To place a satellite in orbit satisfactorily it is necessary not only to hitch a ride on a rocket, but also to put it in the right orbit for its task, and once it is there, to keep it there. With billions of dollars or roubles of investment over six decades of engineering behind them the national space agencies and commercial satellite builders solved these problems long since, but replicating those successes for open source microsatellites still represents a significant engineering challenge. One person working in this field is [Michael Bretti], who is doing sterling work with a shoestring budget on open source electric thrusters for the smallest of satellites, and he needs your help in crowdfunding a piece of equipment.
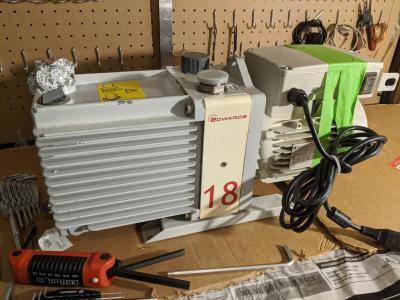
As part of his testing he has a vacuum chamber, and when he places a thruster inside it he has to create a space-grade vacuum . This is no easy task, and to achieve it he has two pumps. The first of these, a roughing pump, is a clapped-out example that has clearly reached the end of its days, and it is this that he needs your help to replace. His GoFundMe page has a modest target of only $4,200 which should be well within the capabilities of our community in reaching, and in supporting it you will help the much wider small satellite community produce craft that will keep giving us interesting things from space for years to come.
We’ve mentioned his work before here at Hackaday, and we hope that in time we’ll have a chance to look in more detail at his thrusters. Meanwhile you can follow along on Twitter.
Thanks [Bruce Perens K6BP] for the tip.
We have reached the cost of the pump in our GoFundMe! The community really stepped up, we got three $1000 donations and reached the goal much faster than I expected. If you want to contribute, though, I am sure that Michael can put additional funds to good use.
Many, many thanks for the incredible support the community has shown! The fundraiser was a resounding success in such a short time, and has literally helped save this effort. The funds will not only help support a new high-reliability pump for the next phases of even more advanced propulsion testing, but help me jump-start several new open source plasma and ion thruster builds, and allow me to continue providing resources, builds, and educational material to the community!
Roughing pump (forepump) is usually furthest from the vacuum and not called the first pump, is it? Nobody like waiting for chambers to pump down. Turbos are under $500 these days. Or get some more dough for a controller and turbo forepump for this https://www.ebay.com/itm/Oerlikon-Leybold-TW250S-Wide-Range-Turbomolecular-Pump/114059223561?hash=item1a8e75a209:g:Cv8AAOSwjCBeF4ge
Yes, he has a high-vacuum pump that, fortunately, works. I’ve noticed that a few people have picked up that turbomolecular pump at a low price you can’t ignore.
The pump we raised for is the pump that supports the high-vacuum pump and gets the chamber to a medium vacuum.
There are also some really cheap vacuum pumps made for the refrigeration industry, which pump out the cooling loop in an air conditioner before the refrigerant is added. But these do not last when made to support another pump in getting to space-quality vacuum.
Here’s an idea for a very rapid vacuum pump that should be able to pull at least 50% of the air out in a few seconds.
You’ll need a double acting air cylinder with more volume than the vacuum chamber, and a second double acting air cylinder that’s even larger diameter, with the same stroke.
The idea is to have the larger cylinder pull the piston on the smaller cylinder, which is connected to the vacuum chamber. It should pull a large fraction of air from the chamber as fast as the larger piston can move.
Two ways to mount the cylinders. Side by side so that the piston rod ends are connected by a rigid block of metal. Inline so that as the large piston’s rod pulls into its cylinder, it pulls out on the smaller cylinder’s rod.
With double acting cylinders you can put the suction line on the port for in or out stroke. Valve it right and could do a couple of strokes to pull a bit more.
This setup would also need an air compressor with a large air tank, with more volume than the large air cylinder.
Advantages? Sheer speed of doing the initial pump down and a lot less wear using the roughing pump to take considerably longer doing that part of the job.
If the chamber is small enough you could hang an air cylinder from the ceiling and use a bunch of heavy weight to pull the piston, with a hand crank or electric winch to raise it up for the next use.
