Someone who decides to build a house faces a daunting task. It’s hard enough to act as the general contractor for someone else, but when you decide to build your own house, as my parents did in the early 1970s, it’s even tougher. There are a million decisions to make in an information-poor and rapidly changing environment, and one wrong step can literally cast in stone something you’ll have to live with forever. Add in the shoestring budget that my folks had to work with, and it’s a wonder they were able to succeed as well as they did.
It was a close call in a few spots, though. I can recall my dad agonizing over the wiring for the house. It would have been far cheaper to go with aluminum wiring, with the price of copper wire having recently skyrocketed. He bit the bullet and had the electrician install copper instead, which ended up being a wise choice, as houses that had succumbed to the siren call of cheaper wiring would start burning down all over the United States soon thereafter.
What happened in the late 60s and early 70s in the residential and commercial electrical trades was an expensive and in some cases tragic lesson in failure engineering. Let’s take a look at how it all happened.
Cheap or Good – Pick One
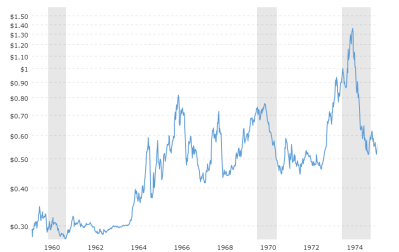
To understand the aluminum wiring fiasco, it pays to keep in mind not only the material science and electrical engineering issues, but also to the market forces that made aluminum wiring in residential construction so attractive at the time. Worldwide copper production had been high through the early 60s, but voluntary production limits to reduce the glut raised prices a bit. At about the same time, the escalation of the Vietnam War and a home construction boom increased demand for copper, while nationalization of the copper industry by overseas producers and strikes by miners crimped supply. Squeezed at both ends of the supply-demand equation, the price of copper nearly tripled between 1962 and 1964.
Copper wire had long been the standard for residential and commercial branch circuit wiring, the runs of wire from the load center to the lights and outlets around the structure. Electricians knew copper well, electrical codes were written around its performance characteristics, and equipment manufacturers engineered switches, outlets, and connectors specifically for copper wire. But as entrenched as copper was, increased prices were starting to turn copper wire into unobtanium, and electrical contractors began to feel the squeeze on the bottom line. Something had to give.
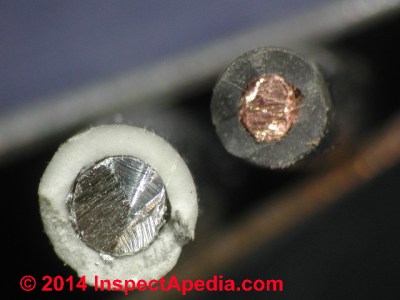
Enter aluminum. Aluminum is an excellent electrical conductor — ignoring the precious metals, it ranks right below copper on the conductivity chart. Aluminum has long been used for electrical wiring, but mainly by utility companies for overhead wiring in the distribution system, where its light weight and low cost are huge benefits. Aluminum has also been used in residential construction, mainly in the service drops from utility pole to meter and on into the load center. But while aluminum had been common in the higher amperage branch circuit wiring for electric dryers and ranges, it wasn’t used for the lighter branch circuits that make up the bulk of a house’s wiring. All that was about to change.
Wire manufacturers began to produce aluminum wire for 15 A and 20 A branch circuits in response to the copper crisis. Such circuits are usually wired with 14 AWG and 12 AWG copper wire respectively. But as good a conductor as aluminum is, it’s still only about 60% the conductivity of copper, so aluminum wire for branch circuits needs to be stepped up to the next AWG size — 12 AWG for 15 amp circuits, 10 AWG for 20 amps. Manufacturers had to use more metal, but aluminum was so much cheaper that it made economic sense. And so aluminum wire began to make its way into residential branch circuits, to the tune of two million homes between 1965 and 1972.
Creeping Out
This decision would backfire for a couple of reasons. Foremost was the aluminum alloy that manufacturers chose for the wire. Utility wires use an alloy called AA-1350. While perfectly fine for use in overhead and underground distribution systems, AA-1350 is essential pure aluminum with a few trace metals added, and its physical properties differ markedly from copper. Because of its higher thermal expansion coefficient, AA-1350 aluminum exhibits significant creep, where the wire deforms as it expands and contracts due to heating.
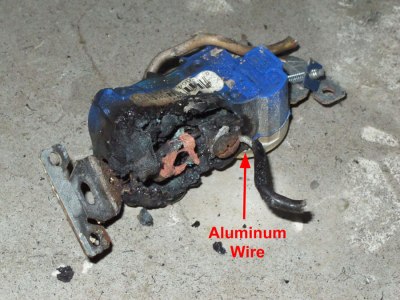
Creep can be very bad in an electrical connection. Any conductor heats up as more current flows through it, but aluminum expands more than copper due to its higher coefficient of expansion. The expanding and contracting wire can actually unscrew terminals, loosening the wire and causing arcs, which cause more heating and more creep until finally creating a source of ignition inside the walls of a house.
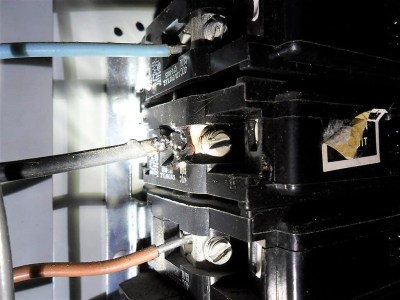
Creep is exacerbated by incorrect installation, too, which tended to happen a lot as electricians switched from copper to aluminum. Aluminum is much softer than copper, so proper torque of screw terminations was harder to achieve. Aluminum also oxidizes rapidly when exposed to the air, forming a thin insulating barrier that can increase the resistance of a connection. Aluminum wires were supposed to be treated with anti-corrosion compounds before termination, but rarely were. And manufacturers of outlets and switches were slow to adapt their products to the needs of aluminum, resulting in dodgy connections that were even more prone to creep.
Finally, basic chemistry seems to have been ignored. Recall that galvanic effects occur anytime dissimilar metals come into contact with each other. All that’s needed for that to induce corrosion is a little electrolyte, like condensing water vapor from warm heated air infiltrating a cold exterior wall and wiring. Corroded connections are high-resistance connections, with predictable results.
