If you’re running an army, chances are good that you need a lot of portable power for everything from communications to weapons control systems. When it comes to your generators, every ounce counts. The smaller and lighter you can get them, the better.
Connecticut-based company LiquidPiston is developing a high-powered generator for the US Army that uses the company’s own rotary x-engine — a small, light, and powerful beast that sounds like a dream come true. It can run on gasoline, diesel, natural gas, kerosene, or jet fuel, and is scalable from 1 to 1,000 horsepower (PDF).
Co-founder and CEO Alex Schkolnik describes the design as a combination of the best parts of the Otto and Atkinson cycle engines, the Diesel, and the Wankel rotary while solving the big problems of the latter two. That sounds impressive, but it doesn’t mean much unless you understand how each of these engines work and what their various advantages and disadvantages are. So let’s take a look under the hood, shall we?
Suck, Squeeze, Bang, Blow
For the purposes of this discussion, the Otto cycle, the Atkinson cycle, and the Diesel are all four-stroke engines. This means that for every pulse of power produced, the pistons move four times, the crankshaft rotates twice, and ignition occurs once. These four strokes are called intake, compression, power, and exhaust, or as they’re known colloquially, suck, squeeze, bang, and blow.
Any given piston engine’s efficiency can be explained in terms of the compression ratio of the cylinder. The static compression ratio refers to the difference between the volume in the cylinder when the piston is at the bottom of the stroke — the beginning of compression — versus the volume when the piston is at the top of the stroke, or the end of compression. Calculating the dynamic compression ratio also takes into account the gasses entering and exiting the cylinder. In general, the higher the compression ratio, the better. A high compression ratio makes the most of the fuel in the tank.
The differences in these engines lie in the number and shape of the moving parts, the air and fuel intake schemes, and the ignition of the fuel. As a jumping off point for the purpose of discussing the four strokes in general, let’s look at the typical gasoline-powered internal combustion engine found in many cars, aka the Otto cycle engine.
Otto Cycle
An Otto cycle engine consists of one or more pistons moving within cylinders. The pistons are attached to a crankshaft via connectors that turn the up and down motion of the piston into rotational motion of the crankshaft. This rotational motion is delivered to the gearbox and on to the wheels, moving the car forward or backward.
During the intake stroke, the piston moves downward toward bottom dead center, and the cylinder fills with a fuel and air mixture from a valve at the top of the cylinder. On the compression stroke, the piston moves back up toward top dead center and squeezes the air-fuel mixture, compressing and heating it up. Power is produced when the spark plug sparks, igniting the compressed air-fuel mixture and forcing the piston back downward, which turns the crankshaft a second time. Finally, the piston moves back toward top dead center on the exhaust stroke and pushes the spent air-fuel mixture out through the exhaust port. The speed at which the engine does this is anywhere from 600 to 1,000 revolutions per minute (RPM) at idle to the point where a given consumer gasoline engine redlines — usually somewhere around the 5,500-7,000 RPM mark.
The more pistons an Otto cycle engine has, the smoother it will run. The main advantages of the Otto cycle engine are that it doesn’t burn much oil, it’s fuel efficient, and has fewer harmful emissions than Diesel engines. One of the main downsides is that these engines have a lot of moving parts, and when they fail, they tend to fail spectacularly.
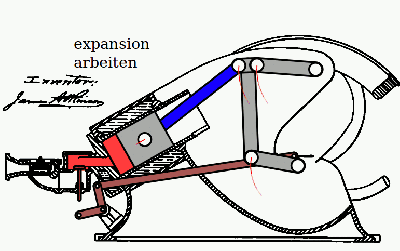
Atkinson Cycle
Atkinson cycle engines have been around since the late 1800s and are commonly found in hybrid cars today. The Atkinson is a four-stroke internal combustion engine much like the Otto cycle, but there’s a big difference: the intake valve stays open during the first part of the compression stroke.
It may sound wasteful, but that air-fuel mixture isn’t just lost through the open intake — it gets pushed into the next piston, preheated and ready to burn. Since variable valve timing wasn’t a thing yet, the original Atkinson cycle engines used a linkage to vary the piston timing.
The expansion ratio of the Atkinson cycle engine is greater than the compression ratio, which means it’s more efficient. It has less power, but when paired with an electric motor, the two complement each other. Other advantages are reduced pumping losses — pumping in air and fuel and pumping out exhaust takes work, and less power is needed to perform these functions.
Diesel
Rudolph Diesel’s engine is also a four-stroke, but it does things a little differently. During the intake stroke, the cylinder only takes in air — no fuel. The compression stroke squeezes the air and heats it up to ~1300 °F. At the beginning of the power stroke, fuel is injected into the cylinder where it ignites instantly amid the hot air, forcing the piston downward. The exhaust stroke is the same — the spent air-fuel mixture is vented out the exhaust valve.
The interesting thing about the Diesel is the lack of spark plugs. They don’t need ’em — compression heats up the air enough that when the fuel is injected, it explodes without needing a spark. Diesels have better fuel economy than Otto cycle engines, but they cost more to buy and maintain than gasoline-engine cars. Diesel fuel is often more expensive, too.
