It is not uncommon for a Hackaday writer to trawl the comments section of a given article, looking for insights or to learn something new. Often, those with experience in various fields will share kernels of knowledge or raise questions on a particular topic. Recently, I happened to be glazing over an article on aluminium casting with interest, given my own experience in the field. One comment in particular caught my eye.
And no, the water won’t cause a steam explosion. There’s a guy on youtube (myfordlover, I think) who disproves that myth with molten iron, pouring the iron into water, pouring water into a ladle of molten iron and so on. We’ll be happy to do a video demonstrating this with aluminum if so desired.
Having worked for some time in an aluminium die casting plant, I sincerely hope [John] did not attempt this feat. While there are a number of YouTube videos showing that this can be done without calamity, there are many showing the exact opposite. Mixing molten aluminium and water often ends very poorly, causing serious injury or even fatalities in the workplace. Let’s dive deeper to see why that is.
The Magic Of Oxide Layers
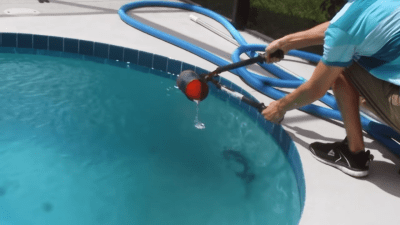
One of the reasons aluminium is so prized as a material is for its resistance to corrosion. Raw aluminium readily forms a tough oxide layer when exposed to air, which protects the metal from further corrosion or reactions with many chemicals. This oxide layer can form incredibly quickly, and is one of the reasons why many YouTubers have managed to pour molten aluminium into water without injury. Given the right conditions, the aluminium can form an oxide layer as it travels through the air from a ladle towards a bucket of water. Many use this dangerous, risky demonstration as “proof” that major explosions from aluminium and water are a “myth”.
Of course, get a job at a casting factory and you’ll quickly realise how serious the matter is. It’s not unusual for facilities to entirely ban disposable water containers and soft drinks, for fear a discarded container could end up in a scrap bin and carry moisture into a melt furnace. In my work as a casting engineer, bringing a water bottle or can of soft drink on site carried a warning for the first offence, and instant dismissal for the second. The danger is simply too high to take half-measures where safety is concerned. Casting operations generally require all employees to watch safety videos that make the risks clear, prior to working on the casting floor.
Examples of the danger are readily available. Often, incidents can occur when molten aluminium is poured into a mould containing moisture. Another risk area is when loading scrap material into a furnace. The scrap aluminium itself can be wet, or bottles containing fluid can be accidentally mixed in with the material. When the scrap is added to the molten metal in the furnace, huge eruptions can occur.
Causes of Explosion

Due to a multitude of factors, intense explosions can happen when molten aluminium and water mix under the right conditions. The first is the most obvious: water coming into contact with molten metal at over 660 °C tends to vaporise into steam nearly instantaneously. The steam rapidly increases in volume, throwing molten metal great distances and this alone can cause serious injury and damage. This also breaks up the molten aluminium, known as fragmentation. This has the effect of causing greater mixing between the molten metal, and the water and steam. This further increases the rate of heat transfer to the fluid, and increases the rate of reaction between the steam and aluminium due to the greater surface area in contact between the two.
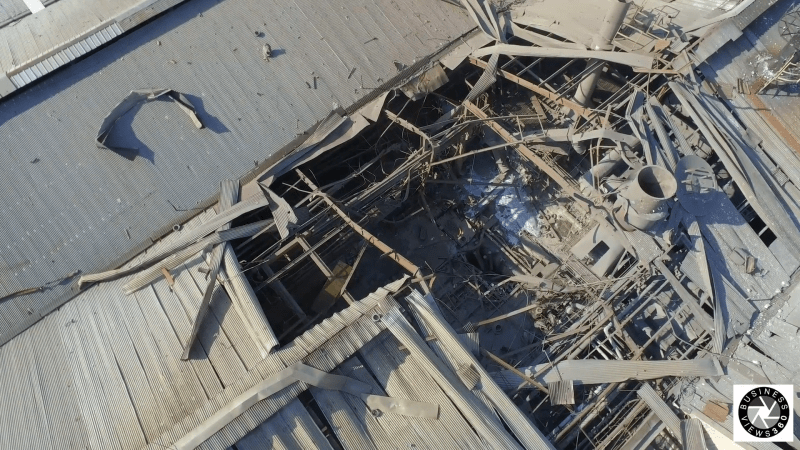
Additionally, the chemical reaction between water and aluminium only adds to the intensity of the explosion. In this case, aluminium atoms react with water molecules, forming aluminium oxide and hydrogen gas. This is an exothermic reaction which releases a great deal of heat — over 2.5 times the amount generated by a similar amount of nitroglycerin. Naturally, the hydrogen gas generated is then free to combust with oxygen in the surrounding atmosphere. Furthermore, any molten aluminium atomised by the explosion can then go on to rapidly oxidise in the air, too, releasing more heat in the process.