The End of the Line
As aluminum-wired homes started burning, fire marshalls and insurance adjusters couldn’t help but notice the problem, and the days of wiring houses with AA-1350 were brought to an end. By 1972, the electrical industry had revamped aluminum wiring, straight through from revised electrical codes specifying new formulas for aluminum wiring sizing to the device manufacturers, who changed their products to be compatible with aluminum wire. Wire manufacturers changed their products, too, devising new alloys in the AA-8000 series that incorporated iron into the mix to reduce the tendency for creep.
None of this saved aluminum in branch circuits, though. By the mid-70s, aluminum was gone from most branch circuits in new construction, but not before the damage was done. There was a huge installed base of aluminum wiring, and houses from that era are subjected to extreme scrutiny by home inspectors when they change hands. The aluminum wiring fiasco spawned a range of products to mitigate the risk, from fantastically expensive connectors to special crimps that cold-weld the aluminum wire to copper pigtails. Removing the aluminum branch circuit wiring completely and replacing it with copper is also an option, albeit an expensive and disruptive one.
The industry’s foray into aluminum proved to be a costly lesson about what can happen when market forces collide with engineering best practices.
So, buying cheap things without undestand they are you cannot expect quality ?
/undestand/understanding what/
Quality is one thing, safety is another.
The issue here isn’t really that the wiring was cheap. It was just that people didn’t know how to use it safely and apparently it’s not a drop in replacement for copper wiring.
there is another issue with AL wire, heat and moisture cause it to break down, I lost my main ground it was down to 2 strands the rest was dust. It cause a cross over in hot leads jumping voltage up to 200 v which showed as a dimming/brightening of my led bulbs.
Interesting, ive noticed this phenomenon a lot at my inlaws house on certain circuts
I put a 100A subpanel in my home, and the electrician I consulted told me to run in with Al as its about 1/10th the cost. To paraphrase, if you install it properly, there is no danger. The wires coming into your house from the street are 95% Al anyway, and nothing has caught fire yet! The trick is proper torque, rated connectors and no-ox.
6yrs later, my connections get inspected annually by me, as well I’ve had the ESA check it, and no issues. If done right there is no danger, the problem in the past was copper only switches etc that were connected to Al wire.
Yes, Al wire is safe if done right. Part of the problem with Al branch circuits is that homeowners often replace switches and receptacles without knowing the correct techniques or connect light fixtures with wire nuts.
I can attest to this, as a homeowner. My house has Metal-clad going to metal boxes. Inside of the MC there’s an insulated black and white, plus a bare aluminum conductor. It’s not a problem when terminated correctly. The MC is actually the ground and the aluminum is either cut off or bent back on the outside of the MC before being inserted into the fitting. But in a few boxes a previous homeowner had connected that aluminum to the ground screw on the receptacle, and even wire-nut with copper in boxes with multiple receptacles. That behavior doesn’t worry me (I’ve fixed it all now), but proves the point that when faced with the unknown people do whatever.
Pfft! They do that when we’re talking about copper. Aluminum is just less forgiving.
I have done that at the insistence of inspectors. It isn’t right, but it isn’t generally an issue, as when it works loose, it usually won’t move enough to contact anything that is live. My preference is to use metal clad with ground (green insulated ground wire in the US). The armor still needs to be bonded, but, with aluminum armor, the ground is generally more reliable with the dedicated copper wire (yes, this statement can be justified: resistance generally stays at the install value with copper, whereas steel armor in cast Al fittings, and Al classing and fittings in a steel box often show an increase over time, even in the absence of liquid water. The armor still needs to be grounded both ends. Major issue as long as never wet? Probably not. Annoying when you need to do a ground test on an existing circuit before installing a new machine and it fails just over limit? You bet it is.)
It is not about is moving and touching something. It is about coming loose in the connector, oxidizing and becoming a high resistance connection that gets hot and eventually melts the aluminum core. The oxidized aluminum is aluminum oxide which has a pretty high melting temperature but the inner un-oxidized aluminum has a much lower melting point. This causes your connection to collapse from within and lead to an even looser connection.
For a grounding connection, it is not carrying current for a long period of time (hopefully) so heating is less of an issue. For the ground connector to maintain connection it only has to have a lower resistance to ground than you and provide a good enough connection to flow enough current to trip the circuit breaker of the load.
The metal cladding is NOT the ground. The Al. ground wire is the ground, and is bent back as you described so that the MC armor is bonded to ground. Spiral Al tubing oxidizes just like any other Al, and in an extreme case could cause the ground current to travel the entire length of the spiral. That might be enough resistance to prevent the breaker tripping whilst simultaneously acting as a heating element, quite possibly buried in insulation of indeterminate age and flammability. The Al. ground wire exists to provide a low resistance path ground to prevent that from happening.
If you have thermal expansion issues with your ground connection then you have something bad going on – ground should never see current except during a fault condition. I’m not familiar with NEC requirements on ground connections for Al. grounds, but I’ll go out on a limb and guess that they require mechanisms specifically UL listed for use with Al..
Occasionally electrical wiring devices may require UL testing to be listed in the White Book that complies with the NEC wiring requirements. Most modern receptacle and switch terminations are UL approved for copper wire hookup only. The aluminum wiring must be copper wire pigtail spliced in order to connect to any commercial or residential grade receptacle and switch devices. The manufacturer instructions are normally compliant with UL listed requirements unless special configurations are acceptable by the AHJ approving authority. R Benton Jacks
One issue is most switches and outlets are designed for 14 or 12 gauge wire and forcing the larger Al wire into them can cause a poor connection or damage the wire.
Your electrician was correct. It is perfectly normal to use aluminum for feeders because they are not usually messed with by home gamers. If they are properly prepared with de-ox compound and torqued to the correct specs there is not a problem. When people replace outlets and switches and such they don’t take the proper care with the aluminum and that is where problems start. Also a lot of fixtures include copper wire leads which get wire nutted to the branch circuit. If you make that connection from copper to aluminum it will oxidize and create heat. For feeders it is hard to source copper in really large sizes and if you can, its gonna get expensive real fast. The power company uses aluminum feeder as a cost control concern and in outdoor and underground connections, the connection methods are different and heat is less of a factor.
