Soldering! It’s the primary method for attaching one component to another in the world of electronics. Whether you’re free-forming a circuit, attaching connectors to cables, or populating a PCB, you’ll eventually find yourself doing some soldering, whether by hand, reflow, or maybe even a fancy wave soldering machine.
It’s a fundamental skill that nevertheless remains one of the biggest hurdles for newcomers to overcome when diving into the electronics hobby. Difficult jobs with tiny components or with large heat sinks can up the challenge for even well-practiced hands. Thus, today we ask the question: What’s your worst soldering job?
It’s All About Heat
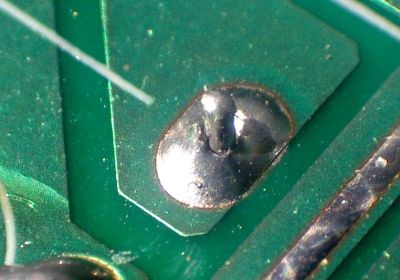
One of the most common causes of a bad solder joint is not getting everything hot enough. If you don’t get the temperature high enough, the solder will simply fail to stick. This doesn’t just apply to the soldering iron, or the solder itself. You have to get the component leads, PCB pads, or wire you’re soldering up to high temperature as well.
If you’ve ever had a molten blob of solder that simply won’t grab on to, or wet, the part you’re soldering, you probably haven’t gotten things hot enough. The principle is easy to see in action. Bring a soldering iron tip with plenty of solder on it up to a stripped piece of copper wire. The solder will blob ineffectually next to the wire until the copper itself reaches a suitable temperature. Then, you’ll readily see the solder wick on to the wire itself.
Of course, in some situations, it can be difficult to get things hot enough. Trying to solder a component on to a PCB pad that’s part of a large ground plane can be incredibly difficult, as the ground plane acts as a heat sink. Similarly, soldering large-diameter battery cables or big high-current connectors can be similarly difficult. Where a little 20 W soldering iron might be perfect for soldering small chips and resistors, you may find you want a 80 W iron – or more – when soldering things like connectors for high-current LiPo batteries in hobby applications. Alternatively, design changes can help – many PCBs use thermal reliefs around ground pads to reduce the outflow of heat from the pad while soldering.
Without plenty of heat, a solder joint will look frosty and have very poor adhesion. It’ll probably fail under even the slightest physical disturbance, flex, or vibration.
Chemistry Plays A Part
Other times, you might find a soldering job difficult because of the materials involved. Metals like aluminium are incredibly difficult to solder, as the metal forms a oxide skin that prevents solder sticking. Plus, it’s a great heatsink as well, only making things more difficult. In situations like these, specialist fluxes are often essential to making a bond without a lot of hassle.
Alternatively, homespun DIY techniques can also help. When it comes to aluminium, some see success by pouring an oil layer over the metal and scraping away with the soldering iron tip or a sharp object. This penetrates the oxide layer while the oil protects it from reforming.
But beware: often, a failed solder joint under these conditions will look like a smooth, well-rounded blob on a wire or component lead, but be completely unattached to the metal below.
Getting It Done, Anywhere, Anytime
In these situations, mistakes are common, and injuries and light burns are often more likely. However, it’s these tough fixes that often bring the most pride and joy. Whipping up a crucial audio cable backstage might just save a gig, and some hasty jumper wiring might just get your company’s product up and running for the big annual convention.
Always Learning
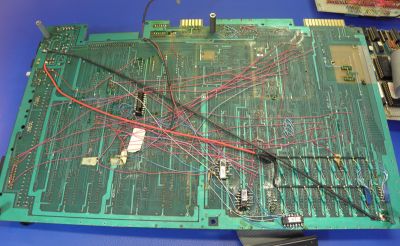
The fact is, we’re all learning every day, with every solder joint we make. Along the way, it’s often the tough jobs and the bad joints that teach us how to become better at soldering, whether it’s through-hole, SMD, BGA, or for a production run of millions.
We’d love to hear your stories, and see your pictures, so hit us up in the comments. What are your worst solder joints, with the worst tools, or with the worst outcome? What have you gained or lost in the process? Let us know!
My 9 year old self built a circuit using acid core plumber’s solder and a large factor soldering iron ( dad was a plumber). Suffice it to say, circuit stopped working a year later.