A combination of all these factors can lead to incredibly violent explosions. Little more than a single misplaced water bottle is capable of blowing apart an entire casting factory under the worst conditions.
Characterising Incidents
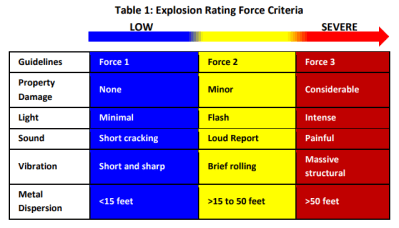
Of course, not every incident goes down the same way. A wide variety of factors can influence the severity of such an explosion, from minor to catastrophic. The Aluminium Association groups incidents into three categories, depending on the severity of the explosion. Force1 events are minor, often concerning the splashing of molten metal of distances up to 15 feet. Force 2 events are more serious, with metal sprayed up to 50 feet away and with loud explosions and a release of light. Finally, Force 3 events tend be loud enough to be seriously painful, with metal thrown over 50 feet and generally causing major structure damage. Force 3 events are thankfully, rare, but often tend to destroy most of the facility they occur in. The annual report of the Aluminium Association notes just 1 event in 2019, thankfully with no loss of life.
Overall, the aim of this article is to highlight that anecdotal evidence cannot be used to declare something safe. It pays to do your own research, and get information from professionals before trying something that could possibly injure yourself or others. Happy hacking out there, and keep it safe!
I have a small scar on my forearm from when I put a not-quite-dry piece of steel into a salt bath while working as a research metallurgist.
And my mother likes to recount how her medical records mention that she was scalded by molten lead, when we were melting down scrap lead to make window frames[1] and one piece had some water in it.
So, yes, real-world experience suggests that caution is justified.
[1] As you do.
I worked at an aluminum extrusion factory right out of HS. We recycled tailings as well as collected aluminum . This was poured into billets the size of telephone poles, then cut into smaller chunks for extrusion. Anyway someone was not as careful as he should have been and a full can of (what we thought at the time) coke slipped thru and tossed into the furnace. This caused a massive explosion of molten aluminum. Shutting down the plant for an extended period. As far as I know there were no deaths.
Some people claim that the 9/11 collapse of the WTC was due to the fire, water and aluminum from the aircraft which crashed into the towers.
https://www.soci.org/chemistry-and-industry/cni-data/2011/19/911-collapse-due-to-metal-reaction
Any comments?
It was due to the intense fire weakening the metal support beams sufficiently that they could no longer carry the load. Firefighters are trained to be aware of this. Conspiracy theorists say the metal would have had to melt and since a fuel fire cannot melt metal, a “secret” demolition must have occurred. This view shows a lack of understanding of metallurgy and materials science. Leave a stick of butter in the freezer for 24 hours and try cutting it with a butter knife – you cant. Leave it 24 hours in the fridge and you can cut it easily even though its not melted! That’s material strength vs. temperature and the same happens with steel. Architects calculate the size of steel beams based on load and max temperature, using as little steel as possible to keep costs down. That a high rise will collapse due to a long lasting fire, is very predictable. Water and aluminum had no effect at all – foundry explosions involving water occur when moisture comes in contact with molten metal.
…and yet no other steel-framed high-rise has _ever_ collapsed into it’s own footprint, despite several raging ‘towering infernos’…
Not until 9/11, it happened after 9/11 but not so neatly.
Well, no other “towering infernos” were first weakened by the structural damage caused by the kinetic energy from a collision of a large aircraft. Which, by itself, has to have been rather considerable, and besides, most of the support columns of those buildings seem to have been in the outside walls too. Then the fire softened what was left well enough that they started to bend. And if there were at least a few explosions when molten aluminum – or magnesium or magnesium alloy at those seem to be used too, at least in small quantities – as came in contact with water… well, the combination is pretty unique, isn’t it?
