When you think of machines you see around you every day, you probably think about your car, computer, or household appliances. However, the world is full of simple machines. One simple machine in particular, the inclined plane, shows up a lot. For example, think of the humble nail. If you are a woodworker or even a homeowner you probably have bags of them. They certainly are all around you if you are indoors and maybe even if you are outdoors right now. Nails have been the fastener of choice for a very long time and they are a form of a wedge which is a type of inclined plane.
What else can you say about nails? Turns out, there is a lot to know. Like other fasteners, there are nails for very specific purposes. There are even nails with two heads and — no kidding — nails with two points. Exactly what kind of nail you need depends on what you are doing and what’s important to you.
Terminology
Just about every nail has a head, a shank, and a point. You can probably guess where each of those terms mean. However, it is the details that matter. Some nails have very specific shapes for the head and the shank to work in particular applications.
There are many variations on each of these parts, though. Heads can be flat or cupped. There are countersink heads and textured heads known as checkered flatheads. As for the shanks, most nails are smooth, but some are twisted to prevent bending or have rings or barbs in them to grip the wood better. Even the point design is important. Blunt points are less likely to split wood. Diamond-shaped points are the most common and in some applications, the point is made longer than normal. Experienced carpenters may blunt a nail’s point a little by hitting it with a hammer to reduce the chance of splitting the wood.
Size is one place where the terminology isn’t as easy to figure out. In most of the world, nails go by a metric size. But not in the United States. Here, we use a system based on an obsolete English measure. Nails are sold in “penny” sizes that vary based on the type of nail to some degree. A 10 penny nail, for example, is 3 inches long, but the diameter of the shaft and head depend on the type of nail. Most of the rest of the world uses a length and diameter in millimeters.
You often see “10 penny” written as 10d, by the way, where the d stands for denarius, which was an old Roman coin like a penny. Odd, yes, and maybe that’s why everyone else went metric.
History
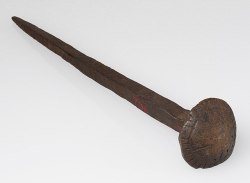
As you might expect, nails are ancient technology. Even the ancient Romans used nails and even invented the claw hammer. From at least that time to the 1800s, people formed nails from iron or bronze by hand — apparently, the ancient Egyptians used wooden pegs instead. Blacksmiths made nails as did nailors. You start with a heated square iron rod and hammered the sides to form a point. After reheating and cutting off, you put the hot nail into a hole in an anvil to hold it and hammered out the head. The resulting nail has a decidedly square shank, unlike the typical round shank you’ll find today.
Nails were hard to produce and, thus, expensive. This was particularly true in far-flung areas like colonial America. There, people would sometimes burn down an abandoned house — even if they were the ones abandoning it — to recover the nails from the ashes. Large structures often didn’t use metal nails but used carefully fitted wooden parts secured with wooden pegs.
Because nails were valuable, families sometimes had the requisite equipment in their homes or farms. When they had time — often at night or in bad weather — they would produce nails for their own use or to trade with others. Apparently, even Thomas Jefferson was known to make and sell nails, sadly, using enslaved farm labor.
Of course, making a nail in the year 1033 was a lot different than in 1733. Some equipment — particularly slitting mills — made the production of nails easier, even though it was still labor-intensive.
However, throughout the 1700s, several people created machines to cut nails directly from iron sheets. These cut nails were cheaper, although wrought nails were still harder and used in things like horseshoes for quite some time. However, cut nails did push out wooden pegs in framing construction and there are still a few niche uses for them today.
In the 1800s, though, a new way of making nails started to become popular and it is used today for most nails you’ll encounter. Using the same process used to form wire, lengths of wire were cut and formed directly into nails. A blade cuts the point and a pressure process forms the head. In 1892, more steel-wire nails were produced in the U. S. than cut nails. By 1913, 90% of all nails were wire nails. Finally, nails were a cheap commodity item you wouldn’t burn a house down to recover.