How in the world did you get the European Space Agency to inspect your home wiring connections?
Probable danger.
The other ESA: https://www.esasafe.com/
when i put in a subpanel, I couldn’t get copper wire locally. I asked at a couple of places.
Aluminum in subpanels w/modern installation techniques and materials are 100% fine.
It’s using it for a bunch of 15-20 amp branch circuits, mixing it in with existing copper, etc that caused the real problems.
This. Aluminum is a standard code rated material for hundreds or thousands of amps in many modern applications under US and other code. Just not most small branch circuits. Those overhead three phase transmission lines you see along roads or as part of large power transmission lines? Aluminum. Lighter, cheaper. Especially at higher voltages.
“The industry’s foray into aluminum proved to be a costly lesson about what can happen when market forces collide with engineering best practices.”
More like: when design changes are made without sufficient prior experimentation. I suppose that in itself is an engineering best practice, however, had the aluminum wiring push been handled by a more thorough engineering program management, it would have worked fine (see the AA-8000 conclusion), and it would be cheaper than copper wiring. So if expensive and works is “best practice,” then cheaper and works must be “best engineering.”
Throughout all aspects of engineering (electrical, mechanical, aero, software, etc) the same basic rules hold, and are routinely ignored. When you make a change to a system component, you need to requalify the system, not just the component.
@p Or to say it another way, changes made to a system, (electrical, mechanical, aero, software, etc) the individual making changes should be smarted than the engineer that designed it. (Not likely)
Not necessarily smarter, but he must fully understand all the original design parameters, including luck. That rarely happens.
Rather amusing that this post about misuse of aluminum without sufficient prior experimentation is right on the same page as a post that starts with an Ayn Rand quote. I put down Atlas Shrugged after I found myself re-writing the first bit of dialog between James and Dagne Taggart to give James a more plausible reason for objecting to the way Dagne had placed an order for a thousand miles of railroad rail stock made from an aluminum alloy that had never seen any testing outside of a lab, instead of having been discretely testing a couple miles for the past year or so.
This.
“Any damn fool can build a bridge strong enough to drive across. It takes an engineer to build a bridge *just* strong enough to drive across.”
Point. But make a mental note comparing early VCRs and the latter ones. Less materials used overall, and different. e.g. plastic where metal use to be used. A design *just enough* to work, if not last.
I have aluminum wiring in my house because it was built in the 50’s. My house purchase price was reduced from the asking price by the appraiser because of it. I’ve spent hours adding alumiconn or ideal twist connectors to ensure my house doesn’t burn down. This is a real problem that still exists today, especially since there are tons of old houses out there. The connectors are expensive, but so are the insurance costs. You are required to disclose this type of stuff because it’s a fire hazard.
This article explains the issue well. The coefficient of expansion is larger with Al compared to Cu. Screws and terminals come loose as older equipment ages, and the risk is higher with Al. I’ve got tons of stories of elevators not working because terminals came loose. Is a short term cost savings worth the risk over the long term? I guess it depends on how often you want to inspect your equipment, and whether you are willing to reduce the worth of your house.
I also remember reading that aluminum doesn’t handle flexing as well as copper does, which is a problem with outlets that would move a little during plugging and unplugging.
^ this. As a scrapper, I’ve noticed that aluminum wiring is increasingly used found in cheap-ish home appliances like microwaves. Theoretically internal wires don’t flex too much but i don’t buy that.
Are you sure its not stranded tinned copper? I do know some microwave oven transformers use AL magnet wire for the primary winding but that isnt really a big deal, its a coil coated in varnish, then soldered in two places. Not much can go wrong.
Yes, quite sure. Copper is like the scrapper’s gold so we do check for it. And yes, a lot of microwaves have Alu wiring in the transformer as well. Kinda ruins the fun of scrapping them…
You see a lot of aluminum in inexpensive transformers and motors. The thing is they varnish it just like copper wire and it is really hard to tell without scraping through the varnish;
There’s nothing wrong with using aluminum wire in anything including appliances as long as you understand aluminum’s properties. Aluminum wiring could even be used in house wire with everything understood today. The last box of outlets I looked closely at were marked AL/CU (rated for aluminum and copper) which tells me that they’ve figured out how to make the failure point (the screw terminals) safe.
Doesn’t reducing the appraisal save you money every year in property taxes? If you can save money on the installation and convince yourself you can do it well enough to be safe, seems like a win-win to me.
It can also increase the insurance costs and reduce the sale value of the house.
Not in most of the US. Tax appraisal is by formula (land area, structures and their size, occupyable structure features such as number of bedrooms and size of each, number and size of baths, other rooms, windows and features (skylights added about $1000 to my tax appraisal) finished basement, fixtures, like a laundry sink, and so on), and, at best, somewhat relate to market value. My tax appraisal is more than twice my market value. The appraisal is adjusted by rate (in my area registered by block) that depends where the property is. If it is too far out from market, you can, in theory, appeal. In my area, the appeal rarely works unless there is either a formula error or it is found that the rate is incorrect.
The type of wiring, crappy paint, and, for that matter, termites and holes in the floor, do not influence the tax assesment, in general.
Insurance rates are tied to market/replacement value and risk assessment, including things like distance to fire plug, wiring type, age and condition of electrical, age and condition of gas service, structural considerations, and things like termite damage, crappy paint, and holes in the floor (all of which lower value but increase risk, so you pay more for less protection).
Reference: pretty much and states property assessment standard formula.
I had an older house that I wanted to upgrade from 60A to 200A service. Everything had to be updated to meet current codes. I ended up taking 3 years to remove and replace all wiring, as it lack a ground conductor. Once done, each room had its own dedicated breaker, as opposed to 7 fuses supplying an entire 5 bedroom/2 bath house.
When I removed the old meter base, I also found the wire jackets showed signs of melting. Two four-fuse boxes were side-by-side and jumpered together using split nuts. Found two of the circuits were connected together, so pulling one fuse did not deenergize the branch (found that out the hard way). There were numerous other minor sins, too many to list. Don’t know why that house never burned down.
