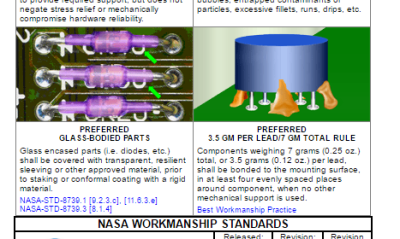
The NASA workmanship standards are absolutely beautiful. I mean that in the fullest extent of the word. If I had any say in the art that goes up in the Louvre, I’d put them up right beside Mona. They’re a model of what a standard should be. A clear instruction for construction, design, and inspection all at once. They’re written in clear language and contain all the vernacular one needs to interpret them. They’re unassuming. The illustrations are perfectly communicative. It’s a monument to the engineer’s art.
Around five years ago I had a problem to solve. Every time a device went into the field happily transmitting magic through its myriad connectors, it would inevitably come back red tagged, dusty, and sad. It needed to stop. I dutifully traced the problem to a connector, and I found the problem. A previous engineer had informed everyone that it was perfectly okay to solder a connector after crimping. This instruction was added because, previously, the crimps were performed with a regular pair of needle nose pliers and they came undone… a lot. Needless to say, the solder also interfered with their reliable operation, though less obviously. Stress failures and intermittent contact was common.
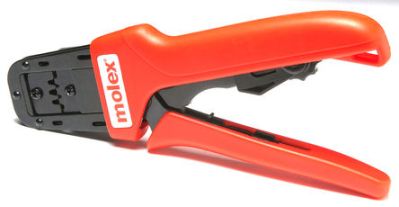
I made a mental count of all the affected equipment and did a bit of breathing through my nose. When I was calm I did a few things. One, I ordered the outrageously expensive crimp tool for the connectors. Two, I informed everyone that I would be annoying if I saw them soldering a connector or crimping it with pliers. It was the only threat I had… Three, I set out to find or write a standard for our connectors. For that I would have to reach to a higher power. In engineering, that apparently ended up being NASA.
Where to Find NASA Standards
Now, NASA stores their standards in two places. The more updated one is here, unfortunately these, while updated, are not complete. Also, NASA has started to adopt some external specifications. While these are proven and tested, it does throw them behind a paywall. Only a few of the standards qualify as, “open,” and are accessible for any regular person to access. To get the rest you need a NASA ID. The older one, but way more complete and entertaining one is buried in a subdomain called workmanship.nasa.gov.
In polite conversation I would stray away from using a sentence like, “this engineering specification was a really good read,” but fortunately this is Hackaday. The NASA workmanship standards are a really good read. The amount of useful, instantly applicable information is great. What should a lineman splice look like? Is the big glob of solder on the end of this connector okay? How tight is too tight for a cable tie? The standard answers it clearly and concisely. I guarantee that any hacker who reads it will soon see less failure in their projects soon after.
As for my connector specification. I ended up writing it after the NASA fashion, using pictures from our own connectors. I’d like to give credit for the perfectly terminated connectors that went out on our devices after that to my wonderful specification, but I don’t think anyone ever read it. In the end my coworkers were professionals who cared about their work. As soon as they had the right tools and right knowledge it wasn’t an issue anymore. It was a more important lesson to learn. Standards are good, but only in the hands of competent people.
[Main image source: Mona Lisa protection shield by Cayetano CC-BY-SA]
“A previous engineer had informed everyone that it was perfectly okay to solder a connector after crimping.”
And that kind of person often doesn’t listen when they’re told it does more harm than good. And they’ll claim they’ve done it that way for X number of years without problem.
“This instruction was added because, previously, the crimps were performed with a regular pair of needle nose pliers and they came undone… a lot.”
Ay carumba.
Ay Carumba indeed!
I hate it when someone thinks that they’re “saving the company money” by not buying the expensive but correct tool for a job. They just push the point of failure down the line – and multiply the pain on the process.