Modern nail machines, like the one in the video below, can create a tremendous number of nails in a short period of time. No wonder nails are cheap.
As a side note, woodworking in ancient Asia used a fascinating but nail-free technique. That region had advanced metallurgy, of course, but they didn’t really need nails.
Common Nails
Actually, there is a specific type of nail known as a common nail, and it is, of course, what you commonly find. These nails have heavy smooth shanks and a wide head. The point is shaped like a diamond. These are great for many purposes. Framing nails are similar but have thinner shanks. Joist hanger nails use hard materials and have ridges along the shank to increase their holding power. Siding nails are also common and usually have thicker shanks for hammering through hardwood.
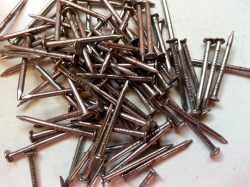
Smaller nails are often known as brads or finishing nails. Both are usually very skinny both to be unobtrusive and to avoid splitting delicate material. Brads typically have a small head and finishing nails are beefier but have heads made to be unobtrusive. In some cases like model shipbuilding, small nails are little more than sharpened wire that you drive in with a nail driver.
Roofing nails tend to have very large heads to prevent roofing sheets from tearing. They also use materials that will be resistant to the weather. Some roofing nails also include a washer to help seal the roof against a leak at the nail hole.
Nails that are meant to go into softer materials like drywall tend to have a pattern of ridges or barbs on the shank or some other method to make the shank grip the material better. Weatherstripping nails have the same arrangement but are usually made of very weather-resistant material. You’ll also find ridges in nails meant to hold panels and some other types of nails.
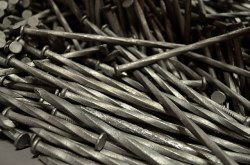
You’ll occasionally see nails with a twisted shank. This makes it harder to bend the nail and will cause the nail to thread into hardwood. Spiral shank nails and flooring nails have shanks like this as do some other specialty nails.
There are yet more specialty nails. Upholstery nails that have large decorative heads. Nails for shoes. Tacks that also have large heads, some for carpet. There are nails with T-shaped heads and nails optimized for concrete.
Then there are the strange nails. There are still places where cut nails are used for decorative or restoration reasons. Cut nails also find use in masonry where they are made out of very strong materials and have a tapered shank to help reduce spalling — that is, chipping away at the concrete surface.
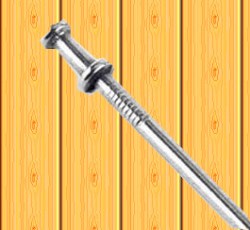
One of my favorite nails is the duplex nail that you use when you are building something temporary like a scaffold or a concrete form. The nail has a normal head but also another head a small distance down the shank. When you are building something you know you’ll take apart later, you hammer down to the lower head and the rest of the shank sticks out waiting for you to pull it out when the time to disassemble comes.
Materials and Coatings
Adding to the complexity of the humble nail is the material it is made from. There are hot-dipped galvanized nails and stainless steel nails. Some nails are made of materials like brass or copper. Some are coated with “cement” — meaning a glue — for holding power. Some nails even have a coating that melts from the hammering friction to glue into the wood.
Of course, steel isn’t just one material. Some nails are made of relatively mild steel and others use harder steel with higher carbon content. It all depends. Mild steel is fine for wood, but nails meant for concrete are likely to use stronger materials.
Or, Get Screwed
Of course, you could use screws instead of nails. When I was a kid, people didn’t like screws in wood because it was faster to hammer in a nail, but screwdrivers were slow. With power screwdrivers, this isn’t a big deal anymore, but I guess nail guns are even faster. The video below covers a lot of good information about screws versus nails.
There was a day when nails were a common part of circuit breadboard and you used a real bread board. Now, we are more likely to see them in a very different context.
You’ll need a Hilti gun for those concrete nails.
