Airliners have looked largely the same for a long time now. The ongoing hunt for efficiency gains has seen the development of winglets, drag reducing films, and all manner of little aerodynamic tricks to save fuel, and hence money.
Boeing now has its eye on bigger, tastier goals. It believes by switching to a truss-braced wing design, it could net double-digit efficiency gains. It’s working together with NASA to see if this concept could change the face of commercial aviation in decades to come.
Aspect Ratio Matters
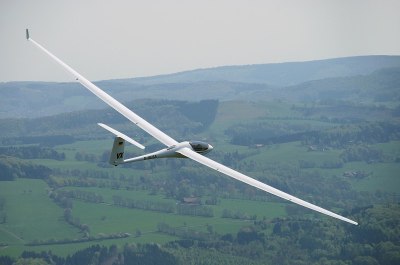
The key goal of using a truss-braced wing is to enable an airliner to use a wing much thinner and narrower than usual. These “high aspect ratio” wings are far more efficient than the stubbier, wider wings currently common on modern airliners. But why is aspect ratio so important, and how does it help
If you’ve ever looked at a glider, you will have noticed its incredibly long and narrow wings, which stand it apart from the shorter, wider wings used on airliners and conventional small aircraft. These wings are said to have a high aspect ratio, the ratio between the square of the wingspan and the projected area of the wing itself.
These wings are highly desirable for certain types of aircraft, as lift-to-drag ratio increases with aspect ratio. Any wing that generates lift also generates some drag, but this can be minimized through careful wing design. By making the wings longer and narrower, and thus higher in aspect ratio, the wing tip vortices generated by the wing are weakened. This reduces drag on the plane, and quite significantly so.
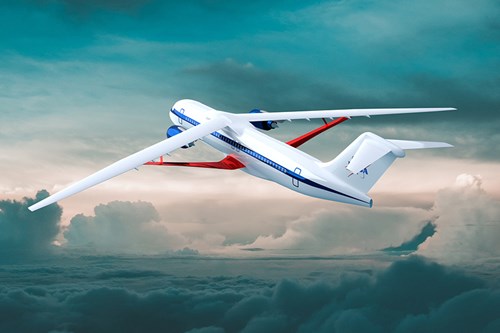
For a glider, which has no forward propulsion of its own, minimizing drag is a must. Hence, high aspect ratio wings are very useful. Similarly, the high-flying U2 spy plane had excellent range because its high aspect ratio wings were very efficient. Both of these types of planes have fairly limited payload requirements, and are specialized enough that high aspect ratio wings can work as-is.
Airliners have other concerns that make high aspect ratio wings impractical. They must carry huge payloads in order to make lots of money per flight from paying passengers. It would be great to have high aspect ratio wings on airliners, as the efficiency would slash fuel bills significantly. Unfortunately, it’s difficult to make them strong enough for such heavy-duty purposes. There simply isn’t room for the structure and material required.
Instead, where a glider might have an AR of 30 or more, an airliner will feature wings with an AR closer to 7 to 10. High-end gliders achieve lift-to-drag ratios of over 50. Airliners do much poorer in this regard. The original Boeing 747 achieved a L/D ratio of 15.3, for example. Decades of development have seen today’s modern airliners push that number closer to 20, like the Airbus A380 and the Boeing 777.
Brace Yourself
Throw on a brace for support, though, and suddenly the high-aspect ratio concept becomes plausible. Of course, it’s a radical change to the basic airliner concept. That means there’s plenty of work to be done to determine just how truss-braced wings could work in practice.
