Carburettors versus electronic fuel injection (EFI); automotive fans above a certain age will be well versed in the differences. While early EFI systems had their failings, the technology brought with it a new standard of reliability and control. By the early 1990s, the vast majority of vehicles were sold with EFI, and carburettors became a thing of the past.
The Mazda Miata was no exception. Shipping in 1989, it featured not only multiport fuel injection, but also a distributorless ignition system. Consisting of two coilpacks in a wasted spark configuration, with computer-controlled timing, the system was quite advanced for its time, especially for a budget sports car.
Despite the Miata’s technological credentials, those in the modified car scene tend to go their own way. A man by the name of Evan happened to be one such individual and decided to do just this — scrapping the EFI system and going with a retro carburetor setup. It was around this point that this I got involved, and mechanical tinkering ensued.
But why?
It’s true that the Miata’s stock EFI system is perfectly capable of doing its job, and is also capable of handling some mild engine modifications without too much trouble. Those building for higher power levels will usually replace the ECU, injectors and fuel pump in time, but the general architecture of the system is kept intact.
However, this is not to say that carburettors don’t have their merits. Due to the Miata’s engine layout, it’s possible to fit a set of twin carbs with the right manifold, and have a very short intake runner length. This has the benefit of both reducing intake restriction for more power, as well as greatly improving throttle response. Given the restrictions inherent in the standard intake and air flow meter, there are significant gains to be made here. Additionally, such a setup can increase induction noise considerably, which is a big plus point to those who enjoy the symphony of a naturally aspirated engine. Finally, having a unique build is a great way to score some solid attention at Cars and Coffee, even in the face of expensive Italian competition, and this can’t be discounted.
Alternatively, just refer to the title of this article!
But… This Engine Wasn’t Designed for a Carburettor
Obviously, fitting carburettors to a car never designed to have them takes some doing. It’s made all the more complex due to the Miata’s computer-controlled ignition system. This means that modifications to both the fuel and ignition systems are required in order to pull off the modification.
The work required has been documented by Norman Garrett, in the Mazda Miata Performance Handbook, from the era when print still reigned supreme (pages 79-82). The first step is to remove a whole bunch of hardware that is no longer required. The original intake manifold, intake piping and air flow meter are all removed, as they are not compatible with the carburettor install.
With that done, the carburettors can be mounted to the engine. This requires a special manifold designed specifically for the application. Mazdaspeed manufacture a suitable part for both the 1.6 and 1.8 litre Miata engines, which allow twin Weber carburetors to be fitted, and this is what our project used.
The fuel system in an EFI car usually runs at between 30 and 70 PSI, far above the 7 PSI required for the average carburettor. To solve this, a fuel pressure regulator must be fitted that is specifically designed for carburettor use. This can be installed in the engine bay near the carbs, as there’s plenty of space with the original intake hardware removed.
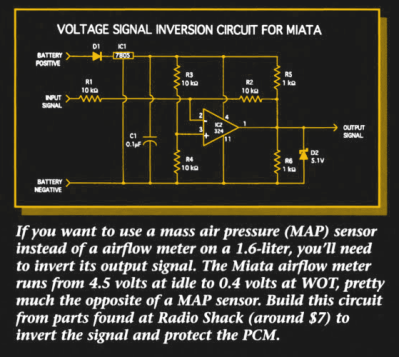
There’s also the matter of ignition. Timing advance is computer controlled, based on the signals from the cam angle sensor and the air flow meter, which give the ECU the ability to calculate the load on the engine. With the air flow meter deleted, it’s no longer possible for the ECU to know how much timing to run. This can be left as-is, but without a proper timing curve, the engine is giving up performance.
Normally this would be handled by a distributor. Due to the design of the Mazda B6 and BP engines, it’s not practical to switch to a classic distributor-based setup. Instead, there are two common methods used to spoof the air flow meter signal to the ECU, enabling it to properly control the timing. A throttle position sensor can be installed onto the throttle linkage of the carburettors, with the throttle position standing in for air flow as a load signal.
