When that fateful morning comes that your car no longer roars to life with a quick twist of the key, but rather groans its displeasure at the sad state of your ride’s electrical system, your course is clear: you need a new battery. Whether you do it yourself or – perish the thought – farm out the job to someone else, the end result is the same. You get a spanking new lead-acid battery, and the old one is whisked away to be ground up and turned into a new battery in a nearly perfect closed loop system.
Contrast this to what happens to the battery in your laptop when it finally gives up the ghost. Some of us will pop the pack open, find the likely one bad cell, and either fix the pack or repurpose the good cells. But most dead lithium-based battery packs are dropped in the regular trash, or placed in blue recycling bins with the best of intentions but generally end up in the landfill anyway.
Why the difference between lead and lithium batteries? What about these two seemingly similar technologies dictates why one battery can have 98% of its material recycled, while the other is cheaper to just toss? And what are the implications down the road, when battery packs from electric vehicles start to enter the waste stream in bulk?
Time + Chemistry = Economics
Understanding the disparity between lead-acid and lithium-ion battery recycling boils down to two major factors: time and chemistry. On the time side of the equation, consider that the big chunky battery under your hood is pretty old technology. Lead-acid batteries have been around for as long as cars have, and then some. As such, they have over a century’s head start on their lithium based cousins in terms of infrastructure. We’ve been using these things forever, and we’ve really dialed in their lifecycle management. From cradle to grave and back to cradle again, lead-acid batteries benefit from an extensive and highly integrated manufacturing and distribution system, one that the lithium-ion industry just has not yet had time to develop. The lead-acid infrastructure goes so far as to often use the exact same trucks that deliver batteries to retailers for the return trip to the recycler.
Time also plays into it via the rapid turnover of automotive batteries. The average car battery lasts about four years, give or take, and since the average lifetime of a car is now about eleven years, each car will likely see three or more batteries over its service life. For electric vehicles and hybrids, the battery pack is designed to last for pretty much the service life of the vehicle, so barring accidents that render the vehicle wrapped around them useless, lithium-ion packs are just not going to enter into the recycling stream nearly as often as lead-acid batteries do. This is somewhat negated by the number of lithium-ion battery packs from consumer products like laptops and power tools; those enter the waste stream far faster than lithium-ion batteries from electric and hybrid vehicles. But those numbers are a rounding error in the equation compared to the number of lead-acid batteries recycled every day.
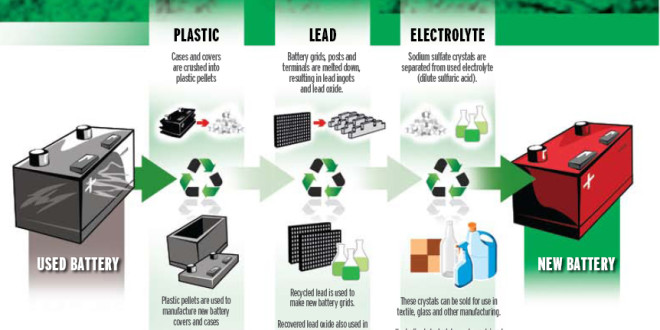
As for chemistry, the simpler the mix of materials in an object, the easier it is to recycle. Aluminum cans, which are just aluminum and paint, are incredibly easy to reclaim with the addition of a little heat. Lead-acid batteries are not quite that simple, but they’re close: just lead, lead oxide, and sulfuric acid in a plastic case. Each material in the battery has a simple path from old to new: the lead plates melt easily at low temperatures and can be easily purified, ditto for the PVC that typically makes up the battery’s case, and the sulfuric acid electrolyte can either be diluted and disposed of as wastewater, or the sulfates can be recovered to manufacture new electrolytes or used in the production of other consumer items, such as soaps.
Lithium batteries, on the other hand, have much more complicated chemistries and a mix of materials that don’t work and play well together in an industrial recycling process. A lithium-ion battery is not just lithium but also has cobalt, manganese, iron phosphate, or nickel compounds, not to mention aluminum, copper, and graphite. Not only is the mix of metals more complicated, but their physical form as powders coated onto metal foil makes recovery of each component far more complicated than just throwing it in a furnace.
