Blacksmiths were the high technologists of fabrication up until the industrial revolution gained momentum. At its core, this is the art and science of making any needed tool or mechanism out of metal. Are you using the correct metal? Is the tool strong where it needs to be? And how can you finish a project quickly, efficiently, and beautifully? These are lessons Blacksmiths feel in their bones and it’s well worth exploring the field yourself to appreciate the knowledge base that exists at any well-used forge.
I had an unexpected experience a few days ago at the Hacker Hotel weekend hacker camp in the Netherlands. At the side of the hotel our friends at RevSpace in The Hague had set up a portable forge. There was the evocative coal fire smell of burning coke from the hearth, an anvil, and the sound of hammering. This is intensely familiar to me, because I grew up around it. He may be retired now, but my dad is a blacksmith whose work lay mostly in high-end architectural ironwork.
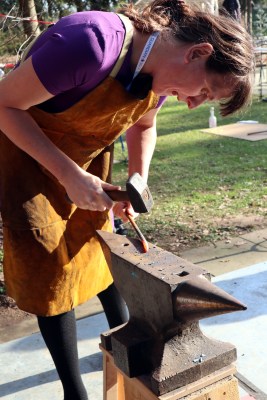
The trouble is, despite all that upbringing, I don’t consider myself to be a blacksmith. Sure, I am very familiar with forge work and can bash metal with the best of them, but I know blacksmiths. I can’t do everything my dad could, and there are people we’d encounter who are artists with metal. They can bend and shape it to their will in the way I can mould words or casually solder a tiny surface-mount component, and produce beautiful things in doing so. My enthusiastic metal-bashing may bear the mark of some experience at the anvil but I am not one of them.
It was a bit of a surprise then to see the RevSpace forge, and I found myself borrowing a blacksmith’s apron to protect my smart officewear and grabbing a bit of rebar. I set to and made a pretty simple standard of the dilletante blacksmith, a poker with a ring on one end. Hammer one end of the rebar down to a point, square off the other end for just over 3 times the diameter of the ring, then bend a right angle and form the ring on the pointy end of the anvil. Ten minutes or so of fun in the Dutch sunshine. Working a forge unexpectedly brought with it a bit of a revelation. I may not be a smith of a high standard, but I have a set of skills by virtue of my upbringing that I had to some extent ignored.
Where others might have put effort into learning them, they’re things I just know. It had perhaps never occurred to me that maybe all my friends in this community didn’t learn how to do this by hanging round the forge next to the house they grew up in. If I have this knowledge merely by virtue of my upbringing, perhaps I should share some of it in a series of articles for those in our community who’ve always fancied a go at a forge but have no idea where to start.
What Is A Forge?
Blacksmithing starts with heating a piece of metal to a temperature at which it becomes readily malleable, so every forge must have some form of hearth or furnace in which that can be done. There is a choice in this matter, between solid fuel, gas, and even electric induction. We’d love to see our community prove us wrong on this but the last option may be beyond the mains hook-up of most experimenters, so assuming that you have somewhere with enough ventilation or flue to safely run one we’ll look at the solid fuel and gas hearths that might be within the reach of an experimenter.
Gas Or Solid Fuel, Which Is For You?
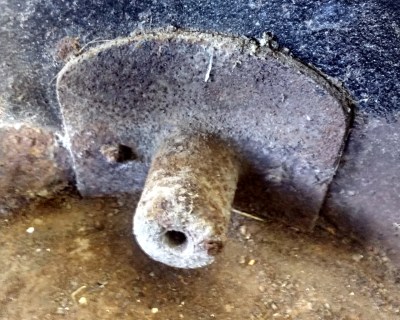
If you think of a traditional blacksmith’s forge, you may be imagining a broad square or rectangular hearth with a chimney hood over it, upon which sits the bright glow of a coke fire. (If you are unfamiliar with it, coke is simply coal which has had the volatile components removed by heating, leaving mostly just the carbon. This is the fuel upon which blast furnaces run.)
In older buildings they may be built into the fabric of a wall, but more modern ones will be more like a steel table. They will have a recess lined with firebrick in which the fire sits, at one side of which will be a cast-iron nozzle called a tuyere (Originally a French word, pronounced something like “tweer” in English) through which air is blown to sustain the fire.
Rustic traditional forges might have had a set of bellows for the air supply, but modern ones will have a centrifugal fan or similar. It’s important to note that the requirement is not for a blast of high-pressure air but for a constant draught, as if you were able to blow continuously upon it. For this reason fan motors will often have some means of speed control.
