Have you ever wanted to own a full-sized ShopBot? What if some geniuses somewhere made a tool the size of a coffee maker that had the same capabilities? Does an augmented reality, real-time feedback, interactive, handheld CNC router that can make objects ranging in size from a pillbox to an entire conference room table sound like a thing that even exists? It didn’t to me at first, but then I visited the Shaper Tools office in San Francisco and they blew my mind with their flagship tool, Shaper Origin.
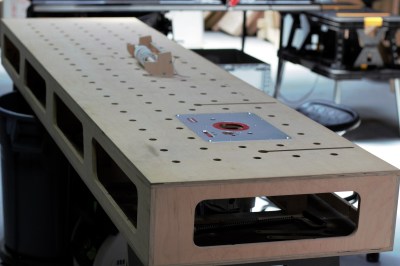
It’s impossible for me not to sound like a fan boy. Using Shaper Origin was one of those experiences where you just don’t know what to say afterwards. This is what the future looks like.
I’ve used a lot of CNC tools in my life, from my first home-built CNC conversion, to 1980s monstrosities that ran off the floppy kind of floppy disks, and all the way over to brand new state-of-the-art vertical machining centers. I had to shake a lot of that knowledge off when they demoed the device to me.
Origin is a CNC router built into the form factor of a normal wood router. The router knows where it is on the work piece. You tell it where on the piece you would like to cut out a shape, drill a hole, or make a pocket. It tells you where to go, but as you move it keeps the cutting bit precisely on the path with its three axes of control.
It’s easier to show than explain so don’t miss the embedded video at the end of this post of [Ben Krasnow], who is one of Shaper’s beta testers. He is using the tool to mill out some plates for a CNC conversion he’s performing on an old knee mill. This is actually how I found them. I saw him use the tool, googled Shaper, found out I was going to be in the same area as them, and emailed them asking if I could come check it out. Fortunately, they were all long-time Hackaday readers, who we’ve covered a few times, and were kind enough to oblige.
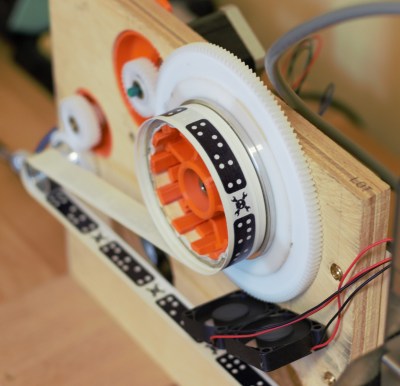
In the video you can see the basics of its operation. The first step is to place some of their non repeating fiducial tape onto the work surface. The tape is inexpensive and basically sold at material cost. Shaper Origin looks at the tape to keeps track of its position; it is surprisingly precise. Next you move Origin over the material and simply press a button when you’re over the area you’d like to cut. After that, tell Origin what tool it’s holding, how deep you’d like to cut, and press go. Origin will help you do the rest.
I suppose I wouldn’t be as impressed if it were just a cool tech demo, but this tool really works. It’s well-built. The interface is polished and intuitive. The machine I used had been in service for a year and was still going strong.
We’ll be covering the tool in a lot more detailed article soon, but we wanted to get this post out before the Bay Area Maker Faire where Shaper will be demoing the device. If you’re headed to the Bay Area Maker Faire this week you need to play with the tool yourself over at their van in Zone 10 near the east gate entrance. If you get a chance to use it I’d love to hear if your experience matched mine in the comments.
How precise do you have to attach the tape in order to get good routing results?
The question might rather be: How precise can the system keeping track of its position being told its absolute position once at the beginning. I would expect that the exact placement of the tape is not the problem. It is rather the same type of problem you have with optical computer mouses. I assume the tape is simply an additional help for the position tracking system. Please correct me if I’m wrong.
Well, I would say that is an additional question. I assume that the markers have to be placed within a certain distance of each other, otherwise the camera lens distortion correction matrix can not be calculated correctly. Also, the table top has to be as flat as possible. Still, from a practical point of view, the user has no influence on that apart from fixing the tape, so I wonder how precise that has to be attached.
The camera distortion is certainly pre-calibrated from factory and not being calibrated from the tape. The tape is just a bunch of markers the system uses to track position/orientation once you show it where on the workpiece is it positioned and set up your coordinate system orientation.
With a decent camera you can expect the best resolution to be somewhere in the range of 0.1mm or so. More would be possible with high res cameras, but then the image processing costs and the camera sensor price skyrocket. Also the vibration of the machine limits the tracking resolution. 0.1mm would be certainly more than good enough for a wood router (especially a handheld one!), but I wouldn’t rush to replace a proper CNC mill with it.
