The widespread availability of inexpensive 3D printers has brought about a revolution in what can be easily made at home. However these creations aren’t perfect, particularly when it comes to the adhesion between their layers. Aside from structural failures along the layer lines there is also the question of those joins being permeable, limiting the possibility for waterproof or gas proof prints. It’s something [German Engineer] has tackled in a new video, in which he’s looking at the design and preparation of small propane tanks.
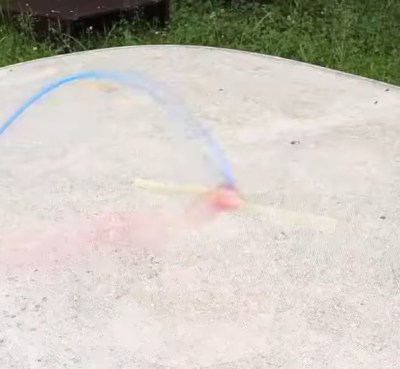
The attraction of propane as a fuel is that it liquefies easily on compression, so a propane cylinder or tank will be an equilibrium of liquid propane with pressurized gas above it, whose pressure depends on the ambient temperature. This means that any tank must be expected to have a working pressure somewhere between 150 and 200 PSI, with of course a design pressure far exceeding that for safety reasons.
Filling a 3D printed tank immediately results in the propane escaping, as he demonstrates by putting one of his prints under water. He solves this with a sealant, Diamant Dichtol, which is intended to polymerize in the gaps between layers and create a gas-tight tank. A range of three tanks of different thicknesses are treated this way, and while the 1 mm thick variety bursts, the thicker ones survive.
It’s clear that this technique successfully creates gas-tight prints, and we can see the attraction of a small and lightweight fuel tank. But we can’t help worrying slightly about the safety, for even when the material is a lightweight 3D print, high pressure equipment is not to be trifled with. Tanks do burst, and when that happens anyone unfortunate enough to be close by sustains nasty, even life-threatening injuries. Use the technique, but maybe don’t hit it with high pressures.
“but maybe don’t hit it with high pressures”…
It might be a good idea to define “high pressures”. Even in the range of 30 psi / 2 bar – a typical automotive tire pressure – a rupture with fragments might be life-altering in a bad way.
I applaud experiments like this in the pursuit of knowledge, but I worry about some eager beaver trying to replicate them without understanding and mitigating the dangers.
20# propane tanks here in the USA are limited to 12 years of use.
In the case of these tanks, I would not want to put volatile fluids or flammable gasses in them.
They’re also HEAVILY regulated by material type, tests on that material to prevent any El Nassir situation, hardware and valve requirements, pressure testing and safety margins, and failure modes designed to be as safe as possible.
The requirements are extensive.
The requirements are NECESSARY.
This is lethal irresponsibility.
The requirements are written in blood. This guy would do well to remember that.
id also worry about embrittlement, propane can get pretty cold in its liquid form. i have a bbq grill that is always blowing up because the regulator freezes. and the tanks themselves get pretty cold as they are emptied. pla is pretty brittle when you aren’t putting it out in the cold.
You do not have a gas fired BBQ grill. By definition.
BBQ is hot smoking.
What you are, sort of, doing is grilling. Damn gas grillers. Cue Hank Hill.
Just because the smoke doesn’t originate from the fuel, doesn’t mean there isn’t any. Besides purposefully incorporating wood chips for smoke, there are also the stainless steel “flavorizers” that produce smoke from the fats coming from the food itself.
My homemade grill uses a hybrid of propane and charcoal, with a homemade flavorizer/heat spreader, and makes delicious BBQ.
You _can’t_ BBQ on a grill.
This is sheer madness. Pressure vessels and DIY do not go well together. Especially 3D printed stuff with no quality control. How does such a vessel degrade over time?
Too many people have already died or sustained serious injuries from things such as exploding car tires or abuse of airbags just to name a few examples. Just watch some youtube video’s to get some idea of what the dangers are.
If this method can be used to improve layer adhesion and make parts stronger then I’m interested, but I’d leave it to someone like CNC Kitchen before I watch video about this. I’m not going to watch a video about some idiot putting propane in a DIY 3D printed pressure vessel. I’d be happier to give him the Darwin award. At least (probably) nobody else gets hurt, but I’d still feel sorry for friends and family.