It’s just a theory. Because there is 33 tonnes of aluminum in a fuselage. That coupled with the conditions inside the building, it’s quite possible that an exothermic reaction could have occurred which increased the surrounding temperatures. There’s no proof of that though. It’s more likely because of the heat from the fires that weakened the support beams. They don’t need to melt them down for it to collapse. Once temperatures reach half the temperature it takes to melt the steel loses it structural integrity by 50% and it’s likely with the sagging that the temperature was higher in and around the impact area. Therefore explaining the pancaking of floors.
All the burning office furnishings, plastic housings on computers and other electronics, and the huge amount of paper stored in file cabinets also contributed to the heat.
I agree : https://www.youtube.com/watch?v=gui_ATdfHx4
>‘All that was put on fire due to very strong friction,’
OR maybe because the plane brought an active flame source with it.
>Scientists from aluminium company Alcoa agreed it was an aluminium– water explosion
BTW, Alcoa makes parts that are in that active flame source.
Al / H2O explosions are from rapid expansion of the water not from a chemical reaction. A surface reaction of oxidation of Al will just slow down the heat transfer and any further reaction, hardly an explosion.
Boring things like adding some heat and 30 tons to a structure weakened by impact will make it fall down in time. The people who planned it knew that. Who did it is more important that inventing fantastical ways they did it.
The reason for the collapse of the towers was researched by actual engineers, and the reason is well known. Older buildings exposed to fire in this manner didn’t collapse because they used steel ‘I’ beams. The towers used steel trusses coated with fire retardant material. The impact knocked off the retardant, then the open structure of the trusses allowed them to heat up faster, leading to weakening and then to the collapse.
Molten aluminum turns into aluminum oxide and hydrogen gas on contact with water. This reaction is very exothermic. Furthermore, given the conditions in which aluminum is molten, there is a high probability the resulting hydrogen gas ignites/explodes, contributing to the exothermic nature of the reaction.
Happened to me many times in various occasions with Aluminium and Magnesium. Only precautions and safety clothing reduced the incidents to one with an acceptable risk. Liquid metal in experimental machines can be quite nasty in the moments where you least expect it.
Has anyone ever seen what happens to magnalium( aluminium & magnesium ) when poured into water? Moulton Magnesium is for more dangerous than aluminium, let alone the 2 together! A few years back I was making magnalium,among other alloys,when I lost my train of thought and poured the 10grams of molten metal into water instead of smothering it with coal🙄NEVER AGAIN!! The explosion was so loud the cops,fire brigade,paramedics all turned up within minutes only to find spot fires everywhere and belowing smoke still going. Thankfully I only ended up with light-medium burns to the top of my head,but had I had more than 10g in the crucible,or the explosion blew my way instead of outward it would of been a life changing experience for the worst,I should of been hospitalized with major burns due to the magnesium and air/water mix that day (as I look up and thank lady luck for looking over me) I have never made magnalium again since that day!
thank you for this PSA.
As someone who has worked in a TiAl casting plant, I can say with most certainty that banning drinks in a casting area isn’t something that is universally banned. Our only rule was that is had to be covered. Ironically, our water-jet cutting machine was also in the vacuum casting furnace building along with out burnout and heat treat ovens. Also I was the 5-Axis water-jet programmer. Our normal castings were 20lbs of TiAl per shot. Maybe it was because they were centrifugally cast under vacuum.
Our rule was that it was fine if it wasn’t in a disposable container. i.e. steel drink bottles were okay.
wouldn’t that be worse? as in more likely to be confused for a piece of scrap metal if in the bin?
I pray Lewin that your former employer has changed that policy. No closed containers should be allowed in any department where molten metal is present.
That is one thing that bothers me about the internet. We all get to share our knowledge and experience, but not all we share is true.
Thank you for caring enough to explain. There is no way of knowing how many people have been hurt by not following safety guidelines for molten Aluminum and other home foundry projects.
That is true RandyKC, from my experience on this topic I believe 10-20 people a year die from this hazard globally in the aluminium industry. My familiarity of incidents in home foundries is limited to only what makes the news media. I only hear on occasion an incident from a home foundry. Please note, the vast majority of explosions occur from one or a combination of the following: failure to follow training, skip production steps, or they made assumptions. One incident is too many. My goal on commenting to you is two fold, to respectively respond to your comment, and to educate anyone who will read my comment. I simply do not want anyone to be injured or killed in either a workplace incident nor a home foundry incident.
