While the jury is still out on 3D printing for the consumer market, there’s little question that it’s becoming a major part of next generation manufacturing. While we often think of 3D printing as a way to create highly customized one-off objects, that’s a conclusion largely based on how we as individuals use the technology. When you’re building something as complex as a rocket engine, the true advantage of 3D printing is the ability to not only rapidly iterate your design, but to produce objects with internal geometries that would be difficult if not impossible to create with traditional tooling.
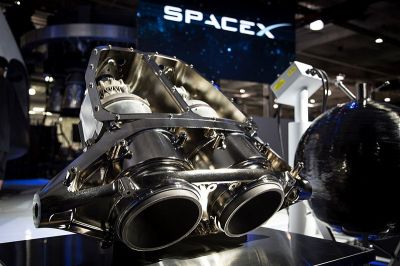
So it’s no wonder that key “New Space” players like SpaceX and Blue Origin make use of 3D printed components in their vehicles. Even NASA has been dipping their proverbial toe in the additive manufacturing waters, testing printed parts for the Space Launch System’s RS-25 engine. It would be safe to say that from this point forward, most of our exploits off of the planet’s surface will involve additive manufacturing in some capacity.
But one of the latest players to enter the commercial spaceflight industry, Relativity Space, thinks we can take the concept even farther. Not content to just 3D print rocket components, founders Tim Ellis and Jordan Noone believe the entire rocket can be printed. Minus electrical components and a few parts which operate in extremely high stress environments such as inside the pump turbines, Relativity Space claims up to 95% of their rocket could eventually be produced with additive manufacturing.
If you think 3D printing a rocket sounds implausible, you aren’t alone. It’s a bold claim, so far the aerospace industry has only managed to print relatively small rocket engines; so printing an entire vehicle would be an exceptionally large leap in capability. But with talent pulled from major aerospace players, a recently inked deal for a 20 year lease on a test site at NASA’s Stennis Space Center, and access to the world’s largest metal 3D printer, they’re certainly going all in on the idea. Let’s take a look at what they’ve got planned.
The Promise of Additive Manufacturing
Relativity Space isn’t the first company to realize 3D printing in metal could be a revolution for rocket engine design. During the reveal of the Dragon V2 in 2014, SpaceX CEO Elon Musk commented that certain weight-saving elements of the vehicle’s SuperDraco engines, such as the chamber’s internal cooling channels, were made possible by the ability to print with superalloys such as Inconel.
“It’s a very complex engine, and it was very difficult to form all the cooling channels, the injector head, and the throttling mechanism. Being able to print very high strength advanced alloys, I think, was crucial to being able to create the SuperDraco engine as it is.”
If expanding the concept to the entire rocket proves viable, the advantages could be immense. Relativity Space believes they could eventually go from raw materials to a completed rocket in as little as 60 days, compared to the months or even years it takes other manufacturers to assemble their vehicles. This rapid production cadence, along with the capability to augment the rocket’s design on a case by case basis, promises to offer a uniquely bespoke experience for customers.
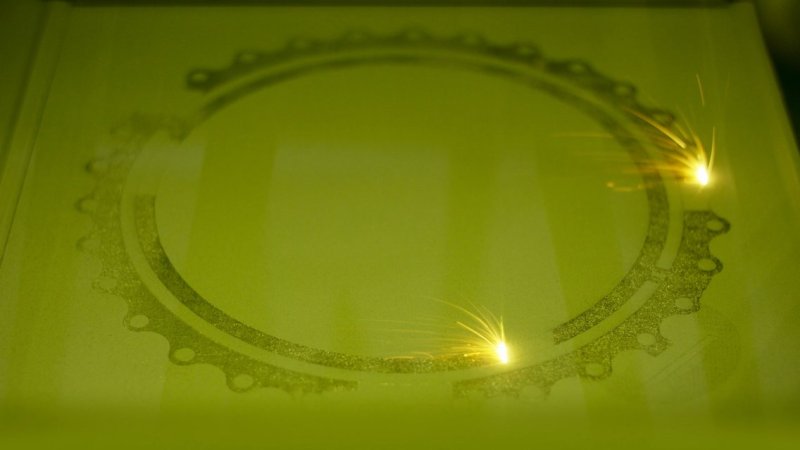
Not only would printing the rockets be faster than assembling them via traditional means, it would also be simpler. Parts designed for additive manufacturing don’t necessarily need to adhere to the traditional design paradigms. Rocket components which previously would have needed to be designed as several parts to be welded together by human workers could conceivably be redesigned for printing as a single unit. This allows for a sharp reduction in not only the number of individual components required, but the human effort in assembling them.