Alternatively, a manifold air pressure sensor can be installed, sensing the vacuum in the inlet port. This signal can then be inverted, similarly emulating the original air flow meter closely enough to serve as a good reference for engine load. Depending on your tastes, you may prefer the mechanical complexity of the throttle position sensor, or the electronic complexity of the MAP sensor route. This author favored the former, but the owner favored the latter, and thus we set about building an inverter circuit for the car.
Like any major engine modifications, there’s also a litany of additional tasks to be done to get things up and running. On this build, the throttle cable required modification, and the lack of vacuum available from the carburettor manifold meant the brake booster was no longer as effective. Like any big project, expect pitfalls along the way.
Electronic Pitfalls: Wrong Side of the Connector
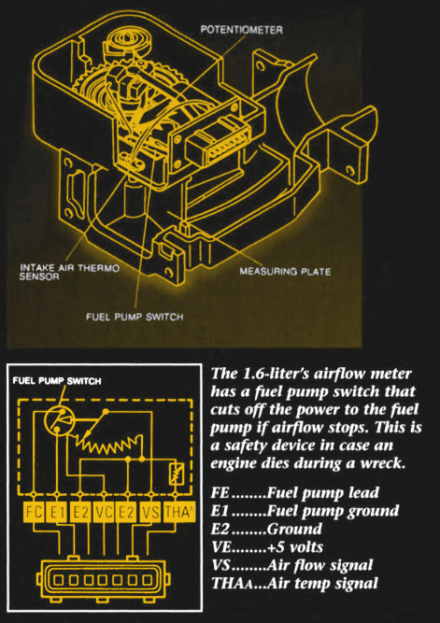
I was primarily involved in the electronic side of the build, whipping up an op-amp circuit to invert the MAP sensor signal, as designed by Norman Garrett. As per the schematic, this relies on an LM324 op-amp to do the work. Only a single op-amp of the four available is used, set up in an inverting configuration with a gain of 1; i.e. simple inversion, with no amplification. This is intended to be used with a common GM 3-bar map sensor, which is readily available either new or used, having been used in millions of cars worldwide.
After whipping up the circuit on some perfboard, we struggled to get things operating reliably. After trying to power the circuit from the 5 volt line in the air flow meter connector, we gave up and used a 7805 regulator with the Miata’s 12 V auxiliary feed in the engine bay. Unfortunately, despite this, we still had issues. The circuit was simply outputting either 0V or 5V all the time, rather than cleanly inverting the MAP signal.
With little idea of the root cause, the circuit was rebuilt with scrap parts, substituting an LF356 op-amp. This worked in limited bench testing, but again began to play up when connected to the car. As is the way, several hours of frustration ensued until it was realised that we’d read the diagrams backwards. As drawn in the Mazda Miata Performance Handbook, the AFM connector is shown from the side of the air flow meter itself, not the wiring loom in the car. With this oversight rectified, we were able to get the circuit running, and the signals inverting nicely. Without a dyno or any high-end diagnostics available on the Miata ECU, it was difficult to determine how much of an effect the circuit has, but we proceeded to take the car out for a test drive.
Performance: Your Foot Makes the Engine Soar
In short, driving a carby Miata is an absolute hoot, above and beyond the stock model. There’s a touch more power on tap, of course. But above all else, the snap of the throttle is intoxicating, with the engine surging ahead with the slightest twitch of the pedal. Induction noise is also gleefully present, and combined with a good exhaust system, the raspy bark is to die for.
Obviously, there are also some notable drawbacks to the setup. It’s unlikely to pass emissions rules in jurisdictions where that matters, and cold start performance would be diminished in areas where frost and snow are a regular occurrence. There was also the issue of a small flat spot in the powerband around 4000 rpm. Without the time to conduct proper A/B testing, we were unable to track down a definite culprit. Suspicions lay around the carburettor intake setup sacrificing mid-range torque for top end power, or the op-amp substitution causing issues as the LF356 is not a rail-to-rail part like the LM324.