I worked for a company that did die casting of aluminum parts,, I was a member of the safety committee which walked around the plant and looked for safety problems. The first problem I found was with another member of the committee, lets call her “heffeny” which worked in HR, and decided to walk through our die cast faucilty with…..open feet high heels, no safety shoes. The second thing I pointed out was our “furnace tender” loading wet aluminium blocks from outside using a forklift and dumping them into our furnace. Water and heat…….this was ignored by our our …….HR member and our safety manager we will call JohnsonS for short. 6 months later our furnace tender had a nasty experience and had to have serious surgery due to molten metal burns. He was terminated 6 months later upon return to work. The others? This heffeny and johnsonS? Why they were promoted and continue to make the best decisions money can buy…….
Who puts an HR drone on the safety committee??
Theoretically, one responsibility of HR is employee wellbeing, rather than pounding on square pegs until they fit the round hole of company policy.
HR only exists to support the company interest. To protect the company from you and to pay you as little as possible.
it’s actually standard practice for internal audits – you take someone from a different department, the idea is to minimize bias. He is paired up with someone from the department they are supposed to be auditing and off you go, find problems and plop them into some kind of weighted average score sheet. The problems with most (or least, depending on how it’s set up) points get priority in solving.
Everyone. Welcome to the real world.
A six or seven years ago, there was an incident at Artisan’s Asylum makerspace which didn’t even involve molten aluminum, but which showcased the staggering reactivity of the stuff:
Someone was polishing aluminum bells on a lathe, using abrasives lubricated with water. Rinsing the abrasives in a bucket both reapplied water and removed much of the *very* fine aluminum powder, which remained in the bucket.
Anybody who’s made thermite probably can tell where this is going:
In order for the aluminum finings to make their passivation layer, oxygen had to be found in solution.
A few hours later, and there was a magically-boiling aluminum-finings slurry in the machine shop and an angry thread on the mailing list, but very thankfully, no injuries.
Yes, if you leave a steel nail in a couple of inches of water in a plastic bottle, and put the cap on, it’s amazing how much the bottle collapses as the O2 is sucked into the water to react with the iron and rust it. (Over days, don’t expect to watch it in real time) So never consider oxidation under water “limited” by the amount of oxygen it currently contains.
Also, that kind of situation has made me nervous in the past, making lots of aluminum dust. In theory you could also have a fuel air explosion from it.
Stripey, I am glad no one was injured. Aluminium fines and aluminium dust is very reactive. A common incident involves the removal of the fines from a workplace. Companies will use specially designed vacuum cleaners to remove any localized fines around machinery. Those vacuums have to be emptied immediately. If they are not emptied the aluminum and water (internally to prevent an explosion) will generate a gas that will build up overtime (days). I know of several incidents that at the end of the week a vacuum was used and was not emptied. It sat for several days and then started up, resulting in a spark. The resulting explosions caused severe burns. Some workers succumbed to their injuries. Again my goal on commenting to you is two fold: respond to your comment respectively, and educate anyone who many read my comments. I simply do not want anyone to be injured or killed in a workplace incident.
I have a friend that worked at the local aluminum smelting plant here, one of his co-workers had brought in new dies from the snowy yard and put them directly into to the die-machine (the dies where for casting large bars 6’x2’x0.5′ I think) and when they poured the metal it created a steam-explosion due to the amount of snow that was left in the die. My friend had 60% burns 60%, mostly on the back of his body, cracked thoracic vertebrae and a broken arm from flying debris and molten metal.
The normal procedure was to always pre-heat/dry the dies, in this case it was at the end of the shift so the guy getting the new dies skipped the pre-heat/drying so he could leave a bit early.
This happened about 25 years ago and he never fully recovered and he haven’t been able to do any type of physical labor since then due to the pain from his back.
Hello Rocky, I am sorry for your friend’s injury and the lasting effects that they have suffered. I pray that anyone who has read your comments understands the importance of following your training, never skipping steps, and never make assumptions. With all due respect to your injured friend. On that day your friend’s coworker did not follow they training. By properly heating the die. He skipped steps, and made the assumption that all would be ok. We all know that by this worker’s actions Rocky’s friend has had to live with the aftermath. As I talk to production workers I ask a rhetorical question. What is worst than being injured or killed in the workplace? The answer is that one’s actions can result in the injury or death of a co-worker. Rocky your story illustrates this point.
