[Martin Roberts] wrote to us, telling us about a build that his company, [Ocean View Workshop], was tasked with. Creating a four meter wide window able to open vertically is no small feat, and it had to be custom-built because the local company building such windows wasn’t comfortable working with anything other than aluminum — insufficient for the window’s scale. With massive weight of the glass alone, structural requirements for supporting it, and the mechanical loads to be applied, some careful planning was in order.
To start with, this window had to be motorized, as an average person wouldn’t be capable of pulling it upwards. Not satisfied with the linear actuator choice available, they went to a hardware store and found some swing gate actuators that, in workshop tests, proved themselves to be more than capable of handling way over the weight required. In fact, they were capable of lifting [Martin] himself off the ground without much hassle.
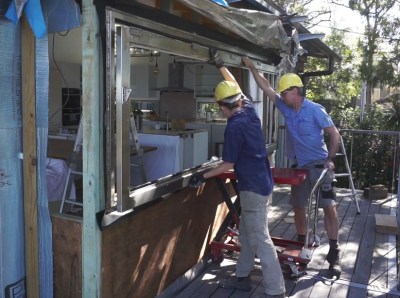
From there, it was time to figure out the mechanical parts — building a strong enough frame for the window, welding the frame, figuring out the mounting and leverage intricacies, gauging the loads to be handled and adding gas struts. The nitty-gritty of the mechanical bit is covered quite well in the 14-minute video that [Ocean View Workshop] published, embedded below, so we won’t repeat it. Instead, our focus is on the swing gate-intended hardware reuse part that [Martin] shared with us in his letter.
The swing gate controller’s built-in features, like adjustable limit switch support, soft start/stop and configurable overload/stall protection, proved themselves to be instrumental for smoothness and safety of the window’s operation. As for the automation part of it, they interfaced the motor controller with one of the numerous Sonoff devices tied into a Home Assistant-based system, and then even integrated it with Amazon Alexa, adding a 2001: A Space Odyssey Easter egg while at it. In other words, the motorized swing gate hardware and this servery window build turned out to be a perfect match for each other.
We appreciate the ingenuity and hope that the spirit of this story can guide other hackers in similar situations, tasked with building things beyond the scope of what local companies have the toolkit for. [Martin] says he already can think of a few more unintended applications for these – an extra heavy-duty adjustable workbench or a height-adjustable king bed. Limiting availability of linear actuators is somewhat of a pain point, to the point where people build and even 3D print their own, for loads big and small.
While it’s nice to see people wearing helmets, the words “engineering”, “safety” and “code” (standard) are not mentioned in the article – what’s to keep peoples head getting bashed in?
Just don’t make any disparaging remarks within earshot, and you’ll probably be fine.
What makes american bay windows from getting peoples heads bashed in? What makes cars rear hatches from chopping necks or hands off?
Please don’t search danger where there is none^H^H^Heglegible, to invent safety measures that do not prevent any percievable risk.
Vertical sliding windows are normally counterbalanced so the actuator isn’t holding most of the weight and windows with broken counterweights have been known to claim victims. Same with car rear hatches, there’s been plenty of injuries from those once the gas struts start going (or one of the ball joints breaks off), but they’re typically not that heavy.
The construction of this window has a LOT of weakpoints and failure of any number of them (or a combination of unnoticed defects) could easily lead to this heavy window coming crashing down. There’s a reason engineers are trained to perceive risk and invent safety measures. Oftentimes you need it.
a simple safety hook once it is deployed is the easiest thing i can think to prevent this. i usually use compression latches for such things.
I’ve got some 60/70s era double-pane vertical windows with broken supports. They are a bit heavy and could easily take a finger off.
Failure was a major consideration in the design of the window and why there are 2 rams and 2 gas struts. This provides 4 independent paths of load support for the window. To fail both rams and both gas struts would have to fail.
One of the nice things about hydraulic actuators is the ability to put a flow restriction on the outflow and a check valve on the inflow.
Unless the cylinder itself fails, the thing can only drop _slowly_. e.g. Old school hydraulic car lifts.
high wind forces could easily rip that window off. i’d put chains you can easily attach to the wood frame with huge lag screws. so if the wind did sheer it off, it might not become a hazard outside the immediate area. I just went to a particularly windy beach the other day and all sorts of things could be seen careening down the beach. luckily nobody lost control of a beach umbrella, ie, a wind spear. 😁
The window is fabricated out of 3mm thick 316 stainless steel. It is far stronger than the professional windows I have seen made from aluminium profiles. Its also attached with 5 heavy duty stainless steel hinges via M6 nutserts. Professional windows typiclly use plastic hinges with self tappers as thats far cheaper. On windy days this window is rock solid.
the hinges were what I was thinking may be a weak point IF anyone was concerned. by the nature of the sleeve bearing a hinge employs, allows for play, which over time in heavy wind conditions could potentially weaken or work the screws loose. I honestly wouldn’t be worried about it. it’s more likely that the glass become shattered and turn into laceration projectiles.