Regardless of the tradeoffs, the final product was a dream to drive, and had the underhood looks and soundtrack to match. For those daily driving, it might not be the best choice, but for the weekenders who want to impress at the local car shows with some old school charm, it’s a heck of a way to go.
That’s awesome! Dual webbers always look nice too.
A carbed 740 was one of the first cars I owned. In Europe they were pretty common. They came from the factory like this.
Carbs are crude way to try control fuel/air ratio for all load, all weather, all altitude, all rpm conditions. This was an exercise in retrogression that only a Luddite would favor. About the only place a carb will work as well as a high performance FI system is in drag racing where the carb is run wide open. Even then the accomplished tuner changes jets and carb tuning to meet current environment conditions for maximum performance. The author would have been better served by creating a four short runner injection setup with a wide band O2 sensor to control A/F under all conditions. Much like used on modern hi performance motorcycles. This wasn’t a hack…real hacks return benefit.
Shhh, let people enjoy things.
“This wasn’t a hack…real hacks return benefit.”
Sometimes the “benefit” is…
I’m no longer stranded.
Also throttle response + old men thinking you’re cool
Not to mention the sound of a pair of double Webers at full throttle. Oh joy !!! :-)
nothing wrong with Luddites, there is much worse to fear from techno loving masses that are sponsoring the Elites plans for a smart grid, surveillance capitalist dystopian prison. Indoctrinated fools are all addicted to technology that is mainly useless in most cases. Analog all the way.
Yeah, well sometimes crude and reliably functional in nearly all conditions is far better than efficient across most conditions. Why do you think full mechanical air start diesel engines are still in use today?
Benefit is a condition dependent, relative term. Also, sometimes its just fun to do something the old fashion way.
Ditching a flap airflow meter is a good step on any car – they’re usually horribly restrictive.
And twin carbs are worth it just for the noise and smell :-)
Now throw a carb in the 740 in the background of the video’s thumbnail!
Or a mustang V8, as many have done to the 240s & 740s
I love the engine noise of some old muscle when the secondaries open up. Thanks for bringing this the carb experience to something more modern!
What’s up with the weird blur around the photo?
Looks like an attempt at “tiltshift” to make the car look like a toy.
I’d be more impressed if they enhanced the fuel injection… I converted an S10 Blazer /from/ carb to fuel injection and it never gave me a lick of trouble. Cleaning carb jets is a problem I leave for weed whackers, lawn mowers, and offroad motorcycles. Upgrading the EFI would have likely brought increased performance gains and retained more environmental friendliness, that carby “smell” is inefficiency. I’ll pass.
I’m guessing that if he just modded the EFI, he wouldn’t have ended up on HaD. I’d even bet there’s a step-by-step for that very process that’s just a Google search away.
I’m sure he learned learned a great deal more than just futzing around with fuel injectors, timing and ignition, how-to guide or not. Learning isn’t always efficient – I’ve wasted plenty of brand new material in my many quests to make things I could have just as easily bought. The result is a base of knowledge that allows me to now use items normally destined for the landfill to make the things I would be forced to buy new if I hadn’t learned anything. Perhaps his next project he can apply what knowledge he has gained here to make something more efficient. Maybe not.
Regarding fuel efficiency – maybe you could convert your lawn implements over to EFI – That might land you a front page on HaD /and/ you’d learn a ton!
As for the blur effect: Hrmph.
Artistic effect
ITB’s and a programmable ecu would have been better.
carbs are restrictive as well
I personally think that any time a computer can be ripped out of a car it’s a win.
You could could say a carb is just a crappy mechanical computer…
Carburetor is just French for ‘Leave it alone’. :)
The austin a series wants to speak to you. Although it’s still in counselling about what happened to it at the end of the 90s
The a-series was an oddball, being a Siamese port motor that somehow survived into the era of catalytic converters and fuel injection, the fuel injection of the time simply not being up to the dynamic demands of the engine.. Im going to assume your already up to speed on the problems or you wouldn’t have posted, but if not check out turbominis.co.uk . plenty of very smart people working on the Siamese issues. me, personally, I seen sense and went to the k-series.
