Like everyone else, hackers and makers want to do something to help control the spread of COVID-19. The recent posts on Hackaday dealing with DIY and open source approaches to respirators, ventilators, and masks have been some of the most widely read and commented on in recent memory. But it’s important to remember that the majority of us aren’t medical professionals, and that even the most well-meaning efforts can end up making things worse if they aren’t done correctly.
Which is exactly what [Josef Průša] wanted to make clear about 3D printed medical equipment in his latest blog post. Like us, he’s thrilled to see all the energy the maker community is putting into brainstorming ways we can put our unique skills and capabilities to use during this global pandemic, but he also urged caution. Printing out an untested design in a material that was never intended for this sort of application could end up being more dangerous than doing nothing at all.
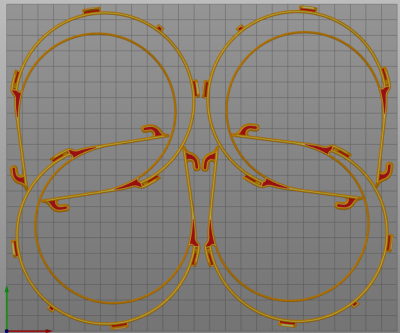
To say that he and his team are authorities in the realm of fused deposition modeling (FDM) would be something of an understatement. They know better than most what the technology is and is not capable of, and they’re of the opinion that using printed parts in respirators and other breathing devices isn’t viable until more research and testing is done
For example, how can we ensure the porous plastic parts are sterilized and not just serving as a breeding ground for bacteria? It’s hardly a new concern; the debate about printed objects in food contact applications has been going on for years.
The safest option is to only use printed parts for structural components that don’t need to be sterile. To that end, [Josef] used the post to announce a newly published design of a printable face shield for medical professionals. Starting with an existing open source design, the Prusa Research team used their experience to optimize the headband for faster and easier printing. They can produce four headbands at once on each of the printers in their farm, which will allow them to make as many as 800 shields per day without impacting their normal business operations. The bottleneck on production is actually how quickly they can cut out the clear visors with their in-house laser, not the time it takes to print the frames.
It’s easy to get excited when success stories featuring 3D printed medical devices are in the news, but that doesn’t mean you should be cranking out lifesaving devices with that roll of bargain PLA you’ve had sitting around the shop. As difficult as it may be for some of us to admit, the safest thing might be to let our spare CPU cycles do battle with COVID-19 instead.
I agree with the final comment. 3D printing is cool, but things like headbands are normally made by injection molding, and produce a solid and easily sterilizable end product. Most 3D printing leaves small interstices which makes it hard to sterilize (high temp would probably melt it, so you’re left with gas, and you have to wait for the gas to diffuse into the little pores)
Use your thoughts and PCs to figure out how to run more shifts on the injection molding machine (which is probably in China, so that’s the real bottleneck). Or find a die maker and local injection molder.
They don’t need to be sterile. Single use is fine.
You need to sterilize them on shipment (or receipt), otherwise, someone who is shedding pathogens at the manufacturer will contaminate them. It is true, that for some applications you could do a surface sterilization with e.g. bleach and water – if the pathogens are in the interstices, they might grow, but in a single use application, the probability they’d come to the surface and be transferred is low.
The whole “breaking the chain” of contamination control is surprisingly difficult.
I read an article that printed plastic comes out sterile. Enclosed printers and regular sterile handling procedures might be all that’s required. Maybe we should convert our printer covers to gloveboxes lol
Microbial spores can survive fairly insane temperatures (see e.g. https://link.springer.com/article/10.1007/s00792-018-1035-6), and I think you’re underestimating what it takes to keep something sterile. There is a reason autoclaves work at 121ºC AND 10 atmospheres of pressure, the temperature alone isn’t enough. Microbes are *everywhere* and float through the air pretty well. Anywhere there are people or animals they’ll generate contaminated aerosols. You’d have to sterilise the filament before it goes into the printer enclosure or else particles could shed off the filement before the filament goes into the hot end. You’d have to sterilise the enclosure between runs, and the entire printer itself. The moment the enclosure gets opened the risk of contamination isn’t small. Is the packaging sterile? How have you sterilised it and to what standard and using which method? Are you certified for that standard?
With medical devices things usually get packaged and injected with a sterilising agent or packaged and then irradiated, so that once the sterilisation is completed the products are already sealed from the outside world. Even in the lab you work with a range of tools to keep an area sterile but the moment you move the item out of that area it becomes questionable, because the consequences of a slip in sterile technique can be a massive headache, and I don’t even work in a clinical setting where a persons life could literally be at stake.
Apparently one of the problems with Covid is that it stresses the lungs and immune system to the point that the body struggels to fend off bacterial infection and then you get pneumonia. In that situation I’d guess that you absolutely do not want to be using anything which isn’t sterile to the proper standards.
Your lack of microbiology understanding is showing. You might want to hide it.