I did this too, but I was younger and my dad helped out. He wasn’t a plumber, but he didn’t realize that rosin core solder was used on electronics for a reason. Our little radio shack skin galvanometer didn’t last a _day_ much less a year.
I was fortunate enough to use the right solder. I put together my Dad’s left-over Heathkit FM tuner with a MONSTROUSLY large Weller soldering gun. It was a fantastically sloppy soldering mess. BUT IT WORKED!
Dad was a little dismayed I’d hijacked one of his “round-tuit” projects but was rightly impressed that a 10 year old figured it all out on his own. Props to the Heathkit instructions, they really explained everything.
As for terrible, let’s just say doing Apple /// motherboard upgrades and lifting circuit traces was not one of my prouder moments as a service tech!
If you’re new to electronics your absolutely BEST money spent will be on a REALLY GOOD soldering iron setup.
Not quite mine, but in high school someone made a Dallas 1-Wire Touch Button holder out of wire and a whole lot of not-RoHS solder. It wasn’t so much bad as it was a creative abuse of materials.
I used to be terrible at soldering. I recently got the pinecil, my first proper soldering iron. Life is so much easier now. I had a normal one that you directly plugged in, no controls at all. Then I bought a gas powered one, which was also terrible. Then the cheapest soldering station, but that was still terrible. I also bought proper solder (309, 60/40, non-RoHS) which is also a massive amount better. Hope to pick up my new points for the iron today. Going to make a nice box with everything I need for soldering.
Get some 63/37 eutectic ratio and say goodbye to cold joints. And a flux pen.
It’s illegal to sell to the public under RoHS in the EU. Can’t find any in the stores.
Wow! I just bought a new spool a couple years ago, here in Germany, and it’s leaded. Now I go look, and I can’t find any anywhere either.
Damn. Good thing I bought the 500g spool! Should last me a few years. :)
Last I checked Poland is in EU. https://www.piekarz.pl/39118-cynel-spoiwo-lutownicze-lc63-0-80-1-00-szpulka-1kg-0-8mm-sn63-pb37-/
63/37 isn’t as widely available as 60/40, but there is absolutely no problem with buying it, either in wire or paste form.
It is legal to sell to businesses and special purposes, like medical devices and industrial instruments. As an individual, you can’t buy it, or the shop is breaking the regulations.
I saw some lead free car battery terminals in an auto store once. Made me laugh. Car batteries still have lead terminals (posts) here.
Very satisfying to see a 63/37 joint *snap* freeze, compared to the mushy, slushy transition a 60/40 makes.
Maybe I’m not seeing things correctly [stumbles while looking for glasses], but is the iron in the photograph at the top of the article being held strangely?
Ouch!!!! Good eye.
Yes! That classic soldering picture where the hand model has never once held a hot iron.
Or used a soldering iron precisely once.
I was wondering why it smelled like chicken! :)
Not in this case. That’s a Metcal iron. For many years I tried to solder with various wand and gun irons without much success. Then someone I worked with taught me how to solder using a Metcal iron, and after learning a few things it was fairly easy. Then when I tried again to solder using my wand iron the first thing that I noticed was that it was awkward holding the iron handle. Then I went back and actually looked at the iron I’d been taught on with an eye towards what was different (and remembering the brand). The pencil grip is so much easier, precise, and less dangerous. The handle itself is mostly hollow with a socket near the cord. The “tips” are as long as the handle and aside from the socket they plug into mostly float in the middle of the handle.
You’re right(ish) about the handle — it’s an AoYue 2901, and it’s about 15 years old now, but it’s a ripoff of the cassette style irons that you’re talking about. And those style irons really do have the tip a lot closer to where your fingers normally sit than the screw-on-tip kind. I love mine!
But you’re wrong about me burning my fingers! Well, you’re right, because the iron was off, but I was grabbing the tip. Just for laughs. :)
I thought maybe it was a scope probe rather than an iron…
Good catch
Someone should build a battery powered remote controllable soldering iron…
I am not quite, but for me this looks like a multimeter probe. Still not quite right. ^^
I have developed a deep loathing for the cheap copper plated aluminum wire. Most of the cheap bundles of jumper cables that are terminated with the dupont male or female terminals are this type. We frequently attempt to cut and splice these jumpers at work for different prototypes or test setups and it drives my blood pressure up every time.
The only way that I’ve found to get even a marginal solder joint on this stuff is to create a solder blob on where it is going, generous amount of flux on top, heat the blob and shove the stripped wire into it.