I have no problem with DIY pressure vessel, shoddy DIY pressure vessels made from a 3d print and some sealing goo on the other hand… You would think unless these folks are specifically seeking after Darwin awards they would have managed to learn from their peers about creating pipe bombs accidentally.
Its not that hard to make a pressure vessel that is safe if you have some understanding of the physics involved or just work to a properly calculated design with the right safety margins for the task at hand.
It’s exactly self overestimation such as your remarks that make this dangerous.
Just try this answer:
How do you guarantee material properties of some self 3D printed device?
Without known / guaranteed material properties, any calculation you make is useless, or worse (dangerous).
For 3d printed plastic, it’s easy to assume some material properties, add some safety factor, do some calculations and even pressure test it. But that is still no guarantee the thing won’t explode half a year later due to UV, creep, weakening from chemicals or other causes. And it gets worse when other people get involved (given away, sold or found in an attic).
Some 150 years (probably more) ago and after a bunch of explosions for example quite strict rules came into place for steam vessels. Steam vessels have to be made from certified steel just to be able to guarantee a reasonable safety level. You’ll never get a steam vessel certified if it’s made from regular construction steel. Even back then lives (or material damage?) was considered important enough to put some strict rules in place.
Even in the DIY marked for model steam engines there are ways in place to guarantee some minimum safety, but the way certification for such vessels work is dependent on which place you come from. You could try to get some information from DIY clubs how they think about steam vessels.
You didn’t read his comment closely enough. the first section mentions how 3D printed plastic vessels are Darwin award worthy mistakes and the second mentions how you can indeed create pressure vessels with safety considerations using materials like you mentioned AKA metal AKA not plastic.
Yes very much this. Use the right materials for the job at hand and you can make one safely. Though it could quite easily still be plastic for many things, you just need to actually know what the operating conditions need to be – water pistol for instance frequently have plastic pressure vessel and are perfectly safe.
Maybe one day not too far from now home 3d printed pressure vessels will be very possible, but right now at least the proven designs and well categorised reliable materials with which you can actually know their material properties don’t exist, and so rule out any of the home printing technologies really.
A ‘dry ice bomb’ (2 liter bottle) is another example of an improvised plastic pressure vessel that can be used safely.
The trick is to sit on it as it strains. Use scrotum/ladybits and butt cheeks as reinforcement.
Danger is acceptable.
Bingo. Fearmongers need to grow a pair. We would never have powered flight, space travel, sea travel, etc if most humans took such a risk averse attitude.
“We would never have powered flight, space travel, sea travel, etc if most humans took such a risk averse attitude”
Let’s not forget carbon fiber deep ocean submersibles.
And even if you have a properly calculated and tested design, different reprints may have tiny defects that could fail catastrophically.
I’m not usually on the side of people complaining about safety in the comments, but… yeah.
This is useful information but I wouldn’t want anyone to replicate it without understanding the risks.
My biggest concern is that although the pressure testing in the video is useful info, you’d need to do a *lot* more tests to be confident those results are consistent, and that still won’t tell you anything about durability over time.
Commercial plastic and composite pressure tanks often have a maximum rated lifespan, and even metal ones need to be re-tested and re-certified every so often.
Even at relatively low pressures, the failure mode can involve violently flinging small plastic parts at speeds that can penetrate the human body. One of the problems with plastic is it doesn’t show up well on x-rays, so the doctors will have extra fun digging it out. Of course, this is an issue with non-3d-printed plastic tanks as well, but at least if you use something like PVC pipe, it comes with a formal, well-tested pressure rating, and as long as you glue it together properly you can trust that rating.
On the bright side, one of FDM’s (literal) weaknesses may at least make it safer than using, say, a soda bottle – the bond between layers is the weakest point, so my guess is it’ll usually fail as we see in the video – by separating into several pieces at a layer boundary – rather than becoming jagged plastic shrapnel.
also of course worth noting that there may be local laws against filling an uncertified pressure vessel with a flammable fuel, or at least using it to store or transport said fuel.
Hackaday with the literal quote “Use the technique”
WTF.
“Use the technique” to seal a 3D print but immediately after that they say “not with high pressure”, perfectly valid technique to seal a print still.
