A lot of people assume that the product development cycle involves R&D, outsourcing to a Chinese manufacturer, and then selling the finished product. It’s almost ingrained in our heads that once a prototype has been developed, the next step involves a visa and airplane tickets. Here is a guide that will explore a few other options, and why outsourcing may not be appropriate for everyone.
First, let’s talk about goals. We’ll assume you’re not a large company, and that you don’t have a huge budget, and that you’re just getting started with your product and don’t have big volumes; a startup trying to sell a kit or breakout board, or a consumer electronics product. Your goals are the following:
- Validate your product in the market. Build a minimum viable product and get it in the hands of lots of users
- Get the most bang for your limited bucks. All money should go towards getting products out the door
- Reduce risk to your company so that any single failure doesn’t crater the whole operation and you can safely grow.
With that in mind, what are your options?
Foreign Outsourcing
Some people will say that you should start in China early because you will have access to assembly methods and components that can be used in the design process to ensure that the final product will be assemble-able and components easily sourced when manufacturing does take place, as well as forging a relationship with the factories that will make the product. No.
You want parts whose datasheets you can read and that can be reliably sourced, and you probably won’t stick with the same company that manufactured in dozens when you move up to tens of thousands. For all the speed that’s advertised, there are just as many delays for unforeseen and more annoying reasons. Remember that reducing your risk is a major goal of a startup, and is a serious consideration for any potential investor or customer. If you are outsourcing manufacturing, you are accepting an enormous risk, and worse yet there are no consequences if your manufacturer messes up any of the billion things that can go wrong. You’re putting the fate of your company in the hands of a manufacturer who doesn’t care and is half a world away.
It is my firm opinion that outsourcing to China (or other countries where manufacturing is stereotypically cheap) is only appropriate if:
- You are dealing in large volumes and your current manufacturing strategy cannot handle it
- You have been manufacturing a while and are looking to shave some of the Cost of Goods Sold (COGS)
- You have been manufacturing a while and have ironed out many of the assembly kinks, the test jigs, the molds, and the product has all the features the customer wants.
So why those three qualifications? Let’s look at each one:
Volumes
It is likely that you will start in small volumes, on the order of hundreds, maybe even a few thousand. Assembly lines take a long time to set up. Travel to a foreign country is time-consuming and expensive. There are many hidden overhead costs that are essentially the same whether you are dealing in small volumes or large. But with small volumes, those costs don’t amortize well into the volumes, so while the COGS may be small, the actual costs once all the hidden ones are accounted for can be significantly higher.
As a small company with a risky product that is just starting to get customer validation, the goal is to stretch money and time as far as it can go, and outsourcing can be really hard on both of those. Delays of a month in transit can be extremely rough for a startup on a time crunch, too.
Cost Savings
You may be able to get components cheaper, and you may be able to get labor on the assembly line cheaper, but that’s about it when it comes to cost savings. You still have to account for a lot of other expenses which are not in the COGS, and which will throw your accounting out of whack. Some of those costs include shipping.
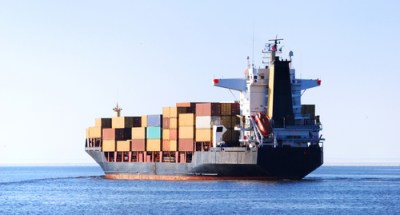
Although shipping by sea right now is super cheap, if you are in a hurry to get product, then air shipping is still and will likely always be expensive. You will have to pay duties, and you will probably have to fly and live over there for a while, both during the design process and the assembly line setup, and possibly even during the production. For a large volume where these kinds of expenses can amortize easily, it makes sense. But when you are looking at making a thousand of something, and a flight costs a thousand dollars, you’ve just increased your COGS by $1, so your spreadsheet comparing local vs outsourced should consider that.
Ironed out Kinks
New products have kinks. They may have certain components that are particularly difficult to attach, or require some skilled labor to assemble. Consistency is challenging, and rework is normal. It is during those first few rounds of assembly that it is crucial to have the designers participate, working on building jigs to aid in assembly, tweaking part designs as necessary to make it come together more reliably. Outsourcing too early means you miss this step, and have a bunch of low-wage workers who have fewer skills and no idea what your product does or how it works trying to assemble it. You will have lots of problems with this. It’s better to have experienced the assembly for a while and know where the hangups are, design them out or build tools to accommodate, and have a test and assembly process that you know works and that is as bulletproof as possible.
The Big Picture of Foreign Outsourcing
Look at the Pebble smartwatch, or the Coolest Cooler. These are projects that were so successful that they had to outsource production. Their volumes were too high to manufacture at home, but that meant that they had to skip the important step of manufacturing locally and ironing out the kinks. If you see where they struggled (or failed entirely), it is largely because they outsourced manufacturing their product too early and quality, cost, and timeline all suffered in the long run because of it. Most projects aren’t runaway successes like this and have a much more realistic opportunity for easing into production in larger and larger volumes, eventually transitioning to a need for large scale outsourced manufacturing.