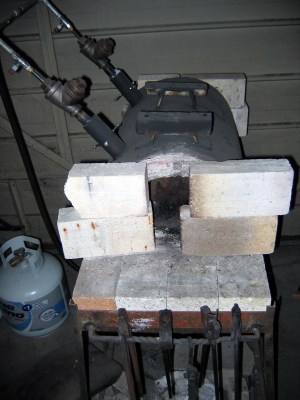
The good news is that you can make your own solid fuel hearth with ease. If you don’t fancy fabricating a large sheet metal construction in the manner of the commercial forges there are plenty of other things that can be pressed into use. The classic quick-and-dirty portable hearth is a truck brake drum lined with firbrick, but a quick internet search will find converted barbecues, automotive wheels, and even pet food bowls. The tuyere will need some attention though, unless you treat it as a sacrificial item that just burns away it will need to be substantial enough not to get too hot. Commercial tuyeres are surprisingly expensive, but there should be many pieces of cast iron that could be adapted. For years my dad’s hearth used the central boss from a very large cast iron industrial pulley, for example.
Gas hearths are similarly easy to construct, in that a decent sized propane blowtorch will provide enough power when its flame is contained within a firebrick structure to contain that heat. At its simplest this can be a loosely assembled set of firebricks as my dad used when he needed to go on-site, but it can easily be a more robustly assembled furnace. A well-known DIY project is the so-called coffee can hearth, in which a metal can is lined with fireclay. A word of warning with respect to gas hearths comes with respect to the safety of handling bottled gas. Some of the smaller handheld gas torches might not quite have enough heat in them to do much good.
How Hot Should You Go?
If you crank up the air on a solid fuel hearth it can become very hot indeed, to the extent that a piece of steel will happily melt or even burn in it when left too long. You will either be left with a puddle of iron in the bottom of the hearth, or withdraw a piece of white-hot steel that is burning and sending off sparks like a firework. Both of these are things a much younger me has managed, you only learn some things as a teenager by experience.
Your aim should be to run the forge with just enough air or gas to take the metal to working temperature, at which point it should be at most a not-too-pale yellow in colour and certainly not shedding any sparks. It’s a finely judged process, but I will push the piece of metal into the coals to about 1″ (2.5cm) beneath the surface such that I can still just see it, and withdraw it at the point that its colour just about matches that of the burning coals. I then have somewhere up to a minute’s working time with a piece of light steel, during which time it progresses from yellow through orange to a dull red.
Our path through starting forge work will be quite a long one, because to do it justice will require a lot of topics to be covered. Having talked in general about the origins of this series and then about hearths, we’ll move on in the next part of this series to the anvil. It’s the most iconic of blacksmith’s tooling, and holds a surprising complexity. See you next time!
Just finished building my first forge (coal) two weeks ago, and picked up a great deal on a 200+ year old Peter Wright anvil. Been hammering away at the local blacksmith’s guild meetings, now I do so at home as well :) Should be warm enough up north here to fire things up this weekend and start making more tools.
Someone on craigslist a few months ago, was asking $600 for a Peter Wright anvil .
I’m hoping to find an anvil, (any kind?) in the $100-200 range.
I wish you luck. I picked up my 120lb Peter Wright for $340 on Ebay because the guy selling it had no idea what he had, and that was a steal at today’s prices. Thankfully it was located about an hour and a half away from me, so I didn’t have to pay the $125 to ship it. I’ve been told I could easily get $600-800 for it as is.
You want an anvil, not an ASO or Anvil Shaped Object. Real anvils are made of steel, or very hard iron. The typical ASO is made of cheap and soft cast iron.
I am lookig forward to read the follow-up articles in this series. Thank you, I am sure I will learn some interesting things!
Ditto!
Same here. This is the good stuff. Knowing how things work right down to the bottom is often key to building up to something new. I found old books by Carpenter Steel useful in learning about heat treat, martensite, austenite, perlite, and so on, was well as how to tell what’s in your sample by the sparks it makes on a grinder…not everyone can do XRF on their budget.
One of my first experiences echoes Jenny’s: that fire is way, way hotter than I anticipated and all the steel rings I put in there were simply burnt to nothingness by the time I pulled them out, intending to weld them closed.
Gas forges are significantly easier to use, clean, start, and weld with. It’s getting harder to even find low-sulfur coal for welding.