Not being able to see plastic in an x-ray is a highly repeated myth that just isn’t true…
That reminds me. I really do want to buy a cheap x-ray machine. I should probably get my Geiger counter calibrated first though.
Chapter 6 from Shigley on Fatigue Failure is a wonderful reference.
From paulvdh, above…
“This is sheer madness…”
NOone could have put it better than this gentleman has.
Propane/LPG is one of the most destructive, most easily abused and mis-used substances readily available to the general public (in the USA; can’t speak to the situation in the ROW); paralleled only by the combination of the too-easily-available combination of the [still] commonly-available lawn-and-garden fertilizer ammonium nitrate (33-0-0) mixed with diesel fuel. (cf. ‘Alfred P. Murrah Federal Building’, which was destroyed, with approx 700 casualties, due to the use of this combination).
Are you aware, Hackaday, that towing a camper-trailer behind your car in the U.S. can result in a VERY expensive detour [sometimes to jail]–a detour sometimes consisting of hundreds of miles– , as most of these trailers contain LP “bottles” (20-lb, or larger), which are strictly forbidden on / in even the shortest of tunnels and bridges. Violation of this stricture can result in fines of hundreds of dollars or more, and even jail time.
Tell you what, Hackaday…
When you CANcan publish an article dealing with the design and construction of propane tanks which meet or exceed the standards set forth in OSHA (Occupational Safety and Health Standards) Standard Number 1910.110 (“Storage and handling of liquefied petroleum gases”), get back to me.
Until then, keep up your outstanding work on your usual fare of entertaining and enlightening–and less dangerous–articles…excepting those, of course, which must entail the possibility of the inhalation of rosin fumes, due to soldering.
You are aware this video is ROW. And specifically a place safer than USA? You appear to want a restriction of free speech because instead of requiring safe propane tanks USA restricted freedom of movement but allows unsafe tanks.
People do safe things, people do unsafe things. People do marginal things. People hack things. People document the hack. People discuss the hack (sometimes more valuable than the hack). This guy did a dangerous thing. I’m glad he documented it and Hackaday publicised it. Doing dangerous things in secret is more dangerous than telling the world, as per your ANFO example.
Might be fun for target practice, but I strain to think of any other application. I do appreciate the tenacity some people have for using FDM in ways that are simply not suited to FDM.
Not even that. Will just vent. Not a tannerite substitute.
If you want something reactive for target practice, just put some chalk powder in a pop bottle and pressurize it with air. It will make a dust cloud and a nice bang when shot.
It’s totally worthwhile to investigate how far you can push printed pressure vessels. There are lots of ways pneumatics or hydraulics could be useful in printed designs, and if you need 30psi then it’s helpful to know how to make a tank that fails at 150psi.
But framing it as a way to make propane tanks is way over the line. Everyone uses propane tanks, most don’t really get how dangerous they would be without regulation, and anyone can watch this video. The only question is how many maimings it will lead to.
YouTube gene pool needs chlorine anyhow.
total waste of time(for propane/fuel)
the certifiction procedure involves propelling a full propane
tank through a concrete block wall@100kph
they dent,of partialy crush,but must not suffer a catestrophic failure
and then there are the DOT tanks
in any case the tank must not turn into a bomb durring
a car crash
right?
Cool idea, but just not for the current plastic and resin printers, better safe than sorry!
You know they 3D print hundreds of parts for commercial airline jet engines, right? Look up the GE9X if you don’t believe me.
Perhaps you meant “desktop FFF printers are for art and prototyping”, but what you’ve written is pretty absurd on its face.
You know they print using special filament, on special printers, and pieces designed by aerospace engineers, with proper testing and certification, right? Look up the AS9100 if you don’t believe me.
The vast majority of 3d printer projects featured in HaD are not made by certified professionals. While some people can see when a project is dangerous while being fun to watch about, some people don’t.
This is absolutely the most idiotic and dangerous thing I’ve ever seen on this site, and that’s a high bar.
Failure to point out the lethality this project is irresponsible and vile incompetence by the author and editors here.
The regulations for pressure vessel design are hundreds of pages long, and every one of those has been written in fire, shrapnel, suffering, blood, and death.
Where are the 3d files for that hat that points all the shotgun shells toward your head?
Where are the DIY suicide bag instructions?
Both of those are safer than this, because they’ll only kill the person wearing them.