Local Outsourcing
You probably have a manufacturer capable of handling your product within 100 miles. It might be a few different manufacturers; a plastics company, a PCBA company, a packaging company, and a fulfillment company. Check them out.
Yes, they will be more expensive than you’d like. But they’ll help you along the way, often with free and extremely useful advice. Your plastics guy is going to say: “that wall is too thin, that undercut means you need a slide, and I need to know what color and texture you want. Come down to our office and check out the book of colors and textures we have.”
They’re going to do that because they want high yield and no returns or scrapped product, so exacting specifications and easy to manufacture parts are in their best interest, too. You can’t rely on them to do all the work for you (not without paying for it anyway), but that kind of help is extremely valuable, and locally available. Yes, there will be some extra cost associated with it on a per part basis or in tooling, but you’ll have your parts sooner, you’ll be able to trust the manufacturer and hold them accountable if they fail, and you’ll be supporting local businesses, which goes a long way. If you scale up, then you can re-examine the relationship later, but when you are small and risky, finding a stable partner has lots of advantages.
You don’t have to outsource all production. Pick and choose the parts you can do yourself vs. things you can’t. Final assembly, testing, and fulfillment are probably entirely within your capability in your garage.
Manufacturing Yourself
This is likely more accessible than you think. We recently finished a series on doing PCBA using home-made tools, and in volumes up to a few thousand boards per month, it’s a reasonable possibility. Sure, there are limitations, so BGA and double sided boards are more challenging, but for most applications, it’s not far-fetched.
Some kinds of enclosures can be purchased outright from sites like New Age Enclosures or Hammond. Others can be made with a laser cutter or 3D printer for small volumes. Eventually you can work with a manufacturer and get maybe just the plastics done locally but the rest assembled and tested in the garage. The biggest reason to do this, though, is that it will force you to work through the assembly line process and figure out all the quirks of your product. You’ll develop all the jigs and make modifications to the design to aid in assembly, and because you are feeling the pain yourself, you’ll be a lot more motivated to do it. Because you are doing it in house, it’s so much easier to just change the design a little and make an immediate change to the assembly line accordingly.
Conclusion
Remember your 3 goals as a startup: get an MVP, spend every dollar on getting product out the door and servicing customers, and reduce risk as much as possible. Make your production decisions with these goals in mind, and you’ll be a happier and more successful company.
Should You Outsource Manufacturing? Short answer: No. Long answer: Hell no.
Poor or inconsistent quality can turn a good idea into a flop and a black mark on your reputation. At least make sure that if that happens, it happens on your watch. Don’t let manufacturers you don’t know and shipping chains you have no control over hold you hostage.
That’s a great TL;DR for this article. Thanks! I’d say there’s a huge difference between foreign and local outsourcing, though, and if you can’t manufacture a component yourself, it’s fine to use a local resource.
Ditto here on the “Hell No.”
We made a huge mistake in this country teaching that the “cool kids” all offshore production. It’s baloney. BMW makes every X vehicle consumed in the entire world here in this country. When Tim Cook says there isn’t enough talent to make Apple’s products here, It’s BS–we manage to make much of the world’s best Aerospace components here. Making a few laptop computers is not only possible, it’s straightforward.
It’s a mystery to me why publications devoted to making don’t focus on making rather than telling folks how to offshore. If you’re a maker, bloody well make something.
Over at my site, CNCCookbook, we’ve profiled numerous small businesses that manufacture their own products quite profitably in house. Don’t fall for the idea that you have to offshore your products.
http://www.bmwblog.com/2015/01/08/1-million-bmw-cars-assembled-chinese-plant/
“The plant is currently BMW’s sole global production site for X3, X4, X5, and X6 cross-over SUVs.”
https://en.wikipedia.org/wiki/BMW_US_Manufacturing_Company
“The automaker announced in 2014 an additional $1 billion investment in the facility that will make South Carolina BMW’s largest factory, with an annual capacity of 450,000 units.”
Given that BMW is a German company: Shouldn’t production in the US still be considered both offshore and outsourced? So I’d say they are not as good an example as Apple ;)
On another note (totally off-topic): thanks for CNCCookbook! Your G-Code tutorial was really helpful when I got started with a CNC mill.
LOL, lw2, I think it’s an even better example for why manufacturing in the US is competitive, which was my point.
I was only trying to make the point that manufacturing in the US and outsourcing are not always as contradictory as they might seem to some. It seems to me like their reasoning is close to the “rule” Miroslav posted below. They simply moved their manufacturing closest to their biggest market for these models. And I’d assume shipping for cars (1.5-2.5t heavy) can be fairly expensive.
Citing Wikipedia: “There were 364,000 vehicles produced in 2014, of which 70% were exported to 140 countries.”
