On January 21st, 2018 at 1:43 GMT, Rocket Lab’s Electron rocket lifted off from New Zealand’s Mahia Peninsula. Roughly eight minutes later ground control received confirmation that the vehicle entered into a good orbit, followed shortly by the successful deployment of the payload. On only their second attempt, Rocket Lab had become the latest private company to put a payload into orbit. An impressive accomplishment, but even more so when you realize that the Electron is like no other rocket that’s ever flown before.
Not that you could tell from the outside. If anything, the external appearance of the Electron might be called boring. Perhaps even derivative, if you’re feeling less generous. It has the same fin-less blunted cylinder shape of most modern rockets, a wholly sensible (if visually unexciting) design. The vehicle’s nine first stage engines would have been noteworthy 15 years ago, but today only serve to draw comparisons with SpaceX’s wildly successful Falcon 9.
But while the Electron’s outward appearance is about as unassuming as they come, under that jet-black outer skin is some of the most revolutionary rocket technology seen since the V-2 first proved practical liquid fueled rockets were possible. As impressive as its been watching SpaceX teach a rocket to fly backwards and land on its tail, their core technology is still largely the same as what took humanity to the Moon in the 1960’s.
Vehicles that fundimentally change the established rules of spaceflight are, as you might expect, fairly rare. They often have a tendency to go up in a ball of flames; figuratively if not always literally. Now that the Electron has reached space and delivered its first payload, there’s no longer a question if the technology is viable or not. But whether anyone but Rocket Lab will embrace all the changes introduced with Electron may end up getting decided by the free market.
A Tiny Rocket for a Growing Market
The first thing to understand about Electron is that it’s incredibly small and light for an orbital rocket. To put it into perspective, the Space Shuttle could have carried two fully fueled Electron rockets in its cargo bay without breaking a sweat. Accordingly, the Electron has an extremely low cargo capacity, topping out at around 500 lb. Compared to the Falcon 9’s maximum capacity of roughly 50,000 lb, one might wonder what the point is.
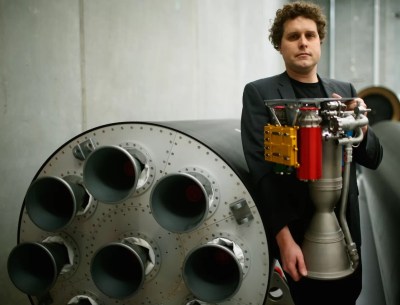
The point, of course, is the cost. A launch on Falcon 9 costs the customer around $62 M, while a trip to space on Electron is less than $6 M. If you’ve got a payload light enough to hitch a ride on an Electron, the choice is obvious. As satellites get smaller and lighter, more and more payloads will be able to fit into this category. In fact, Rocket Lab hopes to be launching as many as 100 Electron rockets per year to meet the anticipated demand.
Pound-for-pound, it’s actually much cheaper to fly on Falcon 9. But a lightweight payload on Falcon 9 will be relegated to secondary cargo. The realities of this arrangement were demonstrated in 2012, when one of the Falcon 9’s engines failed on ascent. This only left enough power to accomplish the primary mission, delivering supplies and cargo to the International Space Station. The secondary payload, a satellite from communications provider Orbcomm, had to be left behind. At only 379 lb, Orbcomm’s satellite could have been a perfect fit for a dedicated Electron launch.
A New(er) Way To Build Rockets
Electron isn’t cheap just because it’s small, the price is also driven down by the state-of-the-art construction techniques being used throughout the vehicle. The combustion chamber, injectors, pumps, and valves of each of the Electron’s ten Rutherford engines is 3D printed via electron-beam melting in as little as 24 hours. This is a first in rocketry, and beats NASA and SpaceX to the punch by years. SpaceX won’t be flying their 3D printed engine until their “Dragon 2” capsule flies later this year, and NASA is still in the early stages of their research.
In another first, Rocket Lab has built nearly the entire rocket out of a carbon composite. This gives the rocket its deep black color, but more importantly, a dry weight that Rocket Lab’s CEO Peter Beck says is “less than a Mini Cooper“. Critically, even the fuel and oxidizer tanks are made of carbon composite instead of the traditional aluminum. Electron is the first rocket to successfully fly with carbon composite tanks, but it certainly isn’t the first one to try.
