Once upon a time, the automobile was a mostly mechanical beast, but no longer. Advanced electronics have weaved their way into the modern car, from engine to infotainment and climate control to the buttons now sprinkled throughout the passenger cabin. The gains in amenity and efficiency can’t be sniffed at, but it leaves manufacturers reliant on semiconductor suppliers to get cars out the door. Over the past year, it’s become much more complicated — with many automakers having to slow production in the face of integrated circuit shortages that can be traced back to Spring of 2020.
Shortages Rippling Through the Supply Chain
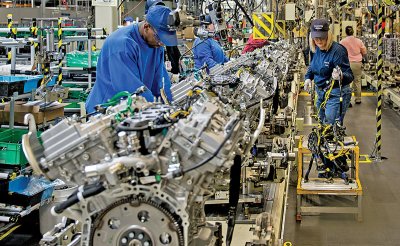
Unsurprisingly, the blame for this situation can be lain firmly at the doorstep of the ongoing coronavirus pandemic. Automakers were forced to scale back production as factories closed to avoid spreading the deadly virus. This meant slashing orders with suppliers, particularly as the just-in-time nature of modern automobile production means there’s little to no space to warehouse excess parts in factories. It coincided with a drop in automotive sales during the early part of lock down, as few contemplated new car purchases during the turmoil of March and April, 2020.
In this same period, demand for consumer electronics shot through the roof, as schools and businesses switched to remote operation. Webcams flew off store shelves, and companies spent great sums equipping their workers with laptops to enable their staff to work from home. With a shortage in that sector, semiconductor foundries switched production lines over to churn out the parts in greatest demand, scaling back on parts for automakers who had curtailed their orders.
As the year progressed, demand for new automobiles rose, often attributed to general fear of being exposed to the virus causing consumers to avoid public transportation. With limited production capacity, chip foundries can’t simply make more chips; instead, automakers have had to shut down production on some lines while they wait for deliveries to catch up with demand.
Honda, Toyota, Fiat-Chrysler, and Ford have all been impacted by the shortages. Tier-one supplier Bosch have noted the shortage is particularly acute in parts used for engine and transmission control units. With these parts being particularly specialised for automotive applications, it’s likely their comparatively small market has meant that foundries are focusing on shipping parts for consumer goods first thanks to their higher volumes. With lead times measured in months, it’s likely to be some time before car manufacturers can get back to full capacity.
You Need Every Part to Finish the Build
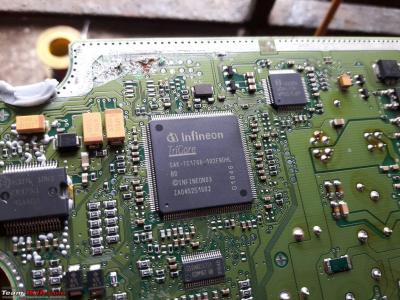
It’s not the first time automakers have faced shortages, and it won’t be the last. A fire at a magnesium casting plant in 2018 led to widespread shortage of structural parts used by several makers. In 2012, a disaster at a German firm producing a chemical for fuel line coatings threatened to curtail production.
While having redundant supplies of critical components is desirable for automakers, it isn’t always practical in the modern marketplace. Chip fabrication plants cost over one billion dollars to build. Idle production lines don’t make money, so there is rarely spare capacity in this industry. Production runs are queued far in advance, with lead times to spin up a new run measured in months. Combine this with an aversion to keeping parts on hand due to the just-in-time nature of modern supply chains, and it’s clear that it’s a problem that promises to reoccur.
Short of a major cultural shift in automaking on a global scale, shortages aren’t going away any time soon. Instead, now and then, the average consumer will have to wait a little longer for that new car to roll off the line, and automakers will have to keep making frantic phone calls to suppliers to get parts on the boat. Of course, if you’re an armchair logistician yourself, sound off in the comments with your best ideas to solve this conundrum!