Even though 30% might not sound like a lot at first, but it definitely is, especially considering that the remaining 70% are distributed over those 140 countries.
yes it is, usa is one of the largest markets for those cars, americans love their suv’s. So they are “assembled” there (where are the parts actually manufactured) but they do the same in other places. so the lessons aren’t don’t outsource, they’re the same as always, supply and demand, do what makes a profit, america is the home of capitalism after all
This article strikes me as pretty one-sided. I recently had a small funded Kickstarter, and it ended up being a lot more units than I was going to be able to build myself, so I started looking for suppliers. Local suppliers wanted a ridiculous amount of money ($40 per unit for something that nobody would pay more than $20 each for a finished part).
I looked at Seeed Studios, and they wanted about $10. I searched Alibaba and found several suppliers that could do it for much less than that. Alibaba has a purchasing guarantee that heavily favors the buyer, so I knew that if the supplier imploded on delivery, I wouldn’t need to pay. I’d risk about 1.5 months on getting a new supplier, but I was pretty sure the backers would understand. In the end, the experience was great, and since it was a low quantity and a low total dollar cost, I never visited the supplier. Honestly, I’m not trained in supplier quality audits anyway, but I had a part that was going to be easy to tell if it was screwed up. It worked out extremely well for me and I learned a lot.
I couldn’t agree more as someone running a KS campaign currently 200% funded at $100k… see my post below
I respectfully disagree on many points:
“you’re putting the fate of your company in the hands of a manufacturer who doesn’t care and is half a world away”:
– I fail to see why company nearness is proportional with the amount of caring
– Your manufacturer cares about money: 50% before, 50% once all the units passed the functional tests and QC
“Remember that reducing your risk is a major goal of a startup”
– having the best quality/cost promise for your upcoming product is as well
“If you are outsourcing manufacturing, you are accepting an enormous risk, and worse yet there are no consequences if your manufacturer messes up any of the billion things that can go wrong.”
– well obviously… the only alternative is making your device in house
“Assembly lines take a long time to set up.”
– I do hope you are joking… it takes much longer in Europe at least
“Travel to a foreign country is time-consuming and expensive.”
– yes it is… but your goal is to lose time/money in the beginning (explaining to your manufacturer, ironing out the bugs) to gain a lot later!
“But when you are looking at making a thousand of something, and a flight costs a thousand dollars, you’ve just increased your COGS by $1”
– if your device is >$50 then it is very likely $1 is worth it
“But they’ll help you along the way, often with free and extremely useful advice.”
– they are not teachers, and need to make money. Not everyone has the patience and time to waste explaining you how to do things. Speaking to your local hacker community will be way better
– this also applies to good chinese assemblers!
“that wall is too thin, that undercut means you need a slide, and I need to know what color and texture you want. Come down to our office and check out the book of colors and textures we have.”
– chinese plastic guys will also say that in my experience
“They’re going to do that because they want high yield and no returns or scrapped product,”
– same for chinese guys!
“MANUFACTURING YOURSELF”
– This is the biggest joke of the complete article…. I’ll expand below
“MANUFACTURING YOURSELF”
Let’s list what you need to produce 100 boards or so
– soldering iron
– microscope
– stencil holder
– reflow (pizza) oven
– good lighting
– fume extraction system (or fan)
How do you value your time? Do you really not have anything else to do (design, marketing, reaching out, improving the schematics / layout, certification process) than to solder all day long?
Your best choice would be to hire someone locally that would assemble your device at your place. But are you really going to easily find someone for cheap that doesn’t already have a job… and is actually going to accept working for you for a week or two?
I have. For three different companies, three different ways:
1) After a small batch order, I assembled about 30 large PCBs with 300 components. Had an assembly party at my local hackerspace and gave out pizza and beer. They thanked me afterwards for getting practice on SMT soldering.
2) Had a small startup that made an electronic gadget. Built 3000 units in the first year by hiring two high school kids to do the assembly. They learned so much and got so good at it that they started their own PCBA small batch company. Now that startup has scaled up and the assembly is being done by a local PCBA company.
3) Worked for a company with an extensive product line but fairly low volume for each. We purchased a pick and place and stencil holder and do all our own assembly. We hired a guy part time to run it all. In house was a few dollars cheaper than local outsourcing, and we had the ability to do small batches of our products as necessary, reducing inventory storage, and giving us more flexibility to modify our design.
It’s definitely possible, and has a lot of advantages.
Hey Bob,
Thanks for taking the time to answer.
1) How exactly does that help in any way preparing for mass production of your product? You can’t do this kind of thing more than once, if there’s a problem on your board you can’t know for a fact that it is a design problem or a soldering problem (because of the non repeatable process), you are not preparing anyone for the mass production run. All you can take away is feedback on how easy it is to assemble by hand.
2) That’s indeed what I was suggesting in my last sentence… so if you had to do it again, would you still hire students or outsource the job? If you look at the amount of time you spent teaching these kinds… is it really worth it? I’m taking out of the equation the love of sharing of course as this article is mainly about the financial aspects of making a product.