For what it’s worth, the fuel to go for here in the UK is furnace coke, and its trade name is Sunbrite Singles.
Essentially it’s the coke you might once have seen produced by old-fashioned gasworks, or I’m told in the steel industry.
I think Mr. Sipola needs a new more tongs… O.o
And my woodshop needs more clamps, my electronics bench needs more meters, and power supplies, every toolbox (including the ones that overflow) needs more tools!
No, the overflowing toolboxes need more toolboxes! :)
Also, Jenny: Why on earth was that anvil so low? I have a backache just looking at the photo!
Every Tolkien reader knows the Dwarves are only surpassed in metal working by the Elves!
Well it’s our “portable” setup, the guy who brings it is not very tall, and Jenny List IS very tall :)
That’s a perfectly reasonable explanation, thanks for clarifying!
I’m extremely tall, and I think RevSpace’s portable forge may be designed for people of less stature. :)
But yes, I’d add a foot to it, myself.
Preferably, the height of the anvil is determined by standing straight with your arms at your side holding the hammer with the handle parallel to the floor. The correct height for the faceof the anvil would be from the face of the hammer to the floor.
Might leave a note here on the distinction between blacksmithing and farriery. The farrier, who trims horses hooves and affixes (iron) shoes is sometimes called a blacksmith. Farriers and blacksmiths reserve the term blacksmith for the fellow who does what Jenny’s dad did. In earlier times the blacksmith’s place of operation or employment was called “the smithy” and one might take one’s horse there for shoes.
It’s a bit confusing, as anyone who knows even a bit of French or Italian will see the word farrier as meaning “worker in iron.” Oh well, if it weren’t a bit confusing, it wouldn’t be English.
Very true. My dad is definitely not a farrier.
In other words, blacksmiths are the serious craftsmen, but farriers are just horsing around?
“WHAT IS A FORGE?”
Related to a Geordi, I believe.
That would be a “La Forge”, or is that just the French version? ;)
Jenny,
WHERE are YOUR safety glasses????
B^)
Oh I know, and the hefty boots. :)
TBH hammering like that I rate as not particularly eye-dangerous. Grinding etc, yes.
Not a safety nazi question, but what about a dust/ventilator?
When I’m grinding I wear one for all the metal dust in the air.
Obviously grinding is often done in forging but I rarely see people in media wearing masks when hammering (or grinding TBH).
Sparks flying off, the “crust” being removed, even the burning of metal of un/known origin, is none of that carcinogenic? Or even just air borne and small particles?
If you blow your nose after a good forging session is it not full of black bits ?
If grinding heavy rust, yes. Bright steel, not especially. Not sure whether that’s the Right Thing To Do, just what I do.
I made a filter out of a couple of ring-shaped neodymium magnets on a string that I hung under my nostrils while I ground bright steel.
What I cleaned off of them made me a believer in good masks. You’re born with a lot of extra lungpower, and lose it year by year, and toward the end, you need every bit.
A great resource for the beginner is http://anvilfire.com/ they also have some amazing new burners if you are building your own gas forge.
I wish I could find an anvil for a reasonable price. Everywhere I look they are ridiculously expensive. I can make everything else, but an anvil, or anvil like substitute is a necessary starting point.
I’m in the same boat. Been looking for years for a decent anvil in the 200lb range that’s a) not a hunk of scrap and b) not priced like it was pure gold bullion. So far I’ve found nothing. I’m in the eastern part of NC, and the pickings are mighty slim…
Get a railroad track anvil and use it. Ebay has a few of them. I know the pros hate them, but for a lot of folks starting out they aren’t that bad. Not everyone can afford to drop nearly a grand for just the anvil.
They don’t meet the requirements for anything much over jewelry making. You’re better off getting a 4×4″ scrap of bearing steel as long as you can afford and securing that in a stump.
You can obviously use anything heat resistant as an anvil but rail will suck the energy out of you making everything harder than it meeds to be.
Ever since forged in fire came out everybody wanted to own an anvil even if they didn’t know how to forge or have serious intent to really follow though and learn.
Among my fellow blacksmiths, the word is if you can get an anvil by weight 4 less then a couple dollars per pound you are doing well if it is in good condition. Going rate for anvils no matter the age or condition if that’s not a factor to the person selling is around $4 a pound.
I started with a piece of railroad tie myself and that’s all I had for a couple decades, but truth be told I wasn’t doing real blacksmithing on it. I only found my forge group about 4 years ago. It works, but is not ideal.