I’m an autospark/ diagnostic tech/spannermonkey, part shortages are a real issue right now, most every big order I put in has one item on indefinite backorder. Not just electronic parts obviously , having to get very creative to get some cars out the door. Far from ideal, and seems to highlight the main issue with just in time manufacturing.
When I worked at GM, we used the term “just too late” for this practice. Upper management loved it though
I always thought the moniker ‘Just about in time.’ was a little closer to the truth…
Eeyup. “Just in time” is one little problem; one minor glitch, away from “not quite in time.”
yuuuuup. ball bearings, O rings, structural steel, you name it, its on backorder.
US manufacturing is on its knees.
You said it, with everything on back order .what makes no sense is getting behind means parts are going out and some orders will be late. It looks more like nothing is going out.
Has anyone else noticed shortages in semiconductors on Digikey? I’ve had trouble getting specific FTDI chips, and voltage regulators, and crystal oscillators.
From 2019 onwards, the highest value capacitor in any small smt package was backordered like a year out, across the whole range of manufacturers. The explanation I was given was that cellphone manufacturers have a habit of as soon as they see available stock dropping consistently, they buy all the remaining stock so they won’t be caught by massive lead times.
The result is that they’re acting as invisible warehouses, and suppliers can get caught in nasty seesaw battles where a perceived increase in demand leads to an outsize increase in purchasing of stock, followed by no orders at all because they’re operating off the surplus they bought. There have been periods where our sales have looked like a square wave with a six month frequency.
Like toilet paper between March and July 2020.
I had an IC that was critical to a work project go from thousands in stock on all of the major sites to 24 week lead over the span of 2 months. Fortunately one disty had some stock and was able to get a few hundred to fulfill the build we we needed to start.
My company is hoovering up certain crystals as soon as they become available. Apparently there was a fire at a large AKM factory, and the factory will be down for at least a year, so there are big crystal shortages.
A fire at a magnesium factory sounds like a joke someone would make about a nightmare scenario.
The numerous examples of fire in an ammunition or fertiliser ship would like to disagree with you, as would the fortunately rare examples of fire in a nuclear reactor.
“fertiliser ship”
The whole industrial agriculture is sadly based on fertilisers, which goes into the water streams and destroy the ecosystems.
I thought Beyrout explosion would be a wake-up call, but no, there is too much money involved.
Before fertilisers, there was not enough available food for all people. Since then, we have 20x more people. How do you propose to feed them without fertilisers?
Feed them less, and feed less of them.
The solution is to have fewer humans on this planet. 1 or 2 billion sounds like a good number and will resolve the root issues of many problems on our planet : resources scarcity (that leads to war), pandemic (that are caused by deforestation which is needed to support humanity growing number).
I don’t get why people cannot see that and just refrain for at least 3 or 4 decades to make children. This is an easy solution but we somewhat makes it hard.
There were studies done 3 decades ago that calculated that from all the land already designated agricultural at the time, using the best known common and sustainable methods (Not anything super high tech) that we should be capable of feeding about 30 billion people.
The simple fact is, that we have ample ability to feed the current population, and that half of it is starving for political and not practical reasons.
The fertilizers themselves also kill off a spectrum of soil biota, leading to compaction and reduced water holding capacity further increasing run-off and fertilizer needs. Gabe Brown has several good talks on his methods and results.
Soil-lent green could be all the rage in a techno dystopian city near you soon!!
There are loads of ways we can make agriculture more sustainable and more widespread and do it without any shipping at all.
1 egg-sample is the fact that if about 1/10 or so households had backyard chickens, the egg industry would be destroyed overnight. This is great seeing as how chickens are easy as hell to take care of and feed, growing the bugs for them is also super easy and cheap. Furthermore, free range chicken eggs knock it out of the park.
You can pack 1/4 acre with enough vegetables to make about 100 grand a year once you’re all set up, it’s not super difficult. There are tons of people doing so. Curtis Stone the urban farmer has a great series on how to do just that. Push come to shove, if people really wanted to save the planet, they’d start by sequestering carbon simply by making a compost barrel and a nice garden. You can actually get quite a lot of carbon back into the soil this way, especially when so many people pick up the hobby that it dumps carbon on scale.
