It started with [CHORL] making a promise to himself regarding constructing a new combat robot: no spending of money on the new robot.
That rule was violated (but only a little) by making his robot’s wheels out of EVA kneeling pads. EVA (Ethylene-Vinyl Acetate) is a closed-cell foam that makes for durable yoga mats, kneeling pads, and products of a similar nature. [CHORL] found a way to turn them into light but serviceable wheels for his robot: the Susquehanna Boxcar.
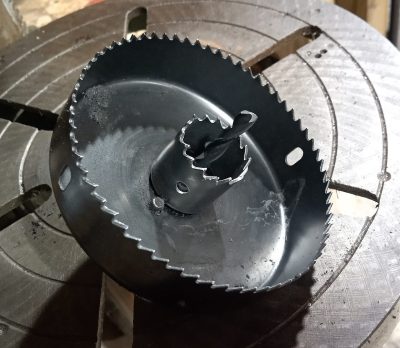
Here’s how the wheels were made: [CHORL] began with two hole saws. Nesting a smaller hole saw into a larger one by putting both on the same arbor created a saw with two holes, both of which were centered with respect to one another. The only problem was that this hole saw was not actually deep enough to cut completely through the thick foam. Luckily, cutting roughly halfway through on one side, then flipping the sheet over and cutting through from the other side was a good workaround. That took care of turning the thick foam sheet into round wheels.
A 3D-printed part served as a wheel hub as well as gear for the drivetrain. We want to call attention to the clever method of reinforcing the connection between the parts. [CHORL] didn’t want to just glue the geared hub directly to the surface of the foam wheel, because he suspected it might separate under stress. To address this, he designed six slots into the hub, cut matching slots into the foam wheel, and inserted six spline-like reinforcements in the form of some ABS strips he had on hand. Gluing it all together with E-6000 and leaving it to cure overnight under a weight resulted in a geared wheel assembly that [CHORL] judged to be about as round and rigid as a wheel should be, so the robot had a solution for nice light wheels that were, above all, cheap!
Lots of robots need wheels, and unsurprisingly, DIY solutions are common projects. [CHORL]’s approach here looks pretty scalable, as long as one can cut some accurate holes.
Interested in knowing more about the robot these wheels are destined for? [CHORL]’s still working on the Susquehanna Boxcar, but it’s almost done, and you can read a bit more about it (and see a few more pictures) here.
Oh there are a lot of clever ideas here. Thanks for sharing this one!
neat. and the lists report EVA is just fine to cut a CO2 laser too. thickness might be an issue, but maybe laminate a few thin layers with more E-6000
If you’re layering, could add multiple plies of that rip stop nylon weave, which will pull out and tangle on a saw blade, if such implements are allowed as offensive weapons in this series.
Just a month ago I used two hole saw blades together (the circular spring steel ones that hook into an annular slotted aluminium base) in a drill press to zap out about three dozen rings from a scrap of 5mm HDPE sheet.
I split the rings and clipped them onto the gas strut column of an IKEA office chair that had started to slowly drop. This fixed the problem but I was a bit annoyed as the chair is only a couple years old.
FWIW, replacement struts are cheap, readily available, and (usually) easy to replace (sometimes the old one is especially tight and hard to remove).
I guess so, but for what country do you define ‘cheap and readily available’ though.
It was an easy bodge, but I retract the word ‘fix’ I used above because it no longer becomes easily adjustable, short of grabbing the ring with pliers and yanking them out of the stack.
Oh hey it me
I was just thinking that if one wanted to make cheapy wheels, that were maybe a bit more durable for mileage, one could modify that tape plotter in the previous article, to draw on a tread pattern with silicone or similar.
I own exactly that foam in the form of (unused) floor padding for work areas, hole saws, a 3D printer and even E6000 adhesive and this has given me the idea of what to use for a cheap friction drive for a lightweight mini-Dobson mount using a bipolar modified 28BYJ-48 stepper motors.
Though if you want a little less slippy cheap drive, you might look at the possibility of expedient toothed wheels made from jar and bottle lids… you can match the serrations such that one seems to engage another well. Not sure if you’re gonna find one bigger than 4″ that easily though.
I’ve got one of those ball ended scopes though, maybe friction drive onto the shell of that would be the only way to point it without major mods.
Just thinking, biggest plastic jar lid I’ve seen with serrations might be those huge jars of cheese puffs or popcorn… kinda stupid packaging for them, but hey, big lid. Also if you know any gym bros might wanna look at protein shake containers.