3) You can’t possibility tell me that it is realistic to purchase your own pick and place for a one off project idea. Is someone having a project idea really is going to make such a big investment (with everything that it involves) when he’d better concentrate on more important stuff?
1) There’s lots to learn about the manufacturing process by doing it yourself. I considered this one to be my graduate school. I learned so many debugging steps, so many things about solder paste and stencils and reflow. Further, there are lots of things that make designs easier in mass production that also make them easier in hand assembly, and figuring it out on your own makes it easier to outsource because you know what is challenging about the assembly of your product, and you can fix mistakes that you discover in small volumes a lot cheaper than when you’ve gone to large volumes. We discovered how terrible USB SMT connectors are when there is a possibility of torque and switched to through hole, for example. It’s so much better to feel the pain points of assembly and tweak the design to fix it than to outsource and discover much later that waste is high and the assembly line is struggling to do a task that could have been avoided easily.
2) Considering the scale of the company at the time, our need for speed (the other companies we considered for outsourcing couldn’t schedule us when we needed), and our budget, yeah, it was the right decision. And teaching wasn’t necessarily unique to this project. Maybe for PCBA, but for product assembly it’s pretty normal to have to train employees to use special tools and do techniques a certain way. These guys took surprisingly little training because I built tools to automate the process as much as possible; something you’d have to do if you outsourced certain parts of assembly anyway.
3) Maybe not for a one-off project, but that wasn’t our intent with this company. We seriously explored options. We ended up getting our plastics from China, but from a company we’ve worked with before, and even then it was painful but worth the price. We got our PCBs from China, too, from a company I’ve been using for years. But we did the math and explored local options for PCBA, assembly, and testing, and for this company came out way ahead by purchasing our own tools and doing it in house. That’s not going to be true of every company, but it is a real option that is accessible to people and shouldn’t be ignored.
1) You could have learned exactly the same if you had assembled 10 beta units and then outsourced the rest of your batch. As I said you can’t do what you have done with your hackerspace more than once every 2 years so I’d keep this special occasion for something worth it.
2) I actually meant teaching them the basics of soldering or product assembly, not the more complex/unique tasks that are needed for your product
3) accessible to an extremely small amount of people who:
– want to do more than a one off
– have space for such a machine
– have the funds to buy it
– have time to learn how to operate it
exactly!
Time is already scarce and those chinese manufacturers are specialized in assembly and better geared toward that then you ever can.
Yes, this. This article is so very one-sided and US-centric, with the assumption that local manufacture is even approximately economically reasonable.
For example, I can get some prototype PCBs made in China and shipped (quickly!) to me for about $40; $25 if I’m willing to wait a month for dirtypcbs. Locally (Australia), that’s about $400. PCBA is nearly as bad: the last thing I had quoted widely (a batch of 40 Pi HATs) came back as being $300-$400 from China, or $2000-$4000 from local PCBA houses.
The only benefit of the locals was slightly faster turnaround, two weeks instead of three or four. That’s worth it in certain situations, if you have a cost-insensitive customer who Needs Something Working Right F**king Now, or you have a whole bunch of engineers sitting idle waiting for the product (in which case you are an incompetent project-manager), but for someone developing a new product in a startup kind of situation, the price difference is unsustainable. The article quibbles about $1 on COGS, but I’m up against a 10x factor here.
Similar economics apply to DIY assembly: I am not paying $5000 for a P&P machine to run a $400 assembly job (or even a handful of them), nor am I willing to spend the best part of a day (engineer-time! billable at $1k-$3k if we’re being serious) poking about with tweezers and an oven to save about $250. If I knew I was about to make 10,000 of something then I’d look at buying equipment and hiring people, but probably not for my first-ever product. Much better to involve manufacturing professionals the first few times to tell you what you should be doing better.
Who ever first came up with this way of doing buisness has a lot to answer for:
“1.Validate your product in the market. Build a minimum viable product and get it in the hands of lots of users”
— which roughly translates to ‘over promise, underdeliver, sell start-up leaving all your v̶i̶c̶t̶i̶m̶s̶ customers with products they’ve paid for but don’t deliver the promised functionality.
There’s a reason I won’t fund /any/ tech kickstarter of pre-order anymore. Bre Pettis and his ‘cult of h̶a̶l̶f̶a̶s̶s̶ done have screwed over so many early adopters.
Making an MVP is to prevent over-promosing though. If they over-promised then they DIDN’T have an MVP or they ignored it
Outsourcing PCBA is easy enough. So is individual other parts, be they laser cut, milled or 3d printed. But you shouldn’t outsource managing the process, and usually even outsourcing the final assembly is more work than it is worth.
If anyone is left wondering, COGS means Cost Of Goods Sold. It’s not real cogs…
Thanks, I’ve added the long-form of that acronym the first time it’s used to help anyone who isn’t familiar with the term.
I thought it was Chip On Glass Semiconductor?
I was leaning towards, “Carcass Of Giant Slug”.