But alas, instead we waste so much water on growing lawns that it’s the largest watered ‘crop’ in the states. Then we burn a ton of fossil fuels driving around in trucks and lawnmowers to trim it and make it ‘look good’.
to me, a manicured lawn looks like a waste of space and a giant pile of ignorance.
Look up ‘reverse desertification’. There are a lot of people that do good work in that area as well, and you can apply the principles in your yard.
If you don’t have a yard. or limited outdoor space, you can use 55 gallon barrels to make vertical gardens, or just use your money to buy stuff from locals. Big Ag is one of the worst things to happen to our food supply, and our health. The algae bloom in the gulf alone destroys enough wildlife to feed countless people via the seafood, but we just keep destroying that too, for what? soy beans and wheat products? meh. Not healthy, and not worth it.
The Beirout explosion is only an example of how not to store potentially explosive materials and why welding metal right next to giant bags of very old ammonium nitrate is a bad idea.
When applied properly, barely any fertiliser gets into the water system. And since farmers have incentive to use as little as possible (because artificial fertilizer is expensive) the over-application has gone down massively in the recent decade to the point where many farmers now have active dosing systems that apply just enough fertilizer for each particular area of soil (usually sampled in a grid every hundred yards/meters or so)
The recent fire at the AKM factory knocked out a load of VCXO suppliers, and mobile phones/modems (mostly) all use (TC)VCXO’s.
https://www.pro-tools-expert.com/production-expert-1/2020/10/29/akm-factory-fire-could-affect-supply-of-a-to-d-and-d-to-a-convertors-for-12-months
Some of these things go into cars too, so the car won’t get its diagnostics modem…
Just in time has a lot to answer for – but the beancounters love it!
This is a good example of poor management. They assumed there would never be a disruption in supply and it came back to bite them. No sympathy for those who are the cause of their own problems.
I think I might disagree with this. The implication here is that the auto manufacturers should have had months (or years) worth of raw materials on-hand in case the entire global supply chain got disrupted. Just-in-time (or close to it) is the standard. I think such a huge amount of inventory would be quite a waste of capital. It’s actually much better to suffer the single year (give-or-take) of production problems during the once-in-a-lifetime crisis. :-)
you cant do years of stock when the designs change every 2 years… even just a tweak deserves a full redesign and throw all the old stock out. the new microcontroller os so much more useful than last years varient. /sarcasm
With the volume of parts that that the OEM suppliers work with, JIT makes a ton of sense. Its not even supply shortages that are the issues. In the manufacturing industry I work in the OEM’s and tier 2 suppliers are looking for quantities that are 150%or more than what the original capacity is.
Of course there is shortage. They need those in the vaccine. *
(* sarcasm)
I am surprised, people still buying new cars during pandemic and unemployment.
Don’t forget that stimulus money has milked things along. Even beating a dead horse, if beat hard enough, will move.
Because most people aren’t unemployed, and very large portions are the economy are business as usual. Many people that did loose their jobs found new ones.
Where I work it amounted to a couple month hiccup where we kept working… since we knew our contracts would get paid just delayed a bit.
The people that did get completely shut down were in many cases the very people likely to have no effect…. small businesses. Certainly none of the big businesses considered essential were shut down.
Hmmm I was an Estimator for one of the largest printing companies in the world. A lot of people were let go.
some of them must have shut down. There have been shortages of sheet metal for an HVAC mfg in the midwest a while ago, and difficulty getting copper piping, early on it was meat packing,etc etc ….
Your right. Around here business as usual… Small business and the ‘travel’ industry taking the brunt. Several of the people I work with have got new vehicles. In fact when I got my truck serviced at the dealer, the mechanic told me they have had one of the best years ever. Around town it seems that fast foods and such are having a hard time finding employees to work. As for my family we still go out to eat, and go to the stores as needed. We just have to mask up for some reason…. Can’t wait for ‘that’ to get back to normal. More government overreach. Actually we’ve had 4 great years here in the states. Now probably see some belt tightening and other things to hamper the economy. Sometimes I think man is his own worst enemy.