First thank you for the article, in my experience on this topic I find nothing incorrect from what you post. Your use of the term fragmentation is grammatically correct, but not used in the industry. Regardless, I want to clarify one matter. Molten aluminium and water react through either a physical or a chemical reaction. The physical reaction as you explained is when water is covered with molten aluminium. The water molecules expand forcing/propelling the molten metal away. In this reaction 3 pounds of molten aluminium will result in 3 pounds of solidified aluminium spread about. This reaction is common with other metals, such as molten steel, molten copper, molten brass, etc. Aluminium is unique that it can chemically react with water. In this reaction aluminium bonds with oxygen from water forming aluminium oxide releasing hydrogen (in the form of energy). In this reaction 1 kilograms of aluminium would generate a force equivalent to 3 kilograms of Trinitrotoluene (TNT). When this chemical reaction occurs the molten aluminium disappears and all that is left is aluminium oxide. Two common characteristics to a chemical reaction explosion is the white cloud (smoke) generated, and the site being covered with what looks likes “snow” (actually aluminium oxide). Lastly, chemical reaction can occur on a molecular level. In other words, visible water does not have to be present for a chemical reaction to occur. This most commonly occurs through the transfer of salts onto tooling, scrap, etc.. Salts absorb water (e.g., think about a salt shaker with rice in it. Rice is used to pull the moisture out of the salt). In aluminum plants salt is present in fluxes (used to remove impurities in the metal), and tracked into the workplace on the sole’s of employees boots (e.g., road salt). These explosions can be so large that they can generate earthquakes. Here is the most recent Force 3 explosion (https://aluminiumplantsafety.blogspot.com/2020/09/casthouse-is-destroyed3-dead-4-injured.html) That is why it is imperative that no hand tooling (tools that are placed into the molten metal) should come into contact with the work floor.
Let’s review the photos in the article: Photo 1 is simply a molten metal spill, no explosion occurred. Photo 2: swimming pool is not dangerous in terms of dropping in the water. The danger would be from the melting and transferring of crucible to the pool. Photo 3: is a physical reaction, there was moisture on the scrap that was being fed into the furnace. Photo 4: was a physical reaction, no more than 50 pounds of molten metal reacted with water in an emergency drain pan.
Overall, I liked your article and keep up the good work!
“Aluminium is unique that it can chemically react with water.”
Sodium says what?
> In this reaction aluminium bonds with oxygen from water forming aluminium oxide releasing hydrogen (in the form of energy).
Hydrogen in the form of energy?
>In this reaction 1 kilograms of aluminium would generate a force equivalent to 3 kilograms of Trinitrotoluene (TNT).
No. Just no.
I bet it’s a powerful bang but TNT detonates, aluminium and water doesn’t, so comparing them on the basis of energy doesn’t work, or in any case, since the “force” different high explosives generate depends on the rate of detonatation and how the material is confined. Even the hydrogen explosion is technically a deflagration, which is slower than a detonation and generates less force, depending on the external conditions. A cloud of hydrogen in air will not detonate.
One food calorie is almost equivalent to a gram of TNT, yet you can’t split rocks with a piece of toast and a blasting cap. You just get a mist of charred toast shooting out of the hole. The TNT equivalent only counts energy, not force or impulse, so it’s a bit misleading. That’s why making the comparison that a kilogram of aluminium is equivalent to three kilograms of TNT is true but completely wrong.
Dude be Wrong!
“Recently, I happened to be glazing over an article on aluminium casting with interest”
I’d like to hear about this in detail. This article can be reduced to four words: “Don’t be an idiot.”
Burns to the top of the feet are almost a rite of passage for foundry workers who get showered in molten metal droplets when there is residual moisture in a mould and they failed to put their spats on, or failed to properly lace up their foundry boots.
Wet tooling or moist slag are another excellent way to cause sudden, explosive molten precipitation, much like a volcano’s pyroclastic blast zone in miniature over adjacent workers, as alluded to by other commentators.
If someone claims heat well above 100C is no good at causing rapid expansion of water to push stuff away rapidly, i.e. harmless in metal casting scenarios, then they need to explain how steam engines or steam turbines work.