My “new” home was built in the 90’s, and was done correctly, as far as I can tell.
What a timely article. I just purchased a home with aluminum branch circuits (yes, knowingly). This summer I will be embarking on a full copper retrofit, panel move, and subpanel for the garage. It’s a fairly large task, but being able to do most of the work myself makes it affordable.
Any data on fires caused by using “back wired” receptacles? I have owned two house that were wired primarily with the push-in back wire connections instead of the screws and found quite a few that had failed or were showing charring.
Like with Al wire, changes have been made to correct early issues. That said, I still don’t use back stabs (spring contact back wire method), as they still can fail for a number of reasons.
I do use several flavours of back wire with captive screw clamp (insert the wire through the guide hole and tighten the screw, rather than hook the wire end)
I love the new captive screw back wire, it’s the old “push it in and hope” type that I have issues with.
I’ve replaced a bunch of push in type outlets that were getting hot. Don’t care what anyone says, won’t use them. Not when a high quality outlet costs two bucks more.
The type with the captive screw + clamp are probably more reliable than than the wire under the screw type. The clamp is actually a stiff copper alloy spring so it won’t creep with temperature cycling. That is standard for industrial screw terminals since the 1960’s.
I remember when they first came out. I had my doubts but used the backstab anyway, hey, it was UL listed. By chance, I remodeled a kitchen for a friend who bought a home I wired some 20yrs earlier. It was a house that I used the backstab method on. The receptacles/switches literally fell apart when I took them out to rework some circuits. High resistance, heat-induced damage was obvious. Makes me wonder about all the stab in connectors that are used in place of wirenuts nowadays.
I replaced every receptacle in my house after having a few fall apart like that.
My clothes dryer stopped working intermittently. So I checked all the connections in the dryer. No luck. On the off chance that somehow my (brand new) home had a problem with the dryer outlet wiring, I opened it up.
Back-stab? Not quite. The person who had wired it assumed that it was a back-stab, even though it was actually a back-wire outlet that required the screws to be tightened. My new house was wired to burn up.
Did an electrician make the mistake? Unlikely. More probably the contractor had hired a plumber’s friend to do the wiring.
Do they even make back stab style 50A or so connections anywhere? Not sure what country you are in (and therefore the voltage and amperage) but typically if you are US based, your dryers are 40A or greater connections and I have never seen one of those even be back-stab style.
He could have a gas dryer and be talking about the 120v outlet.
Given the other pary’s description they where referring to an all electric clothes dryer. And that whoever ran that 540 V. circuit failed to tighten the screws present to secure the conductors
Negatory! It’s a 240-volt connector, probably 50 amp, but I don’t feel like looking right now. The connector was not back-stab, but the “plumber’s nightmare” who put it together apparently thought it was. Strange, because the rest of the house is 20A with proper side-wires, using screws like honest electricians do.
My current project is to fix the electric fence for which I paid someone to install the insulators. They are done wrong and cannot stand the wire tension pulling on them. Wait a minute, that’s not a CURRENT project. It’s a POTENTIAL project. Hmmm. I guess I mean a VOLTAGE project.
In the USA ranges are typically 50 A. , because that would require a stranded conductor it’s unliky they would have a push in option C all electric clothes dryer are typicaly30 A. that can be feed with a solid conducr, but I never ran across a push in option there.
Yeah, 6 outlets in my shop stopped working last year.
It turned out whoever wired the outlets used the back stab of the GFCI outlet that the others daisy chained from.
I brought the charred outlet to work to show my cow-orkers.
The devices are still available for use. Clearly the insurance industry’s lager sampling doesn’t reveal a wide spread problem. Not to degree that those when extremely small data sets want to indicate there is. The insurance industry exists to earn profit. When it comes to the codes they recommend, they aren’t going to be so permissive to incur losses, nor are they going to be so restrictive that it’s nots affordable to construct buildings.
“nor are they going to be so restrictive that it’s nots affordable to construct buildings.”
Yup. Trump can still afford to build things.
It’s just not for people with a sub six figure salary. (Depending on locality of course.)
Insurance companies don’t want to eliminate fires/risks because then people would have no reason to pay insurance – they never want to make themselves redundant.
The risk must always be high enough to keep the premiums up, and the way they make profit is by denying you coverage because of some sub-clause or other catch-22.
Devices with the push in connection option have been available for decades now. Where they are still available. most likely means the insurance industry doesn’t have, evidence that they are common cause of fire. Chances are those devices where designed and approved to fix some problem(s) fire investigations revealed.
There is definitely a problem with the spring held backstab devices. Cant tell you how many times I’ve run across the issue but I may be biased being an electrician. The issue probably isn’t recognized because the chance of them causing a fire is slim. Usually, it just creates intermittent issues or will open the rest of the circuit.
Another issue I see is after a decade or so they still are “functional” if left in place but as soon as someone(electrician) physically moves the device it falls apart/fails.
I never use the stab ins anymore even if in a rush, a proper hook/screw method is the way to go, preferably with everything spliced into a single pigtail. I try to use the hook and screw even if the device offers a straight-wire/backstab option with the screw mechanically clamping the conductor.
I don’t think the UK used aluminium for domestic wiring but British Telecom tried it for twisted pairs. A similar disaster ensued though fires were not a problem communications sure were and once corroded it is a disaster.
Aluminium is all right, even. Couple of years ago I bought a length of flat four circuit, single core conductors telephone cable for in-house use. To my surprise, although the conductors have red glow when stripped of insulation, it is magnetic (attracted and lifted up with a magnet)! So I went to another place and bought myself another cable … and it was the same … copper-plated iron (, I guess,) wire.
You’ll see that in communications wire.
FYI, the US Army field telco wire had a mix of copper and steel strands, the steel provided strength to the wire and numerous tiny stabs to the fingers of the Field Telco Specialists.
Good Ol’ WD-1/TT
Ah, so basically, making savings on skin effect?
no. its a mix of strength (steel) and conductivity (copper). we used this finger-friendly cable in military aswell. at voice frequencies you can neglect skin-effect. btw im using this wire as dipole antenna :D as its really strong…
Iron wire, being magnetic, has a significant skin effect at voice frequencies. it’s practically a non-conductor above 300 Hz.
