[PjotrStrog]’s rugged Pinecil / TS100 storage case is the perfect printable accessory to go with a hacker’s choice of either the Pine64 Pinecil, or the Miniware TS100 soldering irons. There are some thoughtful features beyond just storing the iron, too!
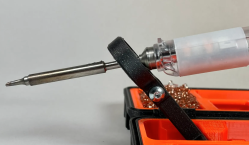
Some of you may have spotted a 608 bearing in the image above, and might be wondering what it is for. In proud hacker tradition of using things for something other than their intended purpose, the bearing makes a heat-resistant stand to hold the iron while in use.
This design has a pretty deep history that illustrates the value of sharing one’s designs and allowing others to remix and refine ideas. [PjotrStrog]’s work makes use of the earlier and highly thoughtful TS100, Pinecil, TS80 & TS80p cases with options by [Termiman], which themselves are based on bearing-equipped TS100 case by [Olvin] that we covered back in 2020.
We loved the Pine64 Pinecil soldering iron, and this looks like a fantastic printable storage and carry option. There are a few pieces of hardware needed to put the rugged version together, but [PjotrStrog] also offers a less rugged design with fewer hardware needs, so check that out as well.
It’s funny, I’m always getting yelled at by the EEs for using their (or my) soldering iron to put heat thread inserts into 3d printed prototypes and how that’s not what a soldering iron is for. Now I get to say that’s not what that’s for in an ironically exactly opposite way. Carry on my friend in arms, I will keep using things as they shouldn’t be, you should too.
I think what they really mean is, “don’t contaminate my favorite tip”
“Favorite tip” is an outdated concept, since unleaded solder dissolves copper like crazy. You could file your tips down to a point and use them for years, but now once you do that and break the coating, it just vanishes. The higher temperature and the composition of the alloy is like dipping your iron in acid.
I always treated filing down the tip as the last resort, flux destroys the tips anyway once you break the coating (maybe not in a “the tip dissolves” kind of way, but still).
Not all flux is that aggressive, especially no-clean flux.
The lead-free solder has a habit of eating thin copper traces off the boards as well.
>This design has a pretty deep history that illustrates the value of sharing one’s designs and allowing others to remix and refine ideas.
I said it the last time, and I say it again: “people will fixate to a known solution rather than a better solution that is more readily available. ” The 608 bearing isn’t even a good heat break, it’s relatively expensive to obtain especially in single units, and it’s packed full of grease that will drip out if it ever actually gets hot. A pair of large washers or pieces of a tin can lid would work better, yet everyone copies this design.
The first guy might have used it because they literally had one in hand and went “That’ll do”. The next person thinks, “Oh, that’s a necessary part.”, and then subsequent people go to troubles rationalizing why since it doesn’t make any immediate or obvious sense. The more people do it, the more people think there MUST be some very good reason why it is specified, so they keep on copying a design that doesn’t actually make sense.
That’s how you do cargo-cult design and engineering. Whether that illustrates the value of sharing one’s designs…
When making things out of other people’s plans, every maker should be aware that there are a bunch of helpful people out there, who are actually building what the Japanese call “Chindōgu”. That translates into “weird tool”. It’s a device that seemingly works to solve a problem, but actually introduces other issues that make it practically useless or downright stupid.
Jokes aside, the same people go on to make long shopping lists of parts available on Asian webstores, which are “needed” to replicate the design. They will sell you the 608 bearing for $7 plus postage. These plans and instructions exist to drum up sales of overpriced items, catching newbies with lesser experience who are brought to believe that they absolutely need a ceramic ball bearing to hold a soldering iron.
>proud hacker tradition of using things for something other than their intended purpose
When copying designs and re-publishing them to other people, one has a responsibility to weed out the bad designs that perpetuate bad practices and bad ideas, because most people will just copy it without question. To rebrand the neglect as “tradition” is irresponsible.
You might be right here, but I think a bearing could be a reasonable heat break. I’d just use an unsealed one or pop of the seal and wash out any grease before using it.
It does its job, since the soldering iron is not actually all that hot at that place.