The electrolyte in a lithium battery is much more complicated too, consisting of lithium salts in volatile organic solvents like ethylene carbonate. This makes the liberated electrolytes much more difficult to deal with as well; no simple dilution and neutralization with a basic solution like sodium bicarbonate will render these compounds safe enough to discharge to a sewer as is the case for lead-acid recycling. Dealing with that adds to the cost of recycling and cuts into the potential profit.
A Hands-Off Process
The mechanical process of recycling is also much easier for lead-acid batteries. In the most advanced recycling plants, used car batteries can literally be chucked into a shredder whole, which pulverizes the plastic cases, releases the electrolyte, and shreds the innards. Process water is added to dilute the sulfuric acid and flush away the plastic bits, which can be skimmed off while letting the lead parts sink. Everything has its own physical path through the process, and human hands need never touch the batteries, which makes for a very economical process that scales well. And even where the process is not entirely automated, the limited number of shapes and sizes of batteries, coupled with their relatively large size, makes orienting the batteries for quick disassembly easy.
Compare this to handling a lithium-ion battery pack. The form factor for these could range from a laptop battery to an old drill-driver battery pack to the guts of a wrecked electric vehicle. While most of these will be loaded with cells like the 18650, each one will differ in size and shape, and the number and orientation of cells within the pack will vary wildly. Most packs will also have some kind of circuit board inside, which requires a separate step to liberate and has to enter a different recycling stream. At least for now, this makes disassembly of lithium-ion packs the work of human hands, which makes it an expensive proposition that scales poorly.
The differences between the effort needed to recycle lead-acid and lithium-ion batteries drive the overall economics of the process. If you look at the price of lithium ($17,000 / ton) versus lead ($2,600 / ton), it would seem that lithium recycling would be more profitable. But if you can’t get the lithium out of batteries effectively, it doesn’t matter how much the stuff would earn. For recyclers, the value proposition is skewed heavily in favor of lead, where huge feedstock volumes and easy extraction methods make recycling a profitable venture. And that’s not to mention the dangers of mixing lithium batteries into the lead-acid recycling stream.
All this leads to the sad fact that currently, 97% of lithium-ion batteries are not recycled. With a huge new input of dead batteries about to hit the waste stream as the first generations of electric and hybrid vehicles reach the end of their service lives, this is going to be a problem we’re going to need to deal with soon. The fact that both lithium and cobalt are sourced from politically unstable regions of the world will probably help skew the economics of recycling such that it makes more sense to recover the minerals rather than commit them in an unusable state to the ground whence they came. Things will likely change, but for now, lithium-ion batteries are a dead end technology.
Interesting one mentions lead-acid, but how many put their UPS batteries in the same stream car batteries go into?
Everybody who scraps UPSes. The lead batteries in a UPS are the easiest and fastest money out of a pile of computer scrap, getting PCBs and wiring out is more effort and often less return.
But how does gel or AGM recycling compare to liquid acid?
I don’t think that makes much difference. The acid is washed out somehow for further treatment (neutralization or reclaim) and the rest (glass fibers or gelling agents) goes into the slag. But this is not much mass compared to the lead.
Part of the problem is not everybody has ‘blue’ recycling bins, some are green or back, or another color. Despite the obvious assumption that all recycling bins are the same color there is a more serious point, recycling facilities vary from town to town, state to state and by country. There is already a good infrastructure for recycling lead acid car batteries but clearly where you are in the world not so much for lithium batteries.
This is a great point. Taking this a step further, it’s astonishing the number of places that don’t even have the most basic system for recycling aluminum and plastic. I grew up in a small town and California and to this day the town has no recycling infrastructure. The prospect of electronics and battery recycling there is far-fetched.
why are you so astonished? for quite a while most of North America has been shipping its waste and recycling to the other side of the world. Its only now that China and India are starting to double think accepting all of our waste that we are concerned about recycling. Its funny because i am now starting to see more public ads about what is supposed to be in the blue box and what isnt. On top of that the waste company in my area wants paper separate from the glass/metal/plastic, so clearly we never had the infrastructure to do one box recycling.
