We’re all familiar with supply chain issues as they relate to chips and DIPs, but anyone who has requested an estimate for home improvements lately knows that the problems extend to things like plywood, and probably tile, marble, and Formica. Faced with adversity when it came to renovating the kitchen, [3DPC] decided to have a go at 3D printing custom countertops instead of buying tile.
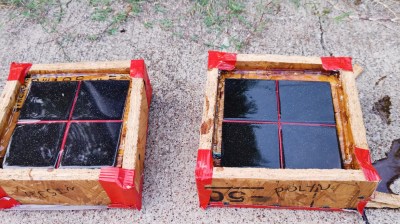
Since grout isn’t required here but is ultimately expected, [3DPC] beveled the edges of the tiles in order to allow for decorative ‘grout’ filler pieces that provide a nice contrast. That high-gloss shine comes from a combination of printing onto glass, the direction of the layer lines, and the resin sealer that [3DPC] hired a professional to pour. Because of these factors, the tiles have an increased transparency that makes them look super cool. Be sure to check out the brief build video after the break.
To be fair, this is not [3DPC]’s first 3D-printed home-improvement rodeo — he has already saved tens of thousands of dollars by printing instead of purchasing. For this particular project, [3DPC] calculated a total cost under $400 — a fraction of what a professionally installed countertop would have cost. We wonder how much he’ll save on tiling the bathroom, which is already in progress. We can’t wait to see it!
Are you still without a printer? Might as well make one that can use trash. Or if you already have a printer, just make filament from recycled plastic. It’s all here among the 2022 Hackaday Prize Round 2 winners; just let your imagination wander.
Continue reading “Style Your Tile With 3D Printed Countertops”