Thus far, the majority of electric cars on sale have been aimed at commuters, fitting into the sedan and SUV segments of the marketplace. Going forward, there’s a very real need for electrification to touch the whole spectrum of automobiles, and that includes work vehicles like pickup trucks. A company called Magna have recently thrown their hat into the ring in just this space, developing a simple drivetrain that can be readily installed in pickup trucks without major modifications.
It’s All About The Form Factor
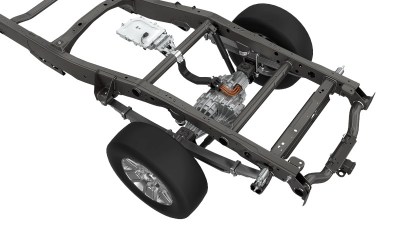
The aim of Magna’s eBeam technology is to make it easier to build electric pickup trucks and other related work vehicles. The basic concept is one of an electric motor drive unit built into a form factor that mimicks that of traditional beam axles, commonly used with leaf spring suspension designs in most pickups. This has the possibility of being a drop-in motor solution for a wide variety of trucks, the vast majority of which use broadly similar rear suspension setups. By simply changing the axle shafts and spring mounts to suit, Magna’s eBeam motor can be fitted to virtually any pickup. The eBeam setup is designed to work with OEM braking and suspension systems, though regenerative brake assist is likely a possibility as well.

The eBeam is a rear-drive solution only, of course, though it need not be limited to only two wheel drive trucks. Magna have already developed a series of electric drive solutions that can be used up front in order to handle four wheel drive, something often considered a must in the truck market. This obviously necessitates a second motor and associated control hardware, but avoids the hassle of differentials, transfer cases and driveshafts typical of traditional four-wheel drive systems.
The line of eBeam motor drives is slated to come in three different combinations. A single-motor drive, a single-motor drive with two-speed gearing, and a twin-motor drive with torque vectoring. Power ranges are slated to be from 120 kW (160 hp) up to 250 kW (335 hp). This is roughly on par with existing engine choices in most low-to-mid market pickups, though falls short somewhat compared to the most powerful truck engines currently on the market which are pushing in excess of 400 hp (~300 kW). Against this, electric motors have the benefit of delivering maximum torque right from zero RPM – a major benefit when it comes to pulling heavy loads. It’s likely that for many jobs, an electric powertrain of slightly lesser peak power would nonetheless fare well against a petrol or diesel competitor.
Currently, Magna are marketing the eBeam axles towards automakers, hoping to secure a slice of the not-yet-mainstream electric pickup market. Nevertheless, the homebrew conversion scene is a lively one, with enthusiasts taking whatever parts are available to create their own electric rides. It’s easy to imagine there’d be a healthy market in selling such conversion parts for popular older trucks, such as Ford’s F-series and older Rams and Silverados.
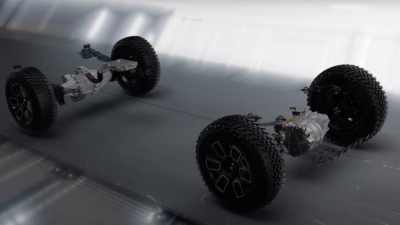
Regardless of the target vehicle, however, the Magna eBeam is not an all-in-one solution. Although it solves the problem of how to drive the rear wheels with an electric motor, that’s all it does. Figuring out a battery solution, charging, and other such concerns are left as an exercise for the buyer.
For the dedicated gearhead, hacking in some salvaged parts from crashed EVs would likely get one most of the way there. For automakers, however, significant design effort is still required to take platforms originally designed for fuel tanks and big combustion engines, and shake everything around until it fits.
More likely, we’ll see electric pickups designed around battery packs from the ground up, for safety, packaging and performance concerns. The market has a heavy focus on the range of electric vehicles, and this is dependent on battery size and performance. While the eBeam design makes for a drop-in rear drive solution, vehicles hoping to compete in the marketplace will still need well integrated battery solutions if they’re going to convince buyers to adopt.