Good point
I suspect your pair of large washers wouldn’t have enough surface area to shed the heat, or enough thermal mass, at least for the longer soldering session with the usual 3d printing filament choices. Though i don’t have hands on with that iron family so you may be right in how little is needed – still using a really old bench top controlled unit myself, as it still works, and inconvenient as it is its not worth paying money to fix (yet).
Removing the grease if it is a problem isn’t hard either, though I suspect it won’t actually get hot enough to be a problem I’d remove it anyway if I was reusing a bearing this way, and as its a common bearing you shouldn’t have to source a new one, or even pay for one really – find yourself a skate park and ask the serious skater for one of their worn bearing (etc). Also this bearing is easy to mount and thick enough to do the job with one part, which is a nice thing for design simplicity.
I do agree its not how I would do it, and there can be better ways out there. But that is partly because I have different scraps available that would do the job as well or better – some nice thickness of offcut Aluminium plate I could just drill the hole in for instance.
Use similarly sized washers, have the same exposed outer area. Boom – problem solved.
I should have also added that people will also try to find special cases and circumstances to force the point. Yet, surely a pair of washers is still both quicker and cheaper than going out of your way to beg for used bearings? I can confidently say I can produce a pair of flat metal discs with a hole in the middle in about fifteen minutes right now, right here, using zero money. That’s because I know I have at least a pair of scissors and some old cookie tin somewhere.
The irony is that makers don’t know how to make stuff anymore because they’ve been relying on 3D printers, laser cutters, and store-bought components to achieve the desired fit and finish.
The bearing with all the balls and inner bearing surfaces have a most likely greater surface area than any washer of a reasonable diameter for such a case, and certainly a heap more buffer mass and thermal resistance between the soldering iron and the plastic than your cut up tin can. As a drop in replacement you are going to need lots of airflow over it the second you introduce the iron I’d think – at least with this design as it requires passing the very very hot end through the holder, so even that little rub on the way to seated is going to dump plenty of heat into that really quite thin metal sheet – enough to be a problem to the most likely very very soft even at a paltry 60c and mostly hollow plastic part that then has to carry all the weight and leverage of the iron and cable.
And with how common those bearing are I doubt most of us would have to go out of our way to get a used one, and if you do it is really not going to be hard to source. Which for a design mean to be replicated is ideal.
>The irony is that makers don’t know how to make stuff anymore…
Not really any tool can supplant previous ways of doing stuff, doesn’t mean the maker couldn’t use other older methods. – who wants to jigsaw or hand saw that acrylic that is going to decide to shatter at least once when you can laser cut it – you could, and then go at it with sandpaper and files for the perfect size and finish… Or let the tool do the work…
> and inner bearing surfaces have a most likely greater surface area
True, but not exposed to the outside where they can shed the heat.
>certainly a heap more buffer mass
Negligible difference. A few seconds more to saturate it with heat.
>and thermal resistance between the soldering iron and the plastic
More material = lower thermal resistance overall.
> that little rub on the way to seated is going to dump plenty of heat into that really quite thin metal
Not really.
Like I said, you’re going to great lengths to rationalize why something that is worse must be better through insufficient knowledge of how these things work. You’re just proving my point here.
>doesn’t mean the maker couldn’t use other older methods
It’s not about couldn’t. It’s about wouldn’t, because they have no experience and practice with it, so they don’t even know they can do it. It’s just not an option that comes to mind. I see this every day with people who look at, say, taking an x-acto knife to a circuit board to break off a piece of solder stuck between traces. They say, “I didn’t know you can do that!”. People with no experience seem to develop strange ideas and superstitions about stuff like that.
What I’m trying to say is, there’s this mental barrier because people don’t like to “step in the dark”, so to speak.
If you’ve never taken a hacksaw to a piece of metal, the uncertainty and not being able to imagine the process and the outcome means that a) you don’t think about it as an option when you’re planning your actions, b) when presented with the option, it appears as an insurmountable obstacle with many difficulties because you’re unsure how it will turn out. But, once you’ve done it and figured out how to saw a piece of metal neatly in half, it’s easy, it’s so easy you don’t even understand what the problem was before.