The truth is that all the talk about saving the world and the 3 R’s was just fluff ment to shut up the enviromentalists for a bit so that the business men and other prophets of capitalism could make a few extra dollars. Take a look at the first two R’s and you will see how quickly they were droped. Reduce is first and well it is clear to see how reduction of consumption is bad for capitalism and selling you more stuff, reducing your consumption means a reduction in their profits. Reuse being second shows the same problem as when you are reusing things then you are not buying new things. Finally businesses co0opted that final one, recycle, they did this by making deals and instead of sending back empty containers back across the world they filled those containers with stuff that the other countries promised us they would recycle. That solution was great for business, the consumer felt good about recycling and the shipping containers went back to countries who would fill them with more cheap goods for the consumers!
The harsh reality is that there are only a few materials which are cheaper to source from recycling instead of extracting the raw materials and creating from new. Until this reality changes, recycling will always be a joke as businesses will continue to use the lower priced option. That is in essence what capitalism dictates after-all; bring to market the best product at the highest price point using the cheapest sources of materials. Capitalism does not care about the sustainability or the future, only the present and until we start electing representatives who understand this and are able to provide balance to the equation. Most politicians since the days of Reagan have been prophets and apostles to capitalism and its all mighty God; profit.
Dismally true!
Putting batteries in to a recycling bin is really not a good idea. Down here in NZ there have been more than a few trucks catch fire as a result of old batteries shorting out. The environmental problems this causes is huge let alone the need to shut down roads while the fire and aftermath is resolved.
We are lucky however that we do have a a lot of recycling centers, some will pay you for your refuse others are council operated and you can just drop off your unwanted stuff.
Something that surprises me is that schools have not jumped on the band wagon, When i was a kid we used to do paper drives to raise money for various sports events. I guess however now days there seems to be no shortage of commercial sponsors willing to put up a chunk of change just for bragging rights.
Near SF, CA, we have 3 bins, 4 as 1 is divided. Cans & plastic go into one, together. BUT batteries go into a baggie on top of the bins. I set a baggie out maybe 2x a year.
I was under the impression that the lithium car batteries could be recharged 1500 times. So if you use the car every day for five years, the battery would be slightly more than totally dead. Personally, I would expect to get a lot more than five years out of my electric car, more like 25 years with a bit of TLC. If my maths is correct, that means disposing of five dead batteries?
I have a 2013 Chevy Volt and drive/charge the battery virtually every day (I’ve had a few cross-country trips where charging wasn’t available and a few international trips where I didn’t drive my car at all for about two weeks). I bought the car brand new and have over 53k miles on it. There are people with 2011 models that have 100k+ without battery degradation. One driver has over 400k on his, still charges it daily (has a long commute) and has experienced almost no battery degradation.
I have had zero battery degradation and still get full mileage on a charge. I’ve had no service on the battery system and my overall maintenance on the car has been almost nothing (two scheduled oil changes at about 24k miles each). In fact, my first real maintenance is coming up to flush the battery coolant system.
The FUD on lithium ion battery systems has been thick and heavy for a while now. One thing to note; the Volt battery systems and those of most major PHEVs and BEVs are liquid-cooled. The Leaf, however, is not, and that’s why those have had more battery issues on the first generation models.
One thing also not said much here is that recycling of lithium ion batteries from EVs is VERY common and typically used for other systems, such as home/grid battery systems and homebrew EVs and such. Individual cells are matched and packed together so that the rate of individual cell discard is fairly low. Now, can *that* aspect be improved. Of course. But it’s certainly not an entire EV battery pack gets tossed out when it only can hold 80% charge, and most definitely not a battery replacement every five years or whatever.
The Volt has a 16 kWh battery with 9 kWh useable capacity. They hide the damage until it really breaks, because the last few cycles on the battery are going to go fast.
10.4kWh on my particular one, as noted in a below comment. And as far as the scenario laid out, that remains to be seen as virtually no one has experienced any appreciable range loss on the battery in a Volt yet, aside from a very small number that have been found to have defectively assembled batteries. Getting over a 30% functional loss of cell capacity over the entire pack so that the system is only running on the 9-10kWh usable left simply hasn’t happened. A number of people have predicted it, but most of those same people also predicted that we’d be replacing battery packs at the 3-5 year mark. Another thing that simply doesn’t happen.