I’m glad you brought this up! To put a carburetor in something because you want to is fine. But to create an imaginary list of benefits over EFI? Come on… On a side note, please do something so those carbs suck in something other than hot engine bay air
More pointedly, a carb relies on a restriction for its very function: you have to restrict the airflow to get the pressure drop that sucks the fuel in. Replacing a flap-type airflow meter with a resistive element, or using a throttle position sensor, both manage to acquire flow rate data with less restriction.
And, presumably the people who did this and some of the people reading this already know this, but: intake runner length reflects engine usage. Mazda correctly predicted 99% of the Miata usage would be people puttering about slowly in traffic, where a long, somewhat narrow intake runner gives the engine better performance. People racing them, at high RPM’s, need short wide intake runners like the carbs (or, even better, ITB’s) would provide. Short intake runners aren’t universally better.
Dodge mad these very long runner intake manifolds for a short time in the 1960’s, for NASCAR. They set dual 4bbl carbs out next to the fenders. https://www.bigblockmopar.nl/2010/08/long-ram-intake-manifolds/
They ran the pants off the competition on the track but were horrible for street use due to the huge throttle lag. But back then NASCAR still had some rules about having to sell essentially the same engines in street cars, so a lucky(?) few got to own those slugs. They were great at the drag strip where launches were done at high RPM to keep the fuel flowing. But at idle the fuel could precipitate out and puddle in the runners.
NASCAR ended this long ram intake and the much more practical cross ram intake with a rules change limiting engines to a single carb.
No long-ram engine was ever run at Nascar. Do some more reading on the subject.
These long ram intakes were actually designed by Chrysler for street-use in their “Letter cars” (1960 Chrysler 300-F to the 1964 300-K models) and some Dodge/Plymouth fullsize cars, to give the engine about 10% more torque at the range of 2800rpm as a luxury, so the driver didn’t have to downshift to overtake another car.
In 1963 and 1964, a (internally) shorter ‘Long ram’ intake was offered to increase rpm range at which they offered a benefit.
After that, no more long ram intakes were offered on the Chrysler models and a “one-piece” crossram/shortram-intake was made for use on the 426 Hemi and Max Wedge engines.
All petrol/gasoline cars rely on a restriction of airflow. Otherwise you’d always be running to lean except for when you’re at full throttle. That’s also what makes diesels more efficient, they don’t need such a restriction cuz there’s no such thing as “too lean” on a diesel (unless you’re trying to make power).
>” a long, somewhat narrow intake runner gives the engine better performance”
Why?
The length of the intake runner determines its resonant frequency. Choose it properly, and over a narrow RPM range the input charge can actually exceed atmospheric pressure. Runner cross section area can be optimized: too big and the effects of resonance are weaker, too small and flow is restricted.
Very much this! Airflow into an engine is pulsed, the valves opening and slamming closed create pressure waves in the flow. By altering the length of the runner it is possible to cause the valve to open in time with the high pressure portion of the wave causing more air to be delivered into the cylinder. Only works at that particular RPM and it’s resonant frequencies, but it can cause an appreciable difference. Manufacturers often use this trick to smooth out the power band, some have gone as far as designing switching intake runners to vary the length at different RPMs.
Daniel Bernoulli would like a word with you.
Anyone interested in this type of modification should check out grind hard plumbing co on youtube. Their gambler car this year was a V12 jag that was having issues with its factory fuel injection, but the ignition was fine. They kept the factory ignition and built a custom intake to fit a carb. They also had a cracked piston sleeve and I believe a bad valve, so to make it to the race they removed the valve and piston and ran the car as a V11.
Those guys do a lot of awesome projects. Lots of fun to watch them hoon about with their project vehicles.
