Many decades ago, a much younger version of me was in the car with my dad and my brother, cruising down the highway on some errand or another. We were probably all in the front seat, and none of us were wearing seatbelts; those were simpler times. As we passed under an overpass, my dad said, “Do you know why the overpasses on these roads are so high?” Six-year-old me certainly didn’t, but it was clear dad did and had something to say about it, so we just shook our heads and waited for the lesson. “Because that’s how big nuclear missiles are.” He then went into an explanation of how the Interstate Highway System in the USA, then still in its infancy, was designed to make sure the armed forces could move around the country, so overpasses needed to allow trucks with big loads to pass.
It was an interesting lesson at the time, and over the years I’ve continued to be impressed with the foresight and engineering that went into the Interstate system here in the US. It’s far from perfect, of course, and it’s only recently that the specifications for the system have started to put a pinch on things that seem totally unrelated to overpass dimensions — namely, the size and efficiency of wind turbines.
The Taller, the Better
Outwardly, the ability to turn the kinetic energy of wind into electricity would seem to have little to do with the design decisions made by civil engineers during the Eisenhower administration. But when dealing with wind power, size, or more specifically height, matters. The higher a wind turbine’s hub is above ground level, the more consistent and the faster the wind. A study by the National Renewable Energy Laboratory mapped wind speeds at 110 m and 160 m above ground level (AGL) over the entire country. When compared to the winds at 80 m — about the average height for a big wind turbine these days — the difference is striking.
If wind turbines could be lifted up to 160 m AGL, vast swathes of the country could potentially be used for wind energy production. The NREL estimates that taller turbines could generate up to 45% more electricity.
Low Bridge Ahead
So the need for taller turbines is clear, but building them taller creates other problems. The taller the tower, the wider the base needs to be, to support the massive weight of the machinery above it and to resist the loads placed on it by the wind. The current crop of 80 m turbines has base sections that are about 4.5 m in diameter, which is just shy of the minimum highway overpass height (16 feet, or 4.9 m) specified for Interstate highways. When placed on a low-boy trailer, or on a trailer tailor-made for the job, the lowest sections of the tower just barely scrape underneath some overpasses, making for some interesting moments.
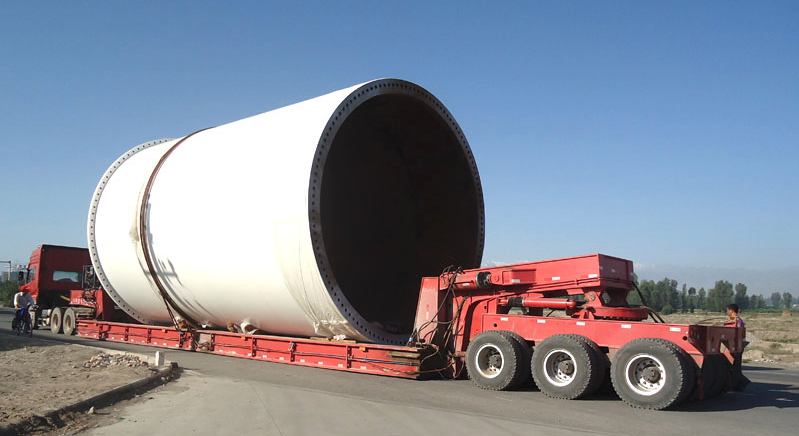
The obvious answer to the need for such large tower base sections is to forget about fabricating them in factories and to just build them on site. And while that’s possible, the economics of construction works against it. The factories that make such huge parts are filled with even bigger machines needed to make them. The workers there are skilled tradespeople working under controlled conditions to produce precision parts that will stand up to enormous loads. Expecting such precision processes to be performed in the middle of a North Dakota cornfield in the middle of February is asking a lot.
On-Site Extrusion
As it turns out, though, it may actually be possible to set up a wind-turbine tower factory on the job site. General Electric, in cooperation with building materials company LafargeHolcim and construction 3D-printing concern COBOD, has recently announced plans to 3D-print the lower sections of wind turbine towers up to 200 meters tall. Their first prototype, a ten-meter tall tapering cylinder of extruded concrete, was printed in late 2019 at COBOD’s Copenhagen facility, was printed using the company’s BOD2 modular gantry printer.