Aluminium wiring still is a headache for British Telecom, I heard figures of about 20% of installed twisted pairs are aluminium in some places….
I was a practicing electrician in the late 70’s, after the aluminum days. And there was still a lot of aluminum installed then. The absolute worse install I saw was where the builder ran aluminum then spliced in copper just before entering into the electrical boxes and just after the main panel. The house was built in 1972. We were called in to solve some weird electrical issues and when I discovered what had been done and told the home owner the cost of a total rewire he said “no thanks” and we left. As far as I know the house is still standing and the witing has not been replaced.
LOL I wouldn’t make a successful crook. I wouldn’t have thought of using AL for the majority of the work and charge for CU.
This was in 1977 and based on when and where the house was built I assumed a major sub found a way to dump leftover aluminum wire. This was in Western NY State and I don’t understand how the rough-in wiring passes inspection unless the inspector was in on the deal. I was wiring houses in 77 and a local inspector would always inspect the rough-in wiring before the sheet rock went up. The wires were literally crimped together with the 4-way compression crimps we used for all permanent connections about 4″ outside all the electrical boxes except for the runs between the panel and the first box.
And if my memory is right, the whole debacle is what shot Giraldo Rivera to infamy. I mean it made him famous in the news industry. And drawing maps in the sand is what brought him down.
s/Giraldo Rivera/Horrendo Revolver
-Cheech and Chong’s Wedding Album
” Removing the aluminum branch circuit wiring completely and replacing it with copper is also an option, albeit an expensive and disruptive one.”
No worse than having to upgrade an entire house from inadequate and old wiring* to something that can handle modern needs.
*Insulation deteriorates even if the coppers fine.
I often come across old-style insulated wire (pre World War II). The insulation used back then – some organic material and cloth? – just crumbles away over time.
That stuffs the worst! We call it ragwire, it has metal coiled armor. Best thing is to replace it but if you cant be very careful. I usually put a plastic bushing where the wire exits the armor just in case, electric tape also is a must. Just looking at it causes a short circuit!
The old wire you mentioned is cloth covered rubber insulated wire and there’s nothing wrong with the wire as long as the insulation is still in good shape. Also cloth covered rubber insulated wire was used well past WW2. Modern THHN wire is nylon covered PVC insulated, and the PVC in modern wire will also break down over time. Armour cable is still used today depending on application. You will see it anywhere wiring has to be exposed because Romex house wire is supposed to be in-wall only, except for very short exposure line the final jump from your wall to water heater.
“as long as the insulation is still in good shape” being the key point though, as you mention. It rarely is even when kept in a climate controlled space. Curious if asbestos was ever used in residential wire insulation applications?
Must be it… the rubber is so dried out that with one hammer blow the insulation just disintegrates into powder. And i’m pretty sure it is pre-war. the houses this cable came out of were built in the 1920’s.
I also come across lead-covered cable from the same period. I understand that was used outside and underground.
@MK 2, how does a lead covered cable work? Lead itself is a conductor.
@Shannon The lead covered cable I sometimes find has two stranded copper cores, an insulation layer and a lead layer on top of that.
Shannon:
http://lmgtfy.com/?q=lead+covered+electrical+cable&num=20&newwindow=1&rlz=1C1CHFX_enUS611US611&tbm=isch&source=iu&ictx=1&fir=uwBoo4uTG6tCmM%253A%252Cq2-bTOMv5qU0qM%252C_&usg=__VDcwjZIpmSeUwTFDnXvc3NtPIjs%3D&sa=X&ved=0ahUKEwitn6z30fbaAhXN21MKHYwIBMwQ9QEIUTAI#imgrc=uwBoo4uTG6tCmM:
There was insulation between the copper conductor and the lead sheathing (the same idea as running wire inside metal conduit.)
Gutta-percha, probably, replaced by polyethylene in the 1930s.
Our house was built in the 50s. A previous owner rewired the house with romex, but never redid the doorbell. Needless to say, it never worked well. We wound up installing a Ring and punching through the wallboard in the dining room to feed it power from a plug-in transformer. It’s kind of ugly, but it works and there’s a cabinet in front of the mess. We asked an electrician how much it would cost to run a new pair through the attic from the actual transformer to the front door and laughed at the answer.
You mean that stuff with the “chocolate” insulation. It has about the structural properties of stale chocolate. Wonderful stuff. /s Almost as bad, the copper has become hardened over time, and brittle.
200+ year old farm house I grew up in had knob and tube in the attic. Exposed copper wire a few inches apart strung between what look like electric fence post insulators. Once or twice a year I had to go up there and get the fried, dead mouse carcass off the wire and replace the fuse again.
This is what happens when someone cuts corners and installs mice rated for only 10A.
My grandparents had knob and tube wiring in their house when I was a kid. Lights were run with ZIP cord stapled to the walls and the light switches rotated 1/4 turn to the right to turn the lights on / off / on / off. The entire house was protected with one fuse at the end of the attic where the cable entered the house. It was very safe unless you were an unfortunate field mouse who decided to step on the wrong two wires – then “poof, no mouse”.
There’s a knob or two buried somewhere in this house. Redid most of the electrical years later (mix of old and new).
I actually like knob and tube. The conductors are physically separated and run across insulators. There’s not much to go wrong with it. What is a bear, is integrating it with modern, unitary wiring.
I did a documentary film once about Bach and a few churches in former east Germany also had aluminium wiring, terminating in a meccano style all metal fusebox. Brrr…
Electrician here. I once worked for a company as a service electrician. Got a call that a person was complaining that the receptacles were glowing. I blew it off because I used to get all sorts of crazy calls( IE; old analog TV is spying on me). Sure enough, if you looked into the receptacles several were literally glowing red when there was a decent load like a space heater on the circuit. The lady said this was happening for years! It was Al wiring, high resistance connections due to oxides/creep.
It was happening for years! My gods, I see glowing wires and I’m turning things off immediately. The sockets and walls must have been charred to bits as well.