“High bar”. I hope that phrasing was deliberate. (ba dum tis!)
“This is absolutely the most idiotic and dangerous thing I’ve ever seen on this site, and that’s a high bar.”
Printing a handgun.
Using a microwave oven transformer to build a spot welder
I actually built said spot welder. I do not see anything wrong with it.
Have to chime in on this with a couple of things not mentioned yet:
1) Propane and butane are excellent solvents for solid hydrocarbons. While they may or may not dissolve the plastic used for this project they will almost certainly leach out at least some of the all pervasive plasticisers. Many plastics are extremely susceptible to solvent embrittlement for this reason.
2) many plastics suffer from cold embrittlement. What happens when propane is drawn off a tank whether on purpose or from a leak? It gets frosty cold.
3) shape is almost everything in a pressure vessel and at 200psi in the sun that thing will try to be a sphere any way it can.
4) someone trying this probably doesn’t know that you are only allowed to fill propane tanks to 80% capacity to begin with so you don’t get really big pressure changes from heat with a failed relief valve (hydraulic vs vapor pressure) most of the kids that fill my tanks don’t know….
and lastly … why? by the time you get the right plastic and make a valve and a relief (over pressure) valve that can hold up it will be heavier than the 1Lb, 7.5 Lb, 20 Lb tanks available (see SpaceX carbon fiber tanks).
I’m all for personal freedom, but please just don’t on this one
THANK you. I’m guessing even this bozo would know better than to soak a print in xylene or hexane and expect it to maintain its strength for long. Propane, compressed to a liquid, will attack nearly anything that hexane will.
Sounds like a lot of good ideas for the next video.
The nannying naysayers are swarming, must be a project season.
Small amount of butane can be used as a convenient propellant for pneumatics. It’s a gas frequently used in airsoft. Can be handy for little actuators like a syringe piston.
Larger pressure vessels are indeed ill-advised. But it is scale that brings the danger, not the principle.
If the sealant is elastomeric, and binds well with TPU (and more generally TPE, though these are more diverse chemically), the technique can be used for a different kind of pressure vessels, the actuators for soft robotics. I am disheartened nobody came up with this.
This is the Titan submersible, but in reverse.
As others have said, a completely dumb idea.
I was just gonna say that… Why not 3d print yourself a submarine and go see the Titanic? Very bad idea, should have never been published.
Well if you watched the video, where the idea came from was a 3d printed remote sub, that was designed to go down to 300ft and with stand the pressure
Haven’t seen the clip (and won’t) but from the ~50€/l price tag on “Diamant Dichtol” I’m guessing the video was sponsored?
But aren’t the gasses such as methane, ethane, propane are often used as solvents for organic materials?
This is super useful. Have you ever heard about ‘blow moulding’?
Print a shape, submerge in warm water, pressurise with air to expand certain parts of the structure. This is a super interesting production method that can be used to quickly print small shapes which then expand into larger forms saving time, material and create shapes that fill a certain space. See also dl.acm.org/doi/10.1145/3544548.3580923
That’s not how blow molds work.
Thou shalt not F with pressure vessels. I wouldn’t be messing with this stuff personally, especially with propane.
3D printed gas bottles is crazy. 3D printed submarine drone – that’s a good application for the sealing technique. Something like water hose connectors would be fine too, as with incompressible fluids the explosions don’t have much energy.
There’s a video somewhere of students trying to 3d print a small sub model of the one that imploded recently on the Titanic site. They are using a similar sealant
The only feasible (safe) use I can see is for a small membrane pressure accumulator/ shock dampener in a small DIY air compressed project e.g. automating something with reasonably low pressure. Keeping the volume small and walls thick would work. Anyway the polymer sealants for 3d prints are not cheap at all. It would be probably easier and safer to make it in aluminium/fiberglass. Publicity stunt for the sealant?
The use I saw was just a test of air tightness. If I want something airtight it’s a bonus if it can take many bar. Let’s me know my safety factor. So if I want to print a non safety critical part I know I have a technique that works.
Hydrotesting. Every single pressure vessel that I own is periodically hydrotested. They fill it with water, and pump it up. It’s easy to get to the maximum fail pressure without storing lots of potential energy. If, at test pressure, the tank expands too much or springs a leak, they send it for recycling.