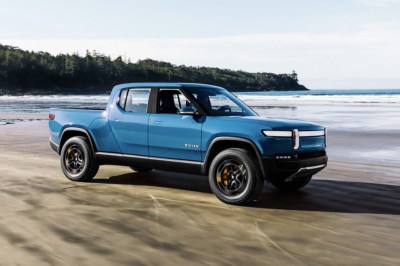
Overall, the eBeam is an interesting product, though one that seems better suited to a thirsty conversion market rather than established automakers. While one can appreciate an integrated rear drive motor solution, it’s something that’s well within the design abilities of just about any top-20 automaker, so we don’t know why they buy it externally. The real challenge lies in the integration of electric drive systems with the rest of the vehicle, and that’s something that a beam-axle motor can’t solve.
Whether Magna’s hardware takes off in the industry depends on what automakers themselves have been developing behind closed doors, and one would imagine they’d started with the motors a long time ago. As always, time will tell.
Many years ago I bought a book on creating your own electric vehicle. It’s recommendation was to convert a pickup truck.
Not surprisingly. At least in Europe, I think pickup trucks are more or less the only cars on the market with a body-on-frame construction – i can only imagine a frame makes it easier to do larger body modifications to a car without changing the structural integrity significantly.
In Europe I guess you can’t do any modifications anyway without going through a regulation bureaucracy and financial nightmare of starting your own car company to be able to do that :'(.
Not always, I mean you can buy a Caterham kit here and build it yourself. Key is to have a donor vehicle that’s certified.
Some EU countries don’t allow any modifications until a vehicle is at least 25 years old.
Varies by country – in the UK we can modify &/or build from a kit / used parts, in Germany they think you’re a dangerous lunatic if you fit a different alloy wheel than it left the factory with.
We have SVA (Single Vehicle Approval) or IVA checks / tests for kit-builds / heavily modified / rebuilt vehicles these days, it used to be quite wild-west.
And in Sweden u can build a car by yourself. Easiest way is to use a certified engine from another car in your build, costs about 600€ in total to register it. But u can even build your own engine and pay a environmental tax for that.
If u want to modifie your car u can also do that by a registration called modified vehicle costs also 600E
But if you want to change the engine, you also need to change the gearbox and the brakesystem. You always need to change three things to be allowed to register a modefied vehicle.
If you replace the engine but leave the majority of the running gear (brakes, suspension etc.) stock you can get away with just re-registering the vehicle as a different fuel type. If you’re doing serious custom work then you need a Single Vehicle Authorisation which is an absolute nightmare, but “pull engine and install motor and batteries” is doable without being buried alive under red tape
once you delete the exhaust lines and fuel tank, there’s a surprising amount of usable space under the bed of a BOF (body on frame) vehicle (truck, van), and even more in the engine bay if you remove the engine entirely (as opposed to replacing with a smaller hybrid-generator unit )
That’s largely because many years ago the only economically viable battery options was lead-acid or NiMH, both of which weighed tons for any useful range.
There was three ways to go around it: make it small, make it slow, or make it big. When the first proper lithium batteries hit the market and they installed them in a regular Nissan sedan around ’96, the energy density was just high enough that they could seat four passengers without exceeding the weight limitations of the chassis. The EV1 was only a two-seater. When Tesla Model S came to market, the energy density of lithium battery packs had effectively doubled, thanks to their development in mobile devices, so you could have passengers AND luggage at the same time in a regular sized car.
Great product for converting a fuel-thirsty full sized Ram van, normally a front-wheel-driver, to a miserly hybrid!
Makes me wonder if a similar idea solution might be possible for camping trailers. Most small SUV/crossovers really can’t pull one, but you could, in theory, have a solution like this, where it would regenerate on flat ground (adding a tiny bit more drag), but on slopes it could assist thus allowing more efficient smaller cars to pull them. Would also want electric breaking which could also be regenerative.
How do you vector that assist though? if it pushes too much you run into the potential to lose control and introduce heavy sway or worse. Now doing something like this to a Class C smaller size RV….that I can see.
