn’t spend enough time over that area for the part fan to actually cool anything effectively. I have tweaked the small radius settings and what not, but my primary point is that the output isn’t good enough to allocate for ‘mistakes’ in the setup. Each part requires a bunch of specific tuning and a large learning curve on the part of the user. The model has a lot to do with that, and if you look at the comment about github for prints, the model maker would not have to actually do a lot of that work, they would simply use a commit from another user, and thus the profiles would be packaged in neatly when you download said model for X printer. see what I am getting at? It’s more about the infrastructure of printers not being efficient or well documented or implemented properly, and as model creators and sellers, we should solve that problem by creating a proper platform or lobbying an existing platform to be more than just a scrolling wall of pictures and actually provide something useful beyond a money grab. It will save literally tons of plastic, and rather than forcing some company to provide a ‘perfect printer’ and a ‘ubiquitous platform’ we simply let the community and software handle the difficult bits, thus making 3d printing easy and sensible for mainstream use, and MUCH easier to get into because it cuts the learning curve down drastically.
it’s literally all about taking a product from some garage tinkering, up to a scalable product that everyone can use.
ps: don’t get me wrong, I can get some nasty models to print, but it’s not fun having to create new profiles for a new object. lol. I can print most good models with a few minor tweaks, til i change filament, then I gotta figure out new properties for that.
You really can cool the parts damn fast if you fit a big enough blower- and if you are aiming for great speeds and quality you will need it (and don’t have a heated enclosure – as that really lowers the cooling efficiency – though you could perhaps introduce some fresh cool air from outside (not sure anybodies ever tried that though))
Just tweak your slicer settings well enough and you can reliably print both fast and high quality – but to do both really takes the tweaking, adaptative travel speeds etc. So just run the printer slower when you care about the best quality.
Unfortunately 90% of getting great prints is in the hardware and slicer settings matching the hardware limitations – yes you can design for FDM, but even designed for FDM won’t print on poor hardware or with a poor slicer setup well.. So the only way to really have a repository of easy printing is to have a very small set of printers being supported – its not really the model its printer – so if all printers shipped with a well matched slicer any old model with FDM limitations in mind should be fine.
So all the model maker/ seller wants to list is something along the lines of default size/scaling and a suggestion of FDM vs SLA to render detail at each scale etc.
what we need is GIThub, but for prints. So that way each model has people’s submissions from their own printer and nozzle size etc, and has a branch for each. So when you can find someone that has printed X model on X printer that matches yours, or something close enough, someday. These “model repositories” we have now, are all CLOSED SOURCE and not FREE AND OPEN, which means they are inherently flawed by design and we should all move to a free platform (and yes, including paid models) that has a better structure.
Like the concept of having a GitHub for 3d prints. I think I’m going to do that on my 3D models from now on.
Sites like thingiverse do have a similar ‘i printed this’ but it doesn’t have settings or any feedback mechanism. That is solely up to the designer if they take any feedback
I’m not sure I want to see non-free models get any better. There is a pretty good library of free models out there. Do a search for a 3d model you might want or need and compare that to a search for a vector graphic or background music. The royalty free pickings tend to be quite slim. Perhaps a healthy non-free market stunts the growth of the free community.
Don’t get me wrong. Making models is work, people deserve to get paid and everyone needs to eat. But when you already have a community of people who want to do the work with only building the community as payment maybe it’s better to leave well enough alone and make money elsewhere.
All of this stuff is where my experience as a polygonal 3d modeler comes especially in handy… it ain’t pretty, but modifying STL is perfectly possible. I don’t think there’s a single model off the internet I haven’t had to clean up or tweak a bit, and few of those had the source files. I would be peeved if I had paid for a model and it came through as trashy as that one with the floating internal geometry (🙄) but I’d get in there and sort it out. I do CAD too now, but I started doing Quake mods back in the day so my core instincts are working with tangles of triangles. There are good tools for dealing with them, but they aren’t associated with the CAD world so they often get overlooked. It’s definitely worth looking into.
Of course, I’d also never pay for a printable model… Having the knowledge of modeling myself, why would I?? I’ll grab free ones to save time and use as a base or reference. But never paid. I really and truly don’t understand people who buy and build and bother to learn to use 3d printers without learning how to model. That’s where all the potential is!
I’ve long used trueSpace for 3D modeling. It can import STL and be used to modify them exactly like anything made from scratch with trueSpace.
There is one gotcha though, for STL and several other formats it imports the model scaled down to fit the X, Y, or Z dimension, whichever is largest, to 8 of the model units currently selected. The workaround is to first load the model in a slicer, note the XYZ numbers, then in trueSpace enter those into the boxes in the object pane, then save as a COB. Save that file and do all work on copies. Every time I export to STL I save that same version as COB. If something needs changed for printing I do it to the latest COB file.