Safety. I will give the OP the benefit of doubt that their explosions have cultivated a respect for the dangers here. Ringing in the ears, and stinging bits of flak will do that. Small vessels is the way to go, and ear protection, and eye protection.
FDM Study. What a great way to systematically test adhesion parameters! Fail pressure for a sphere of t thickness and fail length at a known temperature, would be some great data. Someone please do this.
I’m a certified ASME pressure vessel engineer, and all I can say is that this is ludicrous. The ASME code was created because boilers on steamboats were being created willy nilly that would explode and kill people. This is going back to the same scenario. You must have proper training for those designing the vessel, inspection of the build, and testing of the build to ensure it’s safety. I’m not against developing new ways to make a pressure vessel, but it should only be tested in a certified lab by professionals. Otherwise you may be putting lives at risk, because you don’t understand what equipment is needed to ensure nobody gets hurt.
Metal fatigue is bitch.
Beware black pipe barrels.
Good for (harvesting money/saving innocent guns) from gun buy backs, but you never know when they will explode. Magnaflux is cheaper then medical bills.
If in doubt, make it stout and out of something you know about. However, if I had a metal 3d printer I think I would (through the legal channels) be 3d printing fun parts, including barrels. (Word change was autocorrect but seemed fun enough)
I like it. It’s well documented, it’s educational. Whether to use it as an example of what to do or what not to do is a different matter. And I say that all as a safety professional who deals with pressure vessels as part of my job.
I for one appreciate the article and the YouTuber for this. Everyone is focused on the dangers here (and I get it), but this information could be helpful to me because I struggle with parts I want to be liquid tight too: custom ABS caps for steel parts that get electroplated (so submerged in a tank). Initial tests showed the material held up to all chemicals but I had a leak somewhere despite having integrated chemical resistant o-rings. Our plater suspected it’s the ABS itself being permeated, and this gives me some options to look at. Unfortunately we’re a bit boxed in on this project – the steel parts are unusually shaped and none of your typical push on or thread-on caps work well enough. If we get even a few droplets into the inside bore of our steel parts the heat cycles and chemicals severely damage and rust out the part so badly it can’t be brushed or buffed away. So thank you for this study and write-up!
I have questions.
He said the vessel he made would work for his application but the first attempt of a small copper vessel was too heavy. What’s the application?
Also mentioned the tank would need to hold propellant for 10 minutes.
What’s light that runs for ten minutes?
The initial seal test (white filament) sealed with “dich-tol” (te-he) penetrating (te-he^2) the filaments was filled with butane. Tested whether it can hold the liquefied butane for 24 hours. That test was mostly successful after lots of dichtol on the inside…penetrating the tight gaps.
Then he pressurized the vessels to much higher pressure and the thinnest wall burst…but not at the nozzle instead at the top where the wall angle made the steepest change, so interesting.
So he has designed and tested a vessel that may only hold propellant for 10 minutes for 144x that duration and roughly 3-4 atmospheres higher than he needs.
Seems viable for a single-use, small object that needs to hold fuel for ten minutes.
Finally, how does @Germanengineer1 have one video and his channel is from 29 march of this year? Nobody else snagged that username, impressive.
When you expand the time frame wide enough, all pressure vessels fail.
Would have liked to see some safety glasses.
I’m guessing the application is some sort of rocket or aircraft which uses the gas as fuel.
There are a ton of less awful ways to get a small tank that are at least as safe if not safer than this nightmare;
Small air suspension tanks from cars are at least pressure tested & certified (although not rated for flammable gas) and can be had cheaply from breakers. Also air tanks and parts from heavy trucks.
Likewise small fire extinguishers.
There’s small pneumatic & hydraulic cylinders, accumulators, and reservoirs on the industrial market.
There’s a load of very cool stuff that comes out of aerospace and sometimes makes its way to eBay.
Even soda bottles will withstand a surprising amount of PSI especially if wrapped in something like glass-reinforced tape.
Mmmmm nope!
Sure, I’m all for 3d printing MOST things. This… hey, if someone wants to entertain the rest of us with 3d printing themed Darwin Awards then awesome! Way to go! Besides that… I don’t think so.
This is the same reason I wouldn’t 3d print a gun. You can make it work. But unless your name is Domino it’s going to eventually blow up in your face.