In France during the mid-to-late 1800s, one could go into François Willème’s studio, sit for a photo session consisting of 24 cameras arranged in a circle around the subject, and in a matter of days obtain a photosculpture. A photosculpture was essentially a sculpture representing, with a high degree of exactitude, the photographed subject. The kicker was that it was both much faster and far cheaper than traditional sculpting, and the process was remarkably similar in principle to 3D scanning. Not bad for well over a century ago.
This article takes a look at François’ method for using the technology and materials of the time to create 3D reproductions of photographed subjects. The article draws a connection between photosculpture and 3D printing, but we think the commonality with 3D scanning is much clearer.
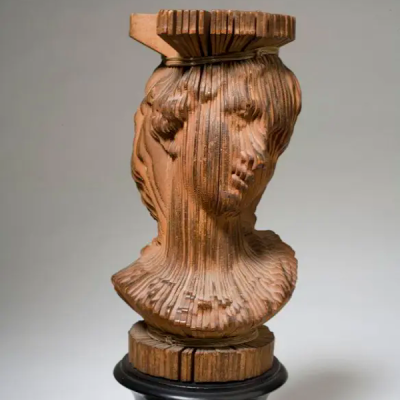
Here is how it worked: François would take multiple photos of the subject, each from a different (but regular) angle. For example, a subject could pose in the center of a large room and be photographed by a surrounding ring of cameras, each showing the subject from a different angle.
Then, one at a time, the photos would be traced with a pantograph. At this stage, only the profile of the subject was of interest. Each profile was then cut from thin slices of wood, and these wood slices were then assembled into a radial pattern matching the positions from which the original photos were taken. That probably sounds a bit confusing, but the image shown here should make clear what was happening.
Once the wood model was finished, more traditional methods took over. Clay and other materials provided gap-filling, and details were added by hand as necessary, again with a pantograph, using photos as reference. But the bulk of the work could be done by persons of modest skill, and the process took only a few days.
The central concept — that a 3D figure can be adequately represented by a series of structured 2D representations — is remarkably similar in principle to laser-line 3D scanning (and shares the drawback that not all details can be captured by stacking profiles.) Fittingly, a 3D scan of one of François Willème’s self-portrait photosculptures is available online.
If you think finding the roots of 3D scanning in 1800s technology is neat, hold onto your hats, because we covered how the 1800s actually had everything one would need to create a laser.
[images: The Patrick Montgomery Collection]
Looking at the nose and mouth of the unfinished sculpture, I think it would take more than modest skill levels to spackle those gaps.
This is the state of the sculpture after those moderate skill workers are finished. This is the “bulk” of the work as mentioned.
This is true, but the sculptor would have had the original photographs to work from for details. Perhaps more than “modest” skill levels, but nowhere near what it would take without the technological shortcuts. I would expect that in the shop, an apprentice could be tasked with assembling the wood flats and performing this “spackling” step, leaving a much reduced amount of work to be done by a semi-skilled sculptor.
In that era, an artisan of modest skill would equate to, today, highly skilled, specialized, rare and of course expensive. It wasn’t Michelangelo that carved all the stone for cathedrals and stuff. It was some average joe-schmoe. But try finding someone to hand carve stone (or wood or anything really) today and you will be paying through the nose.
That’s one thing that I think about from time to time… Norman Architecture, where did all the stonemasons suddenly come from? Anglo-Saxons were building in wood frame. I mean a couple of crews could have done the more significant buildings, but there must have been many dozens to put up what’s still standing, and there’s probably a hell of a lot more that got pulled down. (Barons wars, Dissolution of Monasterys, Civil War etc)
Right. Today, all we would see were the most robust constructions. I’m sure there were many low-budget stone buildings that didn’t age so well.
Yeah, I was about to say. Very few people understand what “craftsman” meant in those days.
Sure we do!
It’s a mediocre line of tools made in China.
This is why the assembled radial slice method of photosculpture was abandoned in favor of the subtractive method shown in the first youtube video of the source article. https://youtu.be/jS_rcwG9mxU?t=31
Yes, but that film was made in 1939, and the technology was much further advanced by then. Which is to be expected since the original process was introduced 78 years earlier.
mmhmm, time happens. Have anything of use to contribute or just compelled to shit post?
It was a comment on the implication that the original studio abandoned this technique for a better one. But 78 years is significant. Why not just say, “this was later abandoned by using DSLRs with shutters timed to trigger at specific intervals, which also allowed for a trucking-during-ultra-slow-mo effect”, if elapsed time is insignificant?