I would not use a “3” series part in anything automotive. That is what the 1 and 2 series parts are for.
I don’t think many people who have not worked with automotive, industrial or military designs really understand the difference.
(for those scratching their heads right not, the difference is mostly in operating temperature range)
Thats a lot of money and effort for an increase in throttle response
For some people that’s the fun part. Especially people around here.
I know I get it, I just did so much of this in my youth and I’m forever disinclined to modify vehicles anymore.
Instead of burning out on it and becoming a boring adult, I instead learned how to stupid things the smart and efficient way.
Terrible idea. The loss of fuel economy, consistent power and disgusting emissions is not a plus. Why not convert the whole thing to four-wheel drums …
Sort out the jets and tune the carbs + add a intake air heat shield, and you wouldn’t give a flying ‘explicit’ about anything else when you floor it and let those webers sing.
I’m not that selfish. I’m not a redneck that likes to screw up my sensors on a diesel pickup so everytime I floor it I have no power but I have a ton of smoke… Not my bag.
Fine. When I’m ready to swap in a newer engine into my 1969-built project car, you can come on down and install and wire the in-tank pump, the fuel return line, all the engine compartment harnesses and mount the computer for me. No? Then shove it and go away.
Interesting, but there’s some bad information in this article, and some things that suggest that they don’t really understand the weber carburetors:
1) These type of webers like a MAX fuel pressure of around 3-4PSI. 7.5 PSI will almost always cause fuel to be pushed past the float needles.
2) A flat spot around 4K sounds a lot like they have the wrong Air-Correction jets installed, or a lower likelyhood of needing a different emulsion tube.
3) Why go to all the effort of inverting the MAP line, etc instead of installing a megajolt ignition controller and completely removing the stock ECU from the equation?
Third could be because they’d wanna avoid the spaghetti of leaving old wiring in place in case of wanting the ability to go back, while also introducing a rats nest for the new ignition system.
Oh, and signals to the gauge cluster might come from the ECU.
Cars with DCOE45’s (my 61 Sprite) or DCOE32’s (1969 Alfa 1750) or DCNF32’s (4 on my Ferrari 308GT4) have been cold starting for decades. That is what the choke is for, including sub zero C. I think if this guy spent a weekend with a box of jets he would get much better performance. From the starting acceleration it seems not enough on the accelerator jets/pump. Takes a lot of time to dial in a DCOE for a new application but once done they are stellar. Sound is second to none as well. They stay in tune & the jets don’t need cleaning unless you let the fuel dry up inside them.
I’m reminded of a cold spell back in the 1990’s at a time when there were about as many carbureted cars as there were fuel injected. Very few of the people with carbs could make it in to work on time until the cold snap broke three weeks later, as their cars wouldn’t start unless they were kept in a warm garage. There were dead cars everywhere until things started warming back up a bit. (I’m in northern New England, so extreme cold is not unusual mid-winter)
Carbs may work in sub-zero temps, but getting them started can be a huge pain.
Had never a problem with a car in cold conditions. Only my ZZR500 motorcycle did not like cold weather even above 0°C. The older Z500 was ok. Only driving a motorbike at -10°C is no fun. Now the car and the bike has EFI – and a place in the garage.
Driving a Miata is like using a toilet without a toilet seat, instead you put some paper on the ceramic rim. It’s fun, exciting and never gets old.
Back in the early ’80s I mounted a pair of Dellortos (almost identical in appearance to the Webers) on a modified VW engine. The results were fantastic from a driving and power aspect, but there were no chokes, like the above conversion. It gets cold around here, the teens pretty much every year and 20 below on occasions. I found that by careful pumping of the throttle, I could get it to start and warm up as low as about +20 (for younger people, carbs have “accelerator” pumps which are used to provide extra fuel when the throttle is opened so rapidly that the fuel through the regular circuits can’t keep up, this prevents a stumble, and let me enrichen the air/fuel mixture on starting) Below +20, I needed a squirt of starting fluid into the air filters to get it to fire, then gentle pumping of the throttle until the engine was warm enough to drive. A little hassle, but totally worth it. While I was driving this car, we had a week of temperatures in the 20 below region, a few mornings -21/-22. No one thought I’d make it to work or school, but I did every day, some of the totally stock cars my friends drove were totally out of commision that week. So was our service van at work. For those who are concerned about cylinder/piston/ring wear from the starter fluid and pumping, I drove the car many miles a year for years, and it was running fine when I sold it. Big mistake selling it.