Thanks for “the rest of the story” on these ubiquitous fasteners.
You didn’t describe the two-pointed nail, though. I have seen two types: One is small, and looks like a thumbtack with a point on each side of the head. You place them between two boards that you want to join with a dowel. Tap the boards together, and pull them apart. The points leave pilot marks to drill for the dowels.
The other type is a longer nail with a head in the middle. It’s used for an invisible joint between two boards. You pound it into one board with a hollow tool like a nutdriver. Then pound the second board onto the exposed end.
Then there are nail plates. These are pieces of sheet metal with many stamped slots that are formed into nail points. They are typically pressed into the the wood by a big hydraulic press, and used to make roof trusses etc.
I actually learned about duplex nails while watching Better Call Saul. Mike is making a concrete form with them in a flashback and I had to look them up. But what I found is there are tons of specialty nails out there so I had to pick some and lose some others.
And of course the two pointed nail with a bend in the middle is the staple of any fencing job.
I’ve helped my dad make two pointed nails by hammering a normal nail halfway into a plank, then snipping the head off and then using a file to quickly turn it into a point.
I can’t remember why we were doing it though.
Wire nails don’t hold into wood all that well. That’s why they have rings and twists available.
Cut nails need to have the long side with the grain to prevent splitting. A pilot hole is usually needed. They are hard to extract.
Blacksmith square nails hold extremely well. It might be easier to burn the wood than pull them out! :-)
Most nails can bend. Screws are harder & more likely to snap. Wood moves with humidity and the give of the nail can deal with it which is why framers use nails in houses.
There are screws that you can put in a nail gun to put them in, then take out w/ a screw gun.
I’d always wondered why nails were still the go-to for things like framing. Thanks for clearing that up!
I can attest to square blacksmithed nails holding really well- I forged my first nails a couple years ago, and just 4 about 1″ long, about 1/8″ at tip tapering to 3/16″ under the head hold up about 30lbs of decorative iron on my livingroom wall.
Nails take some practice, but are actually pretty straightforward to make. You need a tool called a nail header though- it’s a hardened shallow steel cup, with a square hole cut into the middle, with a slight negative taper to the hole, so the forged nail can drop through, and the underside of the nail head can be made slightly concave and form out, so it goes flush when you hammer the nail into something, but you can still get it out of the tool because of the negative taper to the square hole.
I’d always wondered about the history of nails.
And then there are plastic nails (resin + fiberglass?)
They don’t rust, have nearly the same color as wood and they don’t damage tools such as circular saws or planers.
Use the magic words “Composite Nailer” to find them
or CNC bits
Have you notices that the sound of a construction site has changed over the years from the tap tap tap of hammers …to the shick’ish sound of air tools.
Yep, and because of modern air and battery powered tools framers and roofers don’t suffer the joint impact injuries they used to have to live with.
it’s possible to install a drywall screw into wood with a hammer
i finally used masonry nails, putting a line of them into a concrete floor. used a heavy hammer but i still bent about half of them instead of driving them in. crazy that it works at all!
In the Antarctic many decades ago the Navy CBs (ConstructionBattalion) drove screws in with a hammer. Said they held better than nails. No one was worried about ever removing them as everything was “temporary” even when it was used/occupied for decades.
Great article on nails. Well researched AND well written. Thanks for creating the piece. I never thought about how nails differ and why, but it’s all clear now.
As a kid my favorite use for double headed nails was a shiny steel sword for my action figures.
I got a pin nailer that can drive a tiny thin headless pin into 2″ of hardwood with no problem. Considering how small the diameter of a 23g pin is, and no head, the holding power is shockingly good. I think the tip is chisel shaped like a flat screwdriver and cuts the wood fibers so they sort of lock up against the pin instead of just getting pushed aside.
Also, spent the money for a chain-fed screwdriver gun when re-flooring the house. Fantastic investment. Next job, installing a new back fence, will be with screws.
Loved the article thank you