In 2001, NASA famously canceled the Lockheed Martin X-33 spaceplane, a potential replacement for the Space Shuttle, in large part because they determined that its composite propellant tanks were simply beyond the technology of the time.
The Battery Powered Rocket
But the crowning achievement of the Electron isn’t how small it is, or how fast its engines can be 3D printed. Those are impressive feats in their own right, but arguably just extensions of work that’s been going on for years. They were eventualities that Rocket Lab were able to capitalize on, at least in part, because they have such a tiny vehicle.
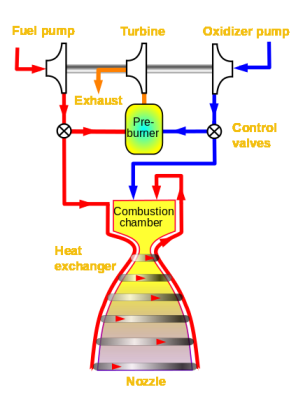
The true revolution is the fact that Rocket Lab has completely done away with the complicated preburner and turbine traditionally used in liquid fuel rockets. Rocket engines consume an immense amount of fuel and oxidizer, and powerful pumps are required to get the propellants injected into the combustion chamber at the necessary pressure. To power these pumps, most engines have a turbine which is spun by what’s known as a preburner. In some cases the preburner uses the same fuel as the rocket engine itself, but can have its own fuel supply with associated plumbing and tanks.
The preburner, turbine, and pumps make up a powerful and complicated system that in some ways is just as difficult to master as the rocket engine itself. Consider that the turbine in each one of the F-1 engines used in the Saturn V developed 55,000 horsepower alone.
In the Rutherford engine, this entire system is replaced with two 50 horsepower brushless motors powered by a bank of lithium polymer batteries. These motors power the pumps directly, and give a level of control over engine operation that would be difficult to match with traditional techniques. With a turbine, spin-up time is directly correlated to throttle response and the engine startup sequence. But by using electrically driven pumps, Electron’s engines are able to respond faster and more accurately to commands from the flight computer.
The downside is that batteries are heavy, and unlike liquid fuel, don’t get consumed while being used. A dead lithium battery is just as heavy as a fully charged one. To combat this, the Electron actually dumps the dead batteries overboard as the vehicle climbs.
This Changes Everything, Right?
The engineering that Rocket Lab has done on Electron and the fact they made orbit on only their second attempt with such a wildly unconventional vehicle is an incredible achievement. There’s no question the Electron itself will be looked back on as a milestone in the history of rocketry.
But while 3D-printed engines and carbon composite propellant tanks are pretty much a sure bet for future generations of rockets, Electron’s engine technology might be looking at a much shorter life. There’s simply no getting around the fact that liquid fuels have a much greater energy density than batteries. While Rocket Lab has managed to find a workable combination of battery weight versus payload capacity in this specific vehicle, the equation just doesn’t work as you scale up the design. At some point, the weight of the batteries simply becomes too great to remain viable.
If Rocket Lab is right, and there’s a huge market for lightweight payloads, then we may see other small rockets adopt a similar engine. But if the market is content getting to space in the second or third class seats of larger rockets like Falcon 9, this innovative technology may end up taking the back seat itself for economic reasons.
Forgive me, but while a carbon fiber rocket with electropump engines is cool, disposing of expensive aerospace hardware is not “smarter.”
And 3D printing does help reduce tooling costs at these small scales, but its material properties are usually worse, and it doesn’t actually reduce cost per unit dry mass compared to most traditional techniques once you scale up. Carbon fiber is also not new to rocketry: even Shuttle used large carbon fiber components (the payload bay doors). And I should point out that SpaceX has been flying 3d printed components on their rocket engines for years. 3D printing does not scale up well, though, which is partly why Electron needs to have 9 engines on such a small rocket.
Electropumps are also cool, but they’re significantly lower performance than typical turbopumps, as was mentioned.
If I were making a small orbital rocket, I probably would also use 3d printed electropump motors, mostly because the setup and tooling costs are low and development is easy.
And a side note: a dry mass less than a mini cooper (~1185kg) is not very impressive since the total vehicle weighs 10,500kg and uses a dense propellant combination like kerosene/oxygen. In comparison, SpaceX’s Falcon 9 boosters have a mass ratio of about 20:1, which is about twice as good as Electron. Electron is pump-fed and uses carbon fiber construction. It should do a lot better than it does.