My rule: if it weighs more than 100 kilograms, make it locally. Otherwise, make it in China :) /Runs away/
If that’s a joke about US citizens being fat, I appreciate it. :)
To my experience outsourcing isn;t as bad as you say. lots of pcba facturers in Shenzhen has the ability to run small runs easily on a day by day basis. It helps if contact your manufacturer regularly for updates and try to steer/adjust the production run. Let them send also lots pictures and check them
Also you should design for manufacture; choose your BOM wisely (use as much jellybean components instead of exotic ones; use as little different components and values) lay out your board relax (no tight routing; 5/5 mil tracks; a bit larger pads for components). I use the rule i need to easily handsolder the boards without too much hassle/rework, so it is easy for the machine too :)
Think of a simple tests to test if your board is soldered ok during the first stages of development, add lots of testpoints (if needed). write selftestroutines in the microcontroller (if applicable). Easy access to programming interface too. Write the testguide in dummy style (such as your girlfriend can conduct the test ;)) in simple englisch, use lots of pictures in the documentation.
Also double check everything :)
I think this is much more of the attitude that should be promoted. Don’t aim for the minimum viable product, rather design for manufacture and design for test.
The attitude that new products will have kinks and that you need an experienced technician to hold your hand through the manufacturing process is absolutely toxic. The clear difference in responsibility between designer and manufacturer is what makes outsourcing streamlined and competitive, and I don’t understand why everybody keeps fighting this separation.
Finally can we stop having click bait article titles on HaD? No question marks please. The author’s slant is clear, and that should’ve been reflected in the title imo.
“The clear difference in responsibility between designer and manufacturer is what makes outsourcing streamlined and competitive, and I don’t understand why everybody keeps fighting this separation.”
This separation is a bad idea in most respects. The designer who doesn’t understand the manufacturing is doomed to designing products that are more expensive to manufacture than the designer who does understand manufacturing.
Indeed, one of the driving forces behind a lot of reshoring was the realization that introducing a profound communication gap between designers and manufacturing was increasing costs needlessly.
One of the key things GE did as part of their reshoring efforts was to involve designers directly with the manufacturing process. As a result, they said they would up almost completely redesigning their water heaters.
http://insiderlouisville.com/business/reshoring-turnaround-ge-appliance-park/
Of course the designer should understand the manufacturing process, that is core to dfm and dft. The designer is responsible for creating a product that is clearly and easily assembled and tested on site by non-specialized workers.
This goes against the author’s thesis, as he calls it “don’t start in China early.” The communication gap is a one-way phenomenon that a designer should overcome with dfm and dft. HaD needs to discuss these principles instead “I got burned by outsourcing” hit pieces.
Appliances are not a good example anyway; the challenges are mostly mechanical and electrical, not electronic.
Also most appliance manufacturers including GE are struggling, and I’ve seen some American firms reshore like this for tax breaks and subsidies. Good on uncle Sam for recovering those jobs, but consumer electronics assembly is not coming back to the states by the same mechanism. Avoiding the acceptance of this and teaching such egalitarian electronic design makes stateside electronics developers less competitive and ultimately offshored as well.
KittCosmo, first, who said the discussion had to be strictly about electronics? Second, you’re kidding yourself if you think reshoring is a tax gimmick. Lastly, there are MANY examples beyond appliances, and does it occur to you that appliance makers may be struggling precisely because of the ills of offshoring?
You don’t bother to support your claim that only some jobs are coming back but never electronics assembly, so I won’t bother believing it.
In our company, Manufacturing Engineers are the lead engineers/project managers for all product development projects. All other design engineers are team members. That way DFM is always on the forefront, as if we miss anything critical, guess who is on the floor or in the QA lab troubleshooting a process? Or in the air on the way to a supplier? As I write this one of our engineers is visiting a large customer because our manufacturing messed up (there will be an reenactment of the Star Wars scene “apology accepted…”).
What exactly are jellybean components?
And if I wanted a product to be as easily sourced as possible in china, how do I do that without revering to 1970-1980 level of technology?
Common passives, common logic chips, generic semiconductors like lm358, bss138, 2n3904 and so on.
But how about switches, connectors and buttons?
How can I choose units that are available cheaply in china, instead of the vendor there importing them from Digi-Key?
Hey everybody.
Could you please recommend some us based manufacturer? The ones that you know that work with good quality. I have to manufacture some boards, just a hundred right now but I need good quality and good delivery time. I’m new in this manufacturing thing and I need to get it right to be able to continue with my client.
Cheers!
I havn’t used him personally but believe he probably has a quality process. Bob Coggshell http://www.smallbatchassembly.com/ (He is also the co-author of the sudo command in unix)
While I haven’t directly engaged them, three different projects I’ve backed have used MacroFab for their final assembly(mechaduino, openMV, and a temperature logger who’s name escapes me) and they’ve all been good hardware, although the projects themselves have the usual range of delays.