Save EVERYONE the headaches and just use the right tool for the job.
Still brings back nightmares…
You should at least flag it or mark it in some sort of errata to save everyone the head ache.
Brings back memories. I did electronic assembly on a couple of NASA spacecraft while in college in the early 1970’s. Just going through the soldering school to get certified took over a week. A couple of years later I assembled a Heathkit HW-8 low power ham transceiver using the same assembly procedures as much as possible. The RF output transistor kept blowing up, but I never had a failure due to a bad connection!
I’m impressed! Which craft? Did they fly? Where to? I’d be satisfied for life if something my own hands had built was out there on Mars, or on a Voyager probe, or something.
A detector on Orbiting Solar Observatory 7 for low energy X-rays from deep space. The other was a net flux radiometer on Pioneer Venus. It is now a sulfuric acid corroded lump on the planet. I don’t think any of the stuff I assembled on PV was the actual flight hardware. I left before then.
But what was the reason for the blown transistor?
Device was over-pressurized with blue smoke.
A lot of Heathkit stuff was under spec’d. Also it was pretty early and no protection circuitry. And sometimes I had the wrong antenna on it providing a poor impedance match. :-)
Gotta hate it when the incompetent of the world mess everything up. :P
As an addendum, for coding styles, it’s hard to beat Carmack’s guidelines for readability: http://fd.fabiensanglard.net/doom3/CodeStyleConventions.pdf
“Use real tabs that equal 4 spaces.”
I agree, but I’ve yet to meet another Python programmer that also agrees, much less the majority needed to use that style on a project.
I’m with y’all. Tabs should be tabs. That’s why they’re there. That function (aligning things in columns) is what the tab _is_. Whether you display them as 2 chars or 8 chars is between you and your editor.
But we’ll never convince them, and it’s not worth fighting.
:set expandtab
:shed tear
Yes, between you and your editor. And between you and your terminal, when you use `cat`, `grep` or `git diff`. And between you and your printer, if you print things.
And even then, if you have anything lining up on the right hand side *after* text on the line (say, comments to the right of the code) you have to go back to using the preferred tab width setting of the original author if you still want that to line up, since that comes after a mixture of tabs and single-space-width characters.
The original point of the tab key – or so wikipedia tells me – was to move the page to the next defined column so that a person using a typewriter wouldn’t have to hit space and backspace a bunch of times. Given that, using the tab key to generate an automatic number of spaces seems consistent with the historic usage and the modern purpose.
At the time, there was no difference between a four spaces and a tab because your only record was blank space on a paper.
Now there’s word-processing, using a computer to remember the keys you have typed while also being able to edit history. In that context, remembering that a tab key produced three spaces (to align with the next tab stop) makes zero sense, so instead the literal tab character was used so that the original intent (align with the next tab stop) could be preserved.
It defaults to 8 spaces. 4-space tabs are a vim config option.
yea some of the suggestions on there don’t play well with popular “auto-format”ers, especially that one
Only poor autoformatters can’t handle a perfectly valid character that is accepted by the compiler.
nah dude i mean they try to enforce their own, different rules, like turning tabs into spaces, removing intentional whitespace, etc
Glad I never worked for Carmack. Who else puts spaces before _and_ inside their brackets?
I imagine an attempt to push code like that to Linux would provoke a reaction…
That’s a horrible spec.
Pad parenthesis? All functions start with a capital?
Recursive end with _r?
Come off it, this was clearly written by some anally retentive loon.
https://en.wikipedia.org/wiki/John_Carmack make of him what you will :)
Having the right tools really can make all the difference.
Good post, I look forward to reading (okay, skimming) through the NASA manual.
In the 70’s and 80’s I had friends who worked in the aerospace industry. They would bring me bags of crimps that did not meet aerospace standards but were great for me! I also miss their surplus sales. They had everything a hacker could need for almost no money.