No idea whether this machine achieves that, though. I haven’t seen specs published.
“There’s no specific position for this tape, I just randomly put 4 strips across”, it says in the video. Makes sense – the router is tracking what it can see for relational movement, not absolute.
ok, thanks
You can place them in any atibitrary orientation. The camera just needs to see five dominos at a time. They even showed me how you can just add more tape if you need it or feel like it and the machine will just add it to its memory no problem. The prototype they showed can hold .01in over a large outline and can get to thousandths for a small outline. So the table top may be off by .01 from one end to the other while the outside of the spool holder are at .001. it’s cool.
ok that’s pretty impressive. In theory you could scan in the dominos and print them out yourself.
I ordered my shaper origin. Save $100 with my referral link
https://preorder.shapertools.com/ref/GPLBFE5EX
As a high school teacher I think this is a great tool to use in a high school woodworking design class. Help me fundraise to buy on of these tools for my students by using my code, and you’ll save a $100 as well!
https://preorder.shapertools.com/ref/2JTYMHQCJ
Thanks to some generous folks, the previous referral code is complete and I now have a free tool for my students. I’m working on getting a second tool. Use this new code instead https://preorder.shapertools.com/ref/N98QCM3KV
Many Thanks!
As a high school teacher I think this is a great tool to use in a high school woodworking design class. Help me fundraise to buy on of these tools for my students by using my code, and you’ll save a $100 as well!
https://preorder.shapertools.com/ref/N98QCM3KV
Damn cool. Want to buy, have no projects to use it on!
Again, this website shows how far it has fallen from it’s original content, this same device was featured years ago already.
http://hackaday.com/2012/08/09/largest-cnc-router-is-controlled-by-hand/
I strongly disagree.
While we certainly make mistakes and repost sometimes, there’s a world of difference between reading an academic paper (even one with a prototype and a video) and having a hand’s on with a (nearly) finished product. We felt these were two different stories.
would say so, too …
I also think that having this device been in use for a year is telling, there are lots of things introduced that then never really pan out past the prototype stage.
So it’s not unfair to have an update like this.
You appear to understand this isn’t a repost Elliot, why reinforce the misuse of the term repost by calling it a repost yourself, while explaining why this post has merit?
How does this differ from https://handibot.com/?
This one looks like a real product rather than some half-assed beardy open-source accelerator wannabe?
This comment is emblematic of the degradation of Hackaday’s culture; the snide derision of an open source, free community effort.
I agree that it’s inappropriately negative and unnecessary to be quite as raw in it’s conveyance. However, there is quite often a wide gap between open source offerings and commercial offerings in both hardware and software that can be quite frustrating to encounter, depending on your intended use of the project in question. It’s not universally present of course but it feels that in general, commercial products tend to be much more polished once they are released. Unclear if there is any way to change or improve that?
Free != good. There are some excellent free things. This doesn’t look like one of them to me.
Last I saw it the handibot used a form of physical registration. It was a small 3-axis cnc router that you would pickup, move to a new location, and restart the process. It would lock into the workpiece with a longer jig-saw like board for registration.
The shaper origin also has 3 axis motion, but the x-y motion is small and only there to compensate for the human in the loop control. Rather than a physical registration it uses a digital method with the camera / fiducial combination.
The results of each should be similar however.
Better answer than alphatek’s trolling yet?
As far as I can tell there are two key differences but the main aspect is how the path motion is achieved.
The Shaper tool uses two cams to achieve x-y motion whereas the handibot moves on rails (it’s more akin to putting handles onto the sides of a shapeoko that has an open base). Okay, the handibot can move to a greater degree in all 3 axis compared to the Shaper which only does smaller motion and is not really intended to alter the z-depth continuously.
Then there’s the optical registration system that allows you to map out larger cut areas in one pass. While technically something similar could be done with handibot, it looks to more of a place-run-stop setup so you’d have to have a way of moving it yourself to pre-defined locations to continue any job.
I’ve used the handibot. It’s really awful. If falls apart. Like , “exposed five cent limit switch snaps off and the machine destroys itself,” apart. It uses a piece of plywood to align itself to the workpiece. It has no intelligence of its own. It can’t correct for errors. It uses shobot’s regular software. Large outlines can have crazy errors. It had no onboard memory worth mentioning. It’s really hard to align parts. It’s intensely heavy. It’s difficult to change bits. It’s really expensive as well.
That sucks. Limit switch’s need to be robust and semi protected. And be DPDT if possible. At least when they start to fail it can be rewired until replaced.
http://hackaday.com/2015/07/26/a-handheld-cnc-router/
This repost is totally acceptable since Brian wrote the original.