Because they are compression-ignited, Diesel engines have a higher compression ratio (and longer cylinders) than gasoline engines. This produces more torque, which is good for heavy loads, but the cost comes in a slower takeoff speed.
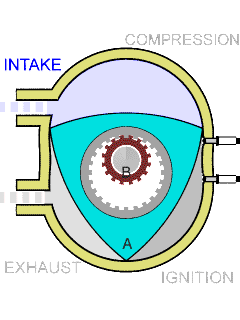
Wankel rotary
Here’s where things get really interesting. Felix Wankel developed his rotary engine in the 1950s based on a dream he had as a teenager. Instead of pistons and cylinders, a Wankel rotary has one big rotor with three sides moving in an oval-shaped housing. The rotor is connected to an eccentric shaft, and the because of its design, the engine converts combustion pressure directly to rotating motion of the eccentric shaft.
The Wankel is a compact engine with fewer moving parts. It utilizes the same four strokes, but only in the thermodynamic sense — the rotor and the eccentric shaft are the only parts that move. The eccentric shaft acts like a crankshaft, delivering power to the drive train.
Wankel engines are smoother-running and can rev higher, but they are designed to burn oil in order to keep the internal seals lubricated. As you might imagine, this means they have terrible emissions.
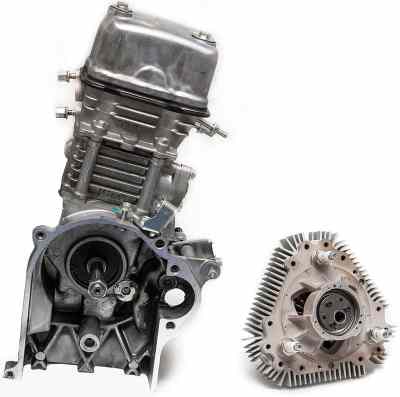
Rotary X: An Inside-Out Wankel
The jaw-dropping thing about the rotary x-engine is the amount of power relative to the size. For example, LiquidPiston demonstrated their engine to the Army by building a Compact Artillery Power System (CAPS) generator to power the digital fire control system on an M777 howitzer.
Today, the system requires a generator that needs a truck to move it around. LiquidPiston built one that weighs 41 pounds (18.6 kg) and is roughly the size of a gaming PC. The Army was so impressed that they awarded LiquidPiston a Small Business Innovation Research contract to further develop the generator for “a range of military use cases”.
If you want to understand how the Rotary X-engine works, take almost everything you know about the Wankel and turn it inside out. The Wankel has a triangular rotor in an oval housing, and the Rotary X has an oval-shaped rotor in a triangular housing. Both engines only have two major moving parts — the rotor and the shaft.
Each of the three housing chambers in the Rotary X is comparable to a piston. The intake and exhaust ports and chambers are built into the rotor itself. For every revolution of the rotor, there are three combustion events. This engine is able to be so small and efficient because LiquidPiston redesigned the thermodynamic cycle to squeeze out more power. The video below explains it quite well.
Will we ever see these engines in consumer cars? Maybe someday, but a lot has to happen before then. More than likely, it would take a major manufacturer to adopt the technology and put it in a car the way Mazda put Wankels in RX-7s and 8s. Even then, it’s not guaranteed to take off, although LiquidPiston says they are suited to be either the primary engine or part of a hybrid system.
LiquidPiston are offering x-mini development kits starting at $30,000, but you have to promise not to reverse-engineer it. However, there’s probably enough information out there to make a 3D printable version, so we’ll be waiting to see what you come up with.
Looks like a slightly modified Wankel engine, complete with all of the problems associated with them (apex seals, poor emissions due to oil/fuel mix required to lubricate engine, etc.). All they did was modify the thing a bit.
Compact? Yes. Revolutionary? Hardly. Efficient? Probably (just like a Wankel). Useful? That remains to be seen.
Also, diesel engines can be EITHER 4-stroke and 2-stroke.
“Looks like a slightly modified Wankel engine”
The biggest difference is the combustion – if you look at the Wankel cycle, the volume’s changing all through the combustion process, whereas since the combustion seal in this engine is a circular end of an oval, the combustion volume stays fixed (isochoric combustion).
If you think about it in terms of a PV diagram, the expanding combustion volume in a Wankel cycle is just a pure loss of work: if you replace the burn with an isochor + expansion to get to the same PV endpoints, you’ve just done more work. And it’s a pretty damn big difference, too: there’s a lot of missing area there.
You’re of course right that it maintains some of the seal issue of a Wankel engine, though (which are literally all of your criticisms) although I kinda think the larger contact seal area might mitigate that.
But there are plenty of applications where power/weight is dominant over practically anything, so I’d easily imagine that they’ll find a use-case (assuming it has a *reasonable* lifetime).
I think I see what you’re getting at. So this engine effectively combines the power density of a Wankel with the PV behavior of an Otto cycle.
I do wonder if placing the “apex” seals into the main body of the engines has some advantages over the rotor such as cooling and perhaps allows for better seal geometry.