A couple of decades ago a friend of mine was managing experiments at Sandia Labs to develop models for core melt accidents, in this case hydrogen explosions. The question was what happens when the aluminum in the fuel cladding melts and hits a pool of water. The experimental setup contained a couple of kilos of molten aluminum, a large tank of water, and shielding. A high speed video camera (10K fps, I think) captured the test. In frame 1 you see the molten aluminum leave the container. In frame 2 you see it halfway to the tank of water. In frame 3 you see …. well, nothing. The entire apparatus had been destroyed. The Al reacted with the water, freeing hydrogen, which then detonated. I guess they needed a faster camera.
I used to have a VHS copy of that video. Can’t find it via google. Any chance you have access to that video?
I spent some time working in a bronze foundry, and the rule there was that ALL food and water was to stay in the break room, period. If you needed a drink, you either got one from the break room fridge (and drank it right there), or you went without!
Can vouch that this is a concern at Zinc foundries in particular also and witnessed this happen mildly until later that afternoon/evening the young man showed up in my lab almost in tears with 3rd degree burns all over his exposed body just prior to being transported to the hospital from loading wet scrap from a lot, into the rotary furnace.
Technically, the plant I worked at/for was a non-ferrous allow recycling center and I ran the ICP-AE. Though, most all the material I worked with were for zinc dross. There were some lead and aluminum samples I worked with. Same concern anyways.
Same if I recall at the gray iron foundry I work at/for also though don’t recall any incidents other than their closing due to EPA concerns which was a bummer losing all that mass and energy influenced to implement infrastructure that was good business not to grandiose or luxury products either. Sad the old Bosch plant completely gone the first time I saw and even now days. What a waste to an economy.
I remember casting some aluminium in secondary school using sand in the metalwork class. It was to make the handle/seat bit of a walking stick thing. Was my school secretly hoping the class would die in an explosion or does this exploding thing require large quantities of molten metal to happen
Sand casting is much less risky in that sense; you’re usually pouring small amounts of metal and slowly, and while there is moisture in the sand it’s incredibly porous allowing whatever steam is generated to diffuse out safely. It’s only when water is trapped or enough comes in direct contact with unoxidised molten aluminium (which generates hydrogen) that an explosion risk becomes significant. Hence why foundries which deal with significant quantities of metal, large crucibles and solid casting containers have to be much more rigorous in their safety procedures.
Very helpful insight. I was just wondering how this fitted with sand casting, lost wax casting etc.
Indeed, you probably can pour metal into water in most situations, as the steam will be generated under water, with a result little more dangerous than a pan of boiling water (hydrogen aside in the case of reactive metals).
And you can probably pour water into molten metal in most cases, as it will float on top and boil harmlessly.
The problem, as i imagine it, (and it is a very big problem as has been seen here), is when somehow water is introduced under the surface of the metal. Or when the metal and water are in a sealed volume.
The former can happen when cold, wet stock is introduced to the melt (I can imagine the cold ingots keeping the water liquid long enough to get under the surface) and the latter would be the situation with a cold, wet die-casting die.
My (minor) accident of this type was caused by a drilled hole for a thermocouple being full of water when the sample was put in to molten sodium hydroxide (400C). The water was held under the surface, vapourised and spat a very hot liquid at the experimenter. I imagine that a thermal burn from NaOH is rather rarer than a chemical burn.
You reminded me of what a guest did on “The Tonight Show with Jonny Carson”.
He heated up a solder pot (full of solder), soaked his hand in water, then quickly dipped his hand into the solder pot touching the bottom of the inside. He was not burned, as he said the water remaining on his hand turned to steam when it hit the solder and briefly formed an insulating layer protecting his fingers from the heat.
Leidenfrost effect, if you are not familiar with it.
It was exactly this. The metalwork teacher, the department head, the principal, superintendent, school board, and the state board of education were all conspiring in hopes of killing a classroom full of kids and damaging a school building. You got ’em!
The head master was held hostage by a pupil with an axe for a few hours. Could of been payback? (it wasnt me BTW)
There was some speculation that the “explosion” at the tower of the World Trade Center was caused by molten aluminum from the airplane that encountered water from the sprinkler system. (Aluminum melts at the relatively low temperature of 1221F. ) In some of the videos of the tower, you can see what looked like molten metal pouring out of the structure. This explanation of the apparent explosion was rejected by the committee investigating the tower collapse. Check out “aluminum explosion”
I just had a trace amount of water in the form while casting some brass. Now I have a scar on my shoulder.