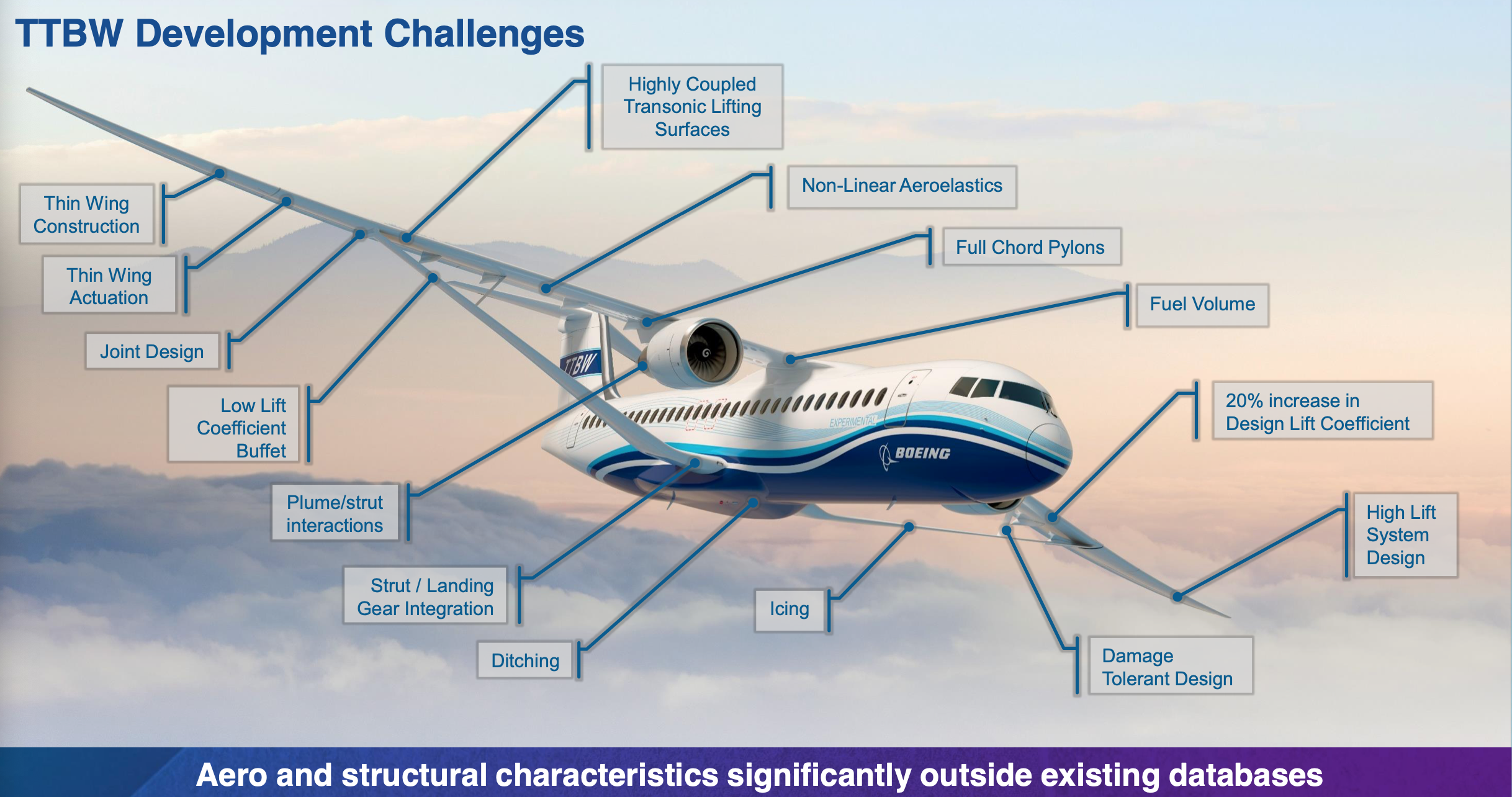
The current concept in development is called the Boeing Transonic Truss-Braced Wing, or TTBW, with a full-scale demonstrator expected to fly in 2028. It’s also been designated as the X-66A within US aviation circles. In development since 2010, the concept involves a plane with an ultra-thin, high aspect ratio wing, supported by a truss underneath. The demonstrator is being built on a shortened airframe from a McDonnell Douglas MD-90, and will be tested at the NASA Armstrong Flight Research Center. The concept is intended to suit either 130-160 passengers, or 180-210 passengers, depending on the exact configuration Boeing lands on.
The demonstrator is on the scale of single-aisle aircraft, albeit with a far larger wingspan, at 51 meters. This is still far narrower than dual-aisle aircraft like the 747, at 68 meters, but much greater than a single-aisle Boeing 737 MAX at 36 meters. To accommodate this extra width in existing narrowbody facilities, Boeing may explore the use of folding wingtips. These have already been used successfully on the Boeing 777X, to ensure the wider-than-usual type could access as many airports as possible. Thus far, the concept is primarily being considered a proposition for smaller narrowbody, single-aisle airliners.