*Plus* the overexpansion of the Atkinson cycle. In an Otto cycle, during the power stroke, pressure doesn’t drop all the way to atmospheric since the expansion stroke = compression stroke. Since the combustion obviously boosted the pressure, the power stroke can’t get you all the way back to atmospheric. Hence the reason why the Miller cycle gains you efficiency in a typical ICE.
In this case, if you put the exhaust/intake ports at different locations, the gas can expand into more volume than it was initially filled into.
So you pick up the extra area from the high compression ratio (200:1) and the very low final expansion pressure (~atmospheric). Plus the standard benefit of a Wankel in the sense that the engine’s already rotary motion.
“I do wonder if placing the “apex” seals into the main body of the engines has some advantages over the rotor such as cooling and perhaps allows for better seal geometry.”
That’s what they say in the conference paper. In the paper it says the engine uses 10x less oil than a typical Wankel. Plus efficiency always helps with cooling.
Just realized that in the cycle shown in the video, you can see the asymmetric intake/expansion volumes pretty easily: when intake stops and compression begins, the rotor is at TDC (the oval’s straight up and down) and the chamber’s at like, half its volume, whereas the power stroke/expansion ends when the rotor is basically perpendicular to the chamber that’s firing.
So it’s actually directly analogous to a Miller cycle engine: the intake valve’s left open during the compression stroke so that the expansion ratio’s bigger than the compression ratio.
Also I have *no* idea where I got the 200:1 ratio idea from (which would be insane), it’s obviously more like 10:1 or 20:1 (with a larger expansion ratio).
You all bring up good points, and dig far deeper into the nitty-gritty of how these work for me to keep up. I have a decent understanding of engines, but only as far as being able to wrench on them, not design them.
I guess if I had to sum up why I don’t think this is a good idea, I could do so in one word: Longevity. Specifically, a lack of it. Wankel engines need to be rebuilt fairly often compared to other engine types.
If power/weight is one’s primary concern, a gas turbine is far superior to any internal combustion engine type, and are available in sizes from the small units used in R/C jets all the way up to ones big enough to power a container ship, and every size in between.
It seems to me that every few years someone comes up with some new, revolutionary engine design that will solve all of our woes, and yet never seem to see the light of day. Forgive me if this seems to me to be yet another one of those ideas.
“It seems to me that every few years someone comes up with some new, revolutionary engine design that will solve all of our woes,”
Just to be clear: you’re certainly not going to ever replace typical reciprocating diesel or gasoline engines in a standard ICE car with a new ICE, because the entire supply chain and support industry’s centered around them. Moreover, stuff like power/weight and fuel efficiency just isn’t that huge a deal, because 1) the car’s heavy already and 2) you’ve also got to deal with emissions standards anyway.
So if you’re expecting a new engine to “break through” in that sense, stop. The main place where new engine designs are going to have effects would be in adding new options in the “power/weight”, “size” and “fuel efficiency” space.
The Sarich Orbital engine had sliding seals, between the rotor and the cylinder casing, but it too suffered from lubrication and heating problems.
I wonder if 3D metal printing could resurrect that design and “print in” more oil channels than they could have ever machined in the early days of its development.
I think small RC Aircraft would easily find a use for this. They’re one of those applications where power/weight dominates everything.
correct. and in highly efficient european ultralight designs like https://en.wikipedia.org/wiki/Pelegrin_Tarragon and https://en.wikipedia.org/wiki/Blackshape_Prime this engine would be gold, for two reasons: ability to run on Kerosene/Jet Fuel and less weight for the engins translates directly to more luggage weight.
Didn’t fancy model aircraft use miniature jet engines until electric technology improved?
They never stopped.
Yeah, Wankel engines are pretty common in those situations. These are actually slightly worse in power/weight than typical rotary engines (at least based on their specs) but the fuel consumption’s like 2x better.
This has a combustion every 120 degrees, i.e. 3 combustion cycles per revolution. Assuming similar compression ratios and top speed as a similar sized Wankel engine, this would be capable of about 3 times as much power. That is also going to be useful for running a generator smoothly without a gearbox. If the generator is placed at the intake end, the combustion air could be drawn through it, preheating as it cools the generator.
The biggest advantage I see here is that the heating isn’t concentrated on one side of the engine. The biggest issue with the Wankels is that you can either make it seal well when hot or move when cold. This thing has stationary seals and heating on all three ends so it should be easier to get to seal without just dumping oil at the problem.
Diesel is kind of thick. Could the diesel itself be used to lubricate it without adding smokey oil?
Diesel has some lubrication properties but it is “kind of thick” mostly in the cold and it IS also “smokey oil” when not finely atomized.
Check this out… an engine-generator that moves back and forth like a steam locomotive piston, but internal combustion…. https://www.aquariusengines.com/ Looks promising for standby generators at telecom sites. Nokia is doing trials at 5 locations.
Basically just another reciprocating ICE engine. The vibration level must be ground shaking. An opposed piston engine can at least run balanced.
kind of interesting. That’s a one-stroke engine, effectively. I bet it, and everything near it takes one heck of a beating while it’s running though.
“Also, diesel engines can be EITHER 4-stroke and 2-stroke.”