All the fancy tech in the world is disappointing if it’s just going to be thrown away every time. It’ll only make a marginal improvement on cost of space access as long as it’s expendable. Which might be totally fine as a business, but it is disappointing.
Smarter in leveraging a continuing trend, of satellites getting smaller and smaller. Kind of the way computers getting smaller changed things.
Well some kinds of satellites are getting smaller but com sats have been generally getting larger as increased data rates need a higher signal to noise ratio and the easiest way to do this without making the ground receiver dish larger is to make the satellite transponders more powerful which in turn means the satellite gets heavier.
Ariane 5 used to be able to almost always two large geo stationary com sats but now it’s difficult to get a co manifest as to primary payloads are often too heavy now.
The article explains quite clearly why the use of carbon fiber in this rocket is impressive and innovative. Did you read the article?
I don’t know about the other guy, but I read the article. SpaceX flies composite overwrapped pressure vessels which carry 5000 PSI helium inside of a supercooled LOX tank. So I am not so impressed with a small vehicle with carbon main tanks. Sure it is nice that they got to space. I am dubious that they are economically feasible when a larger rocket can launch many microsats at once for a much lower cost.
Well. When you have ten satellites you can launch them into one orbit with a falcon nine for $62M, while you can get 10 rides to different orbits on electrons for a very similar price. If I didn’t know otherwise, I’d say that launching ten satellites into one orbit is ridiculous and nobody would want that…..
Sure. But those 10 Iridium satellites each weighed 860 kg or 1895 pounds. So, not a lightweight mission. And they went into different orbits, simply due to timing and direction of release from the payload adapter.
It is to be expected that Falcon launch prices will continue to go down as the technology matures and sunk research costs have been recovered. Right now, SpaceX is experimenting with fairing recovering, which should save a few million per launch. With Falcon Heavy (or BFR), they may be able to reuse the 2nd stage, for full reuse of the rocket.
Also, if the market for micro satellites is really big enough, SpaceX could adapt their technology to make a small/cheap rocket, perhaps with a reused engine from an F9 launch, whereas Rocket Lab has gone into a dead end that doesn’t scale.
Do your math again. The Falcon 9 has 100 x the maximum payload for only 10 x the price. Even allowing for payload adapters/deployment mechanisms you should be able to put a batch of small satellites into orbit for 1/5 or less of the price.
Now if your small satellite requires an unusual orbit then the Electron might be a feasible option, but otherwise forget it.
Adding to that, satellites normally have their own manoeuvring thrusters and can make their own way to their intended orbit once they are at least in LEO (Falcon lifts coms satellites into what is called GTO, i.e. not a geostationary orbit, but close enough to allow the satellite to make its own way to its intended destination).
Rockets tend to benefit from the square cube law so it would be more fair to compare it to Falcon 1 which was closer to the same size and there the disparity in mass fraction is not as bad.
A turbo pump is going to have a much higher power to weight than an electric motor and batteries even pistons engines and gasoline usually has a better power to weight ratio.
But here cost is the driver as the turbo pumps can account for %55 of the total vehicle cost.
The the electric pumps have no combustors and hot side turbines.
Chris,
You mention how the Electron doesn’t scale up; I think the point of this article is how traditional technology like the Falcon 9 doesn’t scale down. That’s the cool thing about economics; in the long run supply is only produced if there is enough demand for it. If current rockets are “better” then no one will pay for Electron’s services and they won’t be around anymore.
> the Falcon 9 doesn’t scale down
SpaceX started with Falcon 1, so it does scale down, as long as you don’t care about reuse. But reuse of a big rocket has the potential to be cheaper than a single-use small rocket.
We’re left to assume exactly what era mini cooper this rocket is meant to be equal to in dry weight.
If it’s a classic cooper like that driven by Mr. Bean then the weight could be anywhere between 550-700kg, depending on the level of rust.
That I would call very impressive.
“And 3D printing does help reduce tooling costs at these small scales, but its material properties are usually worse”
It flies, though. So it must be within tolerance. You don’t have to use the best available, you use what gets the job done. They’re filling a niche in the market. And their second-try track record is pretty dang good, I’d be surprised if they didn’t make meaningful contributions in the long run. I think it’s good that there’s lots of companies trying lots of little variations.