This plays into the company’s long term goals of actually assembling rockets on Mars. They believe that this rapid and largely automated method of building rockets lends itself to off-world colonies, and envisions a future where return rockets from the Red Planet are actually manufactured there, allowing for smaller and more simplistic “one-way” vehicles to be sent from Earth.
Present and Future
You can’t print something as big as rocket without a massive printer, so one of Relativity Space’s first milestones was the completion of what they call Stargate: the world’s largest metal 3D printer. Taking up an entire room, it doesn’t look anything like the 3D printers most of us are familiar with. Made up of three Kuka robotic arms (the type generally used to assemble automobiles) carrying lasers, cameras, and sensors, Relativity claims Stargate is able to print faster and smarter than anything else on the market. Using machine learning, Stargate is able to visually identify and correct for printing defects and modify future runs; so the longer it prints, the better it gets at it.
Stargate hasn’t managed to print a rocket yet, but it has printed the principle parts for the company’s Aeon engine which develops 15,500 pounds of thrust at sea level. While small compared to something like the Falcon 9’s Merlin, it has roughly three times the thrust of the Rocket Lab Rutherford engine which is also 3D printed. Requiring less than 100 total parts to assemble, and printable in under 20 days, the Aeon engine has performed over 100 test fires so far at Stennis Space Center.
They’ve also printed a massive fuselage structure, which on the final rocket would make up the lower half of the second stage. This proposed rocket, named Terran, would use a single Aeon engine on the second stage and a cluster of nine on the first stage; an increasingly common arrangement on New Space rockets.
Terran would also make use of autogenous pressurization for its oxygen and methane propellants, which eliminates the need for a complicated dedicated system to pressurize the tanks with another gas (usually helium or nitrogen). Between systemic simplifications and the fact that the fuselage and propellant tanks would be printed on Stargate, Relativity Space estimates the total number of components in the Terran rocket could be reduced to 1/100th that of contemporary vehicles.
Straining Belief, if not Technology
Ultimately, Relativity Space isn’t proposing anything that hasn’t been done before, at least in some form or another. SpaceX and Blue Origin are currently building and firing engines built with additive manufacturing as part of their next generation vehicles, and Rocket Lab has already put a payload into orbit with their 3D printed engines. Lockheed Martin has already shown that 3D printed propellant tanks can meet or exceed NASA’s performance and reliability requirements for spacecraft components.
The core principles of 3D printing rockets are therefore largely old news, in the grand scheme of things. Relativity Space simply wants to do it bigger. To take the small steps made by other manufacturers, and combine them into a giant leap. Can they do it? Probably. There doesn’t seem to be any technical barrier in the way, at least. But will it really create rockets cheaper and faster? That seems less clear.
Printing the engines, and even propellant tanks, certainly has merit; these are components that require high manufacturing tolerances and expensive tooling. But elements such as the fuselage and fairings seem to be poor candidates for additive manufacturing, especially compared to existing carbon fiber manufacturing techniques. With only two years to go before Relativity Space hopes to launch their first Terran rocket, we might not have to wait long to see how many 3D printed components make it into the final vehicle, and how much of their initial plan ended up being little more than buzzwords to entice investors.
I think that by printing complex pieces as a single unit will improve reliability by eliminating the number of seams, seals, and fasteners needed with conventional manufacturing. Printing engines and nozzles with integrated duct work seems to be a win.
It still depends a lot on the final shape you want to create. I can see where 3D printing is an attractive concept to replace all the complicated duct work in an engine.
On the other hand, 3D printing a large fuel tank or pressure vessel, doesn’t make much sense. I don’t believe you can beat the weight/strength ratio of carbon fiber wrapping.
What about a printed super thin wall, providing the sealed structure with a carbon fiber sock wrapped around it to provide strength? kind of like the way flexible plumbing pipes are made. The inner rubber provides the waterproofing while the outer stainless mesh holds the pressure. I am sure carbon fiber (and the resins) provides some interesting challenges at -187 degrees Celsius.
SpaceX thinks they can solve those challenges without a liner.
https://www.businessinsider.nl/spacex-carbon-fiber-fuel-tank-ocean-ship-test-2016-11/?international=true&r=US
speaking of flexible piping, since those engines are going to get hot, its going to need to flex when things expand, so printing the whole works out, there’s going to be no flex joints, like V-band connectors.
I’m also skeptical about the economics of printing tanks, but there are certainly some useful things you can do that would be expensive with conventional manufacturing. Isogrid walls, for example, help significantly with weight but are usually terribly expensive. When you’re printing the tank, using an isogrid instead of a flat panel is a zero-cost change (maybe even negative, since it needs less material and that means faster printing). I haven’t heard if they’re doing that or not, but I’d be a bit surprised if they aren’t.