I model in any Metric unit in trueSpace. Doesn’t matter which because STL is all millimeters so Meter, Centimeter, Millimeter in trueSpace all equal Millimeter for STL. This does make things a bit odd where if I’m modeling something larger and don’t want it ‘overflowing’ the work space I set the model to millimeters. If I’m doing something small I set the model to meters so I don’t have to zoom way in just to see it.
What would be very nice is if a group could buy trueSpace from Microsoft and release it as an open source project. Would have to leave out some of the closed source parts Caligari had licensed, like the Lightworks rendering engine, but all the main parts should all be Caligari code that Microsoft bought with the company then abandoned when they decided to not continue Virtual Earth VS Google Earth.
As an open source project it would be possible to tackle long standing issues like the import scaling problem, and how it can save VHTML 1.0 and 2.0 but can only open VHTML 1.0. Not that such is an *important* thing these days, but would be nice to squash a *really stupid* problem that should never have made it to release.
https://www.3dnatives.com/en/thangs-search-engine-for-3d-models-200820205/
Had my first 3D printer built over 9 years ago. Still use them regulary. But i never ever saw the need to buy a 3D model to print. I’ve looked at some offerings, sure, but never felt like i really need that thing printed on my machine soo badly that i could not resist. Guess i prefer to invest that money into a new spool of fancy filament before i spend it on some data.
I have not bought a model, but I would be doing a charge back on my credit card if I paid for a model that was worse than something I could design in a reasonable amount of time. I have used free models and they are all over the map. Some of them suck. I am not sure who would want to attach their name to something so bad. On the flip side, I have got some amazing models, where either the people who designed them are either very skilled or put a lot of time into them, or both.
I think having customer comments, customer pictures and 3D views as well as being able to read the printing and assembly instructions go a long way as far as giving you confidence the person selling the model has a clue. Also if there is a marketplace, having a reasonable return policy and removing models that have a lot of returns, or flagging them as being either tricky to print or poor designs.
Judging by the mountains of garbage on Thingiverse, I’m not surprised that the pay-for model sites have a similar amount of trash. In fact, since people expect to get paid there and there’s no return for crap models, it should be a magnet for “designers” who wouldn’t know a 3D printable model if they saw one.
The problem of bad 3D models is a mirror of the internet problem. There’s no filtering to prevent useless garbage from getting posted. Any dope with a computer can get on the internet and say any stupid thing they want and it will infect others. I suspect that many of the most prolific “designers” are in the game to claim as many “designs” as possible, even though their “different” “designs” are something like a series of license plates for kids bikes with different names on them. You can easily generate 50-100 “designs” per hour with that type of stuff.
I was recently in a situation where I was designing a commercial thing, and the poor state of non-free models was a real pain.
1) It was HARD to find good non-free models (they allow commercial use, you see) that were worth a dang.
2) It was EASY to find free models, but “free” models commonly forbid any sort of commercial use. (They are only “free” in the sense of not costing money.)
3) It was HARD (in fact, I never succeeded) to pay someone for a licence to use their “free” model commercially. I stopped even trying.
I sort of suspect there is a bit of a chicken-and-egg problem with sites allowing paid models. It’s not very lucrative so there’s little incentive to improve it. But there is definitely money to be made selling 3D models; the tabletop niches prove that.
Obviously the solution is that you should give away all your work for free too. 😂
Was your commercial project a model or the resulting physical print? Presumably a “free” model licence can’t infect a physical object? If any copyleft advocates say it should, then DRM’d vehicles are also justified, which is something we can probably live without.
Model: Free
Part given to customer: Free
3D Printer Operator: $100/hr
That’s how you do it
And here’s a big cheer to Josef Prusa and the Prusa community for making lots of spare parts and add-ons free available – and guess what: they are relatively easy to print and do work and fit.
Honesty page: I once printed a Prusa Mk3 spare part on a CraftBot…. So sorry, Josef…..
Why would paid models differ from free models? From my experience with free models I know what to look for (in order not to waste my time and filament more than necessary), so if I ever choose to actually buy a model instead, I also know what to look for there. Of course, you should expect (a little) more from (popular) paid models with the proper documentation (not the textual description, but all the technical details/numbers I look for along with test prints), but I would never expect more from the rest. Caveat emptor…
> Why would paid models differ from free models?
For one thing, the license terms of paid models differ from free models. Free models often disallow anything other than private, personal use, and some even forbid remixing (less common, but it happens.)
No, you should be aware of licensing terms of both free and paid models. Just as closed and open source software can have the same or different licenses.
I do agree that currently the pay model system on the web isn’t great as not all sites( or designers) check to verify the paid model (or even free model) is printable before uploading. I’ve unfortunately seen over the years way too many people pollute sites with poor quality unverified printable designs in hopes to make a quick buck. This habit of others detracts from printables designs that are of excellent quality & worth the possible purchase.