In many cases, the best option for that is to use the Thomas Regional directory to look for a PCB manufacturer in your local area, and arrange for a visit. I was able to find a good PCB assembly plant (who can also handle the sourcing for the PCBs – you can just send them a Gerber and BOM, and they’ll handle the rest) literally within walking distance of where I work.
I think there is no “one size fits all”. The different options of self-manufacturing, local outsource or overseas outsourcing will depend on your skills, funding, products and market.
I have contracted locally, and manufactured internally. I have been involved with production in China and Taiwan. One went (and is going) well, the other not so well. I know others for whom it was a success and others a nightmare.
Also, working about 10 years at a contract manufacturer in a previous life, I saw a lot of designs that were not ready for manufacture. Seeing what they went through to get the design in shape, I would hate to think how much more difficult it would have been if they were trying to do it while over there.
In my case I would almost always start initial production locally if there is any way to do it and make sure the product is ready before going overseas.
Aside from the technical details remember if you have a shipment once a month from China, you also have an extra month of product on a boat that you have paid for. That ties up extra cash. As mentioned in the post you can ship by air but that is expensive too.
One last suggestion: In your design try to find ways to reduce or eliminate human assembly and testing. That will reduce the difference between lower wages overseas and local manufacture. That is what has allowed some US companies to bring manufacturing back home.
That’s good advice for any design. I am a contract manufacturer in this life, and one of the services we provide is a full design review, with recommendations on what will improve the design for manufacturability or performance (within our area of expertise). Unfortunately, if cost is the only thing that matters, we lose.
I don’t understand the strong opinions against self-manufacturing. If you consider the typical “maker startup”:
– It typically makes products that has medium to low complexity (e.g. Arduino R3 like).
– It has a small portfolio of products, but is unsure yet which ones will sell in more volumes than others (e.g. 4-5 cool “raspberry pi HATs”)
– It wants the flexibility to pivot quickly in case of an issue (e.g. need to change a connector type, product enhancement, …)
– It has a team eager to learn more.
In this case it seems logical to go for one of those Chinese desktop pick-and-place machines, like the TVM802B, the VP-2500D or Neoden 4. While the PCBs will be made overseas, this should allow assembling in-house 100 to 300 boards of each product in order to test the waters, saving the pain of dealing with a foreign supplier, customs and uncertainty… as detailed in the article. The machine can be reused for many more projects and amortized in a few months.
If demand grows in the thousands then, yes, perhaps it makes sense for such a startup to offload some PCBA overseas. Until then, the in-house approach seems by far more sensible, no?
It depends. Self assembly can definitely make sense if you have a portfolio of short run products and a team of assemblers. I’m not seeing this article as a bashing of a specific approach to putting a product together as much as a reminder to consider all your options and their different strengths and weaknesses. The company I work for has used all three approaches at different points. They all have their place. The above example – short runs where the company has a team of assemblers – would make sense for in house assembly.
If I came up with a really great idea that would sell thousands I would avoid China if possible, by the time I had my product shipped the Chinese clones would have already flooded the market. China is a country in which there is little IP protection and their court system is always skewed in favour of Chinese companies and against foreign companies.
Sure some of the big players do well from china, Apple etc but they have the money, time and staff to deal with the complex legal issues (Which will arise if you have a great product).
Pay a little more and choose a country that isn’t inherently corrupt. I would recommend any western country with IP protection really.
China is the ultimate copycat culture and it’s mostly legal. Where else could you find a Polystation or Chintendo Wii for sale (legally).
Given that it just came out that 90% of Apple accessories on Amazon are counterfeit, protecting your IP is important for a startup. Even with care, you can expect copies within a few months.
I agree but by not using China at least you will be launching your product first not some dodgy employees of the PCB factory who sold your design. If your product is good enough it will be stolen and sold anyway, You just need to be ready. That 90% figure is crazy, That must mean apple is losing more than 50% of their accessory sales overall. apple can take a hit like that but some most startups that could kill them stone dead.
I’ve been using MacroFab and find them to be cheaper and much easier to use that Small Batch Assembly. Their customer service is also outstanding!
Small Batch and MacroFab address different types of customers. As per the credit to this article, Small Batch produced the Superconference badges. Disclaimer: I run Small Batch.
Sorry, you’re right. That wasn’t an accurate comparison.
I’m an American, and have been working on a wearable audio device I’m going to Indiegogo soon. I’ve been a toolmaker and a patternmaker for prototype aluminum and zinc castings, a Linux engineer, a sysadmin, among other things. The reasons I will be doing essentially everything locally are; 1) From my experience in outsourcing software engineering work, the time differences and communication issues eat up an enormous amount of time in small annoying chunks, and the cultural differences about what is ‘good enough’ can have a real effect on morale. Often, work done offshore was redone on local engineers own time because they just could not bear to look at the crap that was delivered. That, and the employee churn at remote houses can often really impact deadlines. Overall, I found the stress to not be worth the potential cost differences. 2) In just one generation, so much industrial and technical knowledge can evaporate if it is not nurtured and supported and grown right here in my own country. Already we see less and less machining, manufacturing, assembly companies, and in many areas of the country, there isn’t anyone capable of doing the jobs even if there were any.