To characterize this as repost would mean; because if HD feature a new tool tomorrow it could never feature it being used in building something at a later date. This is not a repost. IMO.
This is very good principle: using human strength where it suffices (e.g, for moving small to medium objects or work pieces) and using technology to achieve precision control. It is ruler (for drawing straight lines) reinvented and enhanced. Of course, fully automatic production machines can work without supervision, but they may be to expensive to produce require much more materials to be made of, and require too much space to keep, especially if they are not fully utilised.
Furthermore, the principle depicted is something that could be used for fully automatic CNC’s as well:
“Long distance movements of a tool need not be controlled with same high precision as small distance movements (positioning control), as long as you have very good position finding”.
That could be used to make cheaper automatic production tools (including DIY, hacker/maker ones) such as CNCs and 3D printers.
The principle of coars and fine positioning is sometimes already used (wafer stepper for example) where very high precision and accuracy is needed. Main problems are that you need a even more advanced position feedback and a more advanced controller (not SISO anymore).
I don’t think the video has the same wow factor some other demo videos I’ve seen from this device, circles aren’t that exciting.
They had one where they shaped the outline of the US continent if I recall correctly?
I couldn’t find that video. But here is the projects page.
http://www.shapertools.com/projects
Was it the video in the old Hacaday article?
http://hackaday.com/2012/08/09/largest-cnc-router-is-controlled-by-hand/
I think the video you have in mind was from our coverage in 2014. That was before the name was changed from Taktia to Shaper
Frankly, this kind of ad-hock video is more exciting than a manufacturer demo. It clearly shows that the tool is fairly easy to use and useful.
I see this tool being most useful for finishing and personalizing items that won’t fit in a cnc. Carving your kids names in a swing set, cutting a new drier vent, adding cable routing holes cheap cabinets, adding the bat symbol to your computer desk, etc.
It is if you have tried cutting rough circles by hand with a router….
Lol, you got a bit of a point in some circumstance, although most routers come with an arm attachment that you can fix in the center and then it’ll guide into a circle and it’s rather simple that way – I presume.
Presume so you got no practical experience?
Let someone with actual experience tell you.
It is not simple and it is not easy.
Indeed, I left some room for people with experience in trying to route circles that way, because I feared it might not be as simple as it seems. some things just have that ‘seems simple and easy and foolproof’ but then aren’t in actual practice.
At the same time the featured router might have its set of drawbacks and flaws too, stuff not mentioned.
.
I would think that the vibration would affect the accuracy of the camera/sensor. How did they fix the problem?
If the vibration causes uncorrelated noise the accuracy can be even enhanced (oversampling and averaging). But the question is if it is uncorrelated or not!?
Nevertheless, it is quite an interesting tool.
It’s like the DaVinci surgical robot assist. Wonderful!
This looks great, especially for people like me that don’t have a giant workplace. What would this machine cost trough?
I need this thing… I really hope it ends up less than $1500 – $2000 and comes out of beta soon
The web page says the device is linked to the cloud… I’m really hoping it doesn’t require the cloud for its basic function, but that the cloud provides extra features. There’s been enough devices that get bricked because the servers later went down that I wouldn’t ever knowingly buy a device that had such a requirement.
Argh! The cloud crap turns me off.
Darren-
Although Shaper Origin has cloud connectivity, it is 100% operational without it. You can even use the USB port on the side to load on your design files using a flash drive. The cloud connectivity enables downloading designs automatically as well as software updates that improve reliability and performance, but the machine will happily run without a connection to the web or our server.
-Jeremy from Shaper
Thank you! This is exactly how cloud-associated devices should be.
I agree too. The right way or the highway.
25+ years an EE. 15+ years a CNC lunatic. FPGA is my cocaine. Embedded systems are my beer. Every once in a great while you see an idea so good that it transcends your own jealousy / “I could do it better” primal urges to critique. I am truly impressed. The inventors get my seldom given admiration and respect. Well done folks! I only wish I had been part of your team. This is a game changer for too many reasons to list. You are to CNC what the GUI was to personal computers. You have identified something that people do poorly (fine motor control of dynamically moving reactive objects) and something that people do quite well (gross movement of large objects) and used image processing and small (read inexpensive) motors to bridge the gap, using super-cheap super good commodity optical encoders the rest of us dumb-asses think are digital cameras!! You get the slow-clap (think Officer and a Gentleman) from me. Well done!
Wow Luigi – thank you for your comments! We are so excited that you are excited!