” Removing the aluminum branch circuit wiring completely and replacing it with copper is also an option, albeit an expensive and disruptive one.”
Do American houses not use PVC conduits for the wiring? If so, replacing branch wiring isn’t really all that difficult or disruptive.
Remove power from affected circuit
Verify wires are power free
attach wire pulling spring/cable to wires in junction box, pull pulling cable into conduit from the other end using the old cables.
Attach new wires to pulling cable
Pull new wires into conduit
Reconnect devices and power up.
I doubt a practiced electrician needs more than a day to do most of an average sized home.
Nope. Typically Romex stapled to the stud. Going to rip apart drywall to get that stuff out.
I would prefer smurf tube or better, metal conduit, but then your house would cost $20k more.
Rip out the drywall and then put it all back, including all of the time and labor intensive work needed, including spackling the drywall and painting it all again and even then it might not look quite right. It’s an absurdly stupid way of building things. You can’t even look at it, let alone change it or upgrade it.
Reminds me of that post from the other day where that person basically cut out dozens of drywall rectangles just to run some wire in his walls for his closet server thing. Makes you cringe at how long that is going to take to fix back up.
EMT (or thicker) would be great but then (it seems like) nobody would buy your house because it was “ugly”. Fortunately, conduit finds use in commercial and industrial applications where people actually care about maintenance and the structure not being designed to only last 20 or 30 years.
You can bury EMT in the walls. Some cities, like Chicago, require it. I like working with the stuff, particularly in retrofitting, but its lack of flexibility is limiting.
Now you know why quite a few do most everything through the attic, or second-best crawl space or basement. One plus in ripping out drywall is if one has to redo the insulation in the first place (foaming in isn’t as bad, but still…holes)
Non metallic sheathed cable has been used in residences in the US for decades in most locations. Code requires it to be stapled the stud near the device boxes. Generally conduit is found in residences in order cities where the trades have undue sway. I am labor and support labor, but not out of date, make work, code requirements. That’s simply screwing over your customers.
>PVC conduits for the wiring? If so, replacing branch wiring isn’t really all that difficult or disruptive.
Oh ho ho… PVC tubing’s been in the wall for 30 years, try to pull anything through – the tube crumbles to bits. Oh well, time to tear up the drywall.
I’ve replaced parts of the wiring in my house (built in the mid 80s) a few months back, no problem whatsoever with crumbling pipes. I’ve never even heard of that being a problem.
At the same time all this was going on, stainless steel was being used to replace copper water lines. Intergranular corrosion and pinhole leaks were the result.
Lots of lead lines being replaced now too. But as long as the water chemistry is properly maintained (*ahem* Flint), lead water lines are – like Aluminum electric wiring – not a problem.
Less “not a problem” and more “somebody already suffered through the worst.”
Well, then, “not a problem *any more*.” Again, as long as the water chemistry is properly maintained.
not a good addition to an existing mix of copper and aluminium.
you can always tell the after affects of mixing the two metals even when working with wattage, a small (solid-state) radio probably draws less then a half amp at 115v (quarter amp at 230v), but at 12v ??? shit turns black, green, and gooey quick!
the gooey-part is the insulation not being rated for exposure to a combination of: heat, copper-corrosion, and aluminum oxide. it is found when attempting to re-strip and re-twist “twisted” connections, not gonna work, uC will continue to crash/drop-out
The city I went to University in still has some oak water mains downtown. Laid in the 1800’s. They burst one every decade or so. Turns out they can get replacements. The only difference is today they have stainless steel bands (exterior) rather than lead.
The old bands were iron. Lead isn’t strong enough. It was used for the service line from the main to the house. When we did a sewer project south of Tacoma, we pulled out some disused 54 inch wood stave line. It was still in good condition. I believe there is still miles of the old 54 inch line, exposed on concrete cradles, serving water to Tacoma.
Aluminum or copper : Overloading a circuit is not good. Circuit breakers can’t stop stupid only hopefully slow it down and nothing is maintenance free.
I’ve seen a fair bit of modern cheap cable that is copper plated aluminium. The problem being that this looks like copper, it’s mostly in network cable for now but there is some stranded extra-flexible type cable around as well, which can’t be good can it? Even if you’re only connecting up power to your quadcopter.
Anyone noticed mains cables or IEC power leads on appliances, that feel too light? Are they aluminium?
The big problem with aluminum was the failure to see its use case in retrofits and when mixed with other more common electrical components. They failed to assume that people would use copper jumpers and wire nuts with the aluminum wiring and that they might add aluminum wiring to old copper systems. Why this happened is a mystery to me since any electrician with a power company would know what problems that can cause just from experience. This was a huge failure by the NFPA (electrical code).
All this was before my training we learn the then current code for AL branch circuits, and accepted remedial methods. Did the NFPA approve the practices that where used or was it failure on the part of the municipalities? Municipalities can choose adopt or not adopt the NEC, or ad modifications.
For high speed network connections that probably makes sense. The skin effect of the high frequencies are going to make the signal travel the surface of the cable. In high power settings this won’t work because the copper is so much more conductive than aluminum that the majority of the current flow will avoid the center of the cable and your effective cross section becomes the cross section of the copper. Aluminum is not a particularly good choice for a flexible power lead since it would have to be much larger for the same ampacity. Aluminum is only about 60% the conductivity of copper.
Beware the CCA! The Chinese are selling cheap “Copper-Clad-Aluminum” in the smaller gauges for low voltage use. It is absolute crap and corrodes out in no time. It is typically listed on Amazon, eBay, and other sites in the main description as “Copper” but then when you look at the fine print it says “CCA”. With copper prices spiking again, this crap sells often for less than half of it’s copper equivalent.
I made the huge mistake of using some for a 12V LED decorative lighting installation, outdoors, not far from the beach. Despite the fact that everything was soldered, and in enclosures not directly exposed to rain or salty air, it corroded out in under 4 months. I used some more on an indoor installation, away from the beach about the same time, and even it corroded out within 18 months. I ended up having to rewire both projects from scratch at great expense.
Even worse are CCA ethernet cables.