This is my goto document to prove how much current you can pass thru a ribbon cable:
Ampacity Test of 28 AWG Ribbon Cables
http://lss.fnal.gov/archive/tm/TM-1657.pdf
That was a good read! 2.5 amps/wire in a ribbon! Which is kind of in line what I have seen on the mobile phone market with the upwards being 2-2.5 amps on non USB 3.0 devices. I’m off to power my house with a generator connected up with a few IDE cables…wish me luck!
I remember some specification on how to solder and/or make fixes for PCB. I believe it was IPC and always wondered if there was a harness specific book.
It has been years since my pro PCB design era. Anyone has more info on IPC ?
Maybe if everyone read the NASA standards, we could finally kill the existence of those idiotic split washers that people use for “locking.”
NASA’s Fastener Design Manual’s got a fantastic comment on them: “The lockwasher serves as a spring while the bolt is being tightened. However, the washer is normally flat by the time the bolt is fully torqued. At this time it is equivalent to a solid flat washer, and its locking ability is nonexistent. In summary, a Iockwasher of this type is useless for locking.” No pulling punches there – they suck, don’t use them.
Then the washers are incorrectly designed!! A proper split washer is curved in opposite directions at the split, and has a sharp edge on either end of the split one digs into the nut, the other into the metal beneath the nut, and prevents loosening very effectively. modern washers are poorly designed and manufactured, and you would have thought that the highly quali8fied and paid engineers at NASA would understand this!
Here’s what I don’t get. Even if this works as you say, are you not just locking the bolt head or nut to the flat washer that everyone puts under the split lock washer? I see bolt head, split washer, then flat washer, far more often than just a split washer alone without a flat washer underneath. This has never made any sense to me as it seems to me the flat washer negates the locking effect of the spit washer.
Split washers are not designed to prevent the nut from rotating off the bolt, but to keep pressure between the threads of the nut and bolt to allow friction to do that job. The flat washers are there to prevent the nut/bolt head from damaging the work while being rotated.
Interesting. As they note, the cables are still conducting while the insulation is burning. Unfortunately the connectors are the part more likely to fail (https://www.instagram.com/p/BMUdGmzhWfV/). That photo is from a tube guitar amplifier and the ribbon carried a few amps at 6.3V AC. Any corrosion on the pin or mating connector causes resistance which causes heat which causes…
This was supposed to be a reply to Wolf above 8-{
Eek, that bus bar is a fire waiting to happen.
Hey that bus bar doubles as a night light! Who needs vacuum tubes, let us warm ourselves by the glow of the bus bar.
Holy crap on a cracker.
nah, the good old indication LED =D
If I remember right that was a mains buss bar in india.
S’mores anybody?
I see the problem already. None of the other connections are red.
Cut backs.
They say anyone can do a electricians job. Go to school for 3 months and you are a electrician,
Yea right. At the time it took 5 years to get a license. I did it and got more licenses.
Then the government bring in so called trades people that are using the cheaps (toys are us) tools to our country because they say there is a shortage of trades people.
Mean while I know a lot of trades people that are out of work and have been for over a year.
Then there are the contractors that are using 1st year apprentices doing live electrical work.
There not allowed to pick up a tool till there 2nd. And you never work on live electrical.
It would be so nice if we lived in a perfect world. But time is money and if they can push the buck to some one else they will do it. There has been jobs Ive been on that I used a hammer and screwdriver to put holes in block walls because the contractor did not have a hammer drill. ( to say I did not stay on that job long.) And Yes I had tools at home that would of done the job. But I paid for those tools not the contractor.
I am very proud of the work I have done over the years using the right tools. And my work was ART…
But some times the so called right tool is not the right tool. That’s how new tools get invented.
You have to use your head and use what you learn and Always keep a open mind and learn. And then learn some more.
Never stop learning.