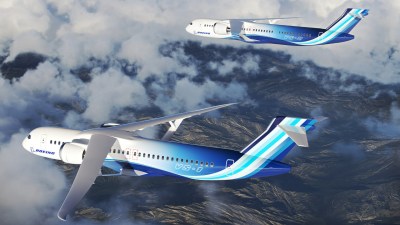
Wind tunnel tests have suggested that the higher-efficiency design could reduce fuel burn by up to 10%, based on the gains from the wings alone. The hope is that further new technologies that could be integrated into next-generation planes could push this as high as 30%. Boeing has noted that with the high wing mounting of the truss-braced design, such aircraft “could eventually accommodate advanced propulsion systems that are limited by a lack of underwing space in today’s low-wing airplane configurations.” To start with, though, the demonstrator will run Pratt and Whitney PW1100G geared turbofans, as used on the Airbus A320neo.
Whether truss-braced wings become common on airliners will come down to several factors. Beyond the engineering required to make things work from a structural perspective, there’s also a requirement to address practical concerns. Airports around the world are only built to handle aircraft of a certain size. Planes that go beyond that, like the Airbus A380, have suffered for their girth. Whether the promised efficiency gains are found is also still a question at this point. In any case, if Boeing’s hunch proves true, we could be riding on some very different airliners as soon as a decade from now.
Featured image from this great video about making a model truss-braced demo plane.
So, they’re pretty much spending millions of dollars to reinvent PZL M-15 Belphegor, an agricultural jet biplane.
Sure, they’re simply redesigning it for intercontinental flight at transonic speeds.
There’s a reason trusses were used for a while, and it’s because the second moment of area is a thing. There’s also a reason they were dropped, and that’s because it’s extremely difficult to optimize interference drag.
It’s hard enough to do optimize the joint between wing and the fuselage (inefficiency here killed off plenty of otherwise sound early business props when their competitors did it better), but interference drag is basically impossible to model mathematically between two lifting surfaces, and only simulatable to a useful degree with modern computation and a ton of experimentation to tune CFD models.
Never heard of ‘interference drag’ before but it’s interested me.
From a quick scan, and intuitively, I think it’s caused by the laminar flow over two adjacent surfaces interfering with each other at the transition point and the sharper the transition point the worse the drag?
So, again intuitively, it would seem the best way to reduce it is to smoothly blend between the surfaces with swooping, soft curves and bends?
This could make for some ridiculously pretty airplanes!
You got it! You’ll see it in an exaggerated fashion on some old fast props. Nowadays most airliners get most of the benefit of a wing root fairing without the intricate metalwork with the belly fairing.
Not always! See the Wittman Tailwind– according to CAFE testing it has very low interference drag between the wing and fuselage for the type of airplane it is (two seat light aircraft)– and it is completely slab-sided, with a flat wing. They meet at 90 degrees. Swooping curves have to be done juuuust riiight or you end up with more drag than you otherwise would. In light aircraft, they were rarely done that well, so Wittman’s slab-sided Tailwind is a win.
The Tailwind is also strut-braced, FYI… like the vast majority high-winged light monoplanes built in the last 80 years.
Laminar? No.
Couldn’t the fuselage problem be solved by using an electric engine and a couple of RTGs? I never really understood why fossil energy was being used in planes. The weight of the fuel itself caused unnecessary depletion of fuel. And by storing fuel in wings, the steering is very difficult and sluggish. Not to say dangerous, if an engine catches fire. By using a thermoelectric generator or solar cells etc, the power source wouldn’t impact efficiency so much.
fossile fuels are used because it is the only thing with anywhere near the energy density needed. Thermoelectric generators or solar cells wouldn’t even power the light it the cabin
Quick google gives you the answer, if the figures are correct then it’s around 12KWH/Kg for jet fuel compared to 250-300WH/Kg for Li-Ion cells.
That should make it pretty obvious why fossil fuels are used.
Not completely, because electric batteries are close to 100% efficient whereas jets are 30-40% efficient at best. So the comparison is really ~4000 vs. 250-300. Then consider next generation solid state batteries are close to 1000. Truthfully that’s probably about where it’ll land long term – batteries at around 1/4 the energy density by weight as compared to jets. But once you consider just how much cost savings an airline can get using electricity (plus solid state batteries last forever) and that fuel is the airline’s largest operating cost, electric planes start to become very attractive for short haul flights.
Plus one other thing that stinks is that with fuel once you burn it you dont need to carry it.