Yes SpaceX is awesome and yes buying in bulk is cheaper but I still buy parts off RS at 10x the price they are on digikey because I’ll have them tomorrow morning.
A small rocket will launch to your schedule. And simplifying the build means shorter lead time. The space industry is dragging itself into the 21st century where waiting 20years from design to launch is not acceptable. Technology moves on too fast. Smaller satellites have shorter build and development cycles and don’t want to wait 5 years for a launch slot because launches to your required orbit are rare, you have to find a suitable main payload and then the main payload has a delay. You don’t want to have to design orbital manoeuvring hardware just because your in a run of deployments not in your target orbit. Perhaps the better analogy is taking a taxi rather than a bus; it goes exactly where you want, when you want, and the driver is flexible to delays because you are the only customer. What is interesting is that normally this would come at a huge cost, but Electron have used smart ways to reduce the natural inefficiency of ‘small’ by reducing part count and complexity to keep costs down and reducing weight and improving specific impulse to compensate for heavy batteries. No this isn’t the distant future that SpaceX is pulling us towards at an impressive rate, but this here and now allows simple small satellites to go into orbit with convenient timing and affordability.
3D printing rocket engines is a legitimate hacker project. Here’s a blog post from back in 2012 that chronicles the adventures of 3D printing liquid rocket engines and actually testing them:
http://rocketmoonlighting.blogspot.com/2012/03/more-testing.html
Almost everyone is 3D printing small rocket motors. There are at least a dozen or so small satellite launcher startups that are 3D printing rocket motors, Rocket Lab is just one of the higher profile such startup, and also one of the best funded.
It’s one of those applications of 3D printing that is legitimately easier with 3D printing, since you can print a nearly complete chamber with integrated cooling passages and the right shape. Lack of moving parts in the chamber component also means you can get away with the worse tolerances of 3D printing. It’s great if you just need a small regen cooled liquid rocket motor. Large motors don’t work well with the technology.
Do they have a filament loaded up with some kind of solid rocket fuel anywhere? That would be neat. You could print out a self-consuming solid rocket with whatever interior passage and nozzle design you want. Stick it in a metal pipe.
It would be very bad news if your hot end thermistor failed, though.
Wrong type of 3D printing. These are using electron beams to melt metal powders (like laser sintering) rather than FDM.
ABS burns just fine as a hybrid propellant!
Not a Rocket Scientist but in theory a hydrogen fuel cell could replace the battery and you would as a by product have waste water you could use as propellant. From other comments I heard the electrical pump does not scale to bigger rockets but fascinating technology to read about.
Fantastic achievement by rocket labs by the way, hope to get up to Hakwes Bay and see a launch sometime in the future.
The power density of the fuel cell doesn’t meet the demand.
After reading your comment, at first I didn’t think replacing batteries with fuel cell might be possible because of the power requirements. Apparently, the battery from the first stage of an Electron rocket delivers 1MW of power. After some research, this seems to be in the range of the most powerfull fuel cells. So, why not ?
However, it seems that power cell have a lower power density (by unit of mass) than batteries. Moreover, the hydrogen used for the power cell is not dense at all, so it would make for even bigger fuel tanks.
As for using the water as a propellant, the main problem is that it can’t be used for a combustion. I think it would only degrade your engine’s efficiency (Isp) as the water would reduce the exhaust’s temperature, but it could still maybe increase the thrust. Otherwise, you could probably use it to cool your nozzle or provide some sort of thrust vectoring.
Electric motors do not scale to bigger rockets because of the power requirements for the turbopumps. The turbopump of one F1 rocket engine on a Saturn V generates 41MW of power. Even for smaller rockets such as the Ariane 5, the Vulcain engine’s turbopumps generates 3 and 12 MW of power. This to be compared with the electric motors available today (I think the max is in the 35MW range)
What about using a small steam-powered hybrid turbopump that uses the water from the fuel cell being routed through the nozzle to boil the water to reduce the electrical energy necessary to run said turbopump?
No point. The purpose here is simplicity. Bringing a fuel cell with you is less mass efficient than using a traditional turbo pump from a preburner. If you want to hunt efficiency, use a high pressure high flow preburner pump and feed this exhaust into the combustion chamber so you get the best Isp. This was thought to be impossible by the US, but Soviet Russia did it in the 70s and those engines are still class leading. However, fuel is cheap so make the rocket cheaper and efficiency doesn’t matter so much.