Amen to always learning and constantly improving one’s mastery of their craft. Unfortunately this seems to be something that is sadly lacking in a large portion of the workforce. I cringe when someone honestly means it when they say “Good enough for government work”, especially when it pertains to a military vehicle that soldiers/sailors are staking their lives on. I know what it feels like to receive that shoddy product and have made people tear apart half a vehicle at the cost of $1000’s of dollars or material and labor. Right is right and anything less is completely unacceptable. To hell with corporate penny pinchers and project managers that don’t agree with it.
…hammer and screwdriver… Not only this wastes time, but also the screwdriver :-(
Why is the ratcheting Molex crimper so &@&#$ expensive? Is it really any better than the $20-$50 options on Amazon? Just to make a buck on large companies who have the cash to burn?
That’s what really grinds my gears… Freaking multi-hundred dollar crimpers. Whatever happened to the “give away the handle and sell the blades” model that did so well for Mr. Gillette & Co.? Yes, it took resources to design crimper mechanisms, but that money’s been made back multiple times over. Quality tools should be accessible… not reserved for profit center use in selling at a massive markup to govt (and industrial concerns bound to govt specs).
(/Whine mode=off)
Having used official crimpers and knockoffs I will say the real ones are better. Less sticking of the connector in the crimper. The dies are harder and wear longer. Which brings up another subject, the crimpers must pass calibration for aerospace stuff, so a high quality one costs less than a bunch of cheap ones that wear out fast.
But the cheap ratcheting one ($15 at Aliexpress) is still much better than using needlenose pliers or this crappy “multi-crimp pliers” stamped out of thin sheet metal (2,5 to 3mm) which bend when you try to apply the needed crimping force. And I don’t like the pre-insulated crimp contacts which you crimp through the plastic sleeve. They are usually sold in a kit with said crappy crimp-pliers.
What is another widespread bad habit is pre-tinning a stranded/litz wire before it goes into a screw terminal. The tin creeps under the pressure of the screw and the result is a loose connection.
Yeah, they are. But he was asking why anyone would spend $$$ on a real crimper.
The insulated terminals are fine if you have one of the nice hex die crimpers.
I just can’t believe that anyone would believe that needle nose pliers would be acceptable as a crimp tool for a professional product. As a quick hack for personal use ok, but a final product no way. This is especially unacceptable as most of those connectors usually come with directions that tell you how to properly put them together and attach them to the cable.
As a side note it is extremely important to check the tool required. I once tried to stretch a material budget for a project I was on by saving 10 to 25 cents a connector only to find out that without the $1000 crimp tool it was impossible to put the connector on the cable without the final cable being dodgy at best. Lesson learned: if the connector is considerably cheaper than the alternatives, there is usually a really good reason.
Oh my. Nice read – thanks for posting this.
Back in the early 80’s when I was in school to become an “EE,” I worked at a place that built military electronics. I had to get Milspec (454 was one I recall) certified and then later “NASA” certified to work on a satellite comms board. After learning the basics and passing the qualifications, placing electronic components and soldering them became an art form. I’ve used that experience to some length working in automated systems, radio and even in consumer electronics since then.
Fast forward to today.
It seems that the lessons learned from our military and space agencies are simply tucked away in silos and mostly forgotten now. The soup du jour in engineering and product manufacturing seems to be to jam it all out the door before someone else beats us to market. And software development is the worst offender here – making a bad situation worse is when you mix in some software-centric engineers with hardware system engineering. This, as we say, results in “predictable outcomes.”
Outcomes like failed product launches, bankruptcies, layoffs and offshoring as a direct result of inability to manufacture a product or system to meet established requirements and standards.
It seems anymore the trend has become to assume all engineers are “equal.” It is an unfortunate and often project-fatal poor assumption that generally speaking, is a load of hoo-hah. People whose careers have been predominantly birthed and educated in software typically don’t make good hardware decisions. Managers who aren’t technical have no background or capacity to understand the difference, and blithely make incomprehensibly bad personnel hiring decisions.