Batteries weigh just as much from take off to landing. This extra weight actually makes landing more difficult as well and can impact cargo capacity.
Im sure there is a scramble in the areospace industry to figure out all the possible aerodynamic gains they can to get decent range when they switch to electric.
To LouNL: modern turbofan engines can reach 70 percent or more efficency at cruise. You can bet 10x to 20x the effective energy density really helps on anything that has to fly.
“by storing fuel in wings, the steering is very difficult and sluggish”
also not really true. first, airplane “steering” in the air is limited by the fundamental design characteristics of an aircraft (stall speed, strength and size of various parts of the airframe, practical limits on control surface deflection, etc), In commercial flights a big factor is also the comfort and safety of the passengers – even something like a 737 can bank a lot harder and pull a lot more g’s than you’ll experience in any normal flight.
putting fuel in the wings has some substantial advantages – it gets all the fuel close to the plane’s center of gravity in two out of three dimensions, and, as long as you draw fuel from both sides equally, it’s fairly balanced in the third. It means you can use an otherwise empty space (wings are mostly hollow), so the body of the plane can be smaller and more efficient. It also puts less stress on the wing roots than carrying an equivalent amount of fuel in the body (insert physics explanation here).
That’s not to say it has no drawbacks, but there’s a reason it’s one of the most commonly used setups on commercial jetliners.
Also landing weight is a huge consideration. Liquid fuel is weight that can be shed during a flight that allows the plane to land on short runways and have less forces on the landing gear and fuselage. Solid state batteries can not be shed therfore everything has to be upgraded tires landing gear brakes fuselage. Which increases weight and cost of the plane.
RTGs are very inefficient and have very low output, generally less than 1000w. That’s not enough to run the fuel pump for a jet engine to say nothing of actually propelling a plane through the air. Even if you could make it work, you’re faced with the issue of a screamingly radioactive lump(s) of material flying over populated areas. Less than ideal if the plane should crash.
Trolling again?
You feel tensbof thousands of flying nuclear reactors would some how be safer than the risk of an engine fire?
Need your eyes checked?
> PZL M-15 Belphegor
Had to look that one up.
Um… that is not an ….. attractive .. airplane
Well, it is named after a demon
If anything this resembles the bracing in the Bellanca Aircruiser, which coincidentally was one of the most efficient planes of the time (according to Wikipedia)
The concluding paragraph is the real crux of the design. As an airport engineer, it would be great for an adoption like this as it would create a lot of new work on airports due to the increased wingspans. More realistically, the wingspans will have to work at what is existing. You will find many airports are designed up to Airport Design Group III, which the common B737 is maximized for. This wingspan max is 118′. Once past this wingspan, the number of airports that you can operate at dramatically decreases without a galactically massive infusion of infrastructure reconstruction. Feasibility for this seems to favor international travel, and as mentioned, the A380 did not make the splash it was intending.
This is totally true. My guess is that they’ll have to figure out a folding mechanism like they did with the wider-wing 777. But it’s probably worth it.
Winglets are only efficient relative to wings of the same span. If you could unroll them and just make the span wider, you’d win. Yet planes have those vertical winglets. QED.
That raises a killer – perhaps literally – of a question. If the wingtip folding mechanism fails, and the craft in question isn’t close enough to a landing area that can accommodate its additional wingspan, what’s a pilot to do? Things could get really ugly really fast.
I suppose they could have some provision for jettisoning the bit beyond the fold; but that could fail too. Not to mention the caveat that pieces of airplane would then be falling from the sky…
They land normally, then disembark with rolling stairs rather than at a terminal. The wingspan limit is for handing at the terminal, not for the runway
Doh! I should have thought of that – thanks for clarifying.
So long as it fails locked lol. If it fails fails, you land in a field for unscheduled disassembly.
The size of the folding tip is no larger than the effectiveness of the eilerons to counter the lift differential in the case of a fold/unfold failure. Otherwise the B777 would have bigger folding tips. Also the tips are never folded/unfolded in flight, only on the taxiway.
>Feasibility for this seems to favor international travel, and as mentioned, the A380 did not make the splash it was intending.
I feel like the intent here is that this would be to the B787/A350 what the B787/A350 was to the A380.
