COVID-19 can seem like a paper tiger, when looking at bare mortality rates. The far greater problem is the increase in fatalities as health systems are stretched to the limit. With thousands of patients presenting all at once, hospitals quickly run out of beds and resources and suddenly, normally survivable conditions become life threatening. One Italian hospital found themselves in such a position, running out of valves for a critical respirator device needed to save their patients. Supplies were running out – but additive manufacturing was able to save the day.
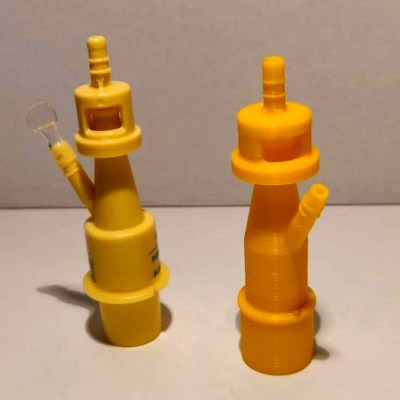
While the article uses the term “reanimation device”, it’s clear we’re talking about respirators here, necessary to keep patients alive during respiratory distress. The valve in question is a plastic part, one which likely needs to be changed over when the device is used with each individual patient to provide a sterile flow of air. After the alarm was raised by Nunzia Vallini, a local journalist, a ring around of the 3D printing community led to a machine being sent down to the hospital and the parts being reproduced. Once proven to work, things were stepped up, with another company stepping in to produce the parts in quantity with a high-quality laser fusion printer.
It’s a great example of 3D printers being used to produce actual useful parts, and of the community coming together to do vital lifesaving work. We’ve seen the technology come in clutch in the medical field before, too. Stay safe out there, and live to hack another day.
Thanks to [Jarno Burger], [LuigiBrotha], and [Michael Hartmann] for the tips!
Can someone explain a bit more the context? is it sigle use? does it need autoclaving?
I don’t think would survive autoclaving, mosly only a low pressure decontamination chamber.
I think the situation it’s desperate enough that “It will last as much as it last” and “It’s better then nothing”
Yes, this is single use, because it has contact with exhaled and inhaled air, so each patient needs his own to prevent cross-contamination. And it doesn’t matter that both have the same virus, this is to prevent contamination with something you didn’t find or isn’t a danger for one patient but might be a danger for other patient. You don’t really want any complications when patient already has breathing problems.
Couldn’t you simply soak it in isopropol overnight instead of throwing it away?
As a former ICU Nurse and Prof. of Nursing, I don’t know the answer to your question. Given the toxicity of Isopropyl alcohol coupled with the possible absorption of the alcohol and release to the inhaled atmosphere to one of the most transmissive tissues, I’d be very hesitant to try that unless there were no alternative.
Is there not other way to sterilize plastic part, like heat (enough to sterilize but not the melt/deform the part) that could be used when you running low on parts?
From this link https://ehs.princeton.edu/book/export/html/380:
121° C Autoclave Cycles
To be effective, the autoclave must reach and maintain a temperature of 121° C for at least 30 minutes by using saturated steam under at least 15 psi of pressure.
My knowledge of plastics is limited to the 3D printing, but the ABS I’ve worked with has a lower glass transition point.
Also from the above link:
Plastic
Polypropylene is an inexpensive resin that can resist autoclave temperatures. Polypropylene containers are often used as secondary containers to hold materials that are autoclaved. Polycarbonate can also withstand high temperatures. Polystyrene (PS), polyvinyl chloride (PVC), nylon, acrylic, low-density polyethylene (LDPE), and high-density polyethylene (HDPE) lab ware and polyurethane tubing are not autoclavable under any conditions.
Yes, there are other ways to sterilize physical items. Ultraviolet light is one way. You can’t look at it – danger . This is used every day (actually best during the night when no one is there) to sterilize hoods in labs handling microbes. The light would have to hit all the surfaces for a minimum amount of time.
Or, you could reprint 30 more of the things so there would be enough.
Due to sterilization issues, lots of medical equipment is single use only. In this case set the 3D printer to make 30 of these valves at a shot and just swap the clean ones in and burn the old ones.
No that’s not enough. But would also damage the plantain I imagine.
This isn’t an issue so long as we have filament.