As can gasoline engines.
As can petrol engines.
First I’ve seen of what I expected to have a ‘liquid’ piston. I can’t see how it’s any different to oil-burning Wankel engines, those presently being phased-out for their grubby emissions. Perhaps someone can fill us in on Rotary X seal lubrication?
It runs 50:1 fuel:oil mixture, so yeah, it burns oil.
Well, for one, the DoD hardly concerns itself with emissions. Mission always comes first, as well it should.
yes and part of that mission always comes first is reliability, the apex seals and surface seals are a big failure point in the traditional Wankel engine, from what i can see nothing in this indicates a fix for those issue, this may have a place in specialty applications like racing. but the added requirements of gasoline with an oil additive would probably make it undesirable for field use, there is a reason diesels are used in most military vehicles
The military might have different cost/benefit equations for equipment than does the civilian world. It might take more maintenance, but they have people that can do this very well. If it’s light, simple, reliable, and has a reasonable MTTR, combined with long operational life, might be good.
Turbojets for cruise missiles have an engine life measured in single/double digit hours. No point in making them out of expensive materials that will last!
BTW, I had a book of NASA/Military patents from the 80’s, and they had developed exotic rubber piston rings and apex seals for engines. I am not making this up. I wonder what ever happened to this.
Rubber piston rings might be great for Stirlings, but I don’t see them being more desirable than low tension Moly faced for automotive gasoline engines.
The secret to these, and Wankels issues is to feed them good old 2 stroke fuel. The Wankels from Mazda were oil-starved, causing most, if not all, of their mechanical issues. Run a RX-7 on 50:1 2-stroke mix and they will run forever.
With modern 2-stroke oils it’s not as bad as it once was. There is 0 smoke, and the emissions are much better than in the past. Certainly good enough for small engine, non-automotive applications. I’d be super excited over a string trimmer (weadeater) with one of these powering it, or a chainsaw, would be sweet on a lawnmower too. I bet they could be produced very inexpensively, also.
Kinda odd but dod small engine generator and compressors were some of the first overhead cam engines, there is some requirements for emissions stamped on them…
So although some people in the military may not care about the emissions, if the contract states it must hit this min…
correction, overhead valve engines. (not the old briggs flat head.)
Everything is a balance. I’m guessing that this engine is worse on HC and CO than a ‘traditional’ piston engine, but better on NOx. It is much much lighter though. I could see a a use case with a plug-in hybrid where the average user sees a net emissions reduction per mile driven due to carrying less weight. This would also mean more range per electric charge.
How about as a range extender, running at an optimum speed on diesel oil? Much cheaper than a full EV.
I like, and have concocted in my kitchen, Ethyl-Ester Bio-Diesel. 100% renewable, and hopefully won’t put you in a cancer ward, like that other ‘bio’ stuff might. Engines that run on it, simply never wear out!
I doubt your concotion combusts differently enough to not create cancer causing micro particles.
So the big difference is that instead of having the oil be added to the fuel to try and lubricate the apex seals on the rotor that is spinning thousands of times a minutes they can actually seal the apex seals directly because they aren’t in the rotor but in the housing. To my understanding this means that from an emissions standpoint they are comparable to a common otto cycle engine. Don’t forget that all engines also have seals just that they are called piston rings in any that have pistons instead of apex seals but the functions are the same. In some ways the seals in the rotary x engine are even easier to lubricate because they are completely stationary unlike a piston that is oscillating, again at thousands of times a minute.
This still seems to have the problem that the Wankel does regarding apex seals. While the seals are now in the housing rather than the rotor, which arguably could make servicing easier, there’s still the problem of oil intermingling with the combustion. That may be fine for stand-alone generators or military applications that avoid emissions laws but it will run into the same issues the Wankel has regarding automotive applications.
Anyone else notice the weird capital p that looks like someone stretched a lowercase p to make it taller in the graphic that says “3. Power” ? No? Just me? Ok, I’ll see myself out…
You’re right! That p is an imposter!
It has a dent in the top between the loop and the left side: p
and isn’t flat across the top like this: P
wow…
I doubt we will see any all-new engines I developed for passenger cars. Which is probably why this is aimed at the military.
“I doubt we will see any all-new engines I developed for passenger cars.”
Please tell us more about the new engines you’ve developed!
(I suspect that was a typo, if so, insert smiley here)
Yes, phone typo.
I do work in engine development, but nothing even slightly exotic.
Maybe not cars, but if you are a country-dweller like me you really, really want a weadeater with this engine on it. These engines would be ideal for kinds of tools. Chainsaws, mowers, tillers, augers, you name it. The first to manufacture a string trimmer with this engine and a competitive price will take over the market.
LiquidPiston has a page with technical papers which is likely to be of interest to some of you:
https://www.liquidpiston.com/technical-papers
I’m sure there will be plenty of skeptics in the comments, and I’m one of them – I’m not convinced that this engine will be viable for general use, since they company noticeably silent on *some* drawbacks of rotary engines that I’d expect them to tout if they were resolved (emissions, durability, fuel efficiency, mandatory oil consumption) but writing this off as “just a tweaked wankel” is really selling it short.