Guaranteed NOT to work properly.
https://www.cablinginstall.com/articles/2011/03/ccca-cda-warn-against-copper-clad-aluminum-cables.html
I’m not going to contradict the experts, but I am surprised that for high frequency applications cladded conductors wouldn’t work fairly well given the skin effect.
I guess it requires a minimal thickness of the cladding that may not be in the Chinese suppliers’ best interests.
The center conductor in CableTV wiring can sometimes be cladded aluminum
The center conductor in CableTV wiring can sometimes be cladded CRAP.
Did some electrical upgrading to receptacles in a townhouse as a contractor. THICK twisted aluminum single strands of heavy gauge AL that barely fit in the wall. No chance of bending it. Tied on copper with correct junctions and anti-c goop. One of the unfunnest things I ever had to do. In theory, replacing a receptacle in SoSF, Ca, requires a permit and inspection. They use all-trades inspectors here who know nothing, to include simple division or 1000/160. “Oh… just give me 4 roof vents.” He got none. I used ridge venting. Also saw my 1st lead pipe (after Clue,) in an SF victorian. A perfect P trap in perfect shape. Replaced it. And Roto Router here that I used said, “Need to cut the pioe. Can’t do it otherwise. Too hard.” I paid him 300 vs 150. Still couldn’t fix it. No money back. I HATE CRUMMY SUBS. Want everything lucrative and wham-bam.
I work for the cable company, we use all copper clad steel with aluminum trishield(foil-braid-foil) Satellite company uses pure copper conductor as they run power. We only need copper clad due to skin effect. I have yet to see aluminum center conductor, a lot of crap cable but no aluminum yet.
Go with higher main voltage (like 230v) and stop with this 4 times too thick conductors non sense.
Going to higher line voltage isn’t a remedy for the basic corrosion problems when using AL. Not to mention the in compatibility with all the appliances now in use or in the supply stream. Global climate change will cause hell to freeze over before the US adopts a higher voltage for lighting an small appliance circuits. Shut up before our current POTUS makes you pay for the changes. ;)
With LED lighting we really don’t need 15A lighting circuits anymore. We could go to 120v 5A over 18 gauge for lighting applications. One circuit could still light an entire house.
Even our electronics are getting much more efficient. A 65″ tv only draws something like 2A.
We only really need 15A or 20A plugs for heating appliances like space heaters, toaster, kettles, etc… Well and cooling as well like the fridge, freezer and air conditioner.
The change will never happen unless copper gets super expensive. Then I could see other solutions like smart power. Where the devices that plug in talk to an inverter supplying power at requested voltages up to 600v. So your 1000W toaster will request 600V and thus only draw 1.6A which could run over something like 20 gauge wire. Unplug the toaster and stick your finger in and there might only be like 30V. The voltage would only increase as long as the device was calling for it. Every circuit would have to be home run which might negate any cost savings from the smaller wire.
Shush! If people start doing that kind of math then the only place we will be able to run a power tool in a new house will be the kitchen! Is that what you want?!? That could be the death of hobbyist making. The only people building anything a couple of generations from now would be people at work.
We’ll never see 600V in residential. Insulation requirements and working clearances become too cumbersome to make it happen both safely and economically. Smart circuits such as you suggest would be prohibitively expensive for appliance circuits too. Each circuit would need to feed exactly one appliance. If not, the appliances would need to broker a common voltage, each circuit would then be limited by the voltage limitation of the appliance with the weakest voltage rating, and the ampacity of the wiring would need to set to handle the sum current of all appliances on the circuit at the lowest voltage, ie large gauge wire.
If each circuit has its own multi-kilowatt smart buck-boost AC converters, what have we really gained except for a load of additional cost? The ability to move your oven from one wall to another? Your dryer from the laundry room to the bedroom? Your compressor from the garage to the entertainment room? Yes, those examples are absurd, by design, to illustrate that most of the flexibility gained for that massive cost is useless to the homeowner. With a few exceptions, (e.g. hairdryer, electric kettle, microwave, toaster, turkey fryers, power tools) heavy power consumers’ outlet locations can be predicted exactly during construction or remodel, and the circuit designed exactly to safely provide power at the lowest cost. In addition to the exorbitant cost of high power smart AC converters, if we stipulate that those heavy consumers account for 85% of the electric bill and those smart converters are 97% efficient, we will raise the electric bill by 2.63% too. Not very green.
I can see some common sense improvements in our future. Low voltage smart circuits would be a safety win. A collection of 1-n LED bulbs could be able to communicate with a smart breaker upstream – if the breaker cannot account for every mA drawn through it then it could declare a fault condition, trigger a bulb self-test to isolate a faulty device, or trip if it determines that all the devices are good and the wiring is at fault. We could do the same for low voltage low power devices such as phone chargers, toys and other wall-warts.
I would like to see smart power-reporting *affordable* panel GFCI breakers. I can buy a 20A 120V GFCI outlet for about $15, yet a 20A 120V GFCI panel breaker is $40. The dual pole 240V version is about double that. A 50A 240V panel GFCI is pushing $100. Safety has to be affordable. I’d like to see a circuit by circuit power consumption so I can make informed power usage decisions.
Any UK sparkies care to contribute on aluminium wiring? I have done plenty of equipment moves on 3phase indistrial property’s in the uk and never came across aluminium wire. and never seen it in a domestic setting either. Is it a thing here?
Aluminum (US) vs aluminium.(UK/Aus). I still laugh.
Oh go solder something!
Home builders also used plastic pipe to connect from the outside public water supply to the house in the early 1990’s (see big blue) which failed and polybutylene pipe inside the house for distribution. That too failed with pipes breaking inside walls since it didn’t withstand possible water hammer.
Lesson: You pay whatever the market will bear, not a price based on the quality of your home. If the builder can make a choice that saves him money, it increases his profit margin. You do not get the price savings. Thus the need for strict building codes and inspections.
And PEX is making a real comeback, hopefully with more of the bugs worked out of it.
Like aluminum wiring, it was bad application engineering, not that the idea was not sound.
Black pipe from meter to house is still going strong, decades later. PEX survived the recent winter quite well.
I love my copper cold water pipe that can act as a ground connection. I have never had a copper pipe fail.. ever! And sweat soldering pipe… piece of cake!