ALWAYS WEAR PROTECTIVE GEAR!
Of course if you pour molten metal in the ocean, nothing happens.
I think the guy pouring the molten metal into the swimming pool is missing the whole point. That does not really prove anything. The huge amount of water in the pool can cool the molten metal without much if any of it turning to steam, and any steam is not contained. If you were to repeat that test but instead poured that molten metal a soup can with a 1/4″ of water in the bottom, you would have an entirely different and more unpleasant result.
I don’t get why people feel the need to rebut stuff like this that has been worked out over a few hundred years. People who work in foundries don’t come up with stuff like this just to be annoying. It is generally because a bunch of people were maimed or killed somewhere along the way.
> People who work in foundries don’t come up with stuff like this just to be annoying. It is generally because a bunch of people were maimed or killed somewhere along the way.
Amen.
“Safety regulations are written in blood.”
Thank you Mark for your comment. I was assisting a company on their molten metal procedures. The backstory was the authors of the procedure were gone for decades. The company recently split in half leaving it without anyone with experience on molten metal safety in terms knowing the origins of the document. Most of the senior technical employees went with the new company. I was left to defend the stringent safety procedures. Time and time again I would be asked, “why is this required when we have not had an incident because of this procedure?” I was left in an awkward position to defend the original document. I finally commented that the procedures listed were the result of blood on the concrete floor. Very similar to your comment “Safety regulations are written in blood”. In fear that important safety procedures would be reduced or watered down. I contacted one of the former technical managers now working for the new company. I will never forget what my contact told me. “Tell them, they have a gun pointed at them with the trigger cocked. It has not gone off for a long time. If they change or remove anything from the safety procedures. Do they honestly believe the gun won’t go off?” Thankfully, I was able to convince the company to keep their stringent safety protocols. It is important to acknowledge that some safety procedures were written in response to an incident. Do not remove those procedures or alter them without serious consideration of what could occur in the future.
Then again, the procedures can also be voodoo safety. If there’s a cocked gun pointing at your face when you work, are you sure that morning ritual of three minutes of River Dance will help it not go off? How are you sure?
Some measures are ineffective for the original issue – they are installed just because there was a demand to “do something”, regardless of whether it actually helped with the original cause of the accident. In the imaginary example, the rationale for the “River Dance” might have originally been to shake the stones out of your shoes so you don’t trip and fall into the smelter – but the reason has been forgotten ages ago and people are now doing it out of ritual and doing it wrong.
An actual risk audit is in order, not just enforcing the old rules by faith.
Dude, I agree with your points. The difficulty with molten metal explosions in the aluminium industry is the numerous factors that have to be aligned for an explosion to occur. Some like to use the analogy of swiss cheese slices. Only when all of the holes align does an incident, for our discussion for an explosion to occur. The point I was trying to make in my previous comment, no doubt I failed. That many times companies will remove or water down safety procedures because they either have not experienced the hazard or have no experience per se with the hazard. Though we are discussing molten metal explosions this issue is commonplace within older companies involving all sorts of hazards. Management sometimes fails to realize that one if not the main reason that their plant has not experienced a hazard is because of the safety protocols installed decades ago. Lastly, I agree audits should be conducted on a regular scheduled basis. When it comes to this hazard, it can be simply eye opening to those new to our industry. Further emphasizing this hazard is the explosions that occur throughout the globe. Sadly, going back nearly 20 years there has been at least one catastrophic explosion that destroyed a casthouse every year. I pray that streak is broken in 2021.
Agreed! Have worked in a large aluminum foundry for over 25 years. Have seen and experienced quite a lot during my time. It only takes one drop of moisture trapped under aluminum to cause a severe reaction, and one moment of stupidity to see the negative results of it. It can come from that one moment you least expect. From large molds (sand or permanent). Examples are when the molten aluminum leaks out and onto a concrete floor. The heat draws and traps the moisture from the floor almost instantly, making concrete look like pop corn popping. I have also seen smaller sand molds with chills in them, that collect moisture from setting for a couple of days, and this causes a reaction. I have seen mold floor utensils used for prepping/ cleaning/ preparing of aluminum- not properly coated, dried, heated, etc.,, that have caused reactions/ explosions. I have seen a guy rake out a furnace into a sal that someone threw a coke can in. This trapped moisture and blow the whole furnace door off. I have seen guys going to skim a crucible/pot, only to realize they did not preheat the skimmer which was cold and contained moisture. I have seen a great many things… but the things that tend to get most people hurt in the aluminum foundry is the lack of knowledge, proper training, safety/PPE, the lack of caring, & sometimes oversight to where we get to comfortable and forget a simple part of the process.