>let the tool do the work
It’s rather the attitude that people develop where, if the tool doesn’t do the work, it’s no can do.
Your thin enough to cut with scissors metal sheet is about the same mass as perhaps 2 of the balls inside the bearing, it is not even going to be close to the mass of the bearing’s inner race, let alone the bearing as a whole. Even stepping it up to the thickness you need real tinsnips for the mass to heat isn’t going to be large. Its way more than a negligible difference, even if its only 1 second longer to saturate with the tips heat when putting the tool away.. As the really hot end is not going to be in contact that long – that extra second or two adds many times more safety margin, assuming the small sheet metal washers are up to the task at all.
The thin sheet is also a direct solid connection between the heatsource and plastic, where the bearing all the heat has to pass from the inner race through the balls to the outer to then get to the plastic – you get lots of very poor thermal conductive spots and stages. – heat source to inner race, from that to the balls, then out to the outer where your sheet metal solution has a single and direct connection from the hot stuff to the stuff you want to stay cold, and being thin sheet metal is rather likely to deform under the weight of the iron to make really good contact with it in pretty short order… Plus if you take the grease out and remove any tight sealing dust covers off those bearings the balls have great access to the air for convection cooling.
I don’t know, and said I didn’t know if those specific irons would be alright on such a sheet metal stand – if that top end stays cold enough you could use something stupid like flash cotton on the stand if you are careful enough putting it down… But in this case a scrap bearing should be better – much more mass to heat, more surface area to radiate the heat and much more thermal resistance thanks to the terribly small contact areas inside from the hot side to the cold than the solid metal sheet. Along with being practically indestructibly durable and much easier to build around in comparison to sheet metal washers… Now if you were to build that whole plastic stand part in folded sheet metal then I would say you are on to something, as suddenly you have real surface area to radiate the heat before it gets near the thermoplastic bits and its actually going to be much easier to make…
> They say, “I didn’t know you can do that!”.
That will be true of all of us at some point for every topic – the tools you can use competently already have nothing to do with a lack of knowledge on some specific element of making stuff you are not that familiar with. Those with lots of past experience may have more confidence to try something else that might work, but equally they can have less – perhaps having had an assumption bite them in the past…
>It’s rather the attitude that people develop where, if the tool doesn’t do the work, it’s no can do.
Anybody like that, of which we are all bound to know several can still be a very decent maker – not everyone can figure out every step of smelt the junk they have to construct the lathe, to make the mill, to make the very precise sheet metal forming tools, to then crank out their custom embossed zippo style lighter case. And NEWS FLASH you don’t have to, and quite possibly shouldn’t either – as we can’t all be experts on everything required at every step, overconfidence to say we can with just enough knowledge of how to be dangerous is how you ruin the part, loose eyes, fingers, burn down your house, perhaps die. We all stand at some point on the shoulders of others work, and we don’t all have to be able to figure out ways to get from a-b-c-d with junk if the tool exists to make a-d a direct jump.
>Its way more than a negligible difference
Look, I already tried this the previous time we had this discussion, but I can repeat the experiment if you wish. I have now in my fingers a 0.25 mm strip of steel, 8 mm wide, and I’m pinching it exactly 10 mm away from the end. Holding a flame to the end of the strip, it takes a solid 10 seconds before I feel unbearable burning in my fingers – that’s about 60-70 C hot. Still not enough to melt plastic though.
Steel is that bad at conducting heat. It’s not going to do anything just by briefly brushing a hot soldering iron tip to it. One or two seconds doesn’t matter, you have to deliberately press the TIP of the iron to the steel in order to make it hot.
>> They say, “I didn’t know you can do that!”.
>That will be true of all of us at some point for every topic
To be more specific, the exact quote from the person was, “I didn’t know you were allowed to do that.”. Another example was a group of students who had problems fitting tab A into slot B in a 3D printed part. They complained about the poor fit, but nobody thought to put a nail file into the slot and widen it by two strokes. It just didn’t occur to them.