If this thing works with any sort of reliability, it’ll be miles ahead of anything else where power-to-weight ratio is critical, like the drone and generator applications they’re pitching it toward. Including the classic wankel.
Drones especially, not to mention maybe the military will get their robomule back.
“Robo M.U.L.E., catch the Wumpus!”
B^)
The papers actually do address all of the topics you mention: 10x lower oil consumption than a typical Wankel, and the current brake thermal efficiency (effectively fuel efficiency) of ~33% or so. They haven’t done long-term durability testing (… obviously) but as they point out one of the advantages of a Wankel type engine is that they fail “soft” – the seals wear and the engine gradually loses power output, as opposed to, uh, more “rapid unscheduled disassembly” failures.
The cool thing in a military application is that the small size/weight for a given horsepower means if the installation can be simplified they can swap engines in the field and send those to be rebuilt back home for repairs.
Get the cost down and you can just throw the old one away. We destroy 6 to 7 figure bomb guidance systems daily, of you only have to swap your engine block 2-3 times per vehicle lifespan this would be absolutely viable.
It’s technically different because of the constant volume combustion stage, which would theoretically give you a considerably more complete burn. I imagine the animation just doesn’t do it like the Wakel animation, but at 1:20 it appears the combustion begins before the apex…
Anyways, everything in the military leaks and spews when it’s in good condition. They’re not concerned about burning a little oil for the payoff of a lighter load.
The good ol’ “if it’s not leaking oil, it’s out of oil”
No it isn’t.
I don’t like articles that start by bashing existing technology. And this one does just that!
It’s a very poor sales pitch.
Anyone wants some insects? :-p
I’m not sure I’d call it bashing. The problems with existing technologies are well known. It’s more of a summary of known issues than a bash-fest, IMHO.
Interesting… though appearing not to be super high efficiency, i.e. not far above high efficiency versions of gas and diesel engines. The thing missing in the size comparisons though is the size of the geartrain, there’s not a lot that we will want to turn at 14,000 RPM. Most common uses will see it need a 4:1 reduction before you can “swap it in”, though a complete designed from scratch gear reduction unit would be smaller than the maybe 10:1 then 4:1 separate gear reduction units, but I think it would be an easier sell, if offered with a 4:1 reduction so total redesign wasn’t necessary for initial adoption.
No indication there of throttle responsiveness for vehicle applications, which might all be series hybrid so not matter, or indeed how much efficiency curve varies with speed and throttle. If for instance it was 30% efficient from 1000 rpm climbing to 45% peak at 14,000, that would be huge, since low speed operation below torque peak of conventional motors is like 10% efficient, and we spend a ridiculous amount of time not driving the motor anywhere near peak efficiency (Basically you have to be going about 50mph up a 20% grade, without using an overdrive gear, droning along at around 3000RPM, a grade? that doesn’t get me MPG you say, but it got you potential energy! I can’t be bothered arguing this by the way, odds are you don’t know enough about it.)
I’m gonna have to dig back in some old Popular Mechanics issues, I believe I saw something rather similar. IIRC the issue back then was how to manufacture it, the curves they wanted to use in that version were not possible with conventional machining methods at the time.
Anyway, I look forward to seeing these turn up in used snowmobiles or something, to get grubby mitts on one to play with.
14,000 RPM?
Electrical generator/alternator?
Rotor for a Mars helicopter? (Not being snarky, that’s what you’d need)
Speed of sound on Mars is actually lower than near earth’s surface, so you wouldn’t even be able to spin a large rotor as fast as an earth helicopter.
This belongs on a weadeater! and a backpack blower, chainsaw, lawn mower, etc…
“Anyway, I look forward to seeing these turn up in used snowmobiles or something, to get grubby mitts on one to play with.”
Anyway, I look forward to seeing these turn up on AliExpress for ~$50.
FTFY
B^)
EXACTLY! Should be super cheap to make these, and you know they will.
“Interesting… though appearing not to be super high efficiency, i.e. not far above high efficiency versions of gas and diesel engines.”
Uh… why don’t you think that’s true? The isochoric burn + overexpansion are both obviously going to result in higher efficiency.
The paper on the overall cycle (google HEHC engine, it’s the researchgate link) shows the overall efficiency improvement, which is pretty big from a theoretical point. Which isn’t surprising, given the 200:1 compression ratio and expansion back to atmospheric. That’s a ton of extra area.
In theory the burn characteristics of hydrogen mean engines over 60% efficiency… have we got any? Nope because it’s hard to make the mechanics actually do it (piston slowing when it should be accelerating etc). That seems to be what we have here, because on their info sheet, the speculated fuel consumption of their fully developed diesel is given as 185g/kWh, whereas the current best in diesel engines is 169g/kWh. So there seems to be a disconnect between the theory and their current embodiment of it.
Most of any engine’s losses are through cooling and not burn efficiency. And as long as you have cooling pulling away as much as 70% of the BTU’s being burned you aren’t going to have huge gains burning any fuel, even hydrogen fuel.
