I’m writing a series of articles on resin casting as an extension to my experiences with the instructions found in the wonderful Guerrilla Guide. However, mistakes were made. Having run out of my usual mold release I went to a back-up jar that was lying around from a casting project long, long ago in a workshop far, far away.
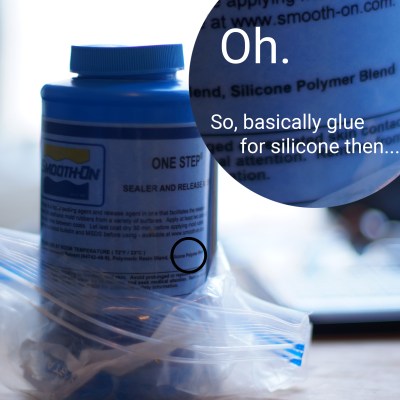
I’m refining a technique of making a mold the quick and dirty way. Everything was going well, the sprues looked good and the master released from the silicone. It was time to do the second half of the mold. As usual I applied a generous amount of mold release. Since it was the first time this mold was to be used I went ahead and did all the proper steps. Rubbing off the dried release and applying a few more coats just to be sure.
I was completely unaware that I was applying mold release designed for urethane molds only. In other words I thoroughly covered my silicone mold in silicone bonding agents. I remained unaware until trying to separate the halves of the mold and found them thoroughly joined. After going through the stages of grief I finally figured out where it all went wrong.
Oh well. I’m ordering some of my regular pick, Stoner A324, and that should do the trick. There’s also Mann- Ease Release 200. While having probably the best name a release agent can have, it doesn’t work as well and needs approximately 100 years to dry. After this setback I’d rather just, grudgingly, learn my lesson and order the correct thing.
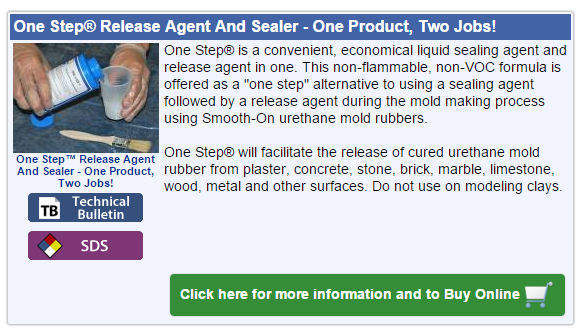
So now that we know the right way to fix this is to order the right product, is there a hack to get around it? Does anyone have a homebrew trick for release agent that can be used in a pinch? Leave your comments below.
Which of the silicone releases you mentioned take said century to dry?
Stoner or Mann-Ease?
He claims Mann Ease Release takes forever but I use 205 and it is dry in 5 minutes.
* Petroleum Jelly / Vaseline:
Usually diluted to 5-10% in naphtha (naphthalene) or mineral spirits and either brushed on or poured into the master. Remove excess and blow dry with air to evaporate solvent. This procedure will leave a fine film of release agent on the master and eliminate puddling. A higher concentration of this mixture (30-50% solid) will provide good release of the uncured silicone against cured silicone in a two-part mold.
– Advantages: Fast drying, readily available, low cost
– Disadvantages: Slimy feel that must be removed with solvent / detergent from cured silicone.
* PTFE (polytetrafluoroethylene) Release Spray
Thoroughly coat all surfaces by spraying liberally.
– Advantages: Effective in very thin coatings, easiest to use, very fast drying. Particularly good for plaster
– Disadvantages: More expensive, must order from supplier, difficult to remove.
* Talcum Powder:
Useful for the release of silicone mold from a cured silicone master, and also when casting a two-part mold. Dust surface lightly but thoroughly.
– Advantages: Low cost, no solvents, no removal necessary (it is absorbed into the silicone).
– Disadvantages: Easy to over-use; dust can be messy; limited application as it can dull the surface of the cast piece when applied to shiny masters.
* Polyvinyl Alcohol (PVA):
Supplied in a water solution, which can be thinned further with water.