Another group thought to print out a test piece with variable size holes so they would find the exact setting that produced a good fit (for that printer, on that day, for that part), but they too wasted hours of time where they could have just taken a hobby knife and gently scrape the burrs off the slot to make it go in easily. It just didn’t occur to them.
Dude holding something yourself massively throws off the results – you are a reasonably effective water cooling loop, assuming you have functioning circulation. So taking 10 seconds while you hold it and your blood shifts the heat away means nothing, other than something under 10 seconds that point of the steel would get that hot.
The thin fold out metal stand my gas travelling soldering iron has is at least 40mm long and similarly wide from the two tiny contact points with the tail end of the iron and the table part that has a huge surface area itself and it in a matter of a min all of it gets hot enough from that ‘cold’ end of the iron to be too hot to touch comfortably all the way through.. Touch it with the actual hot tip end where you are applying probably 3-5x the heat directly to those small contacts its going to heat up rather faster, and get very much hotter, yes being hotter the ability to shed heat to the air will increase, but its not a huge effect..
So,
> You have to deliberately press the TIP of the iron to the steel in order to make it hot…
I think we can safely say isn’t true at all for every iron, and even if it is true for this iron a pair of washers has this void you can easily catch the heater core of the pictured style of iron against – especially the one at the back where you can’t see it, which will give you the PRESS THE TIP of the iron to it effect for a while if you ever fail to put the iron in straight enough. And worse it will be press the tip against the washer that doesn’t have much holding it in against those forces.
And if you print in PLA, which almost everyone does the 60-70 Celsius of too hot to touch without rapidly burning yourself is enough to turn it into a very soft plastic that thin washer under load will just push right though or pop out off having distorted the retaining features. It won’t melt at the temperature, but PLA gets damn soft really easily with a little heat, and as its a 3d print is probably very hollow so doesn’t actually have any great mass there to heat – So that brief touch of the heater core against the rear washer could quite easily soften the plastic enough.
I have never said your washers can’t work, as I said I have no hands on with this iron style, they may be cold enough up there to not be a problem, thin enough to easily pass through every time, and be light enough the thin metal concentrating the load against the plastic print isn’t going to be enough to make the plastic creep… But a bearing is so so much simpler to design around – its a standard part that everyone can get, and almost everyone interested in making likely has cheap/worn broken ones, it is more durable, and if you actually take the grease out (which I note in your test below you didn’t) a good heat break, with a nice wide area to transfer the mass the of iron to the plastic part – no point loads here. It is just a better design than substituting the bearing directly for washer – you really want to use washer move the thermoplastic plastic 3d printed parts further away by riveting or welding those washer to a rod of anything that can actually take getting a little warm, and won’t creep under load…
>But a bearing is so so much simpler to design around – its a standard part that everyone can get
So is a washer. It would be a weird place if you have an easier time sourcing a 608 bearing than a standard stainless steel washer.
The ball bearing has spheres contacting cylinders. Do in theory single point to transfer the heat. Then from the other side of the ball to the outer cylinder.
With washers, we are talking about continuous metal parts, so full on conduction. I think it would melt the plastic way quicker.
If your washer is thin, when heated, it slices trough the plastic more easily. Now if it is thick, that’s more surface area for conduction.
Doing this analysis, it seems to me that the bearing should be vastly superior to the washer at separating the heat of the iron from the printed plastic.
In your argument, you don’t address this.
I don’t think that with such low surface area we will get enough heat dissipation to prevent plastic melting, we need to get low thermal conductivity.
Mild steel, thermal conductivity is 40-50 W/m-K, stainless is much worse, but the bearing won’t be made out of stainless steel so that wouldn’t compare. It’s hardened steel.
Suppose you have a 0.5 mm thick washer, 8 mm ID, 22 mm OD. That makes an average heat transfer area of 24 sq-mm. The distance from the inner to the outer rim is 7 mm. Using one of the many online calculators, you can estimate that such a plate or a bar of material would have a thermal resistance of 6.5 K/W.