Stress sensors on the towing linkage can measure the towing force then regulate the amount of boost to keep the towing force within a target range. There are electric trailer brakes that, when activated by the brake light circuit, work this way. To accommodate driving in reverse, also monitor the reverse light circuit. (Of course, it would be better to have proper control signals fro the towing vehicle.)
Looks like it’s going to add some weight to the suspension.
Unsprung weight is also a concern for wheel motors. The other concern that is also in both applications is how robust they need to be. So I wouldn’t be surprised if that limits this use. I could maybe see this being used in commercial applications, but light truck market will most likely have more “integrated” solutions.
It could actually be lighter. Believe me working on 1 ton axles is fun – I have two foot long snap ring pliers for the hub retaining ring on my custom Dana 60 frontend in my Jeep TJ. That whole axle probably weights 700 lbs., but is beyond bullet proof. These look like they could be great Dana and 14 bolt axle swaps in the future, while still retaining all the aspects rock crawlers and HD trucks love about beam or solid axles as we call em here in the SW USA where nearly everyone has a 4×4.
If you don’t mind, can you share the make / part number for those pliers?
I have a tab-less C-type retaining ring in a superior gearbox that is being a huge pain to remove.
I think I bought them online from Matco. Not cheap, but once you use good ones, it is worth it. A web search (Bing for me) on this “Snap Ring Pliers J-45126” gets me there. That seems to be a valid part. no. Not cheap, but if you do tons of this work it is well worth it. The ratcheting action makes it so you can go a little bit at a time and not get exhausted.
Thanks, those are very similar to some of the Knipex ones I found, but longer overall.
I managed to successfully improvise with the 8-inch ones I had, 3-flathead screwdrivers, 2 u-nuts. But will definitely invest in those to make life much easier next time around. I don’t mind spending on useful / durable tools.
“A company called Magna” : Magna is an established contract-manufacturer of vehicles that are sold under brand names such as “BMW” or “Mercedes” ;-) Quite a player in the market since many years.
https://www.magna.com/innovation/driven-people-driving-change/article/building-a-unique-reputation
Magna also has been building the Ford truck frames for years, they share this with Dana on the F150. They also make the frame for GM trucks and frame on GM SUV’s. They also made frames for the Dakota and Durango too.
Seems like a market move when you had those contracts and now have a bolt in ready option.
Also they were about to buy Chrysler in 2007
In 2010, Magna made a bid to buy GM’s Saturn division. GM rejected that bid. Penskie tried to buy Saturn, but GM rejected all of Penskie’s proposed manufacturing partners, including Magna, resulting in the deal failing.
Magna’s Powertrain division also made “smart” transfer cases and “smart” differentials for several OEMs
Current pickup design is built around having a big engine up front. Drivetrains like this make me think about a pickup that looks more like the old VW T1 pickups or Corvair Corvans, with a forward-control cab and a huge bed that has all the batteries under it. You get way more cargo space for the same wheelbase, and both the battery weight and the cargo weight are over the driven wheels so it has better traction than a conventional rwd pickup.
Well looks like we are the outsiders now as you can see from the comments and engagement above. Looks like people like talking about all kinds of stuff. And there are folks who like correcting the mistakes of others or show their technical depth. So let’s just embrace the fact that being featured here now has a different meaning.
Still rocking my 1996 Solectria E-10 (converted all electric chevy S-10 pick-up truck).
http://www.wolftronix.com/E10/index.html
Thanks for the link. That’ll be a good read. Nice work!
A lot of people think that a hybrid vehicle would be pointless or not as efficient. One overlooked application that would be perfectly suitable would be that of a rural postal delivery worker. You accelerate to the next mailbox and then put on the brakes. A normally fuel efficient vehicle is often reduced to single-digit fuel efficiencies where you accelerate and then dump all the energy into your brakes. I’ve thought for years this would be the perfect use for a hybrid set-up. Imagine having a diesel engine running at constant rpm keeping the battery pack charged up and then you simply use the electric motor to accelerate to your next mailbox. To brake, you regen what you just spent back into your battery and the diesel engine makes up the difference. Long term high-speed runs are seldom utilized unless getting to and from the route. If I had the capability to design this I would, but I don’t. This electric motor solution appears to be a step in the right direction for my idea of the ultimate rural route postal vehicle and delivery vehicles in general.