As in, the A380 (and 747-8I to some extent) was designed to maximize passengers on a single plane that would still fit in (some) existing airport boxes. And it did a pretty good job of that, but then it turned out they’d overestimated the market for “haul huge numbers of people all at once from one hub to another”. Then along came the 787 and then A350, which carried a smaller but still useful volume of pax, and still had true intercontinental range with better fuel efficiency, and it turns out that being able to carry people from a lot more points-to-points is much more popular than crowding everyone into the few mega-hubs.
So I could imagine a TTBW that fits into a 787-size airport – or smaller – could serve a similar market. Open up long-range point-to-point routes that don’t see the pax volume to merit a widebody, but are too far for a 737/A320 class plane to be viable.
Huh, I never thought to look at it from the perspective of the size of the airports. Its a similar argument with the rail road gauge width and horse cart axels.
I remember seeing a study a while back where they took a bunch of college students (some with engineering backgrounds most without) and had them design the “ideal” airport experience. The students were broken up into groups and with a the exception of a few details all most all of the groups came up with the same solution.
The airplane docked with the terminal and the entire passenger section slid into the airport where the seating area would normally be. Passengers could get up and move around as needed prior to the flight and board at their leisure in a secure area. When it was time to board, the whole passenger section slid back into the plane. Similar to the Fairchild XC-120 Packplane.
But, like you said, that kind of change would take a radical redesign of airports and infrastructure, never mind the engineering hurdles.
Hopefully Boeing has sorted out their problems with incompetent engineers and cut-rate assembly.. Anybody wanna take the first ride on a new model designed from the ground-up by those people using technology that radically diverges from time-tested airliners?
I’m sure they’ll have a single, marginally FIKI-rated AOA vane that corrects everything without flight crew training…
They fired their CEO to restore faith in the company. Guess that wasn’t enough. I wonder if Lockheed remembers how to build airliners?
It has never been a problem with competence with the engineers. Boeings problems started when their new management moved to Chicago and they were just bean counters with no appreciation for engineering.
This. I can’t state enough, this.
Not cut rate assembly, but share holders that want more return on their money in a short period of time.
Don’t airliners store fuel in the wings? Would smaller wings still have enough space?
Got essentially 2 wings. Lotsa fuel storage
It’s one of the issues noted in that picture from Boeing.
it says ‘fuel volume’
Look at the larger picture – the size of commercial aircraft faces a practical commercial limitation in that they have to fit into a “box” at the gate. Wingspans are limited to ca. 262 feet/80 meters. Boeing is already putting folding wingtips on the 777x to accomodate this, and it allows more wingspan, more lift, and more things carried – and more revenue. The much-loved-by-passengers A380 faced all sorts of limitations like this – forcing it into a somewhat odd configuration, and to a certain extent dooming it as a world-beating cargo aircraft – almost too much volume for the lift the single set of wings could generate.
In order to stuff more people/cargo into a pressurized metal tube that fits into trillions of dollars worth of global infrastructure you have to increase the wing area without increasing the wingspan. “Biplane” it is.
Doesn’t apply to B52, designed in early 1950s, will probably serve into 2050s. Engineer who was a toddles when it was being manufactured is now an elderly retiree living in Florida.
People back then could in fact engineer things instead of just outsourcing the job :-)
sure as long as you don’t worry about fuel economy or cost of maintanence
This is the endless thankless job of engineers these days. We are largely making incremental gains and improvements on designs to maximize efficiency and profit. This leads to pushing boundaries that don’t look like boundaries to the ill-educated, who don’t understand the complexity and the problems being overcome fully – they then think we are useless. When we do get to work on something ground-breaking and new, everyone says “finally, they found engineers who could design something groundbreaking”. Same people, folks, just different drivers, try not to be so dismissive of people’s work when you don’t understand it (applies outside engineering too!).
The only reason any of the older combat planes are still flying active service upgraded vs replaced entirely is with the fall of the Soviet Union nobody wanted to keep spending as much time and effort on newer better platforms for every job with all the R&D to get over even more initial teething problems inevitable to a new production. You build new only for the roles you really need it.
Equally you don’t keep flying the expensive old stuff you don’t need so much anymore. SR-71 for instance has no real replacement but isn’t still in use, but it would be one or other if the world situation through the 1990’s demanded its replacement – good as satellite can be they have limits an aircraft doesn’t, making them usefully complementary.
Its not that the old gang produced better stuff than modern folks can at all!