That is, if there’s one Watt of heat leaking through the washer, the outer rim is 6.5 degrees cooler than the inner rim. If the iron is 100 C at the stem, the outer rim would be 93.5 C. However, since the point contact has easily 10x the thermal resistance (unless we’re pressing down really hard and the contact surfaces are smooth as glass), the combined thermal resistance is more like 65 K/W or more, and the washer remains at around 30-40 C under steady state conditions.
Compared to the bearing, sure, there’s more interfaces to act as heat breaks, but the bearing is also 7 mm thick and full of grease, which helps the heat jump across the bearings and into the side walls. It’s not that much better at stopping heat from flowing across, if not worse. What actually does the trick is the very poor conductivity touching against the iron.
Now, I don’t know if this works, but here’s a picture of me holding a 22x8x0.25 mm washer I just punched out a sheet of steel. I’m heating the inner diameter with the point of a butane soldering iron, trying to see if my fingers start to burn. After two minutes, nothing.
https://imgbox.com/67BHL18U
Now, I dug out a 608ZZ bearing and did the exact same test. At the 2 minute mark it was slightly warmer than the thin washer, and it kept getting warmer and warmer. At around 5 minutes it was noticeably warm though it was starting to level off. I took the soldering iron off and touched both inner and outer races to confirm that they were more or less equal in temperature, which means that there wasn’t much of a heat break between them.
The proof of the pudding is in the eating.
Then, for a final point.
Let’s ignore all the thermal mass and properties of the metals and just look at the geometry. Suppose there’s 1 square millimeter area in contact between the bearing and the iron. Against that, there is 330 square millimeters of the side surface facing out and radiating the heat away. Twice that counting both sides.
Both the washer and the bearing stay cool because the input area is much much smaller than the output radiating surface. It’s a heatsink, not a heat break.
This is Hackaday, not Instructables. If your hobby is 3d printing, you definitely have a 608 somewhere. You *might* have cheap 608s lying around, and you probably also have an used or seized one too.
Where I live, I can get decent quality 608zz’s for less than $1 a pop. You definitely won’t want to use them for applications with high RPM or radial loads, but they work for everyday things like desk fans or 3d printers, especially for printed assemblies (lots of them use 608s as they are ubiquitous, as is the case here).
Your washer approach won’t work for shit, at least not with my own soldering iron, because it also heats up considerably on the heater’s shielding. On the other hand, this is proven and works fine.
I do agree with you with everything else though. Not long ago there was an article here about a 3d printed knitting machine that made knit tools, and they seem to be selling “knitting weights” (to pull down the sock so the machine works correctly) that are simply big washers, probably M12 or more. and they were selling them for several dollars apiece iirc. I couldn’t believe it
>Your washer approach won’t work for shit, at least not with my own soldering iron, because it also heats up considerably on the heater’s shielding. On the other hand, this is proven and works fine.
I don’t see why that would be the case. For similarly sized washers, it would have similar heat shedding properties along the exposed surfaces.
The main “heat break” in this application is the fact that the soldering iron touches the metal at two small points, which greatly impedes heat transfer into the metal, which keeps cool because the exposed surface is much larger than the area of the two point contacts. The thinner the disc you use, the smaller the contact point and the harder it is for the heat to move radially out towards the plastic holder (thermal resistance along the metal). What you actually want is like resting the soldering iron on a knife edge. The idea that the bearing acts as a heat break because of the ball contacts is bunk, because the heat also transfers through the metal side walls and through the grease which in this case works more or less as a thermal paste.
A bearing should in fact move heat as much as possible from the axle to the outer rim to avoid overheating in its intended applications, which in this case it would mean melting the plastic holder. The fact that it works at all is simply because the soldering iron doesn’t give off all that much heat into it.
I’m still not entirely convinced by your analysis, but it seems neither of us is going to try making these stands. In any case, a simple metal wire bent in an U or O shape with enough separation from the plastic will be much safer than either bearings or thin washers insofar as melting the plastic. But my main point is that these bearings aren’t unobtainium. plus the end product at least looks better than a bent wire or two washers in my opinion.
It looks more complicated than a pair of washers, but whether that is any better is a whole different debate.