Once it is printed sure its sterile. but literally everything downstream won’t be sterile. I can guarantee you that at home printers(even professional print shops) aren’t sterile and the people who handle them won’t know what aseptic technique is.
The question is: is it more sterile than someone’s face? If yes, then it’s useful in a pinch. We can track down the trail of sterilization if you want, but when we’re facing war-like conditions, compromises have to be made. The Cautionary Principle is really a luxury at times like this. It’s just reality.
correct to a degree. if you want to make sterile parts you injection mold them then walk them on a conveyor belt in front of a gamma ray source for like 10 mins. the injection mold kills most stuff (300C) and the gamma ray source kills the rest, you need both.
I really hope no one is 3d printing an implantable. PLA filament has all kinds of stuff in it you dont want in your blood or lungs
Don’t give problems without offering solutions. If sterility is a concern, print in PLA and use alcohol friendly material. PPE should assembled by the end recipient after alcohol bath, dry and use.
This is not because we have other choices, it is perhaps this or nothing… no one is immune to this virus, eventual if dramatic steps are not taken there will not be anyone left to respond….
So stop giving problems and offer solutions….
If coming up with practical solutions to a complex problem were so simple do you think we would be in this situation in the first place?
The potential solution I suggested is bleach and water, but I do not have the skill set nor experience in sterilization to be sure it would work as intended. Partly this is to prompt the discussion – others (Shoe) have commented on temperature/pressure autoclaving not being viable – perhaps gas sterilization would work – it’s used for things which can’t tolerate high termperatures.
In a design review, the reviewer does not have to necessarily have the answer, but they’re expected to point out the *potential* problems that need to be addressed.
According to published tests, the CoV-2 virus doesn’t survive in a transmissible form on various surfaces for longer than about 3 days. If they’re kept reasonably clean and sit in a dry environment for a week or more, they should no longer be contagious regardless of who handled them.
I wonder if we could upgrade it to incidental contact sterile, so personal use mask frames and shield frames would be re-usable. I’m wondering if the salt infusion method mentioned for masks would work or could be adapted, so everywhere there’s holes there’s salt crystals. If that works, maybe a good idea for doorknob covers etc.
Do you think that the standard medical gloves are sterile? Standard “tuff-cut” shears? Standard masks? Standard eye protection? Hell, even pre-filled medication syringes – Braun Omniflushes do/did come in two versions, a “Sterile packaged version” in which everything is sterilised, and a standard version where only the actual saline itself is sterile, the packaging is not designed to keep the outside of the syringe sterile.
Generally items are only manufactured sterile if they are entering the human body, anything external isn’t sterile (unless used in a theatre setting).
I think there’s a hammer in search of a nail issue here.
If they used a CNC cut or 3d printed steel die rule holder to punch out the clear visors they could be producing them at a much higher rate. A few cycles of R&D should be enough for such a simple object.
I agree – Injection molding and die cutting is I’m sure how they’re done commercially. 3D printing is good for small quantity unique objects, especially for design iterations. For mass production nothing beats squishing plastic into a die or cutting 100 at a time in a press.
I wonder if there’s some other common use widget that 3-d printing owuld be good for. One that strikes me right off is if you could scan someone’s face, you could 3-D print a custom respirator half face or full face mask. Right now, you have to start with a box of different brands and sizes and try them all until you find one that fits “you”. It’s much like buying shoes. Not that there’s huge need for such respirators today, but if the next disaster is something where you need filter cartridges, that would be a huge help.
I don’t own a factory nor much more than a simple little CNC, K40 laser cutter and a couple of 3D printers. I have no problem spending my day making these things and delivering them by night to area hospitals. If someone with a factory wants to pick up the task, these are all open source projects and they are encouraged to join and help.
A lot of people seem to have a need to appear useful to others. One of my friends was using a resin-curing UV chamber to sterilize paper towels with rubber bands which he was handing out as masks. When I responded with incredulity, I got a lecture about how it’s not like I was doing anything to help.
It’s like the rise in Folding@Home participants. People care more about looking like they are helping than they do about actually helping.
There’s evidence that things like that are useful. Even a scarf would help mitigate COVID-19 spreading somewhat.
I am not disagreeing with your point, but here’s hopefully a bit of constructive advice. If you are pointing to the existence of evidence to make a claim, why not go all the way and provide a link to the peer reviewed article/publication/study providing that evidence?
Just saying something is true (even if it really is) without backing it up makes it look like you care more about looking like you are winning an argument rather than actually convincing others with solidly supported logical arguments.
(And please don’t use the cop-out I see so many throw around that the people you are trying to convince should just “google it for themselves”, the onus of providing evidence is on those making a claim not those they are trying to convince). Hopefully I don’t sound too heavy handed or dismissive, but I think doing due diligence can make conversations like this more constructive and effective.
here you go, a couple studies that show that something is better then nothing when talking about masks during a pandemic, this site has lots more of these studies most have been peer reviewed and have supporting evidence,
https://www.ncbi.nlm.nih.gov/pmc/articles/PMC2440799/
https://www.ncbi.nlm.nih.gov/pubmed/19797474
l
These do not appear to be designed similar to what I know of as surgical use face-shields, but more as a general barrier system. Splash-prevention surgical face shields tend to open up, not down, for most purposes. The idea here is to stop the spray of fluid/droplets/etc from getting on your face. These appear to be more of a general purpose face-shield, the type you would see in a quasi-triage situation.
