Vacuum tubes fueled a technological revolution. They made the amplification of signals a reality for transatlantic telephone cables (and transcontinental ones too), they performed logic for early computers, and they delivered that warm fuzzy sound for high fidelity audio. But they were labor intensive to produce, and fragile, so semiconductors came along and replaced tubes in almost every application. But of course tubes are still with us and some tube applications are still critical — you’ll find them used in high-power RF and there are even satellites that depend on klystrons. So there are still experts in tube fabrication around, and Charles Alexanian is one of them. His newly-published talk at the 2018 Hackaday Supercon (found below) is a whirlwind tour of what goes into building a vacuum tube.
The process of building your own vacuum tube isn’t hard, but it’s not a walk in the park. The difficulty comes in the sheer number of processes, and the tricks of the trade found at every step. Charles’ methaphor is that if you build one tube at a time each step is like learning to ride a bicycle again, but if you build many you get into the swing of it and things go a lot better. His talk is a brief overview of everything, but if you want to drill down he also wrote an excellent article that goes further in depth.
In the working components of each tube are the precision parts: the grid (or grids). For the tube to function well these must be accurately produced which can be done with photolithography, but Charles usually uses a winding process involving a lathe. After winding, the grid is stretched to straighten the nickel wire, then cut to length. Other components such as the plate are stamped using an arbor press and simple forms he fabricates for the purpose.
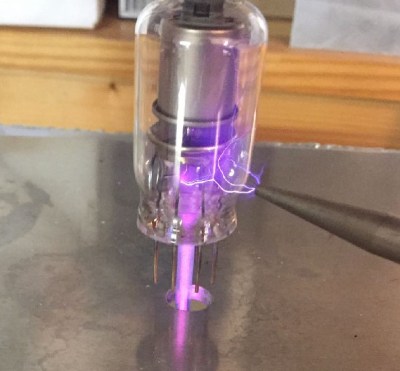
Two glass components are used, the dome itself, and feedthrough stems that have a wire for each lead passing through a glass disc. The components are spot welded to the inside portion of the feedthrough stem, then the glass is fused together, again using a lathe. It heads over to a pumping station to evacuate the air from the tube, and is finally tested for leaks using a handheld Tesla coil (see, we knew those weren’t just toys).
Charles proposed his Supercon appearance as a chance to fabricate tubes on-site. We loved the idea, but the amount of gear needed is somewhat prohibitive (annealing ovens, vacuum cabinets, torches for sealing, and the need for 220v, plus space for it all). That’s too bad since we were really hoping to see the Jolly Wrencher in Nixie-tube form — incidentally, Charles says Nixes are simple to make compared to amplifiers and switches. He also mentions that the majority of your time is spent “washing” parts to remove impurities. Fair enough, that part sounds boring, but we hope to endure it at some point in the future because vacuum tube fabrication demos feel very much like a Hackaday event!
I can’t get past reinventing a light bulb.
as much as i love the work shared, your comment makes me feel happy enough to smile for once.
-steve dave, pLa
I didn’t do a whole lot other than Flame Test loops and the term isn’t coming to mind with melting broken glass edges until they’re rounded… mental fart. The knowledge and hand crafted talent of Charles Alexanian is impressive. I want to see the 90 minute presentation. Wondering if there are any potential advancements for vacuum tubes or even testing other electronics components inside? Seems for cooling might be capabilities or even temp stabilization and not just electric or magnetic effects.
Wondering if there is something regarding the Rydberg Laser Excited Gas Cell EMF Modulation Detector that can be studied and advanced in a novel way? Seems like can be coupled with the solar concentrating trough systems unless there is a temperature fluctuation issue that can’t be compensated for. https://www.technologyreview.com/s/611977/get-ready-for-atomic-radio/
Not sure if the technology is related… though seems like a valuable area of opportunity.
“the term isn’t coming to mind with melting broken glass edges until they’re rounded”
Fire polishing, or flame polishing.
Thanks… I knew I’d have a “…man… I knew that!” moment. I kept thinking glazing and I knew that wasn’t it.
Are there benefits in lower power circuits to having components in a vacuum other than reducing size maybe which is more practical for the larger spec’d components like say variable capacitors?