+20° is not “low” but about room temperature. If your car had a problem at that temperature I would suspect a serious issue. Or was your car tuned for tropical climate?
20 degrees Fahrenheit. – 6.7 Celsius Cold for carbs with no chokes.
Nothing, but nothing, looks better on an engine than a set of Webbers, the more the better, with velocity stacks sticking up from the engine. Working on a project at the moment that will take 4 of them…The linkage is such a nightmare I’m considering doing it with 4 servos! ;)
Komrade, get yourself some SUs. Big shiny domes all the way.
I’ll keep my Flyin’ Miata turbo, thanks. 265 HP at the wheels, no tom foolery with non-automotive spec pixie wrangling.
I’ve done some work on and driven my friends FMII equipped Miata hard numerous times. It’s custom tuned on a Megasquirt to 305 HP at the wheels (on forged internals). It’s amazingly fun on-boost, but the fun doesn’t really start til after 4000 RPM. Personally, I would have went with a smaller turbo (I believe he went with the GT3071R), it’s really too much power and not enough response for a street driven Miata. The powerband is much more suited to drag racing.
Oddly enough, he’s considering going back to natural aspiration. With ITB’s, he’s witnessed me cussing out the Mikuni’s on my old Suzuki enough times to go with carbs!
A bit of software fiddling would have gotten better performance and maintained reliability. Also, the engine needs cold air, not under-hood air.
What’s next? The pros and cons of draw-through & Blow-through turbocharged carburetor setups
;)
Since he already spent 3x the cost of a megasquirt on the carbs AMD mani, im.sure he will be doing blow thru.
I put some ITB’s on my car with fuelinjection, but without airflow sensor or map. Just runing Alpha-N on a Megasquirt. The problem is that converting a car to carbs will fail thw MOT in the Netherlands.
I don’t know about Mazdas but on Subarus the output from the MAF is non-linear where as the output from the MAP is linear. The ECU uses a lookup table to convert the non-linear MAF signal to a linear one. If you’re just inverting the MAP signal this could explain why things are a bit off in the middle of the rev range as that would be where the fake signal varies from the real one the most.
Ah, sounds like a excuse to dabble with a MCU that’s gotten a fast & high res DAC and ADC.
But I’m pretty sure that the early “flap” based MAF sensors like on first gen Miatas are linear, since the arm of the flap goes to what’s essentially a big ol’ potentiometer + some support circuitry and possibly a intake air temperature NTC.
It sounds like it’s quite different to the MAFs I’m used to. The Subaru ones are hot film/wire based, I think those types are usually (possibly always) non-linear.
One way to possibly figure it out without breaking out any hardware would be to check sites that cover remapping the ECU in that model. They will most likely have information about MAF scaling for increased airflow.
Technically its not a MAF as it measures volume nor mass but yes its quite non-linear. At the same time a 3-bar sensor has been used to mess the scaling completely, not to mention the fact that a MAP uses a completely different algorithm to the AFM.
All arguments about Carbs/EFI and pixie wrangling aside, I’d have put a damping chamber in the vacuum line (a small bit of pipe with a barbed fitting at each end and a restriction on the sensor side – think of a cored out fuel filter – would probably do it) to damp out that high frequency fluctuation in the sensor. The capacitor-based version that evens the signal out is a neat fix, but not having that sensor fluctuating in the first place might be a good idea.