As for the heat transfer, it’s quite simple. It’s kinda like Ohm’s law. Think of the material in the bearing like a bulk resistor with current going through it from the hot to the cold end. The temperature at any point is like measuring the voltage along the strip of a potentiometer. Where there’s any choke points, like a point contact, you get a large change in thermal resistance and a large drop in temperature.
The worst choke point for the heat to move inside the bearing is right at the two points where it touches the iron. From there the heat has many paths and lots of material to travel through to the outside.
> these bearings aren’t unobtainium
True, but I can get a whole bag of washers for a dollar. The most expensive suitable washer I can find by quick search from the local shops is ten for $6.40 and that’s at the DIY section of a supermarket. Half a mile from that is a general store where they sell nuts and bolts by the pound, so two would cost something like… dunno, 5 cents?
This is why the WHY is so important…
Not directly relevant here but It’s kinda the same reason why I “hate” most YT tutorials on Minecraft designs.
Not just because a few pictures and blueprints/schematics with a bit of text would make an actual documentation instead of just a demonstration – most don’t explain why they do something in a specific way or use specific materials, they just talk about what they’re doing right in that moment (which we can see anyway)… :-(
I’m sure the same complaint is applicable on many other “real” (hardware) hacking “tutorials” too.
On that note: I love this HaD Article! Actual images of the “hack” not just blank spaces left by eviscerated YT videos (µMatrix does a great job of removing embedded YTs globally here :-) ).
The “why” would take more effort and actually require you to understand the topic to the point that you can explain it to someone else (insert Einstein quote here).
A lot of the time the people themselves only know how to do it, not why they’re doing it. Hackers and makers especially, because we tend to stumble upon solutions that just happen to work and so we go “If it works then it isn’t stupid” – and go tell the others immediately.
The reason why a bearing works unreasonably well for this application is that the balls have very small contact points between themselves and the inner and outer races. Those create a choke point for heat transfer, and keep the outer race substantially cooler than the inner one.
That said, your points about grease dripping and cargo culting are definitely valid. The optimal 608 bearing solution would involve removing any shields so that the bearings are exposed, and washing all the grease out before using the bearing. Once you do those things though, the 608 is actually pretty ingenious.
In theory, but assuming the heat doesn’t get removed from the bearing into the surrounding plastic, which is what we would prefer, the temperature inside the bearing would eventually equalize. The heat has to flow somewhere for there to be a temperature difference, and we don’t want it flowing into the plastic because then the plastic would get hot.
What the part actually does, it’s not acting as a heat break or an insulator, but as a radiator through the side walls, shedding heat off to the surroundings more effectively than it can get in. This is what keeps the temperature towards the outer rim down: the heat goes away before it reaches the plastic.
This is actually an important part of sharing your own design. It impedes ignorant people copying and selling your design. An experienced hacker can read between the lines and see obvious “design faults” immediately. They change the design according to their needs using the parts they have. I have couple of these particular bearings. They are very common size. You can find these seized in old motors and already degreased in fidget spinners.
That’s the 19th century mindset of inserting errors into patent drawings to stop your competitors from copying your invention.
The question is, why? If you’re going to sell it, then you won’t publish the plans. If you’re not going to sell it, why trip other people out of simple elitism?
You are so condescending today…
Sorry, I mean yesterday
They use 608 as they are the standard. The vast majority of 3D printers have multiple of them, they are used in tons of prints. The reason is that most people with 3D printers have tons of those laying around. That’s not cargo-cult design and engineering, but smart. Why force people to buy new when you have something that just works? It doesn’t matter that it’s not a good heat break, it’s cheap and works. Washers won’t work properly, are messy to work with, have tons of variations between brands and then you have the normal and american versions which means a large portion can’t make it, depending on which model you use. Washers is a terrible idea. Besides not only that, they are not rounded and will damage your tips, while bearings have a nice smooth curve, protecting the tip, prevent a lot of heat transfer, easier to obtain, usually people have them already so it prevents buying new, everyone can get them anywhere, it’s just plain better to use. And your grease complaint isn’t even a thing. The tip is heated, that’s not in the bearing. Pinecil is usually configured to turn off after a short while if not used, so it’s highly unlikely to heat up anything back there, if it does, it would also mean the case of the pinecil will melt. So honestly, all your arguments are invalid
This is exactly why I almost never print things I find ‘as is’ and instead I either start from scratch and use it as inspiration for my own design, or make minor alterations to the original model
I just needed a stand and I wasn’t too excited about the bearing: https://www.printables.com/cs/model/125646-ts-100-holder
Interesting design.