I am committed to using local – likely mostly in-house – resources to build and grow my product and company because I want to nurture these things here in my country. I know it’s cheaper in China, and that I would make more money that way, but honestly I do not want to support a country that censors the Internet, steals the ideas of others for profit, and generally is just an horrible and oppressive regime. Profit is not everything. Making something great that you can be proud of, and building a great company that respects it’s workers as part of a larger extended family is the direction I want to go in.
-C
I’ve been in the same place, never ending redos eating up time just to reach acceptable levels. Sending simple, clear and concise CAD and prototypes then having to rework each sample that was shipped to us, sending it back to communicate what is acceptable. In the end having the quality of the design go down a couple of notches because there was not enough time for fixes. That said, If it was economical to manufacture here it would have been done. These were large orders, 30,000 to 1.2 million. We are really hoping to do most if not all our manufacturing here on our next product as it will be 5,000 units if at all possible. As for shipping, surface is the only way to meet your margins unless you have a high priced luxury item. Air freight eats up almost all profit in my experience. The blatant copying is another worry, even if you’re a good sized company finding out exactly who is manufacturing the article is not easy and taking counterfeiters to court is usually not worth the money. The money spent on investigating and filing suit can be better spent on developing the next product because the product that was copied can be off the market by the time your case is heard much less settled.
BTW, camping out at a China factory for weeks trying to troubleshoot issues in time for first shipment sucks, I have PTSD issues whenever I am exposed to yellow tinged fluorescent lighting (kidding, but not by much).
I applaud your efforts, I hope you go far. I hate to admit this but Trump is right on one thing, China is killing us economically. I live in the UK, We were once a nation of manufactures, Some of the things created in this country were known for quality (Land rover, Aston martin, Mini, Dyson, Virgin). I see the same happening in the USA, Look at Detroit. This is our future if we can’t reverse the trend. I am not blaming China I think they have been economically smart. I blame our leaders for allowing one way trade with China that has created the next super state from ashes in a mere 50 years.
We need to get our act together, We need to get good at making things again. Price is the killer, but hopefully with more & more automation that will cease to be so much of an issue. The west’s biggest downfall has been wanting everything cheap then wanting it cheaper. Its sad it costs me more money to send a product nationally than it does for a Chinese company to send products globally. We need to get the public to support local business and buy our own nations products (when viable).
There is an old saying “Buy quality and cry once — Buy cheap and cry forever”
We are more a nation of manufacturers than any other time in our history, and we’ve tripled our manufacturing output in the last three decades. We have fewer manufacturing jobs, but that’s because of automation. Check it: http://www.marketwatch.com/story/us-manufacturing-dead-output-has-doubled-in-three-decades-2016-03-28
My opinion obviously, but somehow I heard “lies, damn lies, and statistics” in the back of my head while I read that article. And it wasn’t in what was said, but it felt like it was in what wasn’t. Maybe it’s the automation that has me ‘feeling’ that way, and I’ll admit it’s a feeling rather than hard data. How much of that manufacturing is weapons or weapons related I wonder? Are we making chips anymore really? Are we making electronic devices all that much anymore? Relying on other countries, especially ones that are in reality hostile towards us, to produce things that are essential to our survival is simply insane. It’s an insanity that is fueled by greed.
Maybe this article is true but it doesn’t feel true, Maybe things are made in the west but because of automation the jobs just are not there any more? I don’t know it just seems to me nearly every product is made in China. Maybe it is because we use so many more products these days and the population is up that we make more but it seems like we make nothing? I really don’t know it just doesn’t seem right to me.
I would also note that it pays to shop around a bit, especially with injection mold tooling and board stuffing. I recently quoted out a part for injection molding, and prices ranged from $9500 to $49500.
Places like Protomold can be great for getting your part right, and a big help. Their interactive quotes can make you quite confident on what you are getting. Stratasys direct is usually a little bit cheaper, but less helpful on the design and communication front.
When it comes to offshoring, Stratasys gives you a little of the best of both worlds… they offshore the tooling, then shoot the part here in the USA.
On the board stuffing, make sure you know what is important to you quality wise. I’ve noticed a big difference in price here in the midwest, but it usually comes with a hidden cost in overall quality.
I just received some prototype products assembled by MacroFab yesterday. If you’re curious about what they can do, I made a way too long unboxing video, here: https://youtu.be/0wxtDBv1rsY
Hi Nicholas, thanks for the great unboxing video! To answer two questions in there: the reason for the different color PCBs, is that if you select “any soldermask / any silkscreen” (the default and cheapest option), we’ll panelize you with other orders, some of which may choose different colors. As for why some things are pasted and not, our process uses the paste layer to determine what to paste, even if the part there is DNP (two different processes use two different inputs). Now, as to why some of them are not pasted on one side — we run multiple copies of panels based on different order demand, and if the orders left on the later copies of the panel have one-sided assembly, we’ll stop pasting the second side during processing. HTH and thanks again!