Anyone know of a good source of jumper wires that use actual copper wire?
Your best bet is to make you own. They sell the crimp pins and housing.
My first projects were awful, never worked and I didn’t have the skills to figure out why. In retrospect, the awful soldering must not have helped. I used a woid burning kit that was around, and certainly only knew to heat up the solder. So blobs of solder on every joint.
The first things that did work were made from parts I pulled off boards, so by then I knew enoigh to decide what would work. And I just twisted the tiny leads together.
Then with a proper soldering iron, I was able to solser, I don’t remember it being a slow start after the. first disasters.
“The bigger the blog, the better the job.” Words to die by.
D’oH! can’t spell tonight. “The bigger the blob, the better the job”
Great tools make a lot of difference. I began soldering with cheap everything (solder, iron, etc) and thought my skills were garbage; that is until I got a hand in quality tools, my soldering improved like crazy.
I needed a lot of wires to come together to one point (in a wooden enclosure), and decided somehow a washer was a good place to do this. Which it isn’t because the washer I chose is galvanized and relatively large so the washer kept being not hot enough to hold the solder to.
Teaching my kid how to solder without him getting burnt fingers in the process.
Was just doing that this weekend! He soldered together his first buzzer + button circuit — we’re going to set it up as a doorbell on his playroom.
His favorite part of the whole experience? The solder sucker.
I hate to say it but a little burn would be a good safety lesson.
As a young teen, I was working at the bench with a wood burner style iron. I set the iron on the edge of the bench (as I often did), then moved and knocked the iron off the bench. I caught it… by the hot end. Instant regret. I had blisters on my right thumb, several fingers and the palm near the fingers. Bad enough, but we were going to an upscale restaurant in an hour or so.
You do that kind of thing just once. Since then, I’ve always just let the iron land on the floor. I’m 62.
I had my own experience like that but luckily I wasn’t fast enough and just touched the iron with the back of a couple of fingers. There’s definitely a reason they say not to try and catch falling chisels/knives/soldering irons.
Heh, yep, been there, done that, have the scars between my fingers to prove it.
When working on a crossover, I had problems soldering non-enamaled wire, which was coated with something which wasn’t supposed to need scraping before soldering. I could not find the correct temperature, which caused the coating substance to contaminate the joint.
I’ve used something similar, with similar problems, for PCB bodges – fine wire wrap wire. I ended up using two soldering irons, one set hotter than normal. The hot one I used to burn off the coating first (in front of a extractor fan!) and it would then solder normally with the other. It wasn’t quite the quick convenient solution it was made to sound like!
A solder pot and rosin are your friends for heat-strippable coatings. Hold the wire with some needlenose pliers to act as a heatsink, and that sets the strip length very easily.
I was starting with serious electronics and decided to assemble PCB faster by spreading solder paste across the whole PCB, put SMD components on it and reflow it in the oven. Somehow I thought solder paste stencil is only optional. You can see results published here :D Be careful – ugly picture :)
https://hackaday.io/project/19799-lifetime-fails-project/log/53106-solder-paste-wont-be-easily-cleaned-from-pcb-after-reflow-in-oven
Oof that is pretty bad, just starting with smd myself. I kinda get your logic though because when you heat the solder paste up it collects on the pads and is pulled on to the pads but it doesn’t quite work out if you try it like you did.
Plumbing of course, after filling the system and there’s one leak on a joint, and the inside of the tube is all wet after draining, so it takes ages to heat up before the solder will flow again.
I actually spent over an hour trying to do a solder joint on a vertical pipe which still had water in it. with a very crappy soldering burner (based on a lighter). The standing water made it impossible to heat the pipe enough for solder to flow. In the end, we cut the pipe at the lowest point, which drained all the water for at least two metres, and managed to do both joints in about 10 minutes, even with this crappy burner.
Been there, done that!
I can just barely get pipe to solder correctly with water based flux.
Last time I looked, they still had good flux at Lowes (in CA at that), but you had to look for it.
I now have a lifetime supply stashed away with my freon based contact cleaner, tetraethyl lead octane booster, 2 stroke oil and lead containing solder.
Pads that are part of a ground plane without thermal isolation!
“IT’S ALL ABOUT HEAT”
Naa no heat in the world could replace a decent flux!
I once soldered with a screwdriver that I’ve heated with a candle. But I had decent solder, so i consider it cheating.
