Research activity into 3D printing never seems to end, with an almost constant stream of new techniques and improvements upon old ones hitting the news practically daily. This time, the focus is on a technique we’ve not covered so much, namely binder jetting additive manufacturing (BJAM for short, catchy huh?) Specifically the team from Oak Ridge National Laboratory, who have been exploring the use of so-called hyperbranched Polyethyleneimine (PEI) as a binder for jetting onto plain old foundry silica sand (nature, free access.)
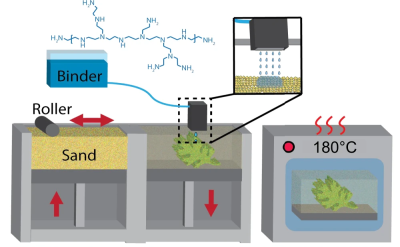
The PEI binder was mixed with a 75:25 mix of water and 1-propanol (not to be mixed up with 2-propanol aka isopropanol) to get the correct viscosity for jetting with a piezoelectric print head and the correct surface tension to allow adequate powder bed penetration, giving optimal binding efficiency. The team reported a two-fold increase in strength over previous jetting techniques, however, the real news is what they did next; by infusing the printed part (known as the green part) with common old ethyl cyanoacrylate (ECA, or super glue to us) the structural strength of the print increased a further eight times due to the reaction between the binder and the ECA infiltrate.
To further bestow the virtues of the PEI binder/ECA mix, it turns out to be water-soluble, at least for a couple of days, so can be used to make complex form washout tooling — internal supports that can be washed away. After a few days, the curing process is complete, resulting in a structure that is reportedly stronger than concrete. Reinforce this with carbon fiber, and boy do you have a tough building material!
Not bad for some pretty common materials and a simple printing process.
We covered a similar binder jetting process for using sawdust a little while ago, and a neat way of printing with metal powder by carrying it in a stream of argon and cooking it with a laser, but there is an opening for a DIY effort to get in on the binder jetting game.
Thanks [Victor] for the tip!
Can you put it in nature, or will it shed toxic particles?
The PEI binder is toxic. No idea if it will shed toxic particles but it seems like a safe bet.
Replace it with bicarbonate of soda and you can make all the super glue concrete you want. Plus it’ll bake itself.
So, basically an ultra-complicated form of concrete using polymers as a binder?
No thanks, I’ll stick with Portland cement as a binder instead. No need to reinvent the wheel, IMO.
Cement has a massive carbon and energy load — 7% of global CO² emissions in 2019 according to the first source I found (https://economictimes.indiatimes.com/industry/renewables/cement-the-carbon-cost-of-construction/articleshow/87100671.cms). I don’t think anyone will know if this new process is better or not until it starts being used in bulk, if it any does, but we seriously need to investigate alternatives.
BTW, sand is not free — it’s also a non-renewable resource which is in increasingly short supply. https://www.bbc.com/future/article/20191108-why-the-world-is-running-out-of-sand
Non-renewable?
It is a product of erosion.
The issue is that you have be specific about what sand you use. Sand that’s too eroded has a round shape which isn’t good for making concrete.
True. And even worse, “sharp sand” as it is called, is running out. The millions of tonnes a year we use can’t be taken from beaches and the like, it has to be dug up. Regular sand, of which there are tonnes without end, has not enough pointy bits for a good mechanical bond, being, as you said, weathered.
Well, sounds like it’s time for another hack; turn round sand into pointy sand!
Crush it into a powder, squish it between two heated and cooled rollers so it extrudes sheets of tempered glass, smash it up as it leaves, so you get the little cubes like a car windscreen.
We could mine it from the moon.
I’m full of great ideas like that.
Concretes pollutes a lot because it’s a cheap material that with a simple process can be used to build massive structures and because we produce 10s of billions of tons of it each year. While concrete pollutes a lot in absolute terms, its better to compare the pollution generated by a specific weight of concrete vs the same weight of other structural materials.
Given how involved it is, the process discussed in this article clearly isn’t meant to replace concrete in that role, it is meant for more specialized uses.
Cement does not emit carbon, only stupid ways of producing it does.
There is no need to burn fossil fuels to heat up limestone, or any other step in the production.
You could easily make it using renewable energy!
And we could do as the romans, and use volcanic ash instead of sand.
(but then should you count non man-made CO2 emissions?)
The most commonly used type of hydraulic cement starts with CaCO3 and the calcination emits the CO2 leaving CaCO. Through various steps, the Calcium Oxide is reacted into something like 4CaOAl2O3Fe2O3 which then hardens through a hydration reaction.
Notice where the CO2 from the initial calcination step went? Up in the air. Even if this was done in an electric oven, you would still emit tons and tons of CO2.
Non-hydraulic cement hardens by carbonation with CO2 from the air, but it’s a reaction that happens so slowly that it’s hardly ever used because large structures would take centuries to set, and it doesn’t work underwater.
Binder jet 3d printing is well established, so that’s not what’s interesting here. It works well when the material is to be sintered after printing, but is otherwise fragile. Since colorants can be mixed in it’s used frequently for visual prototypes that don’t need to have mechanical strength. IIRC binder jet is expensive and messy, but not as costly and dangerous as DMLS.
The innovation is a binder that results in less fragile prints off the machine, but can also be washed out with water for casting or sintering purposes. Having a curing window after which the binder can’t be washed away means that the same binder and printing system can be used for all of the above use cases.
The primary use case here is to produce strong high precision sand casting moulds that can be dissolved away after use. This isn’t a permanent structure (see water soluble). Think cheap to print and less machining to do on the casting afterwards.
3d printing cast iron and aluminum molds?
That’s something I would be interested too! If it can be reusable that’s even better
I’ve been patiently following the oasis 3d printer build for this exact reason. Some stuff is going on in the forum here, but it’s slow progress. https://ytec3d.com/forum/viewforum.php?f=8&sid=b6e14d591741e627c2891f28b243c5f0
Good thing I have 4 or 5 other projects that I need to work on first anyway.
After reading the blog, I was unsure how they went from a box of sand to an oak leaf.
While reading the linked article, it became apparent that the sand is built up layer by layer between applications of the binder.
I wonder if this could be used on Mars with the native sand.
To form bricks, or better yet, the entire structure as a single unit. Although it begs the question, how can we make superglue on Mars.
Anything made with Martian dirt/dust is almost certainly going to make use of it’s iron content because there is sooo much iron on that planet.
“it turns out to be water-soluble”
Water soluble or “turns into plastic nanoparticles you can’t see”?
You mean “sand”? That’s not a plastic, though you will find it all over many beaches.
They are using plastic and super glue to bind the sand.
There is a repair product Q-bond for plastic panel repairs (cars, bikes, etc). That is just powdered plastic and CA glue.
In reef aquarium keeping, it is quite popular now to stick together reef rock with sand and CA glue, for producing interesting aquascapes.
So sort of surprised to read this as some sort of ‘3D Printing breakthrough’. I thought it would already be quite common.
Makes me think of the baking soda and crazy glue trick, I wonder if you could 3D print with a baking soda slurry and then soak it with crazy glue to make a hard model?
What kind of Sand did they use?
Was it sand from the beach or the desert?