Not enough energy density to make the system lighter than a bettery.
You might say it’s a worsery.
would like to see the lithium batteries replaced with a beamed energy receiver and ground station
That would be… interesting indeed. The first stage engines together use around one megawatt of electric power. To make up for losses, the transmitter needs significantly more power. So, if launching an orbital rocket is not exciting enough, let’s go and point a multi-megawatt energy beam at it!
Glo-stick.
To combat this, the Electron actually dumps the dead batteries overboard as the vehicle climbs.
Oh, I _soooo_ want to know more about this.
Probably check Ebay. :-D
By this, I’m pretty sure they are referring to the staging of the rocket.
No, they stage off the batteries as they are used. This is particularly important on the upper stage, where the burn lasts a long time and there is a very harsh penalty for burn-out mass (as it effectively reduces the payload one-to-one).
This is analogous to staging off the fairing or in the original Atlas where some of the booster liquid rocket engines (not stages!) were staged partway through flight.
There is an onboard video* of the rocket dropping pairs of battery packs out the back as it ascends.
*youtube is blocked at work, so I can’t post the link.
If I’m not mistaken they are the blocks wrapped in some type of of aluminium-looking foil, that you can see near the engine nozzle. You can see them being dropped in the video from the launch:
https://youtu.be/eg5234BOED8?t=21m16s
So I don’t think much will be left of them afterwards !
My immediate reaction was also to get a boat and go downrange with my fingers crossed. Might be a fun physics problem to figure out where they would jettison and where they would land.
When they either figure out how to recover the used packs of batteries(lithium…should be rechargeable right?) or find a way to construct the skin of the rocket as a huge supercap, then they will be on the right track.
Well, there are consumer lithium batteries that are not designed for recharging.
For example (PDF warning)
http://data.energizer.com/pdfs/l91.pdf
And then they pull this stunt…
https://science.slashdot.org/story/18/01/28/0217253/rocket-lab-criticized-for-launching-their-own-private-star-into-orbit
Yawn…
“long term graffiti” is going to de-orbit soon.
It’s a sad worl… universe full of complaining people.
True, it’s only going to be up there for a few months. But when people recall RocketLab, they’ll think of how they used their first flight to put up space spam.
“100% PURE New Zealand” as the marketing campaign went, but they’re happy to send crap into orbit :)
Yeah, really, why couldn’t they just send up a dog or monkey to die like everyone else, or maybe an electric car like some other PR stunt… This is just proof of concept but people like to bitch.
Some people are offended by this because some people are cripplingly stupid.
I assume you also talk in libraries ?
“Free market” there’s no free market today in any industry.
Maybe meant in the open source “free” as in freedom to hack.
I wonder if an electric motor cycle would be appropriate for thrusters and kick motors. If they could largely use satellite or upper stage onboard power and reduced (possibly autogenous) pressurization, would mass savings be attractive enough to use electric turbopumps?
I was thinking Rutherford could be used as a OMS on a manned vehicle as they already have large batteries that could power the engine and solar panels or fuel cells to recharge them.
Two of them would have slightly lower thrust than an AJ-10-190 but would have a higher ISP and the propellant tanks could be much lighter.
For RCS, even the lag of using an electric pump is probably too long, and almost certainly still too complex. For maneuvering you really need a cold gas or hypergolic thruster: something you KNOW will work as soon as it gets the command.
But low-thrust kick stages for circulization and that sort of thing, there’s definitely potential.
What Rocketlab accomplished is an amazing feat for such a small aerospace company. It’s a great example of the thoroughness and practicality of their talented engineering and manufacturing team as well as management in getting all their ducks in a row. Pulling off a successful launch on their second attempt is extraordinary, and even more so when you consider that their first may have ended up being successful as well if they didn’t terminate the flight (due to a contractor’s faulty configuration of their ground-based tracking system).
As for their tech, I’m really impressed with the power density of their turbopump motors. 50HP in a motor of that size seems unusually high. I don’t know if it’s achieved strictly on account of its operational speed, or they benefit from potentially using the propellants as coolant.
Well done, Rocketlab team with your fantastic rocket.