Piston pumps are almost useless for any kind of vacuum setup like this. If you need to pump down fast you get a decent size roughing pump and a roots blower. Rotary oil pumps last for thousands of hours, just pop in a rebuild kit and you are usually good to go unless you sucked in some crap and scored the rotor and stator.
You gotta be very careful with turbos and used ones. Bearings have a limited life and the turbos themselves are easy to crash and when they do they do so violently. I have seen the remains of crashed pumps and it is not pretty. Really a diffusion pump is a lot better candidate for something like this and almost nothing to break.
I am currently using a 600 L/s diffusion pump as the main pump. My system is designed to maximize throughput and pumping speed as physically possible to handle higher gas loads of thruster systems at high vacuum. In fact, you can actually download all the calculations, CAD, thermal simulations, and molecular flow simulations for my vacuum system off the Applied Ion Systems website, and I have written a lengthy tutorial on in-depth vacuum engineering design looking at a smaller chamber example for optimizing performance. Regardless if using a diffusion pump or turbo though, a foreline pump is still needed, and needs to handle the main pump gas load. The system can hit 10^-5 Torr in about an hour from cold start (which is the bare minimum vacuum level before I turn on any thruster system), and usually hovers around mid 10^-6 Torr during longer term testing. Most of that time is actually spent roughing – once the diffusion pump drops below 10^-3 Torr, pumping speed greatly increases and the pressure falls extremely rapidly. Turbos are definitely very nice, especially for cleaner pumping with less power draw and cooling requirements, but diffusion pumps are pretty much indestructible, and are great for brute force pumping.
Spending 4k on a pump is nuts, there are tons of used pumps on the market, you just need to find someone that has tested or can test a pump before they sell it, or if they are close to you test it yourself. I have a friend selling used, tested pumps in the RV12 size range for about $500.
A used, tested pump isn’t really the same as a professionally rebuilt pump, though. Their lifetime between rebuilds is in the thousands of hours. The goal was to get something that would last lots of hours before needing a rebuild, so that he could spend his time on actually designing thrusters.
Unfortunately, I have had a lot of really bad luck with roughing pumps. I did have a cheaper two stage rotary vane refrigeration pump I used last year that, despite working well, died after only a few tens of hours of use (the pump was brand new too, and was used in a very clean system). I bought a used and “working” Edwards E2M18 on eBay, which ended up not working upon arrival. I got the full rebuild and vane kit, fully scrubbed and cleaned the whole thing, put it together, and no improvement in performance was made (could not get below 1 Torr still, and the vacuum chamber and gauge was already qualified and checked using a friend’s working pump.) Due to these setbacks, and very limited funds, I have been out of testing for nearly half a year (though still doing research and putting out designs and details for the community.) Unlike a lot of other high vacuum work you might see at the maker level (semiconductor, sputtering, basic plasmas, and even amateur neutron sources), thruster testing requires very long up-time and operating periods, often thousands of hours continuously for lifetime qualification of thrusters in research and industry. In order to support this next phase of more advanced testing, unfortunately I need a very high reliability pump for the many hundreds of hours of testing required for these new thrusters. Thanks to the incredible support of the community, I am able to purchase a new pump to continue this effort and advance electric propulsion even further at this level. I found the required RV12 at lower than the target goal (brand new, full manufacturer warranty, etc) and have plenty funds leftover to jump-start several new thruster development phases. All of my work is completely open source, and I provide a significant amount of electric propulsion and vacuum resources for the professional, educational, student, and enthusiast communities. It is the first fully open-source, independent maker-based electric propulsion program out there, aiming at ultra-low cost propulsion (over an order of magnitude cost reduction compared to current plasma/ion thrusters available on the market), and with two plasma thrusters aboard AMSAT-Spain GENESIS PocketQubes, which have a shot of being the first thrusters to ever fire in orbit aboard a PocketQube (launching this September), and new ion electrospray thrusters potentially flying next year as well (the first ever PocketQube compatible fully integrated ion thrusters I am aware of), there will be a lot of exciting developments to come that this new roughing pump will help support.
Wow, HAD is running ads for friends now?
I want a nicer laser cutter, I want a big assed CNC couter, I want a big assed CNC plasma cutter, I want a nice LCD digital scope. Drop them off at my doorstep and I will come up with the next bunch of things that I want.