What would be ideal is finding your local scrap yard that buys scrap tool steel h13 dies from a local tool and die shop. It’s already hardened and if you don’t mind random shapes machined into it, finding a solid block of high-quality tool steel several hundred pounds or more should not be a problem.
Very true. The next installment deals with anvils.
There are cheap anvils, but you get what you pay for. You may be better finding the largest piece of steel stock you can and using that even if it’s not the hardened stuff.
Aside from the railway track anvils there are people who make their own full-size anvils, amazing work but for the time invested I’d buy one.
Because if you think about it, how much is too much? On my bench I have a ‘scope that cost about £350, for instance, that’s >$400 afaik. Do I consider that to be too much? No, it’s a decent peice of kit, indeed it represents something of a bargain. So £500 for an anvil isn’t too bad if it’s the signature tool of the work you are pursuing.
I don’t think I’d pay new anvil money foe a second hand one though, and *especially* not for a damaged or broken one. Old anvils are great, but they’re not special, they work *exactly* the same way as a modern anvil of the same quality. There is no mysitic woo infused into them by the sweat of the smith that owned them in Days of Yore, you ain’t going to forge an eldrich blade or something.
Reasonable price?
B^)
https://eauclaire.craigslist.org/atq/d/eau-claire-peter-wright-anvil/6835523234.html
Its not a bad price for the condition. The seller doesn’t take any pictures of the markings so whether it really in a Peter Wright or not is a question you would want to answer. You can however tell from some of the photos that the it does have a hardened steel face. My advise would be to take a close look in person.
Make friends with a large animal veterinarian. GF of mine who was in Vet school got to know all of the farriers in the state and put out the word I was looking for an anvil in October. She (and my friends) left me a very nice used Peter Wright under the Christmas tree (literally) that year for which they paid about $1/lb. Yes, I have great friends!
Getting it home on the airplane was another story altogether.
You really don’t need a flash anvil to start out with. Heck in the history of the blacksmith everything from rocks, meteors to tree stumps have been used.
If you have a grinder my advice would be to take a trip to the local scrap year, get a piece of railway, grind the top flat, cut and grind a horn on it and mount that to a heavy base (tree stump).
My first anvil was a 300mm diameter and 150mm thick chunk of scrap high grade steel. I cut and ground the surface, formed a bit of a horn and cut a tool hole in it (hardie hole). Served me well for about 3 years before I managed to get a good quality anvil.
Also when you get an anvil try and find an old one, New ones tend to be cast and although they are OK to work on a comparison between a forged anvil and a cast anvil becomes prety clear after you have been beating on it for a day.
A good old anvil will reflect the energy back in to your work where as a cheap cast anvil will just absorb the energy. (you can test this my gently bouncing a large ball bearing or hammer on the surface).
When you locate an older anvil go over the surface with a hammer and tap it all over the place. Some older anvils have a tool steel plate that has been forge welded on to the surface. You can sometimes hear a dead spot or a kind of hollow tink noise if the tool steel plate has not been welded correctly or if the anvil has been abused and the plate is coming away from the lower grade steel base.
Another thing that many people do not know is usually the anvil face has a slight curve in the surface, they are often not totally flat. This helps when drawing out stock. Many new anvils are however surface ground flat and dont have the same convex curve.
Thanks for that. I wrote the article but am no Anvil Guru, having primary experience with only my dad’s ones.
About the “Also when you get an anvil try and find an old one” This is not true in general. It should say “Do not get a cheap new anvil” . Here you really get what you pay for. Cheap modern stuff can be cast iron, and that is worse than useless, as described. New quality stuff is far and far superior to any old anvil. I own a 100 year old 104 kg one, the one in the picture, and a ~200 year old 250 kg one and have also used modern ones, and the steel quality is incomparable. Hardness, elasticity, wear resistance etc is vastly superior. You can not beat 200 year of metallurgical progress.
However, assume that a quality new anvil costs ~ 15 EU/kg, and you want at least a 100 to 150 kg one. For example angele.de sells top quality stuff, but you will pay. If you are starting out, do take the railroad track advice.
Yes, I should have stated “This part of the world” as down here the market is flooded with cheap Chinese cast anvils that are shocking quality. Getting a forged anvil or even a high quality cast one that has been heat treated is near on impossible.
I have a collection of about 5 anvils. still the best is one is the oldest one in my case. followed a close second by the hand forged mini anvil I have. Where i used to work we had a further 3 anvils.