Keep the heat in it then, like Smokey Robinson’s adiabatic engine… (Apparently that made bad NOx though)
Dammit, Smokey Yunick, got a neuron crossed up for a moment there.
I wonder if Smokey Yunick’s engine and the “dry steam” engine used in the VW XL-1 are operating on the same principle.
https://www.hotrod.com/articles/hrdp-1009-what-ever-happened-to-smokeys-hot-vapor-engine/
https://en.wikipedia.org/wiki/Volkswagen_1-litre_car
I don’t know, but VWs performance doesn’t seem that far off R Q Riley’s XR-3 design… https://rqriley.com/product/xr3-hybrid-plans/
“So there seems to be a disconnect between the theory and their current embodiment of it.”
Yes, which is directly mentioned in most of the papers – the brake thermal efficiency’s only around like, 40-45% at this point, with most of the losses coming from the seals underperforming, whereas full simulations show BTEs nearer to 58%, which is totally out of reach for a diesel. You’re literally comparing a first-generation engine design with engines that have practically had over 100 years of design improvements. “Typical” BSFC for a diesel engine is usually listed as ~200 g/kWh.
So you might say “big deal, if they can’t get it now, why are they claiming this is such a big deal?” It’s because the fuel efficiency’s only *one part* of the advantage.
Assume the spec sheet they put out for the “mature design” is what they actually reach. That means they’ve hit or passed the efficiency of a typical modern diesel engine with probably 1/3 the weight and direct rotary output.
No surprise that the first two markets are generators and UAVs.
I know that current diesel has many more years of development, but it’s still not better until it’s better.
UAVs are gonna need a reduction gear I think, depending on the size of the prop, I think it’s gonna be supersonic at 14,000 RPM for anything with more than about a foot or 30cm of blade. (Get away with it maybe on small motors/drones, but the 40 horse on something the size of an ultralight is gonna need the same size prop as one.) Then they’re not competing on power to weight with 4 strokes, they’re competing on weight with 2 strokes. Also relatively exotic fuels are in play in that market, hydrazine etc.
Use a lightweight permanent magnet alternator and do the power conditioning electronically (inverter generator).
Back in the 60’s the German manufacturer NSU fitted their cars with Wankel engines. They had a very distinct sound but i don’t remember the smell.
>Diesel fuel is often more expensive, too.
Except in the EU where most governments raised the tax on road fuels to collect a ton of money (€440 billion last year), but couldn’t do so for diesel because all the commercial and public mass transportation used diesel and would have required massive subsidies to keep running, so diesel got taxed more lightly.
In the beginning, people started modifying their cars to run on kerosene, lamp oil, and even turpentine to dodge the taxes. Some car companies (Saab, Talbot) made cars with dual fuel systems. Kerosene is lighter than diesel, so it burns in an otto engine once you get it warmed up. People with diesel cars started using heating oil, since kerosene kills the high pressure injection pumps over time.
The governments responded by adding dyes to heating oil and the rest, and outlawing their use in cars. They couldn’t jack up the tax on diesel though, so diesel cars got really popular, so they fixed that by adding ownership fees on diesel engines to stop everyone from switching over. Still, if you drive more than the average person, a diesel car is more economical to own, and about half the people are driving diesel.
To put that in contrast, the US state and federal fuel taxes generate about $40 billion, give or take. This is the reason why in the EU the cost of driving has nothing to do with the price of oil. If the oil prices go up, fuel prices go up, and if the oil price go down, the taxes ratchet up to meet the difference.
The federal and state fuel excise taxes don’t ratchet up or down to compensate for fuel prices. They are a constant that adjust up over time.
Also, these taxes are the most fair way to pay for interstate highway upkeep, at least until electric trucks start appearing in mass. Diesel has the highest excise tax because diesel trucks cause the most wear and tear to the interstate system.
Not automatically, no, and I wasn’t talking about the US but the EU where increasing fuel taxes in times of fuel price slumps is a common practice.
Maybe he thought E.U. meant Estados Unidos!
B^)
>these taxes are the most fair way to pay for interstate highway upkeep
And for that, the fuel taxes should be slightly higher to actually pay a significant part of it, but that’s besides the point. In the EU the governments collect 10x the taxes from fuels which would pay the entire US federal AND the state roads and highway budgets about 2-3x over.
Most of that money is collected for entirely other purposes; it’s mainly wealth redistribution from the working class to the idle classes.
Alas, the upkeep is the one thing the taxes seldom are used for, at least up here in the far north. They get used for just about anything else than something that would benefit the tax payers.
Here in the U.S. diesel fuel used for agricultural purposes has a lower tax rate (tax exempt?) and is dyed green. It’s been said that if a Highway Patrol[person] dips a rag into your highway vehicle and it comes out green tinted, you’ve just lost $10,000.
Correct on both points – off-highway fuel is not taxed as a motor vehicle fuel, and I don’t know about the $10K but it’s definitely high enough to wipe out all your savings, ever. A problem in my area is that at least some off-highway diesel is not ultra-low-sulfur and will, I’m told, wreck a modern injection pump. I don’t want to find out, and the tractor doesn’t use *that* much fuel, so…
Although $10k is a lot of money, that sum hopefully will not “wipe out all your savings, ever” (forever?). AFAIK the sulfur is a problem as it generates acid when it burns. Engine oil contains some alkali to neutralize some acid, but if this is used up the acid leads to corrosion.Therefore, you should change the oil more often, if you run e.g. a generator on heating oil.
