One of the keys to making money with manufacturing is to find something that you can make a lot of. Most small manufacturers have one or two “bread and butter” items that can be cranked out in quantity, which of course has a quality all its own. The problem with that approach, though, is that it runs the risk of being boring. And what better way to avoid that than by automating your high-volume job, with something like this automated CNC work cell?
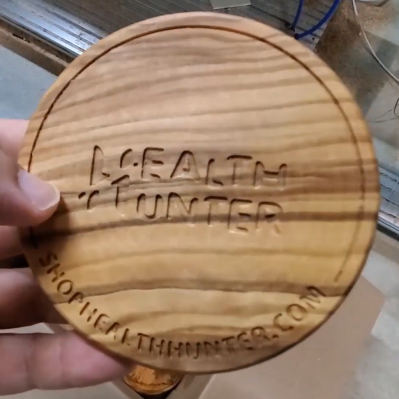
[Maher Lagha] doesn’t offer too much in the way of build details, but the video below pretty much tells the tale. The high-volume items in this case are customized wooden coasters, the kind a restaurant would buy for their bar or a business would give away as swag. The small 3-axis CNC router at the center of the work cell is the perfect choice for making these — one at a time. With no desire to be tied to the machine all day to load raw stock and unload completed coasters, [Maher] came up with automated towers that hold stacks of pallets. Each pallet, which acts as a fixture for the workpiece through multiple operations, moves from the input stack into the router’s work envelope and to the output stack using a combination of servos and pneumatics. The entire work cell is about a meter on a side and contains everything needed for all the operations, including air for the pneumatics and dust extraction.
Each coaster requires two tools to complete — one for surfacing and one for lettering — and [Maher] has two ways to tackle that. The first is to allow a stack of coasters to go through the first operation, change tools, and switch the roughed-in stock back to the input stack for the second round of machining. The other is just to build another work cell dedicated to lettering, which seems to be in progress. In fact, it looks as if there’s a third work cell in the works in [Maher]’s shop. The coaster business must be pretty good.
I had to blow up the photo of the coaster about twice actual size to be able to read the logo. I guess if it gets properly painted, readability will improve.
But, a good build!
You´re getting old …
“And I would have got away with it, if it hadn’t been for that meddling Beatle wife!”
B^)
Let me show you how old I am!
https://m.youtube.com/watch?v=0ZXZ8QlyMkQ
Heh, I should change my cellphone ring to that “first phone” ahaha ahaha ahaha noise
Nah, we’re not old. Old is when you remember when dial phones first came to town and the phone company had to train us how to use them.
https://www.youtube.com/watch?v=p45T7U5oi9Q
It’s because of how the designer split that big H, but also it would be more readable in person, with higher contrast and better depth perception.
There was this dude some time ago that invented cars but mostly a way to make many things in a row in a line. A line where people assembled stuff. Called the Line Assembler or something like that. It allowed him to crank out a bunch of cars. I wasn’t alive then but I’m told this method had long lasting consequences.
Sarcasm aside, the Meta of automating CNC is pretty funny. I mean. That’s what CNC is supposed to do anyway- automate a tedious task. So to automate an automated tedious task to reduce, ahem cough, tedium, is funny to me.
im not sure this is about automating cnc, its about integrating 2 tools to go way faster. you could carve the entire thing using a 5mm ball end mill, it would just take 24hr/coaster. Generally speaking I would definitely consider this not anything like an assembly line as the whole thing the scope of the machine addresses is fabrication. That may seem like a semantic point, but I think it’s an important one – once this is streamlining making a part, not screwing together many parts.