Either way, kudos on the design work.
Ah, many a reddit thread I’ve came across on this topic. . So, so many. I knew we’d be hitting this conversation all over again frankly. But obviously now that there’s an accelerated need, I would hope those with the proper imaging gear would be starting to do some real research on this sort of application. Nothing is impossible.
One of the best parts about Prusa’s blog post on this subject ISN’T the fact that they were able to crank out tons of face shields within three days and by using materials sourced locally in a single afternoon.
The best part is showing that validating the design and process is inseparable from consulting with the actual end users and experts (and conforming to what the experts say) is a critical make-or-break part of the whole process. Anyone who doesn’t do that is probably falling into the Engineer Savior trap.
But I just came up with a whole new color coded branching tree paradigm for control of existing respirators with only two buttons, just 23 simple button press decisions to change a parameter on the fly. They don’t know it yet but it’s going to be MUCH better ;-)
We have just published a bit simplified version of face shield. 3D printing was eliminated and whole shield can be made on 40w trotec laser in about 80 seconds. Feel free to use!
https://hackaday.io/project/170481-laser-cut-medical-shield
Here’s a vastly simplified design inspired by this shield. It only uses laser cut plastic sheet and is very quick to produce.
https://hackaday.io/project/170481-laser-cut-medical-shield
I think the point of the choice between no part or a 3D printed part has been missed. Yes, there needs to be much more research before 3D printed parts are used routinely. In extremis you take whatever you can get.
no part on a ventilator might be better depending on the part! If you can’t count on the part’s reliability you might just kill someone too.
for the face shield above just skin contact it’s probably fine.
If it’s a choice between not having the part and them dying, or a 3D printed part and them only maybe dying which do you go for?
I would like to say that for older me I vote for the maybe not dying.
Sorry, I think you’re missing the point.
The point is that a badly made item is not necessary better than nothing. It can create more problems than it solves.
We’re all hopefully smart enough not to try home radiotherapy. But when faced with what appears to be simple plastic parts etc we’re tempted to think “I could make that” without necessarily understanding the issues.
I made a UVC box at home that you can put objects like this in and the UVC kills the viruses. We are using it for amazon and mail and grocery deliveries.
yo there us RC2 version with major design changes https://www.prusaprinters.org/prints/25857-prusa-protective-face-shield-rc2
Had another expedient solution occur to me (Given that hospitals are calling for sewed up masks now, I figure we need every type of solution possible) Cellulose acetate sheets, as used for OHP slides in the past. Got a stash somewhere? They are a little floppy, but put a curve in them, snip the corners off to stop them catching and you’ve got some sort of face shield, ad hoc as it is. Headband, there’s some elasticated fitness headbands you could slide one under. Another idea is to use extra large 24″ plus, cable ties. The acetate sheets should be able to be thermally bonded to it. Either with a soldering iron, quick dabs to spot weld, or maybe friction weld, with a drill press on high speed with a rod, or reversed drillbit again to spot weld at several points along it. Suitable adhesives need to be tested, gut feeling is that rubber cement type compounds will work best. Before using with a ziptie, use a needle file or a strip cut off an emery board type nail file, to blunt the catch inside the end of the ziptie, such that you can pull the ziptie open again, yet that it still holds fairly well.
Hospitals in my area put out the call for face shields 2 days ago. That I know of, 2 different major hospitals in the area. Talking with a nurse and dr online from a local
hospital they ‘are taking donations because they can’t afford to be picky in this situation.’ This isn’t just sitting at home being armchair biologists and dreaming up sci-fi
movie scenarios. We’re being asked to help these people live, and keep not only their families but our own safer in the process.
“As difficult as it may be for some of us to admit, the safest thing might be to let our spare CPU cycles do battle with COVID-19 instead.”
As difficult as this is to admit; We’re past that. Spare cpu cycles is a luxury of our advanced society. Thats the kind of stuff you do comfortable in the knowlege that you,
me, and our families are safe and nothing we can do will help our systems cope. This was true a month ago. This is not true now.
We’re not talking magical death spores. We’re talking 1 specific pathogen that we’re being tasked with helping defend against using the tools and materials that we have
available. Not next year, not next month, not when when we’re sure all the contingencies have been covered. Now.
This isn’t panic speaking, but practicality. We know we can provide help with well made products. Perfect help? No. As good as injection molded parts made by billion dollar
facilities? No. But better than these medical personel working with the sick without any PPE at all, which is what they are facing. ..and is what they will be doing if we
don’t fill the gap where there is a need.
also.. sorry about the formatting.. browser being on my tablet.