You mean….
Why not shit post as you are so compelled?
Had I intended to muddy the post, I could have dumped a hundred and fifty years of patent citations. I dont work for HAD, not my job.
I merely referenced a video included in the articles link, at a moment in an included video relevant to discussion, as so many HAD readers comment without bothering with the jump, let alone the youtubes within. So sorry if you cant comprehend the difference between a comment intended to enhance discussion by drawing focus to information easily missed, and your “contributions” DimJim, Enjoy your Bliss!
I don’t understand all the controversy. I was not “shit posting” anything. I was pointing out that doing this in the 1860s was far more impressive than the improvements to the process made in the 1930s, which I felt was relevant. I also found your comment to be relevant and useful, and did not intend my comment to be taken personally, so sorry for any misunderstanding there. As for [makes you go hmmmm….]’s comment, it added nothing at all to the discussion, so they can take it any way they want.
Gobsmacked. Just wow.
I have a vinyl album from the late 1950’s that was the
hard copy of an early live streamed concert,availible
through a high fidelity phone service.
Liner notes baby,some odd and interesting stuff
Indeed!History is interesting and always good fir a surprise!
Turns out that the prototypes* from the distant past had higher quality audio than what we know from our modern smartphones or those 20th century rotary phones with their muffled carbon mikes (speakers were fine). 😎👍
*There were different pioneers, not just Mr. Graham Bell.
Such as Antonio Santi Giuseppe Meucci or Philip Reis.
https://en.wikipedia.org/wiki/Invention_of_the_telephone
20th century engineering was all about making things better than necessary, so nobody would complain. For example, GSM phones sounded better than NMT phones not because they needed to, but because it was nicer.
21st century engineering is all about making things worse without anyone noticing the change. It’s supposed to be optimizing, but as the public accepts and gets used to the new reduced version (at the same price of course), the expectation and perception of what is bad, average and good, also drops. The bar for what the average person will accept goes down and a new round of optimization makes it worse.
Examples: plastic power tools, cellphones with atrocious battery life, laggy bluetooth headphones, High resolution “HD” television that stutters with each key frame, WebP instead of JPEG…
Sad but true, Dude. For me this started when I read about iphones and “tethering.” What the hell was tethering? Oh right, using a mobile phone as a modem… Like the GSM standard has allowed ever since it was invented! Fuck you, Apple. See also, mobile devices not working as a USB mass storage device, non-replaceable batteries, deletion of removable storage, non-socketed memory, removal of headphone jacks… I used to love technology. I still make my living from technology. Unfortunately, most new consumer devices make technology worse.
Speaking of which, I’m still trying to dig up deets about a 3 dimensional RADAR mapping display from the 1950s/60s… all I got to go on is a dim memory of a magazine picture.
Incredible and what an interesting story. It perhaps bears a passing resemblance to the effect in ‘The Matrix’ referred to as ‘Bullet Time’ and I looked to see if François Willème was mentioned there, alongside Muybridge et al., but sadly seems he and his technique were consigned to the dustbin of history.
https://en.wikipedia.org/wiki/Bullet_time
Imagine if this technique was applied to say, the frames of an HD video, passing around a subject, with the slices cut out of vinyl on a laser cutter. I wonder how it would compare to 3D printing if you were to add up time and cost, verses accuracy, depending on scale, it might be cheaper, discounting the manual assembly time and time changing sheets of material, for an automated industrial process.
@CRJEEA
Since it has to be assembled in a radial pattern, with each slice pointing to a central axis, it would require a stiff material and vinyl would not cut it.
Notice the little pun there :)
I wonder if there is a way to have a material that is ablated to a specific depth by a modulated laser so that method from [random noise from the abyss….]’s video link could be done that way.
I know you have 3D printers with liquid/UV, but that’s so messy – and uses flat slices.
There must be some such material that is more solid surely.
I suppose you could also use a ‘normal’ material and combine a dozen low power cutting lasers and create a focus point as a way to ablate with variable depth. You’d have to precisely aim them all though and it would require a clever mechanical setup. But since all those lasers would have to tilt at the same angle to adjust the depth you would not need all that many actuators and you’d just interlock them and use a single actuator for depth adjustment, and if you rotate the target as in that video the whole assembly could remain stationary, thus keeping cost in check somewhat.