Sterilisation; sorry this is a little late. Today I put a fragile 3D printed battery-caddie made of PLA in my pressure cooker and cooked it for 15 minutes. It came out unharmed, unaltered and sterile. Pressure cookers are used in medical facilities where there are no autoclaves. The temperature of the steam inside the cooker is 121ºC.
See theis link: https://www.ncbi.nlm.nih.gov/pubmed/12267939
Hope the .stl file are free . Some link for the file .
they said that stl will no be distributed, beacause is only for this emergency case and in other cases will break the license. italian recap article: https://help3d.it/valvole-stampate-in-3d-a-brescia-facciamo-chiarezza/
Yeah I’m sure those in need can get it. But distributing freely online doesn’t make sense.
Get the right designers and engineers involved and we’ll have an optimized version of this in no time. Already working on it.
please put it on web some stl. site that everybody can download it for free, it is stupid not to be free!
It’s a patented design so if it were free the company that designed it would not make any money
Plastic items like this in medical settings are almost always single use. (If it’s multi-use it’s usually made out of stainless steel). I suspect that this will be sterilized by just soaking it in a sterilisation fluid for while. If it’s printed in a clean environment it’s likely already sterile straight off the printer (the filament and the hotend it comes out of are all well above the temperatures needed to sterilise it. So if the printbed itself is kept clean and sterilised, and the printer is in a flow hood with filtered sterile air, it might not even need sterilising)
It certainly makes sense why these items are for one time use. Hospitals sure do have a lot of stuff like that though. It would be nice, some time that is not during a crisis if that were looked into. Rather than throwing it all away it would be good to have a process for recycling those plastic items, something which sterilizes during the process. Or maybe hospitals are a place where composting PLA would be practical.
In every hospital room I have seen it all goes in the same trash can and no doubt from there to a landfill. That’s an awful lot of petroleum wasted!
They won’t because of liability reasons. No hospital would ever allow reuse of disposable parts in another patient.
And since the parts have come in contact with human body fluids – they go to a incinerator. They do not go to a your neighborhood landfill.
Dialysers are reused after flushing them with acid.
I once got a chemical burn from the acid after carrying canisters with that stuff.
Who would expect that these canisters have a ventilation hole in the cap…
Yes, but there are various bits that get tossed after every use. Not just the tubing to the person. It was shocking the amount of “waste” each session generated, and I was only doing it for ten weeks, three times a week. Some people get dialysis for years, ending when they get a kidney transplant, or die.
I didn’t say anything about reusing a part in/with another patient. I was commenting on the resources that are wasted by “throwing away” all that plastic. It doesn’t really matter if they incinerate it or landfill it.
I was imagining it getting melted down and then turned into… anything. Would that necessarily be enough to sterilize it? And I only mean so that it is safe to re-use for some purpose. I didn’t expect it to become new medical equipment again.
Or could it become fuel? Could it be broken down into something compatible with gasoline or diesel? Would that process also kill any germs? Then again, going down that train of thought maybe the incinerator could also boil water for power generation. Maybe it already does, I don’t know.
Resin parts are a better candidate than thermally deposited parts for surviving boiling. But do we still have a porosity issue?
Once used these items are considered bio-hazards and are disposed off as medical waste. While SOME items in a hospital might be recyclable safely, it’s generally better to avoid all risk of cross contamination and dispose of all of in a matter that ensures it poses no further danger. The overall amount of resources used for medical applications is very small compared to other uses which makes it not quite worth the risk.
PLA can be recycled pretty easily.
Note that filament and hotends are not involved here. This uses a powder filled bed, and a laser passes the surface curing the resin, the remainder removed, the bed lowered, and next layer made. There is little to no endothermic heat worth mentioning.
They also say “and a custom polyamide-based material”, although no further details.
I would presume being more fit for this purpose, where withstanding high sterilization temps might be one of those attributes. Can’t say for sure.
Since the things are being printed en-mass and sent to the hospital, they are no doubt going to be sterilized if only because you can’t make assumptions in their handling.
The on-site printer mentioned was only for the person designing and testing the part to verify it works. Not being hooked up to a human wouldn’t need sterilization, think of it more as a fitting test. After that they sent the design file to a larger print shop
This seems like the type of item the hacking community can look into making for local hospitals. Can someone share the CAD files for this?
There might be legal consequences for distributing them as these things are covered by patents. They might be able to get away in Italy in a state of emergency because the suppliers could not supply it. Big Pharma value money over lives and they are more than happy to sue people.