Pouring molten lead into water used to be (is?) a German New Year tradition.
https://en.wikipedia.org/wiki/Molybdomancy#Germany,_Austria,_and_Switzerland
And some details on how to do the divination:
https://alpinevillagecenter.com/bleigiessen-lead-pouring-predictions-new-year/
But this is the case of a lot of cold water and a little hot metal.
I thought that screen capture of the pour into the pool looked familiar. The youtube channel Backyard Scientist!
https://youtu.be/JEEOkMW1CYI?t=6
It affects not only aluminum, but every molten metal – also steel. If water gets into the melt of a steel mill (e.g. in the cavities of an scrap engine block), catastrophic explosions do occur. These have literally been known for centuries.
The point is: there has to get water INTO the melt (below the surface). There it expands suddenly. A few litres of water are able to throw tons of molten steel out of the vessel.
Just a little bit of moisture is enough to make an impressive bang. It used to be a popular joke among trainees in a steelwork to make the colleague’s sample spoon for the liquid steel a little damp …
On the other hand, if you pour molten metal into a pool of water, not much happens. The metal solidifies instantly and the water heats up slightly. So nothing at all can be proven in terms of the explosiveness of water in metal (not the other way around).
If you are worked in the real world and you see a news or a post with a image of a forklift, then you know what is the topic of the post.
If you are an office-dweller or simply a student, then you are most clueless about it, but sh*t happens at work so often that :
* You can attest that some people born stupid.
* You are amazed that we, as humanity, we are survived so much time.
Any molten metal not just aluminum with water is dangerous! I work in a steel foundry for 25 years I seen some stuff.
To the author, “Aluminium Association” is an incorrect name for the organization. The correct name is “Aluminum Association”. I.e., American English spelling, not British English.
The difference is obvious.
Pouring molten metal in a pool is totally different than pouring water in a pool of molten metal.
Same thing with grease fires.
A burning deep-fryer is super dangerous if you add water.
A regular pan with a few ml of burning oil is totally safe to extinguish with water. Or pouring a small amount of hot oil into a wet sink will safely cool it too.
Does anyone have experience with a wet sprinkler system in an aluminum foundry?
Here in the uk, I do alot of magnet fishing for metals with my daughter – anything really its fun over here and good to explore the country more. Now recently i found a spot where i went to on a bridge, and i saw what looks like a aluminium apple macbook. That said it is in water only a few feet deep but with no access to the water at all from both sides of the bridge. Let’s just say it is still there and i want to grab it but my magnet does not pick up anything alumnium, So wnated to reach out to ask anyone if there is such a magnet or device to use relitevely cheap to buy or order to obtain the laptop from my rope i have. I mean i can see the laptop very clearly from the bridge but would be curious to get it out, and retrieve the data from it, and hand it back to the person who seemingly lost it over the edge, Why on earth you’d have a laptop on a bridge is something i cant fathom. Any help appreciated. Oh and i work in IT and one such service is liquid damaged devices, so am interested in retrieving this if i can.
I think it would need to be something sticky rather than magnetic.
https://source.wustl.edu/2019/04/the-sticky-science-of-underwater-adhesives/
Or maybe some sort of pump and a sucker.
Thankyou Andy, what i have done so far is plan to return to the spot where the apple macbook is sleeping under the water by a few feet only and clearly visible to the naked eye. I have devised a metal sheet, attached rope and caribeaners to each corner and this will be coated onsite when i am ready to lower down with rope over the spot with a heavy magnet on top of the sheet of metal to give it weight underwater. The next stage is locate a glue that can be used and applied to the metal plate i am lowering into the water and hopefully if i follow the current correctly which is quite weak, i should hover over the area and drop the line to give it a good seal from the glue. only after 30 minutes will i be able to lift it up safely onto the bridge. sounds like a plan right….lets hope it work, just need to locate this glue now.