I call this a symptom of “software thinking in a hardware world.”
It isn’t because the software devs aren’t capable, its generally because they only know and follow the most streamlined of processes to accomplish their work tasks. Typically, that’s a white-washed, thinly coated variant of ‘Extreme Programming’ – be it “Agile” or some other fancy name. When confronted by the harsher realities of the hardware world, most of them (without prior training or experience) fold or fail all too quickly.
These kinds of resources – the NASA workmanship standards – might help produce a better batch of engineers if they’d promote their use from within some of our exalted learning institutions.
Begin early, learn early, train and test. Rinse. Cycle. Repeat.
Engineers should think of their vocation to be a practice, just like medical and legal. Never stop learning and never stop seeking to improve, even if it means changing “how you’ve always done it.”
Cheers.
Well said. “Agile” programming (i.e. failing to do requirements planning) gets by in the software world because you can often update your software or website after it’s live.
You can’t undrill a hole in the field with the press of the delete key.
Software developers today have their programming processes like Agile, then sit down and write Object Oriented code. Burning endless amounts of time questioning the metaphysical nature of the universe in relation to their types. And all you get is graph of garbage with no encapsulation and what is best a shared state.
It’s a train wreck on productivity and then at some point mass hysteria kicked in and DI became a thing along with factory’s.
And it I don’t think there is any end in sight to the pseudo engineering that software developers practice with OO. The tools aren’t fit for the task.
All car wiring harnesses, and commercial vehicle harnesses used to be soldered connections, which very effectively sealed the moisture out of the interface between cable and connector. The result of this was many years of zero connection failure. Today everything is crimped, and the failure rate is huge after a couple of years of service. The only reason for crimping is to sell vast numbers of crimp connectors and very, very overpriced crimping tools because they do the job faster, and the skill of soldering is not neccasary, in other words, they can (supposedly) be fitted by unskilled labour. All about making profit and nothing whatever about doing it better!
Do you have any evidence for that? Crimped connections are gas-tight and when done properly are superior to soldered connections.
Yea that’s true, but crimping tends work better on larger cables in my experience. A good crimped lug should basically press together as one solid. It’s harder to do that on smaller wires. Otherwise, the difference is pretty minor, but the largest benefit of soldered connections is it tins the copper protecting it from oxidation. However then you need make so no ingress works it’s way into the insulation. That’s a different problem though. However, solder is bad idea next to anything that may get hot enough to melt it. Further, anything that may experience a large surge of current in a fault situation like a grounding cable. Solder can also have problems with fatigue due to vibrations, and mechanical strain.
In my experience crimping is better if the wire size AND the lug/crimp size are matched, AND the correct crimping tool is used. I used to be a ‘solder’ guy, but I’ve been converted to crimps (when done right and with the right tool).
If the sizes are wrong, and especially if those cheap-and-nasty excuses for crimping tools are used – the results are truly pathetic.
To address your points, all ‘external’ (outside the cab) automotive connectors I’ve seen are weather proof, and crimping has been done very well. I’ve seen very few failures due to poor crimps. Most crimp connections have a built-in strain relief (not fantastic, but certainly better than a soldered connection onto the same tab).
‘Internal’ connectors are very prone to corrosion if they get wet, destroying the wire/tab and tab/tab interfaces no matter what. Don’t sit your open coke bottle/can on the dash while driving…!
Matching the sizes of the wire with your connector is pretty important. If the wire is too small for the connector you get voids and damage the crimp terminal. If the terminal is too small for the wire you end damaging the wire or the connection may not be rated for the intended application anymore. Also just as with solder any junk or dirt inside your crimp is bad news. Also crimping to hard usually the result of an improper crimp till can cause fractures in the terminal. After time it will work loose.
Especially as Coke is pretty acidic (pH3) and therefore a very good electrolyte.