Jeremy & the Shaper team
Looks to be a great portable machine tool, though I doubt I’ll ever use on in a construction project.
cool. Thank you
Oh god yes please. I’m throwing my wallet at the screen but nothing is happening! This looks amazingly versatile and well implemented.
Hey Scott – pre-sales have started! Thanks for your excitement :) shapertools.com
Now they want you to order over a YEAR in advance to get a good price. And, they’re quoting about $15 for enough tape to cover a 4×8 sheet of material. I think I’ll save my pennies to buy a small ShopBot… Or, at the very least, wait until this tool is released to read hands-on reviews (and, see how much they drop the price due to low demand).
I pre-ordered one, even though there is a wait. I don’t have the space for a Shop Bot, nor do I want to create one. I can do projects wherever I wish with a portable worktable. After you buy they give you a referral link where you can get yourself and others a discount. I found out about the Shaper Origin here, so if anyone needs a link, you can use mine- https://preorder.shapertools.com/ref/F4E7NECBW
Of course admins can delete it if they feel it’s inappropriate.
I personally can’t wait to get mine.
Thanks for your support, Dan! Excited to get one into your hands.
-Jeremy @Shaper
I look forward to owning one of these. Speaking to a US-based company, please make this device universal voltage; outside your borders, 230–250V is normal. I see the router motor is a DeWalt; they sell well here (Australia) and definitely know our local voltages. Or, perhaps, 18V rechargeable is the way to go. In any case, as soon as I saw Gerrit’s video above, and especially the part that showed how a SolidWork’s design could be loaded via USB, I was sold. This device is a game-changer, I believe. For my business, way more useful than 3D printing. And @ Rodney, above, I read that the tape is supplied at cost; can’t imagine any better deal than that. I regard the video above as an excellent hands-on review; the tool can only get better. It is great as it is.
Thanks! We’ve designed to make the 220V switch as easy as possible, from a manufacturing perspective. We hope to bring it international as soon as we can, but want to focus on ensuring it’s perfect on our home-turf first. Furthermore, as a startup, certification and regulatory compliance steps can be really time consuming and expensive – so we don’t want to get in over-our-heads right away by trying to handle lots of different countries from the outset.
-Jeremy @ Shaper
Thanks Jeremy; please consider me an Antipodean early adopter and let me know as soon as you can when I can pre-order one. Later adopters like us can only benefit from home turf refinement.
“Shaper Tools Will Blow Your Mind” and so will the price tag.. $2000 retail. That’s the same price range as a decent hobby grade 3 axis cnc system, or a nice laser cutter depending on your needs.
I pre-ordered. Hopefully this will live up to the hype, since there are a bunch of people with pre-releases that seem to like it.
My referal link is: https://preorder.shapertools.com/ref/32XG5X5BE
It gives an additional $100 discount to whoever uses the link (they also charge $100 shipping), and to me.
Sucker… You apparently haven’t read the comments here carefully enough.
I just ordered one too, save $100 using my link http://bit.ly/2csi4RO
I like the Idea that it still uses the hands on approach with a little touch of cnc. I create several wood crafts by hand which I find more satisfying then watching a full on CNC platform doing it for you. Mind you, I still have small CNC kit which is primarily used for making my company logo. After observing the demos, this may fit the bill being small and portable with no limit in the size of the material to cut. In that note, I just pre-ordered it too. If you want to save a $100 click https://preorder.shapertools.com/ref/4GMJY909X
This is one of the most innovative ideas I have seen in woodworking in a long time. Whether you are new to woodworking or tired of having to use an over sized and cumbersome CNC machine shaper can get you making projects in no time. I have already ordered one and cannot wait to get started. I am already collecting ideas and plans for projects I can’t wait to make. Everything from home-improvement projects to Christmas gifts for the family. Check it out and I guarantee you’ll be excited by what you see. Also if you use a link you can save $100 on your pre-order.
https://preorder.shapertools.com/ref/GLR8R2508
Too bad I can’t use the router that I already own (dewalt 611). IMHO, it would be great if the Shaper Origin was capable of accepting the most common routers that many people already own.
I do a lot of woodworking for my kid’s school ranging from props for plays, art projects, decorative boxes for teachers and staff, and many other needed projects that benefit the school. I have also taught the students some basic woodworking skills. This Shaper Origin will allow me to show the students how to design, produce, and assemble projects that they came up with. If I can ask you to use my code below to help fund this tool, both you and I will save $100! Thanks.
https://preorder.shapertools.com/ref/UBNAVMNGE
This thing is awesome, I’ve built a MPCNC and it definitely is great but I love the mobility of this tool.
if you are looking for yet another referral link please try mine!
https://preorder.shapertools.com/ref/G943WVN3X