The bottom of the pictured tank, with the load-bearing flange smoothly blended in to the tank skin, would normally have a separate thrust-bearing cone or ring bolted or welded to the tank, with reinforcements needed around the attachment area to spread load. There’s a good bit of complexity and labor avoided right there.
The pictured tank is quite small, though (for a rocket). As you go larger, you need more pressure inside to keep the tank from buckling, and forces in the wall go up with radius * pressure. For a fixed tensile strength you need to increase thickness with force, but that increases mass, which then requires a bigger tank to carry more fuel. Moving to a higher tensile strength material and/or manufacturing technique with tighter tolerances becomes more attractive as you move up in scale.
LFC is still a thing.
https://en.wikipedia.org/wiki/Lost-foam_casting
Stainless steel balloon wall construction would have a far better mass fraction than a 3D printed tank.
In fact it can even be better than carbon fiber in some cases which is why the Centaur stage has such high performance.
And if mass fraction were the relevant figure of merit for a rocket, they would be used all over the place. Instead, in the six or seven decades since they were introduced, they have remained confined to the Atlas/Centaur designs. That’s because they’re such a massive pain in the ass to build and handle that it’s cheaper to build a larger rocket that allows more efficient ground operations.
Pardon my ignorance, but what is the rocket shown in the lead photo?
A Soyuz
I would say it looks like a Sojus rocket.
From the looks, it is the Vostok-K displayed at the VDNKh in Moscow, Russia
Looks like the boosters and configuration of the Soyuz rocket.
https://images.goodsmile.info/cgm/images/product/20171011/6786/48061/large/b6c2ea291d02f60da54612743c81826d.jpg
Nice model.
I wonder what are, and the purpose of those “55 gallon barrels” on the bottom of the model, near the outboard nozzles. They are not on the top photo.
I want to say that they are there to prime the turbopumps and get dumped right afterwards but that’s just an educated guess.
They seem to be transport covers for something. Probably red to show they are “remove before flight” items. See also for instance this pic: https://space.stackexchange.com/questions/27679/red-color-in-the-nozzles-of-soyuz-2-rocket-engines-rd-107-and-rd-108-is-it-only. I can’t find for what exactly though. The turbo pump exhaust is routed differently afaik. In any case it seems to be a relatively recent change, as the older rockets didn’t seem to have them (see for instance: https://www.nasa.gov/mission_pages/station/multimedia/gallery/jsc2011e209247.html)
Looking at it further (I’m intrigued now) they seem to be pressure filters for a supply of some kind. What exactly I couldn’t tell. They clearly aren’t transport covers. (Closer up photo here: https://news.rambler.ru/weapon/39392439-rossiya-nachinaet-razrabotku-dvigatelya-dlya-sverhlegkih-raket/)
Thanks!
Those quotes about sitting atop tons of TNT in a machine with millions of parts built by the lowest bidder…
Now something about layer adhesion can be added to that! Congratulations astronauts!
But, but…
it will only be tens of thousands of parts by then!
If layer adhesion fails… THEN it will be millions of parts/pieces.
B^)
Layer adhesion is really only an issue with fused filament printing, and these companies are almost exclusively using selective laser sintering.
There’s something to be said about the difficulty of inspecting for printing defects in these complex geometries made possible by 3D printing, but layer adhesion isn’t one of the things that they would have to look for.
The rocket industry already habitually inspects welds etc. So out of all industries I suspect they’re already set up for inspecting complex parts.
Nice article.
Couple of little things.
Space X is Missing the X on line ” Relativity Space simply ” near the end.
HA! I lost the other one sorry.
Thank you though……..
For tanks it would be faster and lighter to print the ends, with mounting fixtures integrated, then make the straight sides with sheet aluminum rolled and welded. Smaller tanks could use flat metal. Get larger and use vertically corrugated metal for strength.
On the 42nd page of this PDF you’ll find the dimensions used for the isogrid panels in Skylab. https://femci.gsfc.nasa.gov/isogrid/NASA-CR-124075_Isogrid_Design.pdf
For those the manufacturer milled them from solid plates of aluminum, carving away the vast majority of the metal. A current tech version would use an abrasive water jet to cut the triangles. The holes might be ABW cut too if they’re large enough.
Some rocket fuel tanks have been made from milled isogrids that left a thin skin. Then the sheets were bent into cylinders using a press brake. An expensive and lengthy process.
Faster would be machines that progressively punch, form and roll the isogrid scructure then resistance weld that to the inside or outside of rolled thin sheet metal.
That is an impressive looking machine