Garbage trucks and busses share the same go-stop-go-stop-travel too. Little less with busses, but still.
Yes absolutely! I think that is where hybrid technology can excel! So much fuel is wasted with delivery vehicles and they would benefit the most from hybrid technology. I think the big hold up is the cost of a battery because if the cost of replacement exceeds what you saved on fuel, then what did you gain? You just as well burn off the fuel inefficiently because you don’t have to waste time replacing a battery. I’ve even thought of modifying an existing vehicle with an electric motor and belt that could spin the driveshaft. Let the battery bank do the stop and go and once your voltage drops, disengage the belt and shut off the electric motor, start the engine and just drive on that while your battery bank charges up. Once charged, shut off the engine, engage the belt, put the transmission in neutral, and let the motor pull you along. There has to be some savings in there somewhere. Using lead acid batteries wouldn’t give you range, but it would give you cheap replacement cost.
One thing that works great for stop-and-go is a big air compression tanks driven by an hydraulic pump on the driveshaft. It’s effectively a wind-up spring with very little losses especially compared to electric regenerative braking. The downside is the minimum size requirement for the two tanks (air-oil pressure and no-pressure oil-dumping tank) and added maintenance costs.
Cars aren’t big enough, big rigs with loaded trailer(s) are too heavy the trailers would have to have the drive pump and tanks mechanism (very costly, and logistically dangerous: trailer maintenance is often beyond abysmal), city-delivery vans are just right for this.
Lead-acid batteries don’t charge fast enough for regenerative braking to work / be worth it. They are great at being cheap while also being capable of burst-dumping enough amps to power the 1HP electric starter but that’s about it.
Bonus of being terrible at charging is they can handle being constantly charged without a smart charge controller, just push 14V at them constantly they’re fine with it.
Lithium batteries can recuperate braking energy a bit better but dumping that much energy into them requires complex temperature sensing and electronics to make sure they don’t literally explode.
It only works to a certain degree (pun fully intended).
For an electrical solution as effective as the air-oil tanks we’d need affordable super-capacitors to act as a buffer between the motor-generator and the batteries.
Funny thing is diesel-steam hybrids are potentially more energy efficient (can turn a 45%-thermal-efficiency diesel to over 90% efficiency) than purely electric cars when you account for the power losses involved from the power plant to the batteries and back to the motors but the maintenance and refilling your car with water every half hour would suck. And just imagine the humidity in traffic.
That said long-distance big rig truck and locomotives are a potential application if/when the fuel savings will offset maintenance costs. Choo choo m…
If I recall rightly, they did a trial of compressed air braking regen for garbage trucks in Australia a decade or two ago. I think the dealbreaker was noise, otherwise it sounds like it worked great.
This wouldn’t be useful for anything but consumer grade “trucks” (light trucks) and SUVs, and not all of those.
That’s because the power and durability required of medium or higher duty trucks can’t yet be satisfied by motor modules like this one. Those sorts of electric trucks will probably have to be purpose built. There’s a world of difference between something like a package delivery truck and a garbage truck, and an even bigger difference between a consumer SUV and a tractor trailer combination or a tow truck.
I’ll bet big money on it’ll only be a success if you slap a diesel engine on the front wheels.
Pickup truck owners are those who are all about “freedom” and range anxiety is definitely hampering that.
Add an input/output shaft and I’m all in!
I’m glad I wasn’t the only one thinking “this would be a fun Jeep project”.
Fun if you got the moneys
It is for automakers, as described. All the auto makers have been working on traditional drivetrains for years as well and yet companies like ZF, Dana, and Borg-Warner all still exist and make major drivetrain components for nearly all of them. In fact, you may recognize Magna by it’s former name: Getrag, maker of major driveline components such as transmissions for nearly every large automaker on the planet, including the big 3 Americans. Big auto companies buy large pre-packaged modules from 3rd party companies like this for their cars all the time. Not surprising to see electric drivelines moving the same way.