There is most likely no utility patent on this valve design. I see nothing novel about it from the photos provided. As for a design patent on the valve design that is possible, but improbable. To avoid the possibility of infringing a design patent, simply print a few more decorative rings along with any other design changes.
The way that the medical device manufacturer protects this disposable form copies is not through patent IP, but most likely through regulatory IP whereby the governing medical bodies require certified components for medical use.
In summary — I call BULL-S on “patent infringement” as the reason why the valve CAD has not been shared…
The design patent wouldn’t cover it. A close look at the image shows every part of the valve is a different shape and/or size other than where it connects to other things.
That’s how many aftermarket auto parts companies make “work alike” components while the originals are under patent. A design patent is good protection only when the entire physical shape of the item is essential to its function.
LEGO files design patents on all their pieces, but the dimensions of the studs and the areas of the blocks into which they plug, along with the overall lengths. widths, and heights have long passed the point of being patented.
For this valve it looks like it connects to one large and two small hoses. Can’t patent the diameter of a tube or hole.
I think it’s appropriate to rename the article to “Hacking where it matters most” :)
Dear Hackaday: please let’s have more stuff about coronavirus, especially anything practical.
Also, do an article about the folding@home coronavirus effort:
https://foldingathome.org/2020/03/15/coronavirus-what-were-doing-and-how-you-can-help-in-simple-terms/
Agreed but keep in mind the community here HaD and that most of us don’t rely on just HaD for news
we read other things. Bring things like this article.
Actually let’s have less. Some of us need a break from the hysteria.
“hysteria” has a lot to do with perspective. If you lived where I live you would see it less as hysteria and more of a real crisis.
No matter how much real crisis you’ve got, I’m sure you could use less hysteria.
I do wonder if off-gassing could possibly pose a health risk. That being said, if the alternative is NOT getting any treatment, this is most likely the better option.
MIT had a design for a $100 respirator but it seems it never materialized as a product even for emergency cases. Now would be a good time…
http://news.mit.edu/2019/umbulizer-sloan-health-care-innovation-prize-0225
It looks like it’s in clinical trials that won’t end until the end of this year. This might be a situation where it could be accelerated?
https://clinicaltrials.gov/ct2/show/NCT04030208
Thanks for digging that up…
This seems to be one of the scenarios where testing should be skipped because a lot of research and testing has already gone into it.
If the options are:
A) Provide no respirator (And we know what the most likely outcome is)
B) Provide an experimental device (how much worse can the outcome be)
Option B seems to be preferable by a wide margin…
Parts cost is $500, but still much cheaper. Sounds like they’ve been selling in Pakistan. https://www.youtube.com/watch?v=if0Oe2xrSPU
Here’s an even cheaper ventilator – https://news.rice.edu/2019/05/01/student-invention-gives-patients-the-breath-of-life/
Not wanting to knock it but the price tag was $2000? Did they publish the design?
So where’s the patent for the valve? From that and the pictures they provided it may be possible to reverse engineer the valve and produce CAD files for it.
I think I found it: https://patents.google.com/patent/EP1852137B1
It appears to be a venturi flow meter of some sort rather than a valve.
Tank you
Yes, almost all plastic devices in the hospital setting are one-time use “disposables” due to the difficulty they would present for sterilization. Also, in many cases the cost of cleaning and sterilizing would exceed the part cost. So, there is an economic incentive beyond the risks of infecting the next patient if improperly cleaned/sterilized.
My question: Everyone I’ve seen is injection molded, why opt for a far slower production mode? This, and similar mass produced items, would seem to be a candidate for a stepped-up production versus a 3D printed copy?
Just a thought…
Not everyone has this piece of equipment on hand. The respirators were taken out of circulation, the lack of valve was why. Now they have the valve, and a means of reproducing them quickly and distributing them quickly. It’s not a case of get the optimal part, it’s a case of catastrophic failure if they do not have one.
Injection moulding is quicker for mass production, but takes ages to set it up and needs spending on some ultra-specialised VERY expensive molds to set it up. 3D printing is much slower and more expensive PER PART but trivial and cheap to set up. For small volume production or emergencies when you can’t get at an injection molder then 3d printing will do.
True, and I hope that’s what the manufacturers of these parts are doing.
But there are other factors (Supply chain logistics, transport logistics, staffing) that come into play now.