“for some reason” hmm I wonder what reason that could be
Ask the same question again in ten years and I reckon this won’t be any issue anymore. Robotics and AI will be picking up the slack & localised fabrication will become cheaper to operate.
What do you think?
“I say your civilization, because as soon as we started thinking for you it really became our civilization, which is of course what this is all about. Evolution. Like the dinosaur. Look out that window. You’ve had your time. The future is *our* world. The future is our time.”
Ostracus:”And what are you going to do with this civilization that’s yours? It’s seems to be as dead as ours. Your progress depends upon ‘the one’, us.”
Probably not, production is already extremely automated, the robotics and AI “revolution” is about automating things which still require human hands or heads, on production lines both of those have already been long ago replaced by simpler things which are good enough for such a predictable environment as a clean factory.
Right up there with open source hardware.
I don’t see why board fab and assembly can’t be mostly the same thing. A lot of things could probably be done with the same 100 parts, and only a few unique ones.
We’d have to stop letting the analog and mechanical guys have MOSFET Fun Times with their creative ways of saving 8 cents, but really, how many times do you see something that isn’t just a power supply, microcontroller, some switching, some kind of communication, and maybe buttons?
If all of our design tools made it totally frictionless to order assembled boards with something like a smaller and cheaper open parts library from Seeed, maybe we would see less nonsense.
Cars are a special case, because there’s safety critical analog stuff and high quality parts.
But for everything else, you probably don’t actually need a 2.3k resistor and an 0.1273uF capacitor. Just figured out how to make accurate ADCs with built in precision references cheap enough and do it all in software.
Maybe we can actually start repairing things again if we can reduce out total unique parts to the point where a repair shop can stock all common chips.
I can’t speak for other circuit designers but where I work roughly one third of the components on our evaluation boards are there to reduce radiated EMI and reduce the susceptibility of the system to radiated EMI from other boards. That’s hard to do in software. You can dither or slightly mismatch clocks, although that’s often not software either, but a lot of this you just have to sit down with an EMI test setup and start tweaking parts.
“Just-in-time manufacturing is dead… long live Just-in-time manufacturing…” ;-)
Even before a product is out of the certification lab, the essential parts must be secured as inventory for 1 year. SMD parts tend to “rot” after 3 years, and will still slowly oxidize in sealed bags with desiccant.
Standard values of common discreet components are generally acceptable risk exposure. However, if your product depends on some “unicorn-part”, than management needs to accept the initial cost of risk mitigation. RF SMD parts are famous for EOL notices too… digikey sells tiny inexpensive matched 50ohm wide-band attenuators. These save so much grief putting together a project, and yes stocking reels of PAT1220-C-6DB-T5 family of chips in 1dB to 10dB is not that expensive given they reduce part counts/space, and can be reused in many designs given they are essentially just a special resister setup.
I think a lot of resellers speculate on popular components, and often purchase stock to drive demand/prices even higher. We have one inductor that cost $1.58/pc in 2018, and is now over $4.52/pc from anywhere. Population options often won’t save you, as these folks likely target components that have few alternatives. Its a shame, but sometimes the part skelper wins… you have to pay the premium or the line is EOL.
Another thing that occurs is you’ll see new chips launch at rock bottom prices to drive adoption… then they’ll quadruple the price.
Time to optimize designs and reduce chip requirements
Anyone know how one manufacturer is setup for this vs another? Is Tesla’s push for for vertical integration a plus or a minus. How about the reduced need for ics in components and pushing for a centralized cpu?
I know Coilcraft USA distribution was shut down for 1 month.
Sometimes it feels like “management needs to accept the initial cost of risk mitigation” is more of a nice added feature that will eventually be gotten around to after it exits the alpha state the project launched in than an actual real, respected requirement.
When you run at full throttle all the time there is no extra throttle available in times of need.