I’d assume “wipe out all your savings” means it’ll outweigh any cost savings you got from using farm fuel in your car.
In the UK it’s dyed pink, but more colloquially known as “red diesel”.
You are forgetting to mention that the postwar petrol supply in Europe up until the 70s in some parts, was the relatively low octane pool petrol, or two star as some in UK might remember it. Therefore engines were not made to be very high compression 7:1 or 8:1 might have been typical, in order that they would run on this without pinking or detonating. Therefore preheated kerosene, paraffin or TVO could run in them quite well. However, with the wider availability of higher octane gas, newer models got higher compression engines, which were of course higher efficiency because of this, leading to need for the better “4 star” petrol and loss of realistic ability to run on heated kerosene.
Except on the point of Saabs, which were always relatively high compression, high-end engines, because they were made in Sweden which came out of the war more or less unaffected – having traded successfully with Germany while pretending to be neutral. They had proper gasoline all along and could afford to import it.
The Saab 99 Petro was available until 1984 in places before it was finally made illegal – so the dual-fuel engines were converted back – but you’re right, they did have to use the pistons from the turbo version in a naturally aspirated engine to lower the compression ratio somewhat. When the owners converted back to gasoline, they simply swapped in the pistons from the regular 99 engine and got about 30 HP boost from it.
And also, it wasn’t until the 70’s that the tax racket started, right at the point when you started getting better fuels and better engines with lower fuel consumption and more power. That’s when they yanked up the taxes, and that’s when the companies started selling kerosene cars for people wanting to dodge them.
1.) it does not sound strange
2.) they have a p-V-Diagram explaining the cycle
3.) But Efficient! More Efficient! Very high efficient! Just efficient.
But to what percentage?
1.5L / 3 Zylinder / D-DI / Honda / 50 – 70 kW
And IN BEST POINT 39%.
4.) We could reverse engineer the shown p-V-Diagram and lay a normal cycle over it ..
Hackaday,
The video link (for the Rotary-X) in the article, is just a blank white screen on my browser (M$ Edge).
But it just might be a result of our goofy Internet gateway.
Goofy. I’m using the same browser and it’s coming through. Although I’ve known of this engine for some time.
It’s your gateway.
Hot damn, I want one of these in a dirt bike
Can it run on H₂?
I have been interested in the potential of the Wankel engine as a “stratified charge”, turbocharged engine for 30+ years. This engine might have a similar potential. The primary problem with a Wankel engine is its combustion chamber shape with a very high surface to volume ratio. This causes excessive heat loss and fuel loss. This leads to very low fuel efficiency. In a stratified engine, fuel is directly injected into the combustion chamber at the flame front as it burns. This allows very high compression ratios as there is no “end gas” to pre-ignite and cause knock. In a piston engine this requires the air in the combustion cylinder to be swirled past the ignition source. This is hard to do with precision. In a Wankel engine, the air in the cylinder is naturally moved past the ignition point by the rotary action. Turbocharging would be required to achieve a suitably high compression as well as high pressure direct injctors. The primary issue used to be controlling the rate of fuel injection but modern electronics can easily address that. The remaining issue is the cost of a high pressure fuel injection system. The large area of the combustion chamber could probably be addressed with ceramic coating. Such an engine would be small, light and very efficient, perfect for use as a hybrid generator engine. I have been waiting a long time for this to happen!
Well if you “Muntz” a turbocharged Wankel until you’ve deleted all the troublesome and unnecessary parts, you’ll find you’ve re-invented the turbojet.
But a turbine is not well suited to drive a car. So you could only build an APU like generator as a range extender for an electric/hybrid car.
A turbojet would be great for when I have tailgaters.
You’d want afterburners for that… I think that would drive the tailgaters away rather well.
No reason why you can’t drive a car with a turbine, lots of vehicles in the past have used a turbine as the power source, often it is as a generator of electricity to then run the drive train off an electric motor, but there have been direct drive turbine systems before.
As for suited to a car, well that’s all down to what use you put your car to and how you want your car to perform – in a similar fashion to choosing diesel over petrol, which creates differing engineering challenges and optimal performance windows. But you can make a perfectly useable turbine car, and it will sometimes be the ‘best’ choice of power unit. Though nobody is likely to use it even then – as best on paper, vs dumping a commodity petrol engine in with a few customisations to make it closer to your needs… the cost and development speed of that second option makes it the almost certain winner, almost no matter how inferior it would prove for the job..
Turbine engines have horrible efficiency at less than peak power. OTOH they consume 70% of the fuel at idle while providing zero power.
Also, their peak efficiency is almost the same as for reciprocating engines, their advantage is mostly in weight-to-power ratio.