I regularly pick things out of the trash. last pick was a old hospital bed. i stripped the steel and hacked it up to fabricate a mount for my generator onto my bus, the motors and gearboxes still function. 3 of them at 24v, two have shafts. one attaches to the foot and has a lead screw and series of pullies to raise the legs. not sure what im going to use them for as they are high torque and low speed. maybe i can use them for solar panel tracking or some such. i also regularly pick up old power wheels or other electric vehicles for kids that still have perfectly good motors and gear boxes.
also if anyone has a good place i can pick up 24v lithium cells with a charger that would be safe for a 250w electric kids bike, hook me up.
In regards to your question about batteries, I would use a tool battery that can sustain the output. For example, a Milwaukee 6Ah 18v battery can put out roughly 360 watts according to math I’ve seen online. You can use a cheap boost converterto raise it to 24v and buy an aftermarket battery sled so you can just *click* the battery into the bike. You would also use the tool battery’s charger, which would vastly simplify this solution.
I’m just amazed that they managed to source something useful from Bunnings. (other than the obligatory sausage sandwich)
One clever thing somewhat buried in the explanation is how the tails of the two actuators are connected together in a sliding mechanism rather than statically fixed to the joist. This ensures that the force applied to the two sides is always perfectly balanced, even if the two actuators themselves are not.
Yes, that was critical to the smooth opening of the window as the ram speeds are slightly different. Also there a small variations in the length of the leavers and pivot points which have impact. It slides about 10mm when the window opens and closes.
Heavy steel window frame, but whole house structure from wood. Does load bearing beams are from uncooked pasta?
Ok, after seeing whole video, I have to admit – it is some nice fricking window!
RIP those handles if the window actuator can be activated when they are locked in…
“The swing gate controller’s built-in features, like adjustable limit switch support, soft start/stop and configurable overload/stall protection, proved themselves to be instrumental for smoothness and safety of the window’s operation.”
not sure but i suspect that’s one of the anticipated failure modes that has been corrected for
Not sure if the force required to damage the handles is more or less the force required to lift the window.
Nope, the rams trip out on overload if they are locked.
What is not shown in the video is there is variable amount of load applied to the window as it opens because the leavers operate over their 90 deg range. As you imagine when a lever is close to top dead centre there is much lower torque applied than at 90 deg. When the window is just opening the rams have the weakest push to open so the locks easly stall them and also prevent any pinch injuries on closing. Maximum torque is applied when the window is fully open to hold up the weight.
I’m with the people asking for engineering sign off and backup safety features. At least a hardware lock.
Source: the load balance cable fell out of my overhead truck lift at work one day. At least it had the safety locks.
Moving the window upward is one thing, good find. Disassembling it to double check it is constructed for overhead duty and adding safety locks is another.
Does it have plastic, nylon or composite in the screw or gear mechanism? Will it work great until it doesn’t, failing spectacularly?
Counterbalance is something that should be designed in as well.
Agreed.
That looks like a guillotine.
Failure was a major consideration in the design of the window and why there are 2 rams and 2 gas struts. This provides 4 independent paths of load support for the window. To fail both rams and both gas struts would have to fail. There are also buffer springs and rubber pads for the final closing of the window.
They contacted only one glazier? For a job this size they certainly should have worked with a professional. I would bet money there is at least one major flaw in this custom solution.
If it fails and injures anyone, even an employee then they will have a big lawsuit on their hands. It wasn’t installed by a professional, it doesn’t look like much consideration was taken for how it could fail and what would happen when it fails, it probably isn’t up to building regulations, etc. A lawyer would have a great time with something like this. It might not even be within electrical regulations if it wasn’t installed by a professional.
We had several meetings with 2 different glazier on the design of this window. Once we selected our preferred glazer we built one of the small side windows as a prototype and got this glazed to their requirements. Only once we we both satisfied with this design did we proceed to build the full size window, which the glazer inspected to measure up for final glass fitting.
Birds and wasps will love those slots into the inside space. I’d have a pocket window drop into the wall to open. Screw it up with chain drive to both ends.
Was the middle of the original twin windows a load bearing column?
They are too small for birds but there will be and issue with wasps. One of the slots has a prototype door, which has rubber seals which closes to keep the out. I need to make a few adjustments to the design and fit another door to the other slot.
The middle column was not load bearing. The rafters are supported by a bean 600mm inside and they overhang to the top of the window.
I wonder why a hand operated counterbalanced design wasn’t considered, perhaps even with a flywheel damper, that would be more likely to last a long time and require less maintenance. Combining the mass of the counterweight with the mass needed for the flywheel would be very cool. You have the end stops work by disengaging the flywheel drive chain, that clutch could even be used to hold the window at any angle.
I saw quite a few negative comments but I thought all in all a very well done job with great video. I’m sure you knew ahead of time without explicitly mentioning things like design reviews and specifically mentioning safety you were going to catch grief.
Thanks for the positive feedback. Yes you can get grief from the safely police, but I don’t want to make videos too long and boring by including all the details.
However I get a lot of good ideas from articles on Hackaday and also learn a lot from constructive comments. If one person can learn from this hack then it’s all good. Looks like 2 people are going to use my Hot Water Heat Pump hack from 2 weeks ago:
https://hackaday.com/2022/03/25/custom-controller-ups-heat-pump-efficiency/
So a “Servery Window” is a real thing? Maybe…
https://duckduckgo.com/?t=ffab&q=Servery+Window
Who’da thunk it?