Most often the mode of failure on a Chevy Volt battery pack has been a coolant temperature sensor within the pack, at which point the HV system throws an error and will not run; some have been on that pack section alone, some have been altogether.
I have a 2012 Volt myself, and though it doesn’t have a ton of miles on it, it’s pretty much all battery for ~ 30k and I’m still getting full range – I’ve broken 50mi on a charge (rated at 35 and it’s easy to get below that if you drive like Ken Block). I’m showing ~ 245 mpg for the last few years, but since I burned gas for the first half year or so to break in the engine and get an oil change from the factory breakin lube, lifetime is about 160mpg. It’s never been charged via the grid, solar only (and that break-in period allowed me time to upgrade my solar system to handle it). I don’t have to commute…
I think there’s likely some truth to what Luke says (though the numbers are different in different models). This was a Bob Lutz “car guy” project and on top of that was a “bet the company” car for GM. At least the early Volts look like some of the most carefully designed and built cars I’ve ever witnessed. I think they baby the crap out of the battery too (they do say so) because at design time, this was all very new and so much was at stake.
My solar system is lead acid. You know what? If you have LA batteries that will go 1500 full cycles, they’ll go 15,000 cycles at 10% cycling. I’d bet lithium, especially the GM ones with per-cell management of temperature and charge, are going to look about like that.
I only have since 1980 working with flooded lead acid…a little experience. if you treat them right (almost a religion) they last quite well. It’d be no surprise for other chemistries to do the same.
The solar system batteries have the same life issues. You oversize them and they are essentially perfect for a long time, then when they get below the real needed spec, things go downhill real fast.
If your batteries last 10x longer with only 10% cycling, that means you’re only using 10% of the capacity. If you took away 90% of them, and just used a tenth of the batteries at 100% (I know real batteries don’t like 100%, but more or less), then they’d last 10x less. But you’d have 10x as many of them. So you could just throw the dead ones away.
You’d be in exactly the same position! You’re not gaining anything by using 10x as many batteries to get 10x the lifetime.
Apparently since 2010, solar panels have broke even on energy, producing more lifetime energy than it takes to make them, so you’re doing well there.
@Greenaum: You are of course quite right. But it is not always linear. I have a LiFePo4 battery (12V/100Ah) and it specifies 1000cycles @100% or 2000cycles@90% or 3000cycles @80% depth of discharge. So it makes sense to not use the complete available capacity in every regular cycle.
“One thing also not said much here is that recycling of lithium ion batteries from EVs is VERY common and typically used for other systems, such as home/grid battery systems and homebrew EVs and such. ”
“Very common”? Or is that just among the MacGyver set?
More common on the industrial level than the individual level, but the Chevy Volt battery packs that do come available are being reused quite often in homebrew EVs and battery backup systems as the battery modules themselves seem to have been very well engineered.
https://www.engadget.com/2012/11/15/gm-and-abb-repurpose-used-chevy-volt-batteries-to-provide-home-b/
Evidently the Volt packs have a good chemistry design and are setup for a conservatively rated 7.8C, but aftermarket people are testing as high as a 15C discharge capability, and getting wrecked vehicle packs for $1500 to $2000 for 16kWh.
https://endless-sphere.com/forums/viewtopic.php?t=62445
http://www.diyelectriccar.com/forums/showthread.php/power-capability-chevy-volt-battery-109698.html
Thanks for the links.
Nissan Leaf modules still go for $100 each. Like pretty much everything used (and a lot of new stuff as well), supply and demand set the price.
Don’t forget that an expended charge cycle can be broken up into fractions. Driving ten miles round trip and topping back up uses a fraction of the expected full charge to empty mileage.
The battery doesn’t do 1500 cycles and just stop working completely (unless there’s some planned obsolense BS installed in the pack itself)…
Usually after the battery did it’s stated number of cycles, it now has 80% capacity (testing methodology varies between manufacturers, so it needs to be examined before comparing), so your car will just have less range. If you can deal with that, no need to change anything.