Dam, 15 Euro’s / KG… !!! If only the shipping was not so expensive :) I looked in to getting some quality anvils made up down here at a cost of about $8.00NZ/kg thats about 5 Euros / KG. They were an SG Iron base with a tool steel top plate.
It’s really great to see this article here, I’m really looking forward to further articles in the series! It’s a huge pleasure to read something written by people who really love the craft!
Thank you! I’m by no means an 1337 blacksmith though, as I am at pains to say above.
I echo the attitude of gratitude for 1. Your dad sharing his love of the forge with you, and 2. You taking your time to help mold our cast iron brain cells and wanna learnisms with us.
This post got me thinking about the many unoriginal self-appointed experts we have expounding on the lint on their shoulder. Forget TED talks, ‘super’ conferences, symposiums, and all of that other mindless self-congratulatory drivel.
I want to see a monthly discussion board composed of Jenny List, Brian Benchoff, Paul Stoffregen (PJRC), Nathan Seidle, and Limor Fried. Do it. Everyone else (including me) needs to sit down and shut up.
[Benchoff because every group of reasonable people need a source for ‘different’ views]
Well thank you for putting me in such company.Not sure my brand of percussive maintenance would go the distance. :)
I second that, get Jerri Ellsworth and the guy from NileRed too.
Interesting to read on blacksmithing from your perspective. As you implied, there are “blacksmiths” and then people who like to blacksmith. I like to blacksmith(machinist by trade) and I am raising my daughters in the forge, with machining, with welding, etc.. I do not expect them to cling to these trades as I have, but I hope that I can normalize this group of skills in them for whatever path they may follow moving into the future. Do you feel that being raised around your fathers forge is responsible for the type of work ethic you have and how you process work related information?
WRT your question, I don’t think so. But it did give me an innate hardware hacker’s curiosity. There’s nothing it’s not possible to make if you grow up in a blacksmith’s forge!
WRT his question–I think so.
I attribute the letters after my name to the fact that my father was a bricklayer, master stonemason, and the only one in the guild who could lay, and was trusted to lay, a perfect serpentine wall…and that I was his ‘laborer’. There are far too many similar stories in my experiences in academia and research for your case to be an ‘outlier’, Jenny.
Ever hear the old story about the farmer at his son’s PhD graduation? —
Dad: “Son, if I’d known this is where you’d end up, I wouldn’t have worked you so hard on the farm all those years.”
Son: “Dad, if you hadn’t worked me so hard on the farm all those years, I wouldn’t have ended up here.”
Essential Craftsman just posted a how to video on a basic forge/hearth that doesn’t require much to build.
https://youtu.be/TS7wumQt0s8
That tuyere thing – will a leaf blower do the job?
I’ve never used one for the task so i don’t know. I suspect it would be too much air though, a forge is not a blast furnace. You need the equivalent of someone breathing continuously into the fire.
A leaf blower would be far too much. An airbed inflater can work.
On anything over-powered you can throttle the intake, as long as the device isn’t reliant on the airflow for cooling. (Vacuum cleaners often are)
A hairdryer is probably OK for a small forge, for a limited length of time.
I just remembered this article I wrote a while ago: How to build a forge from things you can buy on a Sunday afternoon:
http://bodgesoc.blogspot.com/2014/06/forge.html
In that respect, and interesting observation is to realize, how much metal (considering the different metals), can be melted, with the same energy that takes to vaporize 1 liter of water.
When he was a farmer my father used a modified “buffer stop” from the terminus of a train line. Weighed about 200 kg (440 lbs). Much later, for a “hearth” I used a freestanding cast iron bathroom sink with a vacuum cleaner blowing up the plughole, with charcoal fuel. The enamel would get sticky, but didn’t cause any problems.
I remember some really simple experiments many years ago – one of my setups involved old steel industrial computer case filled with fireclay bricks (probably from some thrown out the stove or similar). Using some wood waste (tree bark etc.) as fuel. Instead of an anvil, I only had a piece of rail attached to a wooden block. For tools I had an sledgehammer, some smaller normal hammers, old pliers and some hand made “tools”. Only tried few things with a pieces of concrete reinforcing iron bars / wire / nails.
Nothing I would now take seriously but in the teen age it had some sort of magic. I still have one of my “products” – rough looking (“medieval” or “viking”) knife which would be probably useless as working tool.
Now I definitely know that I am not going to be blacksmith but it still somehow fascinates me – maybe it has something to do with the riddle of steel :-)