The BOD2 printer was originally designed to print entire structures, from houses to small office buildings, onsite with minimal need for skilled trades. Depending on how the 2.5 m modules for the X- and Y-axes are configured, the BOD2 can print structures up to 14 m by 50 m, so it should be plenty big enough to print the base sections for even the largest wind turbine towers. Once the base sections are printed on-site to a height where the diameter narrows to less than 4.5 m, traditional prefabricated sections will presumably be transported to the site and assembled on top of the extruded pedestal.
There’s obviously a lot of engineering to be done to make sure this hybrid approach will support the loads that such large wind turbines will experience. But it seems like a clever use of a technology that, frankly, has always seemed to us to be a non-starter in terms of its ability to produce buildings that are attractive enough for people to actually want to live and work in them. Such a utilitarian application seems to be the perfect use case for large-scale 3D printing, and we’re eager to see if it pays off in the long run.
When I was in “Jolly Old England” several years ago, I noticed their overpasses had higher clearance than those found om most Interstate highways. My guess it is because the double decker busses are taller. The increased clearance allowed for triple decker car lorries.
If I am wrong, I am sure one of our British readers will kindly enlighten me.
https://assets.publishing.service.gov.uk/government/uploads/system/uploads/attachment_data/file/350114/network-rail-bridge-strike-protocol.pdf
> The standard minimum clearance to be provided over
> every part of the carriageway of a public highway is
> 16’6” (5.03m).
So not much higher than in the US, and bridges lower than that have to be signed as they exist – but they would be known and avoided for high loads.
Err… it’s not quite as simple as that in UK. If you have something bigger than the standard clearance there are special routes where we can move much larger items. They will go up and over junctions to avoid bridges and will have special laybys and escorts to enable the strange maneuvers that may be required – I remember building a junction with one of the special routes for large gas turbines we had signs that swung out of the way, specially designed junctions to prevent the long low loads grounding. Great fun was had by all as we tested it live for the first time. Local roads can be more challenging though.
Fascinating. Local roads must be a nightmare. I once visited Brush Engineering in Loughborough. When they began on that site it was on the edge of the town surrounded by countryside. It is now surrounded by housing. They make very large electrical stuff, like railway locomotives and the motors for Trident submarines!
I reckon thats at least a convincing guess. :)
It may have something to do with the nature of some the roads, narrower and curvy. This puts limits on width and length, which leaves one dimension to exploit.
Also it is important for the queen to be able to ride her carriage without her crown getting knocked off.
Us, in Britain, having something better than elsewhere!
“Expecting such precision processes to be performed in the middle of a North Dakota cornfield in the middle of February is asking a lot.”
You misspelled “sunflower”.
B^)
I wonder if slip form concrete techniques can be adapter for tapered structures?
Has it already been done?
^adapted^
Maybe jump form techniques would be better, if they allow the removal of a part of the form to make it smaller between lifts.
Mod-u-form had a tapering slip form back in the 90’s. It’s how Heinz Field was built.
We used that technique on a small erection in Toronto, perhaps you’ve heard of it, it’s called the CN tower.
I have heard of that “small” tower, I had no idea what construction techniques were utilized in its erection.
Thank you!
On the other hand, I had not heard of Heinz Field, is that where they grow tomatoes for Ketchup?
B^)
I always wonder why instead just horizontally extrude ring big enough to not collapse with “I” or “⊿” shaped extruder with dynamically change curvature.
You can also make dynamically changing 2D geometric models extruder for even faster and universal “3d printing” but it more like dynamically(composite) joint extrusion.
that would be one insanely complex form/mold…
This is cool, but I’m dubious about the practicality.
Big turbines have enormous loads to deal with. The mass of the equipment at the top is almost insignificant because the thrust on the blades is huge: approx 1MN (~100 tonnes) per MW power rating is a reasonable rule of thumb. The structural challenge comes when something on the turbine fails; a fairly normal response is to pitch the blades to their neutral position as fast as they will go.
So suppose your 10MW turbine is operating in a good wind; the blades are pitched away from fine, say about 30 degrees. Something breaks and an emergency shutdown is initiated. Your blades might pitch at 10 degrees/sec so they’ll reach neutral (90 degrees or thereabouts) in about six seconds. You’ve just removed 1000t of horizontal loading on the tower top over six seconds, the vast majority of it happening in the first second or two (there’s every chance the blades will stall quickly, so a significant fraction might be more or less instantaneous).