Why is that funny to you? A CNC machine tool can only perform a series of movements as told by a human. The material in which it machines a part is either loaded by a human, one-at-a-time or automated by some material feeding mechanism (hydraulic bar feeders, pneumatic loaders, vibrating rails, etc). And the automated material loading devices require a human to periodically re-load them with more stock material. Further, a human is typically the one who prepares the the raw material into a specified form factor. The carbide cutting inserts, yes a human changes those as well, and must also periodically make adjustments to compensate for tool wear. THIS IS STANDARD PRACTICE ALL AROUND THE WORLD IN ANY MANUFACTURING ENVIRONMENT. Numerically controlled machine tools are designed and built to run 24hrs/day/365, theoretically that is. But they cannot conger raw materials from nothing nor can they wipe their own ass, if they had one! This is the human/______ automation (fill in the blank) paradox. If only there was something that existed, I don’t know a thing perhaps that could automate all these processes and possess the fine dexterity to manipulate parts, any part along with being capable of wiping its own ass and the machines… Well that would be truly amazing, said the human!
Good summary!
Once he needs to scale he will probably be buying or making blanks. A machine that spins the square blanks against a belt sander or router will make them round quite quickly. And with the proper router bit it can have a pleasing profile.
Although you could argue he would be able to sell custom profiles if he put up selection of outside shapes. Even that could be accomplished with a single axis of the Router/sander. A rotation axis that can clamp a piece, and a router on rails. Then you are in a whole different world.
Also in factories the CNC will have multiple cutting heads on one axis so it can parallel the jobs, make 2 or 6 at a time. Maybe make Minimum Order Quantity 4 and have 2 or 4 cutters
Also you may have to explain ‘surfacing’ to me. I believe there is a machine called a planer that will surface anything you feed into it
Surfacing as in ball tracking a profile
It would require all three axis – z for height, x/y for the arc interpolations.
Why you don’t do this:
https://www.youtube.com/watch?v=D2xoxPlDnW4
https://www.youtube.com/watch?v=4tpxgZUYGSI
Fires among shapeoko users in particular are pretty common.
Few / no hobbyist or even entry level commercial systems have a way of detecting workpiece issues (shifting, breaking), failures in movement systems (such as overheated drivers that start missing steps, belts that slip, or bits of the machine loosening up, like the spindle for example), tool breakage/slippage, etc.
There’s a reason why most CNC shops have operators who at the very least are watching over multiple machines, machines that are made to far higher standards than anything we’re building in our garages…and often have fire detection and suppression systems.
In our industrial lab we frequently set long experiments to run overnight un supervised. All in enclosed hoods with fire suppression etc. this was before cheap cc cameras and stuff. One morning we came in and something “bad” obviously happened and all the safety stuff did its job. Took us a while to figure it out but the computer controlling a bromine gas bubbler had Microsoft decide to update and restart the computer which let it go unchecked till the bromine ran out. If this type of malfunction happened in a garage instead of a specially made fume hood containment it would have burned the house down.
We sucked it up and made someone stay overnight after that.
So let stuff go unsupervised at your own risk is the lesson.
Frankly, my take away from your little disaster would be to not trust Microsoft.
Ha yeah that was one of the takeaways for sure. Or more like continue to distrust… But bigger issue in general was even when things work fine for a while, with complex systems impossible to anticipate stuff can still happen. Best you can hope for is design apparatus to withstand even unanticipated problems and hope you’ll be ok. As in this case.
Well that’s one for Risks Digest if ever I saw one.
Hi Craig, yes you are right. And actually, I am working on a safety system to detect errors, for example take picture of the coaster and compare it to a reference etc. IoT stuff. Also, I plan to move this machine out of my house to a proper workshop. Thx
My brother once had a 6+ hour CNC job in which he had to cancel the “windows update” dialog every half hour, and I had a presentation during a funeral interrupted because of a “mandatory printer driver update”.
For myself, I quite windoze a long time ago
I have shitcanned windows for exactly the same reason.
Scary stuff
A Y axis mill with live tooling and a stock feeder would make this pretty painless 😊
Nice, but the remaining question now is, how many axes does this cnc have now?
It has 3 axes, X,Y and Z.
No, it doesn’t have any axes, an ax is too imprecise for detailing coasters.
Though one could be used to obtain the raw material for the coaster.
B^)
haha, good one!