I’ve seen examples of industrial machines where they fitted “oldschool” inline fuel filters to the pressure sensing lines in order to dampen oscillations of air pressure.
No modifications or anything to the filters, just plopped them in.
The ole’ pixie wrangling routine. I see you’re a man of culture as well. Keep your…!
Yeah nice build and all that, but – the driving wheel is still on the wrong side of the car. I would have fixed this issue first.
It’s okay – they’re in the Southern Hemisphere. It cancels out.
might be able to get the same benefits using 4 independent fuel injected motorcycle throttle bodies. all the airflow volume and better mixing but without the mechanical issues and inability to adapt to changes in weather or atmospheric pressure. Somewhere there’s a guy who did this with an older Honda, a MicroSquirt open source fuel controller, 4 motorcycle throttle bodies and spun aluminum velocity stacks sticking out of the hood old school style
That’s cool and all… but WTF is up with grandma walking backwards around the corner at 4:44 in the video!?
EDIT: 4:54… and 0:05
I was hoping they meant carbines when they said carbs. Having turrets on each side, the front and the back would be pretty cool but better done with a vehicle that is more intimidating. :-)
That’d probably have to be a US based build, but why haven’t we seen more Miata technicals?
This project just goes to show that sometimes optimizing doesn’t mean what we think it means. It’s optimized for its purpose, not for absolute efficiency. Well done overall :-)
It might not be the most powerful or efficient build as you say, but it’s a heck of a good time. Some people fail to see that, but it’s clear that the true car fans get it! Cheers ;D
Are they installing a vinyl turntable on the dash as well? You know, “better sound” and all…
Neat reading into. I’ve been working on Briggs and Stratton Engines along with their Lawn Mower/Tractor in my latest projects.
For some reason I invested in the “L-Head Opposing Twin” design later to find I didn’t need the engine (sheered flywheel key on the engine I was going to swap with that is a OHV 287707) and read that the 18HP 42#### version was used in Briggs and Stratton’s only hybrid vehicle design.
https://blog.consumerguide.com/briggs-stratton-hybird/
That inspired me when I picked up a $50 Murray Lawn Chief with one of the 694cc 18HP’s to invest in another 18HP 461707 parts engine to add to the 15.5HP 402707 first one. Thinking I’ll use the 15.5HP for parts, polish the heads and most likely make one of the 18HP’s into a higher performance EFI EMS’ed design with the 15.5HP heads. Thinking will do like the little 3.5-5HP racing mods and have to custom machine parts also.
Also, I have this vision of using the motor and CVT from a salvage yard Prius to drive the system. Ideally with wheel hub motors/generators… though thinking for the prototype system to leave the mechanical guts in at first… otherwise don’t really need the CVT.
Not sure what the best design wheel hub motors/generators are, any ideas?
This is neat reading into also… as studying the signals in car engine and in general is getting addicting. Seems the future is going to be human body sensors for diagnostics, boundary sensors and perimeter sensors for health and safety risks. I’m sure this will be the future. Like I noted Faraday Cage Anechoic Chamber Room or House options for Residential Home Owners builds… same is going to happen for the vehicles.
Its Weber, with one “b”!
A Megajolt crank fired ignition system is the perfect compliment to this system! https://wiki.autosportlabs.com/MegaJolt_Lite_Jr.
Great idea!
Wet blanket, much? The thrill of the chase alone is enough justification for what they did. Throw in a learning experience, throttle snap, induction noise, and bragging rights, and you have a full-blown hack. Any claims to the contrary are churlish and curmudgeonly!
always use a visibly distinct index pin in your designs people
Please!
Great execution, Lewin Sorry about not being clear in my book about the air flow meter diagram, kudos to you for figuring it out. You are correct: There are few things more satisfying than the throttle response of a single-throat-per-cylinder carb set up. Thanks to the longer time (relatively) for the fuel to evaporate, carbs like your setup have very crisp tip-in throttle response, particularly on four valve heads with smaller ports (and higher port velocities). Nice work.