I blame accountants for changing the working world.
Demand for automobile DID NOT “rise. The article YOU LINKED shows that they never returned to normal levels in 2020.
Are you media illiterate?!
Why do cars even need custom controls? Why can’t it all be standardized like ATX, on nice swappable connectors, with generic modules that use swappable firmware chips?
No more complaints from there car people that you can’t work on your own cars, no more not been able to fix something if they stop making parts, no more parts shortages, just reusable made by the billion PLC-like control modules, that could find their way into non-cars, many better reliability with less duplicated effort, and the possibility for open source controls.
In a perfect world, maybe we could go full drive-by-wire with less panic about reliability.
The IBM PC was a very unique piece of major awesomeness. Now every time someone wants to standardize anything, someone just posts XKCD 927.
The world would be a better place if people did *everything* based on documented open standards and swappable modules, and if people avoided custom “made to fit” stuff.
Sadly hacker culture doesn’t really emphasis one of its very best achievements over off the shelf stuff, and most projects are standalone, non-modular things.
I work in automotive electronics. It appears to us that the majority of people purchase new cars based on differentiating themselves to their peers by their purchase choice. As such, if you’re not talking about a niche where consistent uniformity is the quality metric (as it was with IBM management’s personal car purchases, for instance) the majority of purchasers are going to want cars that visually differentiate and are recognized by their design. That means headlights, taillights, dashboards, most of the driver-facing electronics, are going to be totally different from unit to unit. (Ford F150, which is the bestselling vehicle for like the last decade continuously, has just by itself a wide range of different headlights, with left and right sides using partly different components because of NTSB requirements in how illumination patterns are distributed on the road, so in one make/model you have like six different headlight units.)
People won’t buy swappable module cars.
You can’t even convince a lot of people to buy Mustangs that have more powerful six and four cylinder engines than the old eight cylinder engines they’re replacing, and almost nobody even sees the insides of an engine, because Mustang buyers have a fixation with V8’s.
The whole existence of Veblen goods is an example of how standardization in status goods isn’t economically viable. I think this is ridiculous, but people buy expensive goods with their hearts not their heads.
Most projects are manged by shortsighted, ladder climbing, twits who are continuously rewarded for finding new ways to squeeze more money from an old idea. If ever a part gets so popular that it can be replaced by a generic replacement, a new, completely incompatible, part can be released and included in the latest $product.
This even happens in the industrial world, Siemens just obsoleted all its old pushbuttons, regular old springloaded buttons, and the new line of buttons does not fit the same hole, does not use the same contacts and so requires us to buy an assload of other parts every time we replace a pushbutton. Management yells about the cost but also refuses to stray from the OEM because switching to a generic brand is “unprofessional.”
I used to work in automotive electronics, the amount of vibration and temperature and grit/dirt toleration required from automotive electronics means it needs special connectors rated to stand this, special chips, and the PCBs are all pretty much encased in thick metal shells.
This makes it rather difficult to use boards that just slot together, the connectors on these things are such that you sometimes can’t operate them easily by hand, and the metal case on each module is used as a heat sink. Sticking multiple boards in one sealed metal enclosure sounds like poor thermal design compared to the current standard of each module being sealed in it’s own metal case.
Laptops are using very similar components from the same suppliers and yet they don’t have swappable motherboards nor batteries. The only swappable parts are the M.2, SATA, SODIMM where there are industrial standards.
NIH at work.
Yeah, really. And along those lines, why aren’t automotive hardpoints standardized?
Think about it. You could have different sizes of engines/transmissions/etc with standardized footprints. A Toyota with a class-N engine mount could fit a class-N Subaru engine, and vice-versa. Chevy could make a small-block V8 for mounts that are two sizes too small. And you could drop an Audi transfer box into any light 4WD system.
Oh, I can dream…
You are dreaming of good old soviet union with its planified economy. Except you won’t have any tech you mention, just a two-stroke engine in a glorified steel shoebox.