(Heck in the case of WWII Tanks The Old Gang really didn’t do well with the TOG…)
But if it’s agreed and widely (pardon the pun) adopted then it would take off (again – the pun).
I think it could be done since it’s only a widening of some things and some tweaking, costly but not a 100% change.
But perhaps a 20% gain in lift is not a realistic number to do it for, you’d need more – or alternatively the politicians would need to force it. But in terms of greenhouse gasses air travel is only 1.9% to start with, and it’s already dropping by means of other tricks, so there is no excuse to force it since that brings little gain and lots of cost, and the work would create its own impact, with all the concrete and machines.
You should learn the difference between capital and interest. The CO2 overweight capital is already 2x what is required.
Yet, reducing the fuel consumption by 30% only reduce the interest by 30%. You need MUCH more than 30% reduction in CO2 production, you need >100% reduction in interest, that is CO2 production. But asking to go from 100 to -10 is a challenge that you can’t win, so you perform a small step, from 100 to 70, then from 70 to 50 and so on.
And that’s just one sector, even if it’s only 1.9% of the total sectors. All sectors must deflate to below 0. Since there’s a lot of money in Air transportation, there’s a good reason to spend efforts here.
^^^^^^^^^^^^^^^^^
This is what greenies actually believe.
My point was that the government will only force the companies if they have sufficient (in their view) excuse to do so. And if the benefit is negligible and the cost high then their economic advisors will point out that there are many other things that they could direct their efforts towards with much greater gains.
Although they could of course simply raise the tax on airline fuel through the roof, thereby making any gram of fuel saved of interest to the airlines who then will embrace any saving trick they can find.
Thing is though, the politicians like to travel by air a lot, so they tend to not push too much.
So if politics is not a factor then the economics of the airlines becomes the factor, and they will see the issues with the airports not being suited.
And even with folding the wings as some suggest, there is a limit to that too, it can’t stick out a mile since then you can’t get to the terminal to offload/load passengers, and it will catch wind, causing all kinds of issues.
As for my view on the CO2 thing, I think polution is bad in general, but I’m not convinced that CO2 is the main/only factor in any climate issues.
Fuel efficiency gains just result in cheaper, then more air travel, and more CO2 emissions.
The math doesn’t add up for me. Let’s assume fuel is 50% of the cost of a ticket. And we can cut the usage of fuel in half then the ticket will be 12.5% cheaper and the other 12.5% will be go to increased margins. I don’t think air travel will more than double if tickets got 12.5% cheaper.
Yes, unless efficiency gains allow you to switch to a less energy-dense fuel like ammonia and then also produce that ammonia from carbon free electricity using something like the recently researched reactor that uses phosphonium salts as a proton shuttle in the production of ammonia.
fueling plane with ammonia would be utterly insane
Right, so just use folding wings. This can also be deployed on smaller jets, like the A220. If wingspans are limited to 80 meters, then just increase folded-wingspan right to that limit and use it for smaller fuselage jets.
https://simpleflying.com/boeing-777x-wingtips-benefits/
“Just” use folding wings. This article already explains that there are structural issues with the high aspect ratio wings, putting an arbitrary fold in the middle of one is not a simple task.
People allergic to solving hard problems and the word “just.” ;)
Hard problems are not showstoppers. “Have to” is wrong when you *can* add a fold.
Hard problems are, in fact, often show stoppers.
Usually comes down to material properties. Have to wait for metallurgy to catch up to your ambition.
I don’t trust the concept. In a situation of a combination of roll, yaw and air speed there could be a failure of the brace ,wing, or both.
Yeah… same as the wing of any aircraft. They’ll have to rate it for a certain load and a certain force, at which point it’ll be the same as the wing of any aircraft with a similar rating.
Biplane with large gap between the wings and high aspect ratio will then do even better.
What about flaps, stall speed etc?
HaD covered this already not long ago.
High aspect wings work ok/well with gliders because gliders typically fly very, very slowly compared to a jet air liner. When climbing in a thermal, for example, typical airspeed is just a couple of knots above stall because that is the speed of minimum sink. Somewhat faster but still positively snail-pace compared to a jet is L/D max, which is the point of most lift for least drag, meaning highest glide ratio.
There are videos of high-speed testing of gliders when the long, skinny wings start to oscillate and look like they are going to shatter off- torsional rigidity is a huge problem but, again, considering the relatively slow speeds of gliders, not insurmountable.