^THIS^
Any time I am struggling with a solder joint I will reach for flux before I reach for the temperature control. I have liquid and paste flux on hand at all times.
I am interrupting soldering a replacement SOIC 8 on a conformal coated board to type this. I have taught classes in IPC hand soldering, wire add and rework.
.
FLUX FLUX FLUX
Among other things flux changes the surface tension of molten solder which also helps it flow. It’s main function is surface prep as it burns off it removes the copper and solder oxide. Hidden in that statement is that fact that flux is used up as it works. Your older joint may have flux residue on it, but that doesn’t mean it will help as it may have already been activated and used.
The industry mostly uses NO-CLEAN flux which is pretty much inert after it is activated. No cleaning is required once activated by heat. Our customers that don’t go for a cleaning process usually bake the finished board to make sure any remainder is inerted, but I seldom do in the lab. Regular ROSIN based fluxes work well, but are harder to clean. Both work fine with ROHS or lead solder. You may have to use more flux with ROHS because more will burn off while getting to the higher heat to solder Tin.
We use water and a saponifier in what looks like an industrial dishwasher to clean either both in production.
DO NOT USE WATER SOLUBLE FLUX. It has to be 100% cleaned, which is difficult or it absorbs moisture from the air and will start to leak current. High impedance circuits with stop working eventually.
In the lab I usually use canned flux cleaner or just dry alcohol (~86-96%). It is easy to put just enough alcohol to cover the board in a tray, then brush it with an acid brush after soaking a few minutes. Blowing it dry with mild heat will keep the condensation down as the alcohol cools the board while drying.
I am using a paste style no-clean in the lab just because it stays until heated. I can just dip my SMT leads into it before placing on board. When hand soldering even in production, we almost flood the area with flux. The limit is really how much you want to clean. Good idea as well for a newby, because if you take too long, you can burn up the flux before you get to temperature.
I have used a screwdriver and a butane lighter many times as long as you use solder with flux or add some.
If you take non-flux core solder on a dry board, it will just bead up on the copper patina and refuse to flow. It is a must when reheating a cleaned joint. I also use it when removing parts.
If you see a wave solder in action, the first thing it does is spray the entire board with flux before preheating.
Solder paste is basically ground up solder mixed in gelled flux.
It must be hard putting things down…. B)
No amount of decent flux could make up for not enough heat?!
Flux don’t do jack if the iron ain’t hot enough.
Flux is the **last** thing I reach for. It makes mess.
Your solder should have an appropriate amount of flux in it.
If you have to add flux then either you are doing something wrong or you’ve got crappy solder.
Mostly, folks use crappy solder to save a few cents when buying a roll. Then it sucks so bad they have to buy and use extra flux.
Get good solder from a good manufacturer.
Stannol is what I use, but I’m not sure you can get it outside Germany.
I remember buying some solder, maybe at a hardware store, and it was awful. It seemed to lack flux. I can’t remember if it was mismarked or a bad batch. I did throw it out.
So yes, good solder meant for electronics shouldn’t need flux. Maybe soldering power devices or something with big leads, extraflux helps.
Old joints lack flux. Heat isn’t enough, I find I have to add solder to make the old flow.
You can get it in The Netherlands.
I work on electronics that would be called “vintage” at least. You can scrape component leads all day or you can use flux. Higher heat will *NOT* help.
I used a flat screwdriver left wedged at an angle in a stove top element to heat.
I was staying in someone;s holiday home for free and felt duty bound to repair a few things. The outside light didn’t work and the problem was years of corrosion and one of the springy contacts on the bayonet holder was not springy any more. I didn’t have another bayonet socket so I decided to bodge the bulb itself by putting a blob more solder on one side of the E27 male. However – no soldering iron?
I heated up the electric plate on the stove and melted out a few blobs of solder off the old bulb. Then melted onto the new bulb, with the aid of a knife from the cutlery drawer. All good leaded stuff of course!
As the new bulb is LED it should last many years, at which point the bayonet lampholder can be replaced!
I only started using flux a few years ago. Been soldering since I was 7 years old. Fortunately my dad had a decent ‘vintage’ Weller that I used to use. It needed it’s first element replacement after decades of use.
I find that some switches, fuse holders and audio jacks will not wet unless fluxed; previously I would just lightly file/sand the leads to make a solid connection.