I’ve know people that were afraid to try soldering copper pipe but the only people I have known that actually found it difficult when they did try are the ones that insist on cutting corners skipping things like the flux or brushing the oxidation off.
Aluminum wiring coupled with a FPE or Zinsco panel…..now that’s a recipe for disaster! Wiring catches on fire and the breaker doesn’t trip!
You forgot the old Bulldog Pushamatic panels. Zinsco is the worst though!
Reality is they all can fail, recently I just had a 277/480 20A Square D QO bolt in breaker fail to trip. Was doing some electrical demo on a commercial job, accidentally cut through a live 12/2 AC cable on a 277V lighting circuit (yes, it happens to the best of us), besides blowing up my pliers, I watched in amazement as the arc started melted the cable like some sort of slow fireworks fuse. Ran to the electrical closet about 200′ away, basically found the correct panel by listening to the “hum” and then isolated the breaker by running the back of my had to find a breaker that was warm/hot. I was surprised, Square D is reliable and well regarded in the electrical industry. The panel was installed in the mid 80’s, probably never had any preventive maintenance done since it was switched on.
Sometimes overcurrent protection is too sensitive. Years ago I basically did the same mistake as above(what can I say, crap happens over 25+yrs of being an electrician). It was also a 20A 277V lighting circuit, barely made a knick in my pliers and didn’t trip the 20A breaker instead it took out all 26 stories of an office building! Main switchgear ground fault was improperly set. Can’t believe they never encountered the problem before.
My parents house has aluminum wiring. I freaking hate it! The thicker wire, the compound goo you have to put on there. It. Sucks. When I replace recepticles and switches at their house I always wrap the outside in electrical tape (I actually do that at my house too) and I’m super careful to get a good tight wrap on the terminal screw. Not taking any changes there. But that house has been standing without incident for more than 40 years.
al branch circuits are aweful. i cringe every time i get a service call to replace a receptacle and pull out the old one and find al… blech….
backstabbing is aweful. good friends dont let friends backstab- however it keeps the service calls coming in.
done a couple whole house al retrofits. if the house is wired in flexible conduit its a couple day job. its its not done in flex its four or so deoending on access from above and below.
access is never a problem- good electricians carry sawsalls ;)
The screws don’t turn. What happens is the aluminum heats up, expands, and crushes against the screw, leaving a dent. When the wire cools, it contracts and leaves a gap. The gap allows oxygen to corrode the aluminum, increasing the resistance, which makes the wire hotter the next time the same load is put on it. This process repeats until there is a fire or the wire melts or there isn’t enough contact to conduct anymore. The common observation is the wire is loose and that turning the screw stops that motion, but that doesn’t mean the screw ever turned to cause the joint to be loose.
Personal experience – I had a vendor using aluminum in a similar application tell me the Locktite had failed and allowed the fastener to unscrew, yet the fastener would not easily turn. The aluminum part had simply deformed more than the pre-load from the screw could follow.
The amount of deformation required to come loose is around 0.005 inches. Someone more invested can come up with the expected springy preload that is applied, but I think the screws are fine thread, so about .030 inches per full turn. I don’t recall more than a quarter turn from making complete contact to fully tight.
You nailed the exact cause for the failure. It’s thermal expansion and contraction causing the aluminum wires to loosen over time. Copper expands and contracts too but not near as much as aluminum, plus the brass screws expand and contract with the wires.
A solution to the problem might be a simple washer under the screw to add a bit of lenght to it, since a longer screw has more spring to it.
It’s the same issue in places where sheet metal is joined with screws. Washers are generally avoided because they add more interfaces that can slip, but with thin materials the thermal expansion can easily cause the joint to become loose because the amount the screw springs along its axis is proportional to the free lenght of the screw.
I had an 1979 Oldmobile Cutlass Supreme which had its battery stolen by some scumbag. They used a wire cutter to cut the battery cables instead of unscrewing the terminals. I found this out when I got to my car in the morning, saw the door lock hanging outside the door by some linkage and the hood slightly ajar. Gotta say I was emotionally SHOCKED.
To my surprise, from looking at the exposed severed battery cable cross-section is that the strands of wire had a copper outside but the center of each strand was silver colored aluminum. First time I ever saw that. I expected All Copper.
I tried to use a propane blow torch to acid core solder a new cable to the remnant of the old, but the solder simply liquified and fell to the ground. I ended up getting a clamp to clamp the old wire to the new wire and wrapped it in duct tape. It worked for several years until I sold the car.
Two points missed (after so many comments!)
– When pulled and bent into place, aluminium is more likely to fatigue, causing a point of higher resistance and hence a hot spot
– For similar reasons, Telecom (incumbent Australian telco now called Telstra) used aluminium for telephone cabling in some places. That was ok, until ADSL which got totally messed up by the junctions between Al and Cu. People in parts of some towns, like Dubbo, couldn’t get DSL without a lot of recabling, which almost immediately became redundant with NBN fibre.
Even utility companies can, and do,screw the pooch when it comes to proper installation of aluminum wiring. After a major storm (lightning, torrential rain) our house started having weird electrical problems like LED ceiling lights frying when turned “on” and appliances dying. I turned off the main disconnect and all circuit breakers in our home’s load center, turned on the main, and tested the voltage on either 120V leg, which went from ~121V on both legs to 78V on one and 158V on the other as I turned on more breakers. Florida Power and Light installed the underground wiring from the pole to our electric meter and neglected to put any dielectric grease on the underground connections at the base of the pole, and after almost 40 years the neutral connection was just so much aluminum oxide powder surrounding a couple of remaining strands of partially-oxidized AL cable. At least we saved one of the two neighbors connected to the same pole – they had been having problems with flickering lights, and the connection block for the shared neutral for all three homes was too hot for the repair tech to handle (high resistance due to corrosion -> heat!!!)
Aluminum is a lot more malleable than copper, so the thinner gauge wiring is pulled or or crushed it will be more likely than copper to thin or bunch up. Any wire that changes it’s thickness beyond designed purposes will malfunction due to its changed resistance. Thinned wire will have decreases resistance and overheat; thickened wire will have increased resistance and short circuit.