As far as it being an ad, I disagree. Just because an article features a specific product doesn’t mean it’s an ad. Are all the posts about Espressif chips or the latest rpi just ads, or do you think it’s just interesting news for the DIY/Maker community? I see this as just a bit of news about a product that might be interesting to the huge DIY automotive community. But to each his own…I don’t spend a lot of time reading retro gaming articles but I certainly don’t lament that HaD wastes bits on things that I’m not interested in. I think there’s room for all of it.
Looking forward to seeing the first EV’d G-body….
Yeah, this sounds like a Press Release more than anything. It’d be interesting if someone figured how to recycle electric vehicle parts for a DIY project, or figured out how to get an electric motor to properly link to an already-existing differential, since there are quite a few interesting engineering problems there (like the high moment of inertia problem to avoid shredding the axle, or the problem of getting an electric motor to work with rapidly changing distances, and so on).
At the very least, it could have been interesting if their solution was something that could be replicated by a hobbyist, rather than something that would require massive manufacturing resources.
I am growing dissatisfied with HaD, it was a good reprieve from the PopSci and IFLS bullshit that floods the media, but it is becoming yet another website full of sucking up to corporations or celebrities like Elon. I’d say its still at least 10-15% actual hobbyist-related stuff, but the PR cruft is squeezing it out.
Ford, Mopar, GM and others don’t manufacture their truck axles. They do some of the housing design and some of the specifications, then have companies like Dana make them. Magna is wanting to get into the sort of OEM supplier position Dana has had for a long time.
Actually they have all made their own axles at one point or another, Gm Corp 14 bolt, gm 12 bolt, gm 10 bolt, ford 9″, ford sterling axles, Chrysler 9.25. the list goes on and on. Dana made a handful of axles,
They don’t any more though. This Magna applicatoin is for HD trucks like semis.
Gonna have to kinda hop in with the “who cares?” crowd on this one.
My only vehicle is a truck. I generally drive so infrequently and for short distances that it might actually be viable for me to have an electric version, instead. Except for one huge problem: The ENTIRE reason I own a truck and pay California’s stupidass weight fee every year is for the oddball trip where I have to haul or tow something heavy for a couple hundred miles, probably over mountains (and the occasional bulky item that won’t fit into another type of car). It’s already bad enough that the truck weighs nearly 7000lb, adding another 5000lb+ in trailer/load means I’d need a huge, expensive battery to manage that same trip.
Aside from the few “pretty boy” trucks that aren’t ever used for…you know…truck stuff, I imagine most who own a pickup are in a similar boat. The drive system is a solved problem, more or less. As has been the case with 90% of EV news in the last decade, call me when batteries catch up.
This would let you make your own hybrid, just set your drivetrain up to run the front wheels only. Then run the back on battery, or generator, or both, and the front freewheeling or under engine power. If the electric system is down or empty, run on front wheel drive gas.
Actually, this drive system would not likely work for towing/hauling very well. It would need some kind of active cooling, some software and hardware specifically to handle accelerating/slowing down a heavy (>2000 lb) trailer, integration with the trailer’s braking system, and some other things to work. Battery capacity isn’t the only issue.
Thats what I was thinking, those leafs won’t like that. Not to mention ground clearance
Shut up and take my Money!
speak for you self, this reminded me that I will have to make a production die soon for some of these rivian truck parts we have the contract for at work , more like a reminder that i have unwanted overtime
Combine it with something like this and I would be interested. https://www.piercemfg.com/tak-4-irs
Could bolt this on to a leaf spring trailer to make it easier to move when detached from the tow vehicle. Although it would be heavy….and expensive…and add drag…and reduce clearance.
Hmm, I might just buy one of those electric jockey wheels instead.
I just don’t see the top pickup truck brands going for this. As an example, Ford is well on its way to slowly transitioning to electric over the course of a decade or so. They’ve had start-stop on ecoboost engines for a decade and have worked out the details & brought designers, dealers & suppliers up to speed. That leads into their next step, hybrid pickups & the transit connect platform. Once they’re comfortable with that, assembly lines, dealers and customers will be used to the electric half. Then it’s just a matter of slowly, quietly removing the petroleum burning half. They aren’t looking for a bolt-in solution because fully electric drivetrain hardware is probably the smallest part of the entire transition.
