[Wendy] asked a very good question. Could putting liquid resin into an ultrasonic cleaner help degas it? Would it help remove bubbles, resulting in a cleaner pour and nicer end product? What we love is that she tried it out and shared her results. She purchased an ultrasonic cleaner and proceeded to mix two batches of clear resin, giving one an ultrasonic treatment and leaving the other untouched as a control.
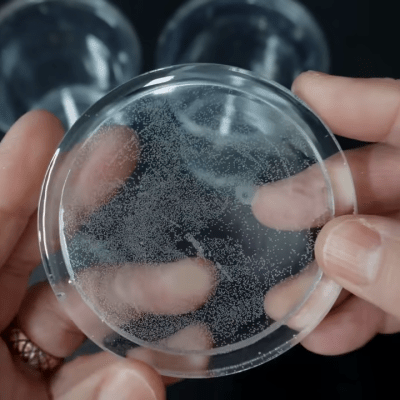
The results were interesting and unexpected. Initially, the resin in the ultrasonic bath showed visible bubbles rising to the surface which seemed promising. Unfortunately, this did not lead to fewer bubbles in the end product.
[Wendy]’s measurements suggest that the main result of putting resin in an ultrasonic bath was an increase in its temperature. Overheating the resin appears to have led to increased off-gassing and bubble formation prior to and during curing, which made for poor end results. The untreated resin by contrast cured with better color and much higher clarity. If you would like to skip directly to the results of the two batches, it’s right here at 9:15 in.
Does this mean it’s a total dead end? Maybe, but even if the initial results weren’t promising, it’s a pretty interesting experiment and we’re delighted to see [Wendy] walk through it. Do you think there’s any way to use the ultrasonic cleaner in a better or different way? If so, let us know in the comments.
This isn’t the first time people have tried to degas epoxy resin by thinking outside the box. We’ve covered a very cheap method that offered surprising results, as well as a way use a modified paint tank in lieu of purpose-made hardware.
It also doesn’t work to agitate FeCl when etching PCBs – using a sealed plastic container in a water bath to protect the cleaner, obviously.
That’s interesting, unexpected and disappointing. My cheap ultrasonic cleaner can etch holes though aluminum foil in a few minutes. I tried that because I saw it in a video about ultrasonic cleaners.
Vaccum negative pressure with heat is what they use in the herb oil industry to remove chems / solvents. Maybe coupling ultrasonic, vaccum and heat would be the ticket..
Yeah. Pull a mild vacuum – slowly or you get resin-foam.
To create a vacuum to test model rocket altimeters and parachute deployment electronics, I use one of the hard, translucent, semi-hemispherical food storage containers with rubber seals and clips to lock the lid on, drill a hole for a car tire valve stem with valve removed in the side, and use a cheap handheld transfer pump with the plastic hose just friction fitted over the valve stem.
https://www.harborfreight.com/multi-use-transfer-pump-63144.html
That might be useful in degassing small amounts of epoxy, too.
I’ve pulled a vacuum to 10,000 feet (3,000 meters, which is as much as I needed) with no implosion, but your SAFE mileage (kilometerage?) may vary according to your container.
I use a vacuum sealer pump for sandwich bags and a mason jar of course this is before I pour so it’s still in the mix cup. You just have to be care ful not to collapse the cup.
Pressure pot works and is less hassle.
As I understand the functionality of a true ultrasonic cleaner, it intentionally creates cavitation within the fluid. That seems like the opposite of the goal. Don’t know if the ultrasound can induce cavitation in something as relatively thick as epoxy.
Possibly one of the cheap vibrating plastic jewelry/eyeglass cleaner might be able to shake some bubbles out.
Well.. that tracks pretty well with their results.
You’re generally better using a pressure pot than attempting to degas resin.
At my old job at a DuPont lab, we would regularly use a temperature controlled water bath that had an ultrasonic feature for resins. The goal was to clear out the bubbles to make a consistent viscosity measurement, so it was for a different reason.
A long time ago, in a galaxy far, far away, I worked at a place casting epoxy parts for some equipment that the company made. We used vacuum to degas the silicone for making the molds and to degas the filled epoxy that the parts were made from. It worked well in both cases.
Me to, watch the silicone rise in the vacuum chamber, then bump it down, repeat until no more rise.
Resin casters use heat to dispatch bubbles. They whack the uncured resin in a microwave, which makes it hot and very runny. Bubbles rise to the surface, and any that remain there, are burst with a gas torch. Same method does not apply to moulding silicone. Pull a vacuum on those.
My ultrasonic cleaner has a “Degass” function to remove air bubbles from fresh water. May be it would work also for that purpose with resin?
Very interesting! Please try it and report back!
Sorry, but i don’t have resin printer.
In my experience, a pressure pot or centrifuge works best to remove bubbles from mixed epoxy. Vacuum can introduce more bubbles as some of the components in epoxies can boil at the lower pressure.
Ultrasonic homogenization absolutely work for bubble dispersion. You have to small of sample or too much power. The bubbles your seeing are from cavitation.
There’s a machine called a “Resiners” that uses vacuum and vibration. Alternatively an ultrasonic cleaner with a degas function could work. Ultrasonic first to dislodge bubbles, but cause some cavitation (which is the point) then degas. However, I’ve had bubbles get worse through vacuum treatment. It causes them to merge and grow, but if they can’t escape, they cause a bigger problem. Ultimately, although the most expensive solution, a pressure pot+air compressor is best.
First you pull a 26 to 28 Hg vacuum to pull the air out of the mix. Then put it under at least 40 psi pressure to cure. Heating may cause an exothermic reaction of two part urethane, epoxy, pollyester and over heat to point of a bad cast. Any vibration will help the bubbles to release from any surface.
I use to cast absolutely clear headlight lenses for the automotive industry for show cars and lighting company photmetric test models. If you pour your mix into the mold and the mold is in a vacuum chamber, you can’t trap air bubbles in the cast. There is no air in the mold to trap bubbles if it’s in a complete vaccum. Note the mold has to be created by de-airing in a vacuum and cured while under pressure as well if your using silicone molds.
Machines like a FlackTek mix and de air at the same time. Used them for thick silicone lsr mixing at my old job. use the right tools!