Hi Norman,
Wow! Thanks for reaching out. We had great fun with the build and driving the car when finished. Your book is an excellent resource, really was great, even if I did misread the diagram initially. Hope you’re well!
– Lewin
Norman and Lewin! It is an honor to able to reach out to you guys. I am simply melting over this Frankenstein project. My thought on the ignition problem is this: why not make the timing totally manual? Like on a stock Ford Model A? Retard the spark when startin and goin uphill, advance it goin downhill. That’s all you gotta remember. I’ve driven those too. Model As can also be converted to 12 volt and still have the manual spark advance set up. A Model A distributer could be used. I would imagine the firing order would be different, but that’s nothing that switching this wire with that one won’t fix. Reproductions are still being made. Just a thought
That would be very old school! Unfortunately not really practical as the B6 AND B8 engines do not have provision for a distributor at all. If they did, no timing mod would be needed – any old 70s sprung distributor could be fitted with a fixed timing curve.
May be the timing could be controlled electronically (yet still manually) through some kind of variable capacitor, like a repurposed volume knob on the dashboard, or something of that nature.
It would be more straightforward to use the stock ECU and coil packs to drive the secondary spark, and trick it using the methods mentioned above. Ignition timing maps are pretty particular for peak performance. Manually swinging the timing is great for a farm tractor (or a Model A), but not really viable for a modern road car. You could even get the engine to run with a fixed timing of 14° at all RPM if you wanted to, but power would be down over 2500 RPM. Getting an engine to run is easy, making peak power is a challenge. If you wanted to go truly “old school”, you could drive an old-timey distributor with a toothed belt off of a crank pulley. However, the best stand alone system would be a Ford EDIS system from any Pull A Part for pennies on the dollar. See for more information.
Oh yeah, I see what you mean.
Lewin,
My youngest son has become inspired to put 45DCOE’s on his ’95 1.8L Miata, so we’re dusting off the inversion circuit and having a go with a 3D printed manifold I’m working up. You mention that you added a capacitor to the circuit to dampen the output. Can you elaborate (your dialogue “nice little 68 puff cap” doesn’t translate to my knowledge database for capacitor specs)? I’d like to try out this improvement to my circuit.
Cheers
-Norman
Hi Norman,
68 picofarads, “puff” is slang :)
A little ceramic, I think I put it across the feedback loop of the opamp.
Hope it goes well!
It was a 68 picofarad ceramic, puff is slang for picofarad around here! I think it was across the feedback loop, let me know how it goes!
Thanks, Lewin. I’ll keep you posted…
Old post, but I just saw this, and wanted to ask why a 3 bar MAP was used? Since the pressure will never get above 1 bar (roughly, atmospheric), it would only output 1.83V max (assuming .5-4.5V output). If the AFM outputs .4-4.5V, the MAP setup only uses a fraction of the “apparent airflow,” which would put the ECU into a lighter load map and increase the timing accordingly. That could account for the increase in power, but also puts the engine at more risk of knock. Am I missing something? As far as junkyard parts go, you’ll have a lot easier time finding 1 bar sensors before you find 3 bars.
SpeedAddict: You are correct – the normal 1 bar GM MAP sensor is the one to use. I don’t specify which one by part number in my book. I think Lewin has such a master of electronics (he owns an oscilloscope, after all) that he used a 3 bar MAP sensor he had laying around and was able to make it work. His idea to add a capacitor to smooth out the response is a good idea.
My son and I are starting a Weber conversion for his ’95 Miata 1.8, so if we learn anything new, we’ll post it on here.
Love Webbers and what you did with the car. In the article you mention using a VTPS to mimic the signal of the AFM ?
Is the AFM signal increasing with air flow or decreasing ?
I’d like to ditch my AFM using the above.
I can not stand electronics in any way shape or form! I also have a set of mikuni carbs for my NA 1.6 and I’m facing the problem of the air flow meter signal. Fancy making me an inverted map because I’m bound to feck it up if I try and make one!