Electric cars reduce the stress on the battery by shutting down the car before the battery reaches true zero charge and limiting charging to less than true 100%, giving far more than 1500 cycles before they seriously degrade. Phones and laptops push batteries much closer to the absolute limits and it hurts cycle life.
My Nissan LEAF has been charged pretty much every day, often more than once, for 3.5 years and has over 90% of the original battery capacity left. Tesla, and others, pay more attention to controlling the temperature of the battery as well as state of charge and do much better.
Yup. Default Tesla methodology is, if I recall correctly, to only charge to 80% SoC, only going to 100% if the user explicitly overrides the default – on a per-charge basis I think?
That’s because spending time at the top of the SoC regime is extremely stressful on a lithium ion battery. (Vastly different from lead-acid – which prefers being constantly topped off.)
Even if the user selects 100%, it’s likely that Tesla leaves some headroom that a cell phone would take advantage of.
So it can be an option to “overfill” it directly before the beginning of a long holiday trip. The time it stays at 100% is greatly reduced when you start the long distance drive directly after the cahrging.
Our Android tablets (at work) shut down (State 0% Charge remaining) around 7.5 Volts and around 8.4 Volts is
“Full Charge”.
I assume that’s for two cells. When I worked for a cell phone maker 10 years ago, we would charge to 4.2 and shut down at 3.2 on a single cell. It sounds like your tablets go a bit easier on the battery.
That’s a very conservative approach. 8,4V implies a two cell pack. So it has a per-cell cut off voltage of 3,75V. That’s HIGHER than the nominal cell voltage of 3,7V. A typical cut-off voltage would 2,7V to 3V/cell
Perhaps think of it in terms of mileage. If your electric car will do 250 miles on a charge and can be charged 1,500 times before the battery dies that’s 375,000 miles. I’ve heard it said that cars need expensive repairs beyond about 100,000 miles so needing the most expensive part of your electric car changed at nearly 4x that distance isn’t bad at all.
Then consider that it’s not 1,500 charges till death, at that point you’ve only dropped below 80% of your original capacity so if you need at minimum 50 miles of range per charge that original battery is still good to use for a few thousand cycles more.
>” I’ve heard it said that cars need expensive repairs beyond about 100,000 miles ”
Only if you mistreat them. At that mileage you probably need some belts changed and brake pads replaced, but that’ll be few hundred at best.
A regular car goes for 20 years and 300k miles if you keep it reasonably well. An electric car cannot go more than 10 years, because the shelf life of a lithium battery is about that long.
A vehicle _can_ go for 20 years and 300k miles in very ideal circumstances, but that is nowhere near the average. The average car lasts about 8 years and 150,000 miles. To get a car to 300k miles would, indeed, require some quite expensive care, even if you don’t mistreat them. Also, at 100,000 miles most cars would have had their brakes changed at least twice, if not more. Frankly, none of what you said is very accurate at all, even if the owner is a mechanic and does some of the work themselves.
Also, to that I would add that all major EV systems these days also do wear leveling on the individual cells. My Volt has a 16.5kWh battery, but only uses 10.4kWh for propulsion and ancillaries. It cycles through all of the cells and uses individual cells more thoroughly rather than using all of the cells and only a small percentage each. The battery management systems in modern EVs are incredibly complex and incredibly efficient. The Tesla ones are even more so, as they have a VERY high cell count comparatively.
I think you’re mixing up charge balancing with wear leveling.
My terminology may be off, let me explain what I was trying to convey.
There is charge balancing that goes into the charging cycle; the charge controller monitors the state of the individual cells in each of the three pack sections and has the capability to control the current going into the cells during charging and to progressively reduce charge current upon hitting the target voltage. It also has the ability to dissipate stored energy within a cell if needed to assist in balancing that cell to others within the cell group.
What I was referring to is that the BMS monitors the state of the individual cells within a cell group and can switch between different cells so that cells of a monitored similar discharge profile are used at the same time, so that cells that are more worn or have a lower output profile are used in conjunction with cells that have a similar but inverse level of use, so that the overall output remains similar. It also has the capability to cycle cells in and out of use, so that the more worn cells are used less frequently than the less worn cells. It’s an incredibly complex monitor and control system, and a good part of the almost mythical “10 million lines of code” to run the Volt is dedicated to the HV and battery maintenance systems. Perhaps the “wear leveling” term was wrong!
https://www.edn.com/Pdf/ViewPdf?contentItemId=4391497
Here’s a good breakdown of the charging and HV subsystems of the Volt.