My first soldering iron was a resistive type based on transformer. It was a pistol grip beast made 10-15 years before I was born. My first project was a kit, an electronic roulette. I managed to burn and partially melt the PCB. I was 12.
My absolute worst soldering job was an attempt at TQFP100 dsPIC. I used rubber bands to hold it down, my wife positioned it, I still managed to bump it while covering every leg and pad in sea of solder.
About 12 years ago I accidentally dropped hot soldering iron on my naked thigh, and two seconds later on the carpet. That was my year of accidents. Few weeks before I grabbed PCB of my (broken) IR2135 SMPS PSU while it was plugged in, touched primary side of ATX PSU PCB with my forearm, while it was plugged in, and discharged primary capacitors of that PSU with my face. To be exact, between tip of my nose and lower lip. All in one evening.
If you don’t have a hot air station (there’s something beautiful the way components just jump into place, or occasionally smt caps get a little too turned on and stand up erect :) then line up the pins with the pads, check with a magnifying glass, Then clamp with your thumb or fingers the chip, double check it hasn’t shifted then solder a corner pin or two to fix it in place – this can be done one handed without applying solder assuming you’ve tinned the pads, it doesn’t need to be perfect it’s just for anchoring. Now the chip’s anchored you’re free to solder the remaining pins with your favourite method (and re-do the joint pins if necessary).
I have a hot air station. In case of TQFP if you are off by more than half of spacing between pins, it will solder incorrectly with hot air. Surface tension of the molten solder would snap the IC to the nearest pads. And my eyesight is so bad, there is an article on HaD about me. So my plan for now is to build a macro camera for soldering small components.
Get yourself a microscope, either a digital or optical one, they do really help.
That’s a lot of learning for a single year!
Si-Diodes as sensors for cryo-applications have to be soldered using indium as solder.
Indium does not like other metals and is extremely difficult to solder.
I was happy when, after many tries I had joined the respective wires with the ugliest solder blobs I have ever created.
Would spot welding instead of soldering not work?
The sensor had to be replaced in the chamber of a scientific experiment with no space for a spot welder.
Also no flux because of ultra high vacuum requirements.
I do spot weld and crimp whenever possible.
Uhhh….
A decade or so ago I got a “used” 48ports GBit switch for cheap which didn’t really work because of bloated caps.
Dunno how many layers that board has but it occupied all available space, the caps were scattered around a bit and replacing them was not much fun. :-/
Maybe I didn’t have a heat gun at that time to preheat the ground plane?
But I got the switch working properly again anyway. :-)
Been there, but with a 24 port GB switch. I had to use a preheater cranked all of the way up, let the board soak for a long time, and then attempt heating up the leads with the iron and solder wick. It eventually worked, but that process really sucked.
My worst soldering job was on a self etched board using my dad’s janky military issue iron. No temperature control, and the iron always had thermal runaway to the point where it heated up enough to melt/warp the tip. The resulting joints were definitely not cold, but it being my first time actually soldering is had very little idea what I was doing. I found the board/project a little while back and apparently I had never cleaned off the massive amounts of sketchy flux, which had eaten through the wires of the 9v battery clip I had used.
It ain’t electronical, but I once had to solder a thin stainless steel gas pilot tube. It got kinked and subsequently cracked. With no replacement available, I cut and sleeved it. The sleeve was thicker stainless with a nice snug id. Flux for stainless is horrible stuff. It was no problem heating the sleeve, but the thin tube was a nightmare. It cooled off almost instantly. I eventually got it to hold pressure, but it was way more education than I would prefer in one sitting.
My worst soldering job was a non-electrical one – a copper pipe that just would not stop leaking no matter what I tried. I finally tried to cover the leaking point with epoxy putty and hope for the best.
And the best was still leaking. So I decided to take the whole thing off and replace it with a compression fitting. But removing that epoxy was tough – so I decided to just light the blowtorch and figure the problem would take care of itself. Big mistake – the whole house smelled like burning epoxy for days. Could have been worse, at least I didn’t burn down the bathroom.
I worked for a couple of years as an “engineer” at a small metalworking manufacturer. Mostly I did whatever needed doing, lots of toolroom work and machine setup. I had mentioned in my interview that I worked in electronics repair for a few years, mostly surface mount only some hot air/BGA stuff, but I generally knew how to hold a soldering iron.