I don’t recall seeing a variable inductor in a vacuum tube before. Was wondering if there is a benefit or potential improvements with new materials for components in vacuum tubes now days?
Maybe water cooling, other components or other sensors inside a vacuum versus just potting to shield.
Love in a Vacuum https://g.co/kgs/fNZEWu
AKA “my embarassing time at the hospital”
The Art of Making a Nixie Tube – https://www.youtube.com/watch?v=wxL4ElboiuA
The dude that probably taught him everything he knows. https://www.youtube.com/channel/UCp4ZTfBiTwQM6YhQcduwuHw
Interesting. that could have easily been a half-hour or hour-long presentation and there’d still be lots left out.
No.. this is the art of the vacuum tube…
https://commons.wikimedia.org/wiki/Category:G%C3%A9rard_Aubry_(botelliste)#/media/File:F8DU_1988.jpg
;¬)
OK I keep forgetting.. no edit button.. just click the image link anyway.. trust me, nothing bad will happen.
https://upload.wikimedia.org/wikipedia/commons/8/8b/F8DU_1988.jpg
A modern day “ship in a bottle”.
Nope- that isn’t Art, it;’s, d’Edmond Aubry.
I imagine art would be something like circuit sculpture with the internals of a vacuum tube.
The early RCA receiving tube manuals had a overview of vacuum tube construction,
http://www.nj7p.org/Manuals/PDFs/Tubes/RCA-R-10-1932.pdf
Those RCA manuals are a trove of good tube information.
I’ve wanted to make some high-vacuum equipment for some of my experiments, but could never find getter rings.
Does anyone know where to purchase these?
You could try… https://www.saesgetters.com/products-functions/products/getters
… or here … http://vdbtc.com/language/en/getters/evaporable-getters
https://youtu.be/EzyXMEpq4qw
I admire the skill, but I’d describe it as a craft, rather thuan art. I’m probably in that last age group that only heard tube audio. I was never turned off solid state, no real old timers never complain about the soud quality, and there ers where still young when solid state took over. On guy said he could hear the old sheo box Jhonson CBs than he could newer smaller solid state units. Well.. yea, but it’s an apples to oranges comparison.. The audio amp in the tobe rigs had a higher audio power output, the radio cabinet made a better speaker cabinet, the speaker was directed to the operator, not the floor.
Sometimes a good external speaker made all the difference.
https://www.youtube.com/watch?v=MbZW4ghzquw
Nice!
When I was in college, I had a job in the basement of the Grad Research Center. My neighbours were the technical glassblowers, the craftsmen who made all the one-off lab glassware for the researchers. They always walked around in dark glasses, and had one of those lathe/array of torch nozzles things. Also, many torches, always alight. They were clever enough to have their lab right across from the elevator, with a large picture window, so you could watch them working as you walked off the elevator.
Real nice guys, too.
It would be a lot more practical to just put a transistor or three inside the tube.
Years ago an acquaintance (ham) of mine was converting a vacuum tube receiver to transistors. He used the broken base of vacuum tubes to mount the transistor circuitry.
I don’t know if he succeeded in that.
There are solid state tube replacements on the market that plug into tube sockets.
Here’s a rectifier: https://www.amplifiedparts.com/products/solid-state-rectifier-5ar4-5u4-5y3-tubes
I’d love to be able to make or get something or someone together and make sweep tubes. Just a few of the more robust ones for RF that are used in some older amateur radio equipment and even the multi band amplifiers that used to be on the inexpensive side. And one with limited income could get an old set restoration going by replacing all the old electrolytic capacitors and out of tolerance resistors and week tubes. Tubes of interest are the 6 or 12 volt LB LF LR6 something with the bigger 33 watt heater and some parasitic suppression for easier 10 meter operation. Like the yellow label Sylvania 6LF6. The 12v 8950. The 6JE6 9pin. The shorty 6KV6. The hot rod 6L6 otherwise known as a 8417 more negative bias and plate voltage. I’d like to see that 8417 for audio purposes too! 813’s where a great tube for rf. Why didn’t they build more amps using those instead of the fragile 811 idk? Use a 572 in the 811s place running on less plate voltage will be rugged like the Ameritron 811HD that you could get a set of 572b’s in it.