1500 full cycles. you do not drive 500km and empty your battery every day you use the car, do you?
In my case I do not even use the car every day. If I use it then it’s on most days typically for about 30km. Of course sometimes more and when I am on holiday much more, like last year 300km/day average for one week. But I have only 5 weeks of holiday/year.
The time I worked on the other side of the city this was about 200km/week extra.
So of course it depends on your daily driving and battery capacity. If you have only a car with a tiny 20kWh battery you wear it much more and can not really go on holiday with this car – but probably you have it only as a second car to a conventional gas powered one.
Good luck on getting a hypothetical 500km in -20 C temperature. Youre lucky if you get even half of that. I drive 120 km per day, in -20 i would not make it 2 days without a charge. On average 2 months per year is that cold * working 5 days a week =30 full charges + change for 2 coldest months in the year. Add 2 more months with temperature averaging around -5 which will already nibble away on the 500 km range, lets say 15 charges. Liberally, rest of the year 5 charges per month * 8 = 40. Total yearly charge amount 30 + 15 + 40 = 85 full charges annually. With this logic the battery would last 10 years easily. Yet they do not. There are many factors playing in on Lithium technology not the least being limited shelf life.
Lithium batteries are mostly aluminum. Why would shredding them and processing out the plastic, pc boards, and lithium be so much harder. All metals melt, vocs boil at varying temperatures. It seems like at some point someone will get a processing plant going that can deal with this.
One thing that comes to mind is the hype to move to graphene. Will that stuff be able to be processed after use?
Will lithium burn under water?
I just don’t see lithium batteries under going any kind of shredding without releasing a lot of heat and smoke.
Water or oxygen and lithium are bad.
Use an airlock system. And do the processing in an nitrogen atmosphere. Shred them, then use a ball mill and spin the dust off the end of a conveyor belt and use momentum and gravity to separate of the powders by mass. Lighter material will not travel as far as heavier material, as long as the particle sizes are the same. You could maybe even use a strong static magnetic field (primary) to induce a repulsive force on the particles (secondary), if the particles are electrically conductive, to increase the travel distance (or decrease the travel distance by placing over the the end of a conveyor belt, instead of under).
Maybe some other floatation agent ought to be used there instead of water. Perhaps WD40? In pure Nitrogen atmosphere, of course …
I know: Export Lithium battery recycling industry to Titan! Liquid hydrocarbons galore and no Oxygen!
Lithium batteries don’t contain native lithium, they contain lithium salts. The bit that burns spectacularly is the electrolyte. A well managed recycling system could easily perform disposal in a nitrogen or CO2 atmosphere, so ignition would be impossible. It boils down to (pun intended) finding a scaleable processing methodology. Crack that engineering problem and you hit pay dirt.
but dont the lithium salts turn to lithium “spikes” when subjected to repeated discharges to ZERO-VOLTS and thusly the spikes puncture the thin seperator, the next time it is (charged first) discharged, the heat causes thermal expainsion and those spikes can go through the holes in the seperator and hit opposite electrode causing short, heat, and fire.
No. It’s copper that gets electroplated through the separators under this conditions. That danger is the reason for a very low current conditioning charge of deep-discharged LiIon cells.
If they have already suffered separator-problems, you will not be able to get any voltage on them, the low charging power is safely dissipated. If they are OK, the voltage starts to rise and you can give power. If you would start charging a damaged battery with high current, you would accumulate big amounts of energy and the resistive shorts in the separator start to heat up, yield to thermal runaway and the stored energy gets released -> heat and fire.
There is no metallic Li in a lithium ion battery.
One other problem is purity.
For Lead Batteries, Lead is almost pure (maybe some trace of other metals, but almost nothing. And the only use of Lead I’m aware of don’t need 99.99+% purity).
Lithium batteries now have a mix. And even if you claim to separate and give a 99.99% purity to your recycled material, your buyers WILL be suspicious.