Well it seems my boss remembered that, since one day we had the second machine for an op go down due to a fried power board. He wanted one of the two machines back up ASAP since we were already behind on an order. The other machine had already fried the same board best we could tell. All we had was a couple of normal multimeters, and I was not going to use it on running 3-phase. But surely it didn’t fry all of the fets on the board? So we decide to swap some from one board onto the other and try it.
The solution? Turn down some copper bar to have a point, file it to a chisel tip, have the operator hold a torch for me to heat it on, and use the pointy copper bar to solder. It certainly got hot enough, made a horrible mess, glopped solder everywhere, and burned some of the board, and had to make two swaps since the first did not work. 50/50 odds that I either swapped a dead one from the donor, or fried a good one with the heat.
In the end it worked, and that board was still in service a year later when I finally left (despite my protests it needed to be replaced). The shop ran like shit, and the focus was always on catching up on orders, not matter the cost. I had warned my boss there was a good chance the “fix” could further damage the machine, he did not care so long as there was a chance it could get the machine working for 3rd shift to use.
Killed a lot of vol pots on guitars before I figured out how to solder a ground to one without overheating. Initially I would just flow more solder down and linger longer. Would create a joint, a joint with some audible quality to it but never held long like that since the solder barely fused at all with the surface. Took carving a guitar to care enough to finally try scuffing the pot then fluxing it, felt like an idiot for how much better that was. Those first proper joints on the back of a vol pot are still holding about 15 years later. Began to care a lot more for fine details of all my craft type work at that point.
Current worst is replacing roughly 1.5x3mm surface mount relays on our 22 layer test board, because for some reason these relays are DFN’s, and are packed in as tightly as the pick and place machine can put them. By the time a hot air pencil manages to get the power and ground planes hot enough, nearby parts (0402) have started blowing off.
All time worst was a QFN capable of several amps, that was on a 12 ounce copper board. The copper plating was so thick it was no longer uniform thickness, so trying to put a part down meant a lot of pads had gaps between the board and the package pad. We only had about 30% first-pass success on getting those to work. Since it had a thermal pad under the package that had to be soldered down, but the thermal pad was electrically connected to the die (ground) we could measure the body diode drop to each pin to check if we were successful before powering it up.
i got a box full of old hand made pcbs ive made over the years. lots of bad designs and bad etch jobs make the bad soldering look almost good. some are stuck in firmware limbo waiting on me to finish code stopped working on. some are analog circuits that never quite did what i wanted them to do. a whole lot of boards were just me experimenting with battery management for my various attempts at a raspberry pi tablet. all could have been avoided if id just ordered pcbs and modern components and stop relying on a bunch of components from the ’70s.
>Without plenty of heat, a solder joint will look frosty
With lead-free solder, it will do that anyways. Difficult to tell a bad solder joint because the surface turns dull instantly after cooling down.
A friend of mine built a Sinclair Scientific Calculator kit. First kit, first soldering experience. He carefully heated the solder on the iron and dabbed it quickly on each pin and lead. Cold solder joints galore – although easily remedied.
http://www.vintagecalculators.com/html/scientific_-_giant_scientific.html
For me it’s got to be microwave carrier plates – aluminium PCB with teflon insulator and gold tracks. Especially stub tuning.
Too much solder? Bad signal.
Too little solder? Bad signal.
Finally got a good signal? Clean that joint. Now it’s a bad signal!
Got a good signal and a clean joint? Put the case on. Now it’s a bad signal!
Too much time or heat put in? Get reprimanded for accidentally damaging a board worth thousands.
Then there was the tuning with ferrite beads and superglue, where you had to get the right position, with the right amount of glue, and hope the signal didn’t change too much when the glue dried.
As a kid, no one would tell me about dwell time and the amount of pressure you should use on a solder joint or pad. I’ve ripped pads and burnt PCBs a lot using a mains powered resistive load iron, about 30W. The tip fell off all the time because it was just clamped and when heating up it expands.
My worst attempt is probably a small audio amplifier on a FR1 perfboard, which burn and rip pads off easily with longer dwell times. The bottom looks more like a rats nest dead bug style soldering with huge blobs and components flapping in the breeze. It got soldered and resoldered until it was just one big mess. With painters tape stuck on it turning it in a sticky mess as well. I was 12 or so, so what can you do?
I went through a couple of soldering irons with attached mains cable after which I got a cheap station with temperature control. Heated up in 1 minute, which what pretty quick compared to the mains cable ones.