Note: This is not a sales call or advertisement for our services, just feedback to this article and associated comments.
I founded an electronics contract manufacturing facility 18 years ago having started in the CM world during a college CO-OP position. We currently run 4 SMT lines and are in the process of adding three more.
I have been involved in the proto, pilot, production process of thousands of products. I clearly see both sides of the outsourcing world, domestic vs. overseas and there are situations where each is a viable and/or preferred option. I have many war stories that I could share on product development through production. Some are painful but many have similar themes and common trends.
I have a few famous sayings, that consistently come up, that are applicable to this discussion.
1. A properly designed product can be built anywhere in the world with reasonable costs.
Take responsibility for your design. If there is high hand assembly requirements requiring more labor, then of course overseas production, with lower labor rates, will be more appealing, but address those aspects of the design during the development phase. A PCB assembly that is most all SMT can be built with very reasonable assembly costs locally with very high quality, schedule flexibility, responsiveness and ease of communication. The delta between domestic and overseas costs are minimal if the product is designed for manufacturability.
2. Don’t design in $40 worth of parts if you need the product cost to be $20 ea.
The final cost of a product should be set at the BEGINNING of the design phase and all component selection and design considerations should be based on the impact to this. Way too many times have I seen designs come through to proto and pilot runs and then the customer says that they need to find ways to reduce product cost by 40%. Well knuckle-head, maybe you should have had that in mind over last year of product development!
3. Component material cost is more of a cost driver than labor, in the discussion of domestic vs. overseas manufacturing.
Why have I seen quoted prices from overseas where the fully assembled unit cost is less than I can even buy the components for domestically? The domestic material market, supply chain and distributors for electronic devices is burdened with overhead, this is not as much the case in Asia. The EXTREME downside is that materials used in your product when built in Asia will be from the common market and some portion will be counterfeit and/or from non-certified channels. That being said the end product will most likely work but there is no guarantee that the parts you specified came through certified channels and that the next build may be junk due to different component supply paths. Work with your distributors and component manufacturers at each stage of the design. You can get the same pricing domestically if you work the disty/MFG relationship.
4. Compare real apples to apples and remember to include all of the costs. Be sure to include the shipping costs, communication delays, cost to prepay and IP exposure, to name a few.
5. Provide clean documentation.
Again, take responsibility for your design and have pride in providing clean, revision controlled Bills of Material, gerbers, Fab part data and drawings. Avoid quotes like “use the REV A i just sent rather than the REV A from last week”.
6. Provide a target cost to the CM if possible along with realistic estimated production volume.
A good CM will provide feedback as to what the cost drivers are and where efforts need to be focused to meet the target.
That’s a few points I see all the time.
I have also seen large companies’ completely destroy domestic vendor relationships with the goal of savings in overseas manufacturing in Asia, Mexico, India and other. They add people to coordinate, VP’s to make reports, accountants to pat themselves on the back and lay-off half their workers and piss off / screw over their existing vendor base.
The costs are foggy and the net savings is lost in the soft costs and BS.
Often the 5 year cycle ends with “re-shoring” efforts and the VP’s get a nice package to move onto the next company and ride the pony again.
I’m not saying that domestic manufacturing is better than overseas in a blanket statement. There are benefits to both and we partner with overseas vendors as part of our process. The important factors are to build a strong OEM-vendor relationship with mutual trust, being open to the goals of each, communicating and working together.
Your vendors are an extension of your company and processes. Treat them as such and not as an adversary.
Be well.
THIS IS WHY I READ THE COMMENTS. in amongst the vitriol and ignorance are little gems like this from experienced people.
I’m just getting started on a shoestring budget and I anticipate a few thousand sales per year but perhaps up into the tens of thousands if it goes well. After reading all of the comments, I think I’m going to build the first few hundred or so boards by myself. Then I’ll hire a small batch assembly service. I checked two different services and found that 100 boards is about six dollars per board, including setup fees, if you supply all of the boards and components. Once the design settles in and if it is selling very well I can order larger batches and increase my profit. A thousand boards at these same houses are about $3 per board.
This is a win-win for me. Agile manufacturing, no tired arms, and I can focus on my customers and R&D. If I’m REALLY going gangbusters, then I might consider China? But maybe that small shop wants the opportunity of handling 100,000 boards per year :-) Would already have a relationship established…
I considered building an PnP machine and hacking a toaster oven but given that the majority of my components are not reflow-capable I’d be doing a lot by hand. Skip that. My time is worth more than $6 :-)
@gregory cronin – thanks for your insight.
Thanks for pointing out that you probably have a manufacturer capable of handling your product within 100 miles. I think it would be smart to outsource manufacturing if you needed something like plastic fabrication done that might be kind of hard to do on your own. I think that it would also help to choose a local company because then you could see how they did everything firsthand which would be nice.