Atkinson Cycle
I’m not sure the description of Atkinson cycle is correct. I thought it was the shorter compress stroke (i.e. less work spent compressing air) that provided the efficiency improvement over the Otto cycle. This is reflected in the animated diagram shown in the article (the intake valve does not appear to be kept open during compression).
The reference to leaving the intake valve open is an implementation of detail of how Atkinson is implemented on modern cars. Instead of reducing the intake/compression stroke, they achieve the same effect by not closing the intake valve at the bottom, and waiting until piston has moved to the desired position and then closing the intake valve, so actually compression is only happening for part of the stroke (rather than the full stroke like Otto cycle engines).
The trade off is more efficiency, but less power (for the same displacement compared to Otto cycle engines).
Oh yes, the company that’s been touting a “new engine” for a decade, and has recently resorted to asking for investors on instagram.
It sounds exciting, and they sure do sell it well, but let’s wait until the tech can speak for itself.
Seal issue solved?
Because of the orientation of the apex seals, it could be possible for them to be longer than necessary, penetrating out both ends of the engine. This way, if they were clamped in place during normal engine operation, and the seal material stored in a reel, all one would need in order to replace seals is to unclamp them, rotate the reels to push through fresh sealant material, and re-clamp. As far as seals go, the material can be a cheap consumable, and one could literally have hundreds of seal replacements on a single reel, as the length of the strip inside the engine isn’t very long. It could even be computerized and automated, so that the engine replaces it’s own seals after n engine hours.
Someone’s going to patent this. Enjoy.
So seal issues: apex seals should work very well in this design. You can oil them directly in the block, and meter that very precisely to minimize the emissions impact. Problem is the side seals that have to either be in the block and sliding past the ports on the rotor, or in the rotor sliding past the ports in the block. I suspect that is why they say “fail soft”. If the side seals fail it will probably still run if spun fast enough.
I’m surprised they aren’t super big on using magnesium-air cartridges instead of generators.
Spent magnesium will eventually absorb Co2 from the air, become soluble, and probably runoff back to the ocean someday, where someone else can fish it back up again using cheap wine power, so it would seem that people will never run out. It’s also nontoxic so heaping it up in a pile and moving on won’t hurt people.
No generator noise, no smoke, I would imagine less thermal signature, no Co2 emission to maybe detect with a drone somehow.
Disposable magnesium fuel seems to be a very easy way to solve the energy storage problem.
Then people could finally enjoy throwing car batteries into the ocean for real!!!!
I would prefer to recharge them against running my car on primary cells which have to be swapped.
Aren’t kerosene and jet fuel basically the same thing?
A spec sheet for an engine that doesn’t exist?
Can someone direct me to the “revolution in thermodynamics”?
It may be limited to a it revolving and something thermal going on.
It’ll end up on The Museum of Retro Technology at some point:
http://www.douglas-self.com/MUSEUM/museum.htm
Interesting web site. Click the home button and you reach a list of analog audio electronics books that Mr. Self has published.
And even with modern digital electronics, we can never get completely away from analog. You often need a audio signal conditioned on the front end or amplified / split on the back end of any digital processor.
Here’s a link to that page.
http://www.douglas-self.com/ampins/ampins.htm
not far from the quasiturbine I think …
https://en.wikipedia.org/wiki/Quasiturbine
I think material science has progressed quite a bit since the time the Wankel was engineered and the military certainly has access to some exotic materials so it might be possible to improve that seal issue. Also, the military tends to do a lot of maintenance on their equipment so as long as seal replacement is a unit level maintenance task, no problem there.
I think it’s an easier engineering task on this than the Wankel seals. Look at all the forces on those, pushed one way, then the other, seems they might have centrifugal pressure at some points, then they’re coupled to the rotor which has no way to sink heat, so it’s just getting hotter and hotter. It looks like the X engine has less inconsistent lateral forces on the seals and the block is sinking heat away from them.
The Business Wire article says their 2kw generator weighs 41 pounds and is 1.5 cubic feet. Is that not about the same as a gasoline powered inverter generator that you get at Costco?
The biggest problem for the Wankel was the torque specs, which were/are abysmal. It could get all the hp in the world but it had no torque. Does this design fix that? That’s my question?
If you have the power you can get the torque you need by gearing.
High reduction gear ratios make fragile gears. When the wheels try to back-drive the engine, there’s huge forces at the gear faces and shafts because the friction and inertia of the engine is multiplied by the gear train.
This is why Tesla couldn’t make the two-speed gearbox last. The motor was designed to spin at 13,000 RPM so it needed a tall reduction gear, which then broke when you tried to apply regenerative brakes.
The forces in regenerative braking are only higher if the regen braking applies more motor torque than the drive torque.
With a combustion engine the reverse torque can _never_ be higher than the driving torque, because that implies that engine friction is higher than full power torque. So that means that the engine would never be able to turn itself.
You need to engineer the gear train. My bike engine runs at 14,000 rpm and the gearbox is still perfectly fine after 120,000 miles.
The Wankle engine more than made up for torque with RPMs and that engine was as happy at 13,000 RPMs as it was at 4,000 RPMs. The only torque issue Mazda has was Americans who were unwilling to push the engine to where it made real power.