I don’t remember burning my hands much with it though, you learn quick enough to avoid touching hot stuff! I did burn a hole in clothes when the iron slipped from my grasp though.
Now got a 70W Aoyuoe rework station with pre heater and hot air gun which was a lot better.
I’ve been reading up a lot on the current state of soldering stations lately though. The newer irons with 130-200W PSU and cartridges with the resistive heater and temperature sensor in the tip seem to be the best. Like the JBC ripoff aixun T3A with T245 hand piece. I’ve ordered one last week, should arrive next week. I’ve ordered a couple of geniune jbc tips, T245-931, which is a hoove/well type tip for drag soldering. And a big 5mm chissel tip for large solder jobs like transformers, large ground planes or speaker filter soldering jobs, PC mainboard recapping etc.
Metcal has even better performing inductive tips which seem to deliver heat to the workpiece even more efficiently. These are out of my price range at over 800-900 euros for a full set.
Heat capacity and heater close to the tip will deliver much more heat and the tip will not drop in temperature as much with heavy leads compared to the more traditional sleeve tips that drop over a ceramic heater.
I absolutely love that main stock photo, where the person holds his soldering iron at the (mildly warmed) tip socket instead of the plastic handle ;-)
Thanks! I actually went looking for a soldering stock photo, and then was like, screw it, I’ll take my own.
So I choked up on the pen a little bit for authenticity’s sake. :)
I once travelled about 3000kM from a tropical environment to freezing environment for a new job. I only had light clothing suitable to tropical environment and rode my motorcycle in the freezing morning to work.
I was given the nick-name “Camelion” as I would arrive to work a blue/grey color.
The soldering irons and all power were controlled by a breaker board that was turned off at the end of every day and turned back on the next morning.
A favourite haunt of mine was to grab someone’s soldering iron with my near frozen hand by the heating barrel for a moment and put it back down saying the breakers must be off. Most people would immediately do the same and burn there hand a little.
My first iron was a one handed iron with a mechanical trigger to advance the solder onto the tip. Horrible thing, I just took the solder out of it and used it normally. Prior to that I was using a hand cranked drill to drill holes in a breadboard (now you know where the name comes from) and use screws for connections. I was about 7 years old at the time so it’s over 50 years ago now.
Probably the better thing about starting so young is that I discovered in much later years that I could braze and do all the other soldering like things, MIG, TIG and even Arc. They’re all second nature when you have spent so long perfecting soldering.
When I was a kid, I didn’t know what a crimp on connector for a ribbon cable was. (This was back in ‘TRS-80 days’)
So I stripped the end of the cable and started soldering. After about 20 pins were connected I melted the connector.
Then realized I was a moron and started over, ‘crimped’ with standard pliers, it worked.
I use a vice with face protectors – bits of angle aluminium. It keeps the pressure even and the parts parallel.
I love guns! A Weller gun hangs out under both home and work benches and a spare downstairs for car work if needed. Most things get wired up with thick wire not frog hair wire. If it takes more than 2 or 3 seconds to get wetting and flow on anything it’s too dirty or there is no flux acting at the surface. That or there is not enough heat hence the gun.
Paste flux is a good thing too. Rework, repair, and retro fitting is often old wire and terminals that need a clean surface to get wet. Heating and shoving flux-core into the joint doesn’t get into the surface because of all the old solder that’s there already. Heat and suck it off and repeat or just dab a little flux on and reheat, flow it’s wet done. Two seconds.
The one time I somehow managed to drip molten solder onto my leg. Melted through my trousers straight onto bare skin. Not fun!
I’ve flicked hot solder into my eye before will doing the heat and smack-down desoldering technique. Needless to say I use eye protection now days.
Yeah… eye protection is useful sometimes.
The worst that happened to me in that regard is cutting of a small end of litz wire with on ~4mm strand flying into my eye.
Luckily it landed in such a way I – standing in front of a mirror – could use my smallest pliers to safely remove it without touching the eye ball. The piece kinda lay on top of the lower eye lid. Not on the front but the top (smushed between both eyelids if they were closed).
Does desoldering an E-Bike battery with a lighter in a parking lot count?