Gliders also weigh very little and do not have pesky fuel or engines taking up space and forcing aerodynamic compromises.
As noted above, the wing root area is also very sensitive to turbulence so introducing extras with a truss will be complex.
TL:DR A wingform that works well for gliders is gonna be a heck of an engineering challenge to adapt to passenger aircraft of any size no matter who is doing it.
The U-2 / TR-1 aircraft are not exactly low speed gliders. They are however notoriously difficult to fly.
I would also like to point out that a L/D max of 15 or so is nothing to sniff at for a passenger jet, or even a glider. An older but still amazing trainer, the SGS 2-33 and the single-seat version, the SGS 1-26 are arguably the most popular gliders ever produced and have L/Dmax of about 15. They are tons of fun! Ironically, they can stay up on light lift days when high performance gliders all land out because their minimum speed and low wing loading means their minimum sink rate is much lower.
Also, forgot to say above, but good article. Thanks HaD.
That’s a good point. The wing may well perform incredibly at speed and altitude, but slow speed necessary for takeoff, maneuvering and landing will be a real bear. Only way to make that work would be a hugely complex set of flaps, slats, etc all of which are already complex in big wings, let alone trying to fit all that in tiny, long, skinny wings. And all likely negating the benefits at cruise.
The year is 2023 and no-one has mentioned that in 40 years the only things that will change in aviation are distance, speed, structral integrity and the type of fuel used. Engines will be built of weigh nothing ceramics. Fuel will be hydrogen /helium / algae mix or if Richard Branson gets his way- used fish and chip shop oil, fusilages will be made of composite Kevlar/ aluminium X 10 strength factor and Sydney to London with 400 passengers in 6 hours. The only things that won’t change are check in and bag drop speeds and paying half the GDP of Belize for a coffee and cake.
Bah. Bring back zeppelins.
Anyone who’s ever looked out at the wing on a commercial airliner has probably noticed how much those things flex, especially in turbulence. With a more rigid structure – more of the motion would be transferred to the fuselage, causing more metal stress, and certainly more passenger discomfort, no?
I’m with you! Just imagine the untapped hipster capital in dirigible travel.
Could work together with Bill Burr’s ‘Sink cruise ships until traffic gets better’ plan.
Wasn’t there a dynalifter idea or something a couple years back? Like a fat, wide, almost double zeppelin thing that needed a runway but TAS was like 60 mph? I remember the idea was for transcon cargo that needed to get there faster than a boat could offer, but cheaper than a plane. Shockingly I don’t think anything ever came of it aside from a prototype.
The Airlander 10 is, according to an article on FlightGlobal dot com cited on Wikipedia, under production and reserved for delivery to Air Nostrum some time in 2026.
That is correct. The U2 is/was flown by only extraordinary pilots. At cruise, the difference between stall speed and structural failure was only a few knots .. citation needed but I heard that somewhere. The design and use constraints of the U2 and a recreational sailplane, or any of those two to a passenger jet are essentially useless.
> At cruise, the difference between stall speed and structural failure was only a few knots
Close, the U-2 flew in the “coffin corner”, which is a region of the flight envelope with a small difference between stall speed and *critical Mach number*. At the critical Mach number shock waves begin to form on the top of the wing, causing airflow separation and potentially a stall due to *high* speed (which pitches the nose down, increasing speed, increasing the problem). And *that* could lead to exceeding structural limits – but the important note is that it’s a controllability limit, and the structural limit that you run into next is the result of loss of pitch control.
In any case, your point stands, that the U-2 is only slightly comparable. An airliner would have to be designed with a higher Mcr margin to ever get certificated.
Small correction to the article. The U2 is still flying and appears to have many more years to go so it should not be referred to past tense.
You’re absolutely correct; this comment started as a much longer ramble about modern developments vs the U-2’s 1950s design, and my brain was still on the past tense of “…was designed to fly in the coffin corner…” when I pared it down.
I’ll just claim I was channeling Mitch Hedberg… “It used to fly like this. It still does, but it used to, too.”
As a firefighter I can only think of bad things about trusses and my fear is intensified here. What happens in an engine failure, wing fire, cracked members, etc. A truss is compromised 18 in each direction if just one truss goes. What happens in mid air incidents will it just break apart like a house fire?