Prepare yourself for some serious purity measurement to sell your gathered materials.
You are unaware of the lead-calcium alloy long used for the plate grids in “maintenance proof” batteries, or the lead-antimony alloy used in flooded lead-acid stationary batteries? The only “pure” lead I’ve seen is in the form of lead compounds (oxide or sulfate) in the battery.
Battery pack life versus charge cycles depends on a lot of factors. One is depth of discharge. Packs can last quite a long time if not fully discharged each cycle. Here’s some data indicating battery pack life vs cycle count (where they consider 70% original capacity as a ‘worn out’ pack):
Discharge Depth Cycle life
100% DoD ~300 / 600
80% DoD ~400 / 900
60% DoD ~600 / 1,500
40% DoD ~1,000 / 3,000
20% DoD ~2,000 / 9,000
10% DoD ~6,000 / 15,000
I´ve never heard any EV roaring at the twist of a key…that must be a side-effect of the lower limit of words for a valid article!
Mine plays a happy tune!
The BIG diff is that lead is horribly toxic to humans and lithium is not. Lead is 80-90% of car batt by weight. Many LiPO batts are in the 1-2% Li range, which is very difficult to recycle at reasonable cost. Toxicity is what determines the current recycle mix, not costs. Current need is lead free solder that is not Hell to use!
I don’t know if I would call it totally safe.
Most Lithium salts are used as psychiatric medication, which if given to a person without a psychiatric condition would not be good. https://en.wikipedia.org/wiki/Lithium_(medication)#Adverse_effects
But as long as it is safely sealed inside a battery, it is safe enough. There is no chance of the Lithium hydroxide converting the fats in your flesh into soap.
Lead free solder is (only) not horrible to use in an industrial setup (nitrogen flooded reflow oven). Otherwise it is just to be avoided.
Recycling lead acid batteries is fairly simple.
Recycling Lithium-ion ones on the other hand.
First off, they contain nearly no Lithium (only a few percent at most), so the value of the Lithium is not really of interest.
They though contain a fair bit of copper and aluminium, but both of these are in very thin foils.
Then there is all the powders and electrolytes…
In the end, I would likely recycle them by putting them through a blender of sorts. (Yes, fire and other nasty “surprises” might be expected from still partly charged batteries.)
This will make the batteries into very small pieces. But since the battery is made mostly of plated foils, then we don’t really need to aim for dust, since just forcing the foil pieces to slide free from each other will be good enough to get a much larger workable surface area.
Then add a fair bit of water to our now somewhat fine mix and use chemical reactions to extract each material at a time. Likely going to be fairly slow, and somewhat expensive. Though, one could use electroplating methods to extract a fair bit of the metals, while most of the electrolytes will likely either boil off as a gas or cloud up the liquid when forces out of solution and either float to the top or fall to the bottom, for further processing.
I would be surprised if it didn’t work, but the question is how economical such a process would be in the end. (And even if it turns out to be marginally more expensive then the materials one gets out of it, it can still be a viable source for conflict free raw materials that honestly could fetch the higher price for this sole reason.)
Freeze, and break apart.
LIthium battery recyclers cool the cells with liquid nitrogen before chucking them in the shredder, to prevent explosions and keep it in an inert atmosphere.
Looks like an area of opportunity to find more cost effective lifecycle management and recycling solutions and create a new market or at least expand on existing market operations. In general recycling seems to be another automation area of opportunity for better resource management, processing and utilization.
The article really kind of misses the main reasons that lead acid automotive batteries get recycled as such a high rate compared to consumer electronic.
1. Most are installed by shops that do a lot of batteries. They might as well recycle them because any other disposal method would actually cost them money and would be illegal in most places.
2. The core charge. In many states including my State of Illinois actually has car battery retailers charge you more if you don’t turn in an old battery when you buy a new one. Most people don’t mind this because who wants an old battery hanging around anyway. Most people are not buying a lead acid battery until they are replacing one. Most people that buy electronic devices are not immediately getting rid of the old one. How many laptops are laying around unused but not thrown away?