I’ve never seen a soldered connection on a car or commercial vehicle of any age used outside a sealed box. Your assertion that there was some transition from soldered to crimped joints is not correct.
There is one welded or soldered splice (I haven’t tried taking it apart to see exactly what the factory did) at one point in the factory wiring harness on my 1966 Dodge Dart. Nearly all the other connections are crimped Packard 56 series terminals.
If you solder a stranded/litz wire in an environment with vibrations like a car then it can very easily break later on at the point to where the tin has soaked in. You have to be very careful about strain relief and vibration damping.
“Part leads shall not be used as terminals, except when the part lead is used as a terminal.
NASA-STD-8739.2 [12.8.2.a.9]”
Slightly confusing…
I was slightly perplexed, then amused when I saw that all the hyperlinks in the article were greyed out… because I’ve been to all those NASA spec pages before. :)
I did rebuilt my 3d printer to meet NASA standard last year and really happy with it. Before it had a lot of bad solder joints that caused random fails. Now it uses high quality crimped connectors, which make maintenance and upgrades very easy.
I also learnt a lot from CE machine certification, now it can’t catch fire even if software fails, easily accessible kill switch, won’t crash or fail a print due a M3 earthquake, a black out or bugs.
Good about the software failures. I’m too often hearing: “this drone is safe above crowds because it has a low battery warning” – or an extra whatever. Or I hear “oh these never catch fire so I’m fine putting this lightbulb in a closed cardboard box” – and so on.
Intrinsic safety is the place to be if the stakes are high.
Buying a $500 tool for Brand X connectors plus a $500 tool for Brand Y connectors plus a $500 tool for Brand W connectors plus a $500 tool for the other family of Brand X connectors is obviously rubbish – not going to happen.
If I needed to make such a large number of cable assemblies – or if the cable assemblies absolutely could not be assembled with acceptable reliability without expensive specific tooling – then I’d simply outsource it to some Chinese cable assembly specialists who have set up the correct dies and tooling and line to do it, and who can economically justify this.
To be honest I’ve never successfully understood “real crimping” of JST/KK/DuPont/etc pins at all.
How the hell is it supposed to work? How is the tool oriented relative to the pin? How far is it inserted? Which jaw to use? Are the $15 AliExpress Plato ratcheting crimpers appropriate, or not at all?
How on earth do you get the pin plus the wire to stay together and be held in position for insertion into the tool? Crimping both parts that need to be crimped without damaging the front of the pin seems impossible.
In my experiments it has never worked successfully once – so I go back to what I always do – careful crimping with needle-nosed pliers. Plus a little bit of solder – and it works securely and reliably every single time with the same amount of labor.
It takes practice.
I did really well with $10 Radio Shack non-ratcheting crimper. The $15 Ali ratcheting crimpers are probably OK. I bought mine from Inventables but I think it’s just a Chinese too, though a decent one.
Soldering a crimp is just a band-aid that risks unnecessary problems.
Like anything else, it takes time and practice to do something accurately and skillfully. If you don’t have the patience to work on either, you will achieve neither.
Actually NASA no longer uses their own standard for “soldered electrical connections” and has instead recently started going with the IPC standard, including the addendum for space qualified things. For everything other than soldering, the NASA standards are still in use. The standards are just as much about inspection as they are about actually performing the work, which is not a bad approach.
One of the most important things I learn in trade school, is that most codes are evidence and research based. Much as I dislike the insurance sector, I have no problem with the NEC, even though it has to be a balance between fire protection, and affordable standards, not to mention the balance between the corporate profit and the consumer being able to afford both insurance coverage along with safer construction. The literature provide by equipment providers was an eye opener as well. Both the article and many of the comment are informative. The best Hackaday has to offer, any why for many Hackaday is a must visit resource.
For convenience, I compiled all the different sub-sections into a single PDF reference. It is available on the Internet Archive at https://archive.org/details/nasa-workmanship-standards