Watching a turbine do this is frightening. That steel tower acts like a spring in a child’s toy and the top of the tower oscillates back and forth in a very alarming way (the middle 30s of this video gives a reasonable view of it: https://www.youtube.com/watch?v=_qVXkAWtH60).
All of this makes concrete a curiously bad material for building wind turbine towers. Concrete has good compression strength and very poor tension strength. When the tower bends back and forth like this, one side is compressed and the other is stretched. Concrete towers are not unknown, but they typically have heavy steel cables running down the inside, prestressing the concrete so that it remains in compression for all likely angles of tower deflection. The bigger the turbine and the longer the tower, the bigger a problem this is.
I’ve got a photo somewhere looking up the inside of a concrete tower and showing the cables; if the site wants to get in touch, I’m happy to pass it on. There doesn’t seem to be a way to attach photos to comments.
On the other hand, this concrete structure does have plenty of channels to run steel in, and is not the majority of the structure; it’s certainly a design consideration but it’s pretty plausible that a base section built this way will work just fine. You can likely also reduce that kind of dynamically driven strain in this section just by having it be a bit more massive, focusing the deflection in the upper, conventional tower.
The tower I have photos of was built like this; 40% of the height concrete and the rest steel. It still needed steel cables to pre-stress the concrete.
On a side note, I was at this turbine in January in Finland; outside temperature ranged from -25 to -30 C. While we were there, some men came to grease the cable joints at the top and bottom of the concrete section of the tower. They had a 3gal bucket of grease which was frozen solid. So they’d set up three diesel powered hot air blowers in triangle around the bucket and wait for it all to melt. Then they’d go and grease joints until the grease all froze again. Rinse and repeat.
When I was in the Middle East, I watched a mechanic grease the wheel bearings on a trailer/float.
The grease was very stiff, like wax. The mechanic scooped it out of the bucket with his hand, and shaped in into a torus, very little of it stuck to his hands. My interpreter said that the grease would flow when the wheel started to turn in the hot temperatures.
when I went to Krispy Kreme, the person behind the counter handed me a torus of grease coated in liquefied sugar. It stuck to my insides.
One time, at the music camp…
This is actually a good example of unintentional “fail-dangerous” instead of “fail-safe”.
Now, the towers are likely designed with this rapid load change in mind, making it safe. (would surprise me otherwise, since there is a lot of wind turbines around the world…)
But going from the current dangerous state over to a safe state isn’t always going to be better if one does it faster. But doing it too slow can be just as dangerous as well… So its all about finding that middle ground. (And don’t expect all failures to act the same in all scenarios, so that “middle ground” can vary rather wildly.)
Though, in terms of wind turbines, there is likely a few methods for them to handle a whole slew of potential issues in a safe manner. (The only thing I can think of that one can’t do much about is if a blade were to dislodge… But that is indicative of poor maintenance.)
And I too wouldn’t really agree that concrete is an all that good material choice for the application. Due to all the tensile stress involved. Though, concrete could likely be used to build a smaller tower to lift the rest of the tower higher. Since we won’t expect as much flexing down at the base. (Ie, an artificial hill with very very steep slopes.)
The rate at which the blades pitch to feather during fast and emergency shutdowns is indeed a very carefully engineered choice to minimise the loads on the structure during extreme events.
There are, however, a number of difficult situations that can lead to turbine failure. Apart from operator error, most of them relate to extreme weather events. Handling very high winds is difficult, especially if the wind direction is highly variable or the turbine has no power. A very strong gust from behind the turbine is sometimes capable of breaking the pitch control machinery; once this happens, there is no control possible and almost the only possible outcome is total collapse unless the wind drops very quickly indeed. Turbines have brakes but not ones capable of opposing the full torque generated by the blades at fine pitch angles in high winds. Likewise they have a locking pin, usually a piece of high-grade steel about six inches across, but the torque exerted by the blades is capable of shearing this through. For this reason, the usually storm strategy is to yaw the turbine into the wind with the blades held at feather; once the turbine loses power, this is no longer possible. It is therefore not unheard-of for wind farms to have large diesel backup power systems. This scenario is also the reason why pitch systems integrated into the blade root have largely taken over from the older design where a central pitch motor acted through levers to move the blade angle.