3, A lot of devices now (yes Apple I’m looking at you) no longer give the end user direct access to the battery making it very difficult for them to separate the battery from the more benign electronics unless they want to get rid of the device through a recycler.
“The core charge” certainly explains behavior on the consumer “supply” side.
$15 / battery (or whatever…) is a very strong incentive. Imagine that you had that much wrapped up in your laptop battery, and that they traded them in exactly where you’d go to buy a new one anyway.
And that they were too heavy to ship in the mail…
(All of the other factors that Dan outlined that make it economically viable on the demand side.)
Of course, one reason the core charge exists is because there is money to be made in recycling the dead battery. If you do somehow end up with a pile of dead lead acid batteries lying around, scrap metal dealers will buy them for cash. If they find a way to get money out of the batteries, programs to buy back dead batteries will follow.
Significant cash if you have very many. I made about $400 scrapping the old batteries out of a lead acid electric conversion.
There is another huge factual fault in the article. It compares the economics based on price per ton of lithium vs price per ton of lead. The problem with the math here is that the lions share of a lead acid battery’s mass is the lead. Depending on the battery, the lithium content of a lithium ion battery is usually less than 20% of battery weight. A lot of a lithium The truth is that in all lithium battery technologies, lithium is barely present in any kind of mass. Probably the most significant material in terms of cost and fragile supply chain is the the cobalt which is way more expensive, way less available, and is far more present in batteries than lithium.
Actually less than 20% which is the amount of lithium carbonate. The real amount of lithium is less than 2% of battery mass. Nickle and Cobalt are far and away the primary ingredients.
When i read the numbers being expressed in weight instead of volume:
“If you look at the price of lithium ($17,000 / ton) versus lead ($2,600 / ton)”
I would also expect a mention about the volume, with a density of 11.34 Lead is much heavier in the same volume as Lithium with a density of 0.534. So volume wise prises are more like $29,484 for lead vs $9,180 for the same volume of Lithium.
This is totally wrong. I don’t blame the author because this is the general view shared in media. However, lithium-ion batteries are widely recycled. However not in North America where only about 1-2000 tonnes currently are recycled. Instead they are shipped to China and South Korea where the recycling processes are very efficient. Especially cobalt is recycled but increasingly also lithium. And lithium is not worth $17,000/tonne, that’s the price for lithium carbonate which only contain 20% lithium. So the actual price of lithium is 5 times as much. Here’s som stats: https://recyclinginternational.com/batteries/second-life-how-recyclers-can-capitalise-on-the-true-value-of-batteries/
It is hard to compare the recycling processes because lead acid batteries are about the easiest to recycle thing there is. You have a liquid or gel electrolyte that can be drained or rinsed out after breaking up the batteries. Then you have left plastics (really lightweight) and lead (really heavyweight). They are trivial to separate and then the lead melts down at very low temperatures (low energy=cheap process).
What kind of shitty lead acid batterys do you guys have?
My 03 diesel Pickup is on it’s original set of 2x90Ah and it is used everyday in temperatures from -30 to +30.
I actually can’t remember changing a car battery ever, and I have had a lot of old shitty cars
Wtf?! Eleven years?
My car is twelve years old and I think it’s still fairly new.
Gotta say, as all “old” carpenters were also electricians, with mechanics being an old technology, I assummed that half of us were home mechanics. I just got a new 2001 F150 w 240,000 mimes. Design of eng & trans shows little wear when one is disassembled. It’s needing an axle and 1 pin on a connector is famous for needing solder reflow so the odo works. I live near a metropolis, not in the sticks. Hate that I can’t buy RedDevil because some junkie figured out how to use it to make meth – so now I can’t make a soap… superior to that which I can buy. I can use lithium salts? Recycling is a necessity. If we boost garbage to space, we lose gravity. We are in a nearly closed loop, admit it, we must.
I would love to see if anyone has any DIY repurposing information, like how to take dead Lead-Acid batteries and get the chemical components (same with Li-Ion and even Ni-Cad and other battery types) or how to fix dead cells on them. I am a chemistry major so its right up my alley.
97% of all lithium-ion batteries? That’s way too much.
Battery pack life versus charge cycles depends on a lot of factors. One is depth of discharge.