My brother-in-law drove a (“well-seasoned”) mid 80s GM with a V-8. Being an obsessively frugal guy, when the engine gasped its last, he dropped in about the smallest GM V-6 (from a boneyard) that would still approximately connect with the transmission and drove that til the frame rusted past the point of safety. It was called a Frankenbeast for a reason…
They could have used a single 555 …
Damn, you beat me to it.
OOOooo the evil communiststs are comin!!! What a load of crap, mac.
Yeah it’d be nice to have standards, but even if we didn’t have chickens like mac here, it’d be a hard sale to any company to have any sort of collaboration with a competitor. It seems impossible even between different departments of a single manufacturer. Making the world a better place, even just a little bit, is not in any business manuals or legistlation. Mac here likes to drink snake oil, cause it’s !!!freedom!!!
God damn this comment system.
Look to the floods in 2011 in Thailand for a precedent:
https://www.reuters.com/article/us-thai-floods/thai-floods-batter-global-electronics-auto-supply-chains-idUSTRE79R0QR20111028
After this, those of us at the grinding point between academia and manufacturing noticed a sudden interest in (and occasional research into) large-scale supply chain failure, working on risk exposure and cost among other things – essentially the “for the want of a nail, which country is lost?
One study (done locally) highlighted that the entire output of “a pre-eminent automaker” depended on a single component, for which there was one supplier and one manufacturing facility only – if that burned down, everything stopped. I’m not going to say what it is or who they were, just to be evil and provoke a little thought, but they responded by helping that supplier develop alternate production facilities (ensuring a good deal of advantage for themselves in the process).
It’s also worth remembering that auto manufacturers are not the vertically integrated manufacturers of yesteryear, but assemblers of supplied components from contractors. They likely don’t have (or have never asked for) the subassembly’s parts lists to examine the secondary risks in the same way that they examined shortages of those “finished” components, much less the arbitrage that may happen when a sub-supplier will take on the penalties of not supplying one component (chips) while expanding profits with them somewhere else.
Churning, faddish management of corporations usually has the corporate memory of a goldfish, so these lessons are examined (perfunctorily), changes implemented (sometimes) and it’s mostly back to whatever infighting among budget lines had been going on before. Taichi Ohno and Kiichiro Toyoda had a good deal to say about shortages and adaptation, since Toyota developed its Just In Time systems under government control and wartime production, but this all gets swept away in a billion consulting “slide” decks and gabble.
“Just in time” usually is implemented as “Just enough for tomorrow – the contract says so” — and here we are.
There’s some kind of event once a decade, and lots of handwringing afterwards about “There has to be a better way!” like the infomercial guy is just gonna pop in and sort it all out for us. The damage is patched around a bit, the duct tape holds, ppl forget it was a temporary fix, then a few years later something else.
This is one of the earliest I remember, though no doubt there were others in other industries before that…
https://www.washingtonpost.com/archive/business/1993/07/22/fallout-from-a-fire-chip-prices-soar/c59d1f0b-493c-4b68-9a37-cf7588ea8641/
Well said!
“They likely don’t have (or have never asked for) the subassembly’s parts lists to examine the secondary risks in the same way that they examined shortages of those “finished” components”
and even if they did, it would probably be at design time, then somewhere down the line some component manufacturer gets gobbled up by another, and pretty soon you are back to the same “single source” problem.
For the AKM fire I posted about above most manufacturers thought they were second- or even third- sourcing subassemblies, but the chips hidden inside were all made by AKM in the same factory.
Try building a successful design that lasts for > 10 years nowadays, it’s a fricking nightmare, with components going end of life, sometimes mere months after you complete the type approval.
It’s probably multiple cases of “We’re using a lot of IP from X smaller company, it would make sense just to buy them” or “That smaller company is making our chip cheaper than we can, it would make sense just to buy them”
Since I built a couple of JIT systems, you generally anticipate as far as your accountants allow you to spend. On widgets I like a weeks buffer, on food staples, maybe a month or so of non spoilables. Shutting down the product line is easier than not feeding people.