Fist this is not addressing grumpy personally, just the people we where pointed to.The “star” has a limited life time, and reads like it will be seen twice a day. In that light those complaining need to figure out how to remove the cob that is evidently stuck up their collective butts.Yea I understand even if it it’s shine can’t be see doesn’t mean it can’t be detected, but given it’s smaller than a man’s torso, and and traveling at least hundreds of miles per hour, but it’s presence will be brief As soon as this is known amateur radio operators will be scrambling to build antennas on a mount they can hold and aim like a gun.
Doesn’t sound much worse than Sputnik, and it hasn’t terrified the shit out of the world with imminent nuclear armageddon.
Should’ve used this as the intro
https://www.youtube.com/watch?v=4zKiow0evjc
How about using a cheap piston engine to drive the fuel pumps? Add a tank of gasoline and bleed off some of the liquid oxygen for the engine. Buy those cheap ones from Harbor Freight then mod them for more power. https://www.ombwarehouse.com/performance-parts/predator/predator-212cc/
A 50HP ICE engine and fuel tank probably isn’t all that much lighter, but is a lot more complex plumbing wise and would need additional considerations. Also it wouldn’t be as fast to react.
Because a LOX/Gas engine would last about 2 seconds before it melted. You really would have to cool it big time. Maybe a turbine since it would be more efficient and a higher power to weight ratio….. Ummm never mind.
I feel like if you’re packing separate fuel and using the engine’s liquid oxygen to burn it, you might as well use a traditional turbine. You’ll never get a similar power-to-weight ratio out of an ICE. Turbines have absolutely silly power-to-weight-ratios, which is why you see so many more of them in aviation than ICEs these days.
Can’t blame you for considering such an idea. Though I’m not sure the turbines need such an engine. Lower weight electric motors with rapid response time and high RPM seem to be the wining formula at this scale as opposed to torque and longevity.
As a matter of fact I don’t discount Rocket labs from considering at least half the ideas brain stormed by commentors here.
Start with a little math. The current system uses 1MW between 9 engines. 1HP is about 750W, so you’d need 9 x 150HP engines as a minimum to match the current system, plus a quantity of nitrogen to mix with the oxygen to stop the pistons melting, plus cooling systems (your IC engine is, at best, around 30% efficient, so you’ll need to remove about 2MW of heat).
You think that lot is going to be light?
“A dead lithium battery is just as heavy as a fully charged one.”
I am not sure about this and doing some research on the we has not helped at all. I subscribe to the theory that the difference will be in the nano gram range but a discharged cell will be lighter. This is just my guy feeling though. I wish I still had access to a lab I used to work in. We had a very sensitive scale. It would be interesting to see if the difference could be measured.
I was thinking that too. Similar to the trivia that a compressed spring is minutely heavier than a spring at rest. But I think it gets rounded off if the extra ink on a misprinted label on the battery would greatly outweigh that difference.
I wonder if they peel the battery sleeves to shave off those grams? I bet they do.
On the pumps, the big win is that if the entire motor is submerged, there would be no moving parts sealing requirements.
A rocket motor pump usually has a single shaft with 800 degree hot gas on one end, and some chilled fuel and also some – 187 degree liquid oxygen I the pumps, all 3 systems share a single shaft. The shift runs ridiculously fast, the temperatures vary hugely. Any leakage could be catastrophic and I could not even imagine the weird lubricants required. A submerged electric pump only has to consider cold temperature lubricants. The cooling effect of being in a steam of liquid oxygen would increase the power output of the motor massively.
I think a submerged rotor would be problematic at the required rotational speed. At the very least, drag would be increased. But maybe the power density increase would offset that. The question is: is it even worth doing? The pumps are probably a small fraction of the dry weight, and since most of them are on the first stage, there wouldn’t be a significant payload increase. Still would be cool to see done.
The major benefit is in the lack of seal requirement. The pressures are huge and the temperatures extreme.
I cant see the rotor being a drag, A turbine already has spinning bits, integrate the motor into the turbine, Assuming the turbine is a centrifugal unit (most likely) then the one end is flat and not in the main flow path, this is where you integrate a flat axial flux brush less motor by embedding rare earth motors into the turbine.
That kind of motor packaging would certainly be interesting, if possible.
Completely off-topic (with a tongue-in-the-cheek): Anyone else spot an AIM-54 Phoenix in the title image of the article? :D :D :D :D :D