I was peering closely at an smd part while soldering and the iron touched my cheek. Needless to say, the long burn mark on my cheek was the object of much speculation at work for a few days
Bad Day Soldering Mark
Didn’t think I’d read about BDSM in connection with bad soldering experiences…. ;-)
8 inch heavy gauge copper grounding strap from a bank of 5 (x) 20 KW FM transmitter cabinets on the concrete floor of the equipment room in a rooftop combiner system to building ground. Because of the mass and thermal dissipation of the copper, I wound up using oxy-acetelyne. Fine line between soldering and melting, but it worked out well and looked good.
Soldering overhead copper pipe, had a blob of solder fall onto my forearm which reflexively retracted bringing the bicep into contact with the solder blob as well! The matching scars were, for a good ten years, a regular reminder to try hard to think about what was going to go wrong.
Not Soldering per say , But when I was a burner (Oxy/cet torch) at General Dynamics in Quincy Mass. I was cutting I-beams and the molten slag flowed right into the tongue of the army boots I had on and settled into the leather base of it ( like a pocket ) .
limped for about two weeks with that burn , still have a scar 40 + years later.
I have a soldering scar on my right hand between thumb and first finger where the soldering iron slipped off whatever electronics I was salvaging (probably some big resistors or caps off an old TV) and dug into my hand, the scar must be 43 years old now. It’s a mark of honour!
My worst soldering job ever was sweating copper supply pipes for a water softener in our garage. There was just a tiny little gap where the solder didn’t go all the way around and it was a slow leak for about a year before I finally decided to drain the system and redo it.
Hacker Battle Scars, Sounds like a new post to write about.
GroupDIY has a Shock Log
https://groupdiy.com/threads/electrical-shock-log-book.59084/
Can I count the ONE time I was featured on HAD as my worst soldering job when, in reality, everyone was criticizing my use of duct-tape as an insulator? Also, Blogspot is still a thing?! Who knew?!
https://hackaday.com/2010/02/04/battery-holder-reuses-blister-pack/
The internet never forgets!
I asked students to solder headers on a board. One team came back, telling me that the board does not work. Looking at their solder joints it was clear why:
https://mcuoneclipse.com/2014/10/14/how-not-to-solder-headers-on-a-board/
I did not think that it would be possible to solder things in such a ‘creative’ way. ;-)
He’s just ahead of his time. You’ve given him PTH to solder but clearly he would be better suited to BGA.
Yes, indeed! :-)
This is from one of my students: https://forum.robodoupe.cz/download/file.php?id=336&mode=view
good one too!
I use Weller Pu81, soldering wire 0.5mm Sn3.0, Ag0.5, cu3.5%, but all my tips become oxidized super fast, I even use tip activator , it helps, but withnin a day, tip is oxidized again. Any help/suggestion?
Thanks
Yes get some tip tinner, for example something like this https://uk.farnell.com/multicore-loctite/ttc-lf/cleaner-tip-lead-free-15g/dp/1115477 but I have the leaded stuff which is better. It will be harder to find leaded versions but you could scrape some lead into it I suppose.
My first PL-239 connector when I was a kid. There were globs. GLOBS! I ended up cutting it off and starting over.
I bought this diy phono preamp. Once finished it didn’t work. I asked a experienced friend and hebtold me that it’s full of cold solders but first of all components should be mounted on the other side.
The guy in the top picture is not an experienced solderer. He is holding the iron by the tip. I’m surprised there is no smoke.
Lining things up to nail down a .5mm spaced part. The last 0.003″ is an itch.
I thought it might be easier to tin a small bare copper board by smearing out some solder paste and heating it. Starting with the “try and see” method, it basically worked but was kinda lumpy and ugly, so I let it heat it some more to let the lumps even out – before figuring out that the lumpiness was the already-overcooked board. It didn’t get better.
https://cdn.hackaday.io/images/8961621629017864419.jpg
Solder Party,my Idea should realized this afternoon.
https://drive.google.com/drive/folders/1oLFll4Gc1S0vyxZiC42PrN6CylLoR_jd
Pipes, wires, tiny SMD components… There’s something about soldering that I’ve always enjoyed.
….recently I had the “opportunity” to try soldering gold by pick-soldering a repair on my wife’s gold chain.
Got it done… but if you haven’t tried it, let me tell you. If you’re micro-soldering electronics, you’ve got it _easy_ compared to a jeweler doing chain repair. And they don’t get paid very well compared to us either. Next time I won’t wait until the last moment and I’ll pay the local jeweler the $50.