Majority of the time I design & print my own stuff. Why? Because like others say it is hit or miss as to the quality of the design depending from whom or where it came from, especially if it is from Thingiverse. If I print someone else’s designs, majority of the time I usually run it through netfabb or meshmixer to verify if the piece(s) are solid or need repair work. Much of my frustration in my early days of 3d printing were due to models that had manifolds. So now I check most models I get off the web before bringing it into my slicer software.
As for the stuff I design & upload to the web, around 80% of my stuff is free. The other 20 percent is paid original content. I run my own model checks through netfabb or meshmixer & test print my designs that I intend to upload on at least 2 printers to find consistent print settings & adjust the design to maximize the result to be printable on almost any printer. I want people that download my stuff be to be able to print without as much issue as possible & not go through the headaches of troubleshooting why my design their printing isn’t printing.
Unfortunately as a designer I cannot fix my designs to work due to factors in control of others such as a poorly calibrated machine, printing with a crappy tolerance filament, or ignoring recommended print settings. I do get occasional comments from people that have downloaded/purchased a design & blame the design as “poor quality” when in fact almost all the time after troubleshooting with the user to find out that it is a machine calibration, or bad filament issue.
I do hope in the future that as more 3d print sites offer a way for designers to sell, that these sites offer a quality check system on the uploads and only designs that pass can be sold.,
Sounds like things can cause their share of frustrations for the model designers as well. Thank you for sharing that perspective.
I’d love it if rating systems were good enough that good rating could reliably endorse a product. I wonder if a PGP signature would be a way to avoid ballot stuffing and to verify the identity of a reviewer such that the reputation of the people leaving feedback can be taken in to account when weighting the feedback.
I used HeroForge once and felt it was very clever and worth the money. IIRC you can assess the quality prior to payment with their system.
A nephew of mine asked me to 3D-print a couple of models that he had downloaded from Hero Forge. My initial thoughts were: no problem at all . . . I’ve designed & printed many models on my printer & I have a very good handle on what it takes to successfully print a final product with my specific printer. It wasn’t until he indicated that the final products should be 30mm tall that I realized the actual difficulty (almost impossibility) of his request. I spent many hours trying to get successful prints that small from my very capable printer. Many of the finer details were simply impossible to produce on a scale that small. I finally settled for sending him a couple of 100mm prints to place on his desk or bookshelf.
Sadly, even at 100mm, many details were very poor (e.g. flowing hair, which could not be adequately held by any kind of supports, so it just turned into a mangled mess, & the money bag on one of the figurine’s belt, for which the top & side details were very good, but because of what other features were around/under it & where it was located on the figurine, the bottom of the bag could not be cleanly printed & looked terrible, & the under edge of the very large lance that one of the figurines was holding *never* came out sharp, again because of the geometry & the poor layout for supports). These were definitely models for which DFM was done poorly, if at all !!
With my quite extensive 3D design experience (mostly cases, tools, & a variety of accessories), I don’t believe that I could have designed such figurines from the ground up, so that was not really an option. Looking at just the models, they looked really impressive !! Unfortunately, that look definitely did not translate into an equally impressive finished part. Luckily, my nephew did not spend a fortune on the purchased models, and he did get a set of halfway decent 100mm figurines that he could finish out with just a little more work (patching, filling, sanding, painting, etc.).
Miniatures are not made for printing on FDM printers – they’re for SLA printers (resin printers). Those have *much* higher resolution but come with their own set of issues.
I am baffled at at the state of licensing for many of these 3D models.
Take for example, a popular baby yoda model. No way they have a license for that from Disney, and yet they insist on a “Attribution-NoDerivatives” license. Where is their attribution to the original designer of baby yoda or to Disney? Don’t they realize that their own model is itself a derivative? You can’t copyright an illegal copy! Well at least they allow other people to engage in the same conduct for free, by allowing commercial redistribution of their “original” (which they can’t legally do since it is an unlicensed derivative).
For a free model, this is more of an annoyance, but in the context of paid-for models this is very problematic and deceptive. They are stealing the original intellectual property, and people’s money who pay for the model. They are just counterfeiters. Someone will get burned buying a design that allows commercial use, only to find out that the modeler had no right to sell it to them in the first place.
Pirating a design at one’s own risk is one thing, but trying to sell it as your own is another. The fact that the online storefronts don’t seem to care about this is probably a good indication that the quality of the models is also poorly regulated.
Hi, Great article. I wish there is a place where one can submit a model and get feedback to improve it from pro designer.
In the EU at least, sellers legally have to allow a 14 day right to withdraw for a full refund on digital content, be that software or models etc. This covers games etc too. If you DL a model and it’s junk, you can at least get the cost of the model back, if not the time, and materials cost.