I could see smaller medium duty truck companies – or ones that aren’t as far along with EV truck designs (Nissan, Ram, and Toyota come to mind) going for this. Particularly since Magna has already been supplying truck frames – somebody could very well see this as an opportunity to get into the electric truck market by ordering a complete chassis / drivetrain, and just adding a battery pack and bodywork.
Did they borrow the design from EZGO or Clubcar?
Retrofit for my van -> Hybrid would be cool. No need for a massive battery as the trips where the battery would be useful would be short and the big ones where I am going long distance / towing / loaded the battery would be too big to be practical. I think for a lot of light goods vehicles (as most vans and pickups come under in the UK (<3500kg max laden, 3500kg max trailer)) have similar usage pattern.
exactly what i was thinking about to keep my 20 year old dodge 1500 rolling when the 318 engine finally gives up….make it articulated and you have front wheel and 4wheel capabilties for a large number of common vehicles..you that are going about unsprung weight and ground clearance are tangentially challenged from US marketting…..for a damn car or truck it is definitelyan acceptable solution
hmmm damn should have been daily
I would think someone could design a slide in battery box that goes in the bed of the truck with the space above it able to be used for usual truck things, obviously not full contractor capability but plenty for harry homeowner to use and then put the chraging plug under the existing fuel flap. Most pickup trucks have at least 1/2 ton of load carrying and a truck load of batteries on a tray is not that heavy.
You’re forgetting the need to protect those batteries in case of accident. A truck load of lithium on fire probably wouldn’t be fun.
This looks like it would be great for camper vans and RVs since you have room for a big battery there and would want to have a battery anyway….
One really big problem that I see with this design is the exposure that the motor, harness etc. would have to salt, mud, rocks, water, snow etc., due to the very low rearward placement of the unit. Anyone who has ever driven a car or truck on the gravel back roads of the world knows all about this; the underside gets a constant abrasive, destructive blast. Also, rear differentials are in just the right spot to take major blows from protruding rocks, or to be dragged when the wheels are in ruts.
Perhaps, the best solution would be to use a conventional differential, and place the motor out of the way, on the other end of a drive shaft.
It’s not quite what the article is talking about, but a lot of AWD hybrids now have electric motor/diff assemblies for the rear wheels that are pretty much perfect for small EV conversion. You can often find them for around £100 here as they seem to outlive the cars they’re used in, and thanks to the great folks over at https://openinverter.org/forum/ you can control it all with a £50 scrap prius inverter.
If you’re planning an EV project and somehow haven’t come across it I wholly recommend lurking on the forums or checking out Damien Maguire on youtube.
Thanks for the link to Open Inverter. I read some stuff a decade ago about repurposing prius electrics (I think the University of South Australia used Prius bits in their TREV project: https://www.energymatters.com.au/renewable-news/em742/)
Good to see people are still hacking on Prius parts. When I have infinite spare time I’d love to build a lightweight EV using scrounged Prius parts…
Hook those motors to the Toyota crate fuel cell module:
https://newatlas.com/energy/toyota-fuel-cell-module/
Still need to find carbon fiber reinforced plastic tanks for 5000 PSI compressed hydrogen, but it’s SO close.
How about the same rig to drive an ultra light aircraft propeller?
It doesn’t look like you could easily create a hybrid and maintain 4WD; you’d have to remove the engine and make it exclusively electric, unless someone starts making aftermarket transmissions that have selectable input shafts, like a reverse differential. The market for pickup truck engines may become really good for buyers as the warehouses are filled with brand new engines that have been removed from conversion trucks. I suspect that domestic auto makers will step up and make trucks that people want, and the market for this thing will be low, because it requires so much effort. Or perhaps this company is hoping to sell this to automakers?
I have a 1960 near perfect Thunderbird. I could put this system in replacing the whole rear assembly , pull the engine and stuff out and build a battery bank there. I wonder what that would cost me? Also, seems to me to be an incredible market for owners of era cars like mine (Chevy’s too!!)Comments?