I sometimes comment and then wonder if my wording is too harsh. I really enjoyed the piece and it gave me a lot to think about, but I have a real problem with the concept, and am wondering if anyone else shares my viewpoint. Firstly, I commend the person in the video for the excellent work and craftsmanship. Hats off to anyone who can get this setup running, like he did. Really. Well done. However, I am unsure about the reasoning behind it. Presumably automation saves time and effort, but I can’t see that happening. Again, please help me if I am wrong. I see all those pallets set up so they can be used in the stack before going into the machine. That takes time, and material. Wouldn’t a simple jig under the CNC be easier/safer? If you have to be there to watch over the process (you would, right?) then exchanging the pieces in the jig would seem to make more sense to me. I might be wrong, and please point that out if it is the case. Thanks!
I imagine you can bang out a load of blanks (perhaps from scraps) quickly & easily and get them mounted on jigs & loaded, leaving the robot to just churn through whatever’s in its “inbox” while you either do other things or go home to sleep.
My main concern is as someone else highlighted above – the day the process goes wrong and you come in next morning to a huge pile of scrap or, worse, a burned-down workshop. Very easy to imagine a broken cutter grinding away at a piece of wood unsupervised for 8 hours is a good way to start a fire.
For whatever reason this issue intrigues me. If business is so strong that the machine needs to go mostly 24/7, that would imply that an investment in a better/faster rig or to start running two or more in parallel could/should be considered. I think worst solution is let it go unchecked during off hours given personal example cited above. I know for a home business (or our startup lab) profits may be razor thin/nonexistent but in the end even we realized that one (ONE) accident would cost us enough to shutter the whole enterprise permanently. We were rabid about lab safety. I wish this person well but cranking out coasters faster isn’t worth damaging your equipment putting your business down and losing money or worse, ruining your shop or family home. If you do go that route then at least invest in some error detection or fire suppression/electric lockout or something like that so that when, not if, it goes haywire you stand a chance of salvage.
I agree with you, actually, I am working on an error detection system to make it safer!
When all you have is a CNC, all problems look like solutions needing a CNC. Right? In my mind, here’s a perfect application for a lathe of some sort to spin the blanks. But since we don’t see the other steps he takes from raw material input, to making of the blanks, to the mounting steps, unmounting since he’s got to finish cutting out the coasters once they’re engraved, and do a finish pass of sanding etc.
Though maybe he’s just automated this part because it’s the simplest thing to do while he takes care of all the other manual steps.
Personally I’d have looked into something where I could mount wood in a lathe, make the shapes and edges, cut out the blanks on an indexing band saw (or chop saw) then feed into a sander. Then figure out some way to drop into the CNC for the lettering. Use the CNC for it’s flexibility and the other tools for their dedication to tasks they excel at.
Then the trick is to automate holding of pucks, but the nice thing is you don’t care about orientation, just holding power. Hmm…
That’s true, we did that few years ago: we started from rounded and empty coasters. But this CNC is not only for round coasters, it can also make square, pentagon etc, and also even coffee spoons.
Yup, that does make sense if you need/want to make more custom outlines. It’s hard to know when you should move to more job specific tooling, or just stay with the more flexible, but slower, CNC method.
In any case, it’s impressive work, it must take a while to debug!
And how do you do the final step of extracting them from the holders/blanks? Suction cup on the bottom? Some other type of holder? I’d love to see your flow from start to finish.
Thank you so much!
Yes I will make a video to explain and show the details per people requests. To hold the wood, I use a sacrificial wood (the white one) attached to a steel plate. The steel plate is held in place with magnets. The other option I tried is to use vacuum, but my little vacuum pump (but expensive) did not last long due to the wood dust, it will always ingest wood dust even if we are careful. Maybe a bigger pump will be OK, but for now, I am happy with the magnets.
“When all you have is a CNC, all problems look like solutions needing a CNC.”
That’s a problem???
B^)
Gents, I confirm Dan’s guess, there is another cell in the making for larger work pieces, stay tuned!