So distributed local production while smaller in numbers is a good fallback-plan.
(I’m pretty sure these parts could be reused by disinfecting them in alcohol/water solution and hot water if needed but that doesn’t help you much if the instructions say to dispose of the part and then suddenly the box is empty…)
Hello everyone
i think we should put our heads together and find/create and publish respitory aids ( stl’s ) for everyone to reproduce everywhere’s a handyman at sight ( preferably with 3d printer and electronics to simple explanations for someone with an airpump and motor ).
any ideas?
There is a definite need for open design medical equipment. This means that an open source design for something that is tested as medically viable. Any manufacturer that would PRODUCE the design would have to get their version of the design and their production process medically certified, but the idea that there are designs that can be readily studied, and annotated, and can have their parts reproduced at will/need seems like a really good thing to have in the apocalypse archive (or in engineering schools and for general public study). I used to work in the nuclear industry. Designs of industrial skids for the nuclear industry need to include complete plans so that in the case of an emergency where they need to rebuild something (ex: an earthquake that damages that part of the plant, or a flood or a fire), they can access the plans and have that skid rebuilt.
I’m getting to be strongly of the opinion that a whole slew of medical equipment needs to have a similar setup on hand in order to be able to remake parts when old equipment reaches the end of life, and the original manufacturer stops making the parts for that product line. Something a lot more detailed than the pictures that are provided with patent applications.
the following is a project on open-source respirators, don’t know much about it yet:
https://www.projectopenair.org/
looks like they are organising using a slack channel. (haven’t looked at it).
Look at http://www.venteclife.com/assets/pdf/VOCSN_Multi-Function_Ventilator-COVID-19-Coronavirus-Response.pdf
Had to put this thought somewhere: In these times of the coronavirus “pandemic” should we be all keeing a little diary of who we’ve had contact with each day, so if we get infected, or one of them does, then we’ve got ready made lists to help contact tracing?
At this point, if you need to keep a list, you are have far to many interactions.
At this point, if you didn’t realise google was already doing this…
From Business Insider:
Coronavirus, a Brescia manca una valvola per i rianimatori: ingegneri e fisici la stampano in 3D in sei ore
https://it.businessinsider.com/coronavirus-manca-la-valvola-per-uno-strumento-di-rianimazione-e-noi-la-stampiamo-in-3d-accade-nellospedale-di-chiari-brescia/
No good deed goes unpunished
https://www.theverge.com/2020/3/17/21184308/coronavirus-italy-medical-company-threatens-sue-3d-print-valves-treatments
This company is about to make a fatal error. Their response should be to attempt to flood the market with their device.
There are a lot of smart, ingenious, and pissed off people out there, and their response will be to
reate a superior device, and place it in the public domain.
As we say in Texas, this company is going to be left “sucking the hind tit on the cow” with the associated dung smeared all over them. What a bunch of idiots!
TheVerge issued a retraction of this story the next day. There is apparently no evidence to support a threat having been made.
The plan for the valve should be available through the patent office website if you know the name of it.
The original manufacturer and patent holder is going to file a lawsuit for patent infringement 🙄
Hi, do you have the plans for me to print more of these
make em transparent and uv resistant and the blast it with uvlight so no germ can enter
for anyone [like myself] asking for the CAD, here it is for a variant design;
https://grabcad.com/library/respirator-free-reanimation-venturi-s-valve-1?fbclid=IwAR2VNSZeDoSPJ5MTUnURTcP4NYhnXJQRmCza79437PH8ysMljOmdidE3AtY
COVID-19 CIVIC TECH communities & hackathons, List per country
(Short URL: https://bit.ly/3bizew3 please share)
Have you considered whether a modified 3d printer itself could be used as a makeshift ventilator? Video discussing this idea: https://youtu.be/tknPh-hj5Yc
Maybe make the design public so citizens and make them for their local hospitals to help.
https://www.thingiverse.com/thing:4241625
You guys are doing excellent work! As hospitals and other medical facilities all over the world are experiencing a shortage of masks, shields, and other equipment in the wake of the COVID-19 outbreak – the 3D printing community, from makers and hobbyists to major companies, are answering the call. Zeal 3D Printing is also producing 3d printed masks, face shields to protect people from coronavirus. We would also like to contribute from our side, you can contact us at https://bit.ly/2yPl0ok We are giving free assistance also a free mask or face shield with each order.