Extreme cold also poses difficulties for turbines. Apart from the obvious risk of machinery freezing solid and so losing control of the turbine, ice can build up on blades in the same way it does on aircraft wings and large chunks of ice can be slung considerable distances (consider that the blade tip on a large turbine can be doing well over 150mph). There was a house partially destroyed in southern England in this way some years ago, though I can’t dig out a google reference to it immediately. The usual strategy for this is simply to stop turbine operation at about 5 degrees C, though some manufacturers have attempted cold-climate versions of their turbines.
if you have a blade unintentionally separate from the hub while turning, the entire thing is guaranteed to crumple like a coke can ;-)
Tall steel buildings with a concrete foundation have the exact same loads applied to them with wind gusts. Those problems have been engineered for over a 100 years. Concrete can take the compression load on the leeward side while blowing and then the spring back on the windward side when it stops. Steel in concrete just holds the cracks together.
Errr… no. The thrust load on a turbine is not the drag load on its surface area, it’s the lift generated by the blades. They are at least an order of magnitude different loads (more likely two) for a similar structure.
GE are total cheapskates. I am sure they would only do this demo if it had a solid business case and engineering evaluation.
You might be surprised at the number of dumb ideas people attempt in wind turbines.
Why do we continue to persue Wind Turbines with the afor mentioned structural problems? I admit there is a certain beauty to watching a turbine spenning away. That being said these mechnical systems are subjected to the same stresses as the towers. Mechanical systems fail, often spectacurarly. Solar and nuclear systems (fourth generation) are the only rational solution. Please over look my spelling errors and my spell checker does not work with this platform.
When LightBridge finishes their current trial, Nuclear power will make a HUGE comeback with a clean fuel.
It’s the power of the future….
It will be too cheap to meter!
I knew of a beautiful single woman with very expensive tastes,
but I was too cheap to meet her!
If we allowed for spent fuel reprocessing, we could do a lot more with current tech. But the process to reprocess the spent fuel is very similar to the process needed to create enriched fuel for nuclear weapons.
Nuclear weapons and the terror they instill has really affected nuclear power a lot.
then again, all the big nuclear players already DO have active programs for nuclear weapons manufacture, so the proliferation scare is mostly just what the green terrorists use as an argument…
The main thing reprocessing would do for us (as in mankind) is extending the expected fuel reserves from about one century to several, with no impact on growth, which should be more then enough to finally master fusion.
Solar is not really practical, though. It is practical as a supplement, but not as our primary energy source due to the lack of efficient energy storage.
The best energy storage method we have so far is pumping water between two reservoirs, but it requires an adequate topography. There are many places where it simply isn’t feasible.
I do agree that nuclear is the best choice. However, I don’t see it happening anytime soon because people panic whenever they hear nuclear.
Wind is ok, I guess. It does work during the night, unlike solar. And while it’s true that mechanical systems fail, solar panels are not except from degradation. I would not be surprised if wind turbines lasted longer than solar panels, especially the towers.
In my opinion (for large scale generation)
Nuclear fusion > nuclear fision > hydroelectric > geothermal > wind > solar
What’s practical is so dependent on the how the grid you are connecting it to uses electricity, if it can store much and how use changes with the weather – if a huge percentage of the load is on the hot summer days because all the aircon is turned on but the night time temps drop enough not to need it solar looks better than if much of your load is heating overnight all the time (there are so many other variables this is but a single example point).
For energy storage where the topology is against hydro compressed air is a good alternative. Does have caveats and engineering challenges same as every tech but it can be reasonably efficient and dirt simple to make and maintain.
Solar panels (modern ones at least) are showing very very low degradation so baring mechanical damage should last usefully damn nearly forever – even the earliest panels if undamaged tend to work just fine but at much lower efficiency (some of them fail despite lack of outward damage though with some effort can often be ‘revived’ as its just a few cells that have been busted)- so you are definitely correct they will outlast a turbine, that said made in the right fashion and used correctly a wind power system can have low enough embodied energy to still be a damn good system (as it stands too few turbines stay up long enough to really look good on that score – replaced by bigger better ones as we can make bigger blades etc – so lots of old blades in landfill).
You did miss out another excellent power generation potential – tidal. Obviously it can’t work for the landlocked nations or be a major part of providing power for every nation as not all have enough suitable coastline. But tides are reliable and predictable so could make great backbones to a grid – you know how much water will flow in every tide and can let it out at a rate that suits.