What if you took a piece of the same U profile and turned it sideways with a hole through, for the actual holder insert? That would be my first instinct on how to make one of these.
I wanted the hot tip to be hidden in the U profile, protection against burnt wires lying around on the table
I know. What I meant is a short piece of the same profile, sideways inside the longer piece instead of the plastic insert.
That way the iron touches no plastic whatsoever, only metal. It can sit there forever without melting anything.
she’s not warm upstairs ;)
There’s also this version that uses an M8 nut instead of the bearing: https://www.printables.com/model/481888-m8-nut-pinecil-stand-for-soldering-iron-storage-bo
I haven’t tried it yet :-)
Why not just use a cheap washer?
This looks very tidy. Gone are the days of just hanging your Antex off your anglepois lamp by its hook!
Ceramic tubes go for $4 per 10 pieces on aliex.
I printed this for my ts100 about a year ago. I fly fpv drones and keep it in my backpack for field repairs and it’s great.
I printed my case off the 2022 article. This looks like a reasonable update. Time to level the bed.
God, I love my self-leveling printer :P
I recon the ball bearing would work adequate, and it’s a commodity item with a known size.
First part of the heat break would be the small contact area between the soldering iron and the bearing in the first place. (and the balls become second).
But wen portability is important, you are likely to power it from a battery pack (which the TS100 is also designed for) and available energy is limited. It would be nice to have some kind of heat insulation for the whole tip that limits heat loss when the iron is in it’s holder. That seems more important to me than the bearing versus washer discussion.
Stainless steel is also a significantly worse heat conductor than regular steel. I would probably make a holder out of a piece of bent stainless steel wire or sheet. With a stainless steel tube over the tip, it would probably already reduce the amount of power needed to keep the iron at it’s working temperature.
It’s good if you have one laying around, I have a ceramic wire insulator laying around that I would substitute, looks like a big life-savers candy with a thick wire wrapped around the outside with a spike. If I see a project I want to build I usually modify it to accommodate my laying around inventory.
Anyone know how to get a replacement shell? Mine cracked and I’m not a fan of the printed ones.
If it’s a Pinecil, you can buy either a black or a clear replacement from pine64.com, as well as replacement contacts and tip sets.
For TS100 I’d imagine that they’re ubiquitous enough that AliExpress has a bunch of options.
And here I am just putting my ts100 or pinecil down directly on the table…
I really need to print this again. When I started 3D printing, this was one of the first prints I made and I had really big problems with it, due to adhesion/warping problems, sizing etc. Got a ton more experience now and got my printer finetuned, so this might be actually doable.
Also planning on buying another pinecil. Not because my older one is bad, but because I want another soldering station at home. I’ve had many soldering irons in the past and they were all just annoying to use. Doesn’t matter if it’s one from a hardware store, a cheaper soldering station, a weller station, none of them are nice to actually use. Even at work, we got the expensive weller stations, I’d rather use my pinecil. especially with the silicone USB-C PD cables they sell for almost nothing.
Recently made my own, using inserts from similar print, and changes I felt are necessary for it to be more durable and modular : https://propiro.github.io/ts100-printable-durable-case-now-with-100-more-cyber.html
I went looking for one of these when I got my Pinecil and couldn’t find anything. I must have really screwed up the search, because it seems like this design is like using a LACK table from Ikea as an enclosure for your printer!
My shed has more washers than bearings though, so I’ll probably ditch the bearing in this design… or just use a bit of coathanger wire, bent to shape. Or, you know, just not rest the iron on anything flammable :-)