– Advantages: Fairly low cost, dilute and cleanup with water, excellent as a barrier coat, environmentally safe
– Disadvantages: Slow to dry, usually must order from a supplier.
Dow corning suggesting these when I was working with their silicone rubbers. The first one worked okay, but we moved to WD-40 PTFE and that worked amazing. Does leave a slight yellow tint, but that didn’t matter for our project.
I’m not into “casting” but a HACK source of PVA might be the dishwasher wrappings that you do not need to take off.
I second the naptha/vaseline mix. I have blazed through dozens of gallons of silicone through the decades professionally (both tin and plat );My go to was always naptha/vaseline. For objects that react to petroleum distillates, like Sculpey, any type of aerosol spraypaint will work instead, just spray everything on the second half, silicone and all.
First, Always look at the Data sheet! It will warn you of release agents that don’t work, or what it recommends. Second, Pam!
The very same thing happened to me at one time.
Once I figured out what I had been doing wrong I lightly brushed some crisco (straight from the kitchen) onto the first half of the mold and it worked out great.
Has anyone tried PAM Cooking Spray. I hear it works pretty good.
Lucky that you were making molds of hard, durable things! Were that a clay model or something…
Vegetable oil works well for concrete or plaster moldings. Just spray on lightly making sure ithe mold is all coated.
Pam works well, but there is an odd one that works even better. Rubber cement on silicon seems to be magical. Dilute with vodka or use streight. Often the glue will ball up and or peel right off after heat application. Note, this is only for silicon molds and will be a disaster otherwise.
” Rubber cement on silicon seems to be magical. Dilute with vodka “….
My first thoughts when I read this was “Is this a homebrew release agent or a new alcoholic drink?”… after thinking about all the alcoholic robots I’ve seen on Hack a Day was “I guess it’s both….”
Thanks, I for the life of me could not get smooth-ons silicones to stick together. This changes everything!
In other words as long as you let the bottom fully cure before you pour the top you don’t need a release agent. This comes from many attempts to try to make a tube for molding an artificial muscle carbon fiber sock. I could never get the patch to stick. It would always peel right off.
I was using dragon skin medium at the time and finally just said screw it and bought a 3d printer to print injection molds. Using vacuum I suck the uncured silicone up into the mold. Now I use PLA sprayed with PVA then ease release 205 and it does the trick.
Now I think I can do some better geometry since I can get different cures to stick to each other.
Molding is not that expensive, so I don’t see the sense in “guerilla molding”. Alginate, silicone, release agents are cheap, at least here in Europe and you don’t want to cast huge things.
My favorite is a little dish soap (like Palmolive) diluted with 99% rubbing alcohol. Put it in a spray bottle and shake well. Great for silicone molds.
My quick how-to on silicone molding. http://partsbyemc.com/pub/mold-making.htm An alternative to shiny cardboard for the mold form is ordinary cardboard with a layer of packing tape. Use a cool melt glue gun on that.
Hot/cool melt glue is wonderful stuff. It can be used to glue masters to the mold form base. I often cut a hole in the base to recess a master model up to a parting line, then glue it in from underneath.
There’s a trick to fast and easy removal of hot and cool melt glue, pour a little rubbing alcohol on it. 70% works but 91% is better. It will even get it out of cloth. Just scrub the glue after applying alcohol and it’ll ball up and come out.
I’ve had fantastic results with Ease-Release 200 and 300 for polyurethane (Scotchcast 2130/2131) castings in aluminum and delrin molds. With the previous release agent we used, we had to beat the crap out of the mold and casting to get it to release. Now it practically falls appart as soon as the mold clamps are removed.
I feel your pain on this one. Done that a few times. I have found that some liquid soaps can be an effective release agent and use it for Silicone to Silicone Platsil and TInsil molds as well as some Silicone to Liquid Plastic molds but you need to be sure the mold dries before use as any moisture will cause bubbling.
You should take a look @ http://www.volpinprops.com and volpinprops.blogspot.com
Part 9 of the Halo Needler Series is about casting http://www.tested.com/art/makers/455623-volpin-project-part-9-casting-process/
I hope these links will hell you with the casting process (and also painting if needed ^^)