On the whole I agree though nuclear fusion isn’t really viable (yet). And I’d put solar above wind and both above geothermal in general (not alot of locations make good sites for it – where wind and sun exist everywhere – its just varied efficiencies and turbine designs etc to make best use of what you get. With tidal probably above hydroelectric – as rain to fill your dam isn’t predictable or certain (and looks likely to get less so) but its a great energy and water store so useful on two fronts where the topography suits it (and many nations could build hydro somewhere – though many probably shouldn’t with the large areas they would have to flood to make up for less than ideal topography).
I’ve always wondered why there are so many incentives to install solar panels in the UK (to be fair they’re mostly gone now). It’s adding extra generation capacity that’s guaranteed only to work during your minimum energy demand.
it depends, in winter of course solar is out, but for summer it’s mostly a match to demand
It’s a subsidy racket, basically. If it wasn’t tax funded, it would not exist at all since all the solar producers would have to compete for the same time slots on the day-ahead market, which quickly makes the price go to zero. The subsidies make up the difference to a guaranteed price, so the utilities get very cheap electricity and the solar producers get high profits. As soon as the subsidies are gone, solar investments drop to zero.
CAES and pumped hydro are also just stop-gap solutions to the storage problem. If the society is going to transition away from fossil fuels, there needs to be cheap Power-to-X technologies where you generate hydrocarbons and other organic chemicals like ammonia directly out of CO2, air and water. These are needed anyways for making other chemicals and materials. With this in place, there’s going to be stockpiles of hydrogen, synthetic natural gas and liquid fuels to serve as the energy storage medium.
You might be a little surprised – is the UK going to get the best possible output for the panel of course not, there are better locations. but they still do work pretty well – even on the dullest winter days they do something. So a great way to cut down how much you have to run other (probably fossil fuel) powerplants.
Its also the only renewable you can really put almost anywhere – wall, roof, on stands in a field, the middle of the lake – so its one that incentives might actually lead to deployment and will get something out of it. You try to run incentives for bio-gas and on small scale and its really not going to achieve much, might get the massive dairy industry sideline bio-gas plant, but almost no company, home etc will be able to pitch in there.
Tidals are not so great as there is only a limited spot on earth that provide enough power capabilities (tidal height is the key).
And as everything that is at sea, maintenance is the worst problem.
There is one tidal power plant in france (Rance), and it’s mostly a failure: too costly, not enough power, big ecological impact and limited site life (due to sediment accumulation).
Same with wave or current generation: sea is harsh so lifetime is very limited, and harnessing sea current have bigger ecological impact than harvesting wind due to current modification (wind power has also an impact, but much lower).
There is no miracle solution, only a handful of ways to generate energy with more or less caveats.
Yeah I didn’t mean to imply tidal is a cure-all super renenwable just another good option to consider. Its also probably the least developed and tested – but its got great potential in the right areas, and doesn’t exactly have an ecological impact – sure you change some ecology to something else but its not wholescale rip out all this nature and just leave nothing (like German coal mining practices with that impressive bucket wheel excavator thing) – tidal wetlands and salt-marsh etc are valid ecological niche, that are often far rarer than they should be as humans love to drain the land for other purposes – so a way to make rare ecologies useful to us so we have a vested interest in keeping them is actually a win.
“You did miss out another excellent power generation potential – tidal. Obviously it can’t work for the landlocked nations or be a major part of providing power for every nation as not all have enough suitable coastline.”
This is why solar, wind and biomass are the most practical large scale renewables – they scale with land area. Tidal scales with coastline, so double the size of your land mass and you only get 40% more tide (and, like hydro/geothermal, it requires specific geography, unlike the other three which just need sun/wind/crop land)
If we can count nuclear fusion, I’d say the list goes “unicorn poop > fairy dust > nuclear fusion > nuclear fission > continuous renewables > intermittent renewables”.
If you include the difficulty of deployment, that list almost completely reverses – building new solar/wind capacity is easier than building new hydro, which is easier than building new nuclear, which has the advantage over fusion power that it actually exists right now.
We rely heavily on a thermonuclear fusion object 93 million miles away.
B^)
As a cloudy island sitting at the receiving end of an ocean’s worth of wind, the UK does a pretty good line in wind power – it makes up half our renewable energy and about one fifth of all production. Saying “solar is the only rational solution” is all very well in Arizona or southern Spain but it ignores the parts of the world where the wind is more reliable than the sun.
Here I sit wondering.
Why not just make that large cylinder into a few pieces?
Yes, we will need bolts/screws to put the pieces back together, and yes, we will have shear forces between the pieces.
But if we rotate each section so that the seem between the two bellow resides on the middle of the piece above, then we should logically be able to eliminate most of those shear forces.
The next advantage is that we can stack the pieces in each other, and then put the pieces for the next section on top, etc.
Meaning that we can now transport a much more significant portion of the tower per trailer. (Ie, less transportation over all.)
And the main advantage is that we can also ship a much larger diameter tower on the same roads.
Though, to be fair, the cheapest wind turbines (dollars/watt) is the ones one can put on a train. (Trains do offer some cheap transportation for the majority of the journey.) Though, we can also ship the pieces on a train too, unless they are too large.
If we ship by train, then each piece can be 3.5 meters wide (to be able to go almost anywhere on most rail networks), that means that the largest diameter tower we can transport is 4 meters if using 3 pieces per section, with 4 pieces per section, the tower can be nearly 5 meters wide. (5 pieces gives us a diameter of almost 6 meters.
If we do road transport and take up two lanes, ie about 5 meters wide (can probably transport even wider loads). Then we can go to 5.8 meters with 3 pieces per section, or up to 7 meters if using 4 pieces per section. (5 pieces gives us 8.5 meters)
Though, if we cut the cylinder into too many pieces, we can risk making the whole structure a bit too flimsy.
Should also point out, when I say “cut”, I mean “Built it with a flanged surface with sufficient bolt holes and strength for the intended application.”
“The next advantage is that we can stack the pieces in each other, and then put the pieces for the next section on top, etc.
Meaning that we can now transport a much more significant portion of the tower per trailer. (Ie, less transportation over all.)”
And the pavement underneath the trailer is crushed to a powder.
Of course we need to take into consideration the max weight the road can take.
But I wouldn’t be surprised if we can load more than one section of tower at a time.
Though, only being able to ship one section at a time still brings with it the advantage that we can transport a much larger diameter than if it were a cylinder.
Good thing railways can handle much higher loads per axle, without oversized loads you’d need only few trips from nearest trainstation to site. USA it night be quite far but in Europe there’s rail even if disused almost everywhere.
Trains can’t swerve to the middle of a bridge span to maximise the width they can move under it. They have a “loading gauge” which is the maximum guaranteed width and height, which is quite restrictive.
Well okay, maybe they can if it’s planned for…
https://en.wikipedia.org/wiki/Gauntlet_track#Belgium/Germany
Point being it’s not so trivial as deploying a few guys in high-vis with blinky lights.
I wonder why more wind turbines don’t use a triangulated Eiffel-tower-style base? Transportation problems would instantly disappear. Only a few use this type for some reason.
Using a cylinder has the advantage that it has the same strength regardless from what direction the force is acting from.
Not to mention the obvious, “there is a lot more material” part…
But technically, yes, the tower can use practically any design, as long as its sufficiently strong and doesn’t interfere with the turbine blades. (A large cylinder just happens to be a very convenient shape.)
http://keystonetowersystems.com/ is an interesting fabrication technique solving this problem. It uses sheets of metal, and spirals them into towers. Started by some Boston area hacker folks several years back
Interesting.
I wonder how it fails, when it does…
Boing?
Sproing!
There’s a few cell towers in my neck of the woods that have been built that way. We get pretty strong winds here (>90 km/h at least a few times a year). I imagine that might work well.
I agree with you, that this is the first application of 3D printed concrete I have seen that is appropriate, and doesn’t matter that it’s ugly. These guys trying to convince people to make an ugly house with it…wow they are stubborn!
Looking how much co2 is produced for every ton of concrete we realy should use it sparesly. So its good thing they are ugly homes because if they get cheap medicore looking well see rapid rise in concrete consumption and co2 production will skyrocket.
the only CO2 neutral building material is wood, which lets face it is not a viable substitute for other materials…everything else is very CO2 positive…normal concrete, AAC, plaster, bricks…
The article didn’t mention that wind energy goes up with the CUBE of the velocity, so a 10 mph wind has 1000 times the energy of a 1 mph wind. That’s why building towers taller to get the stronger winds is critical.
Maybe the power plugs? Though just about anything beats the US power plugs, even the “safety retrofitted” non polarized EU plugs.
I’m curious why bolting together two half sections isn’t done. Is it structural? Or does transporting the width of a larger half section become just as problematic as the height of a full section currently is?
Thanks in advance for any knowledgeable answers.