When the first Bantam Tools’ Milling Machine landed, it put PCB prototyping at the forefront with a smooth software and hardware pipeline for spinning out circuit boards in a manner of minutes. Now the folks at Bantam Tools are back, putting those insights into a new machine that makes cutting aluminum a first class feature. While machine details are still sparse from their announcement page, knowing that Bantam Tools has spent a few years turning classrooms of students into hardware prototypes reassures us that we’re in good hands. Now let’s spill some beans on this beast.
A Big Shift in the Construction
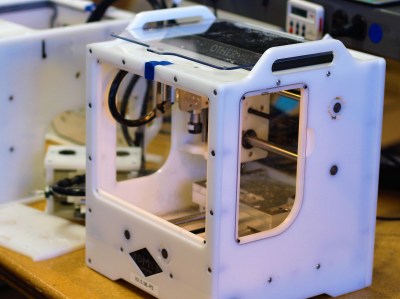
The heritage of this machine goes back a few years to the Other Machine Company’s design known as the Othermill. It was designed from a compact structure made from HDPE. Doing so made the machine fairly lightweight and easy to manufacture from large sheets with subtractive tooling, not to mention giving it an adorable A+ lunchbox aesthetic. In 2017 Bre Pettis — a founder of MakerBot and investor in Glowforge — bought the company, changing the name to Bantam Tools and shifting the focus to professional desktop milling.
Today’s offering — officially called the Bantam Tools Desktop Desktop CNC Milling Machine — grows the work region to a full 3″-by-9″-by-7″. The change calls for stiffer construction, and the design team has spared no expense at opting for thick steel linear motion components installed into a rugged aluminum frame. Just like the previous model, Bantam Tools’ new machine will get a full enclosure, making it classroom and office friendly.
Taking a closer peek at the construction itself, the machine frame borrows the T-slot technique from rapid prototyping with flat panels of laser cut components. However, unlike laser cut plastic joints, an aluminum frame should be more than enough to resist any stresses on these joints from everyday operation. This construction also has us suspecting that the machine is squared up and aligned with separate fixtures by the folks on the factory floor. In this setup the precision of the machine comes from the assembly process using references, rather than the precision of the machine that made the parts, which keeps the components simple and the fabrication expenses down without compromising on the machine’s ability to make precise parts.
Software Encapsulation
Let’s be frank. Cutting Aluminum is hard, especially at high speeds with tiny tools. Without some serious consideration of our cutting tool’s feeds and speeds, we can easily be left with a big pile of broken bits, a smaller pile of metal chips, and a never-to-be-finished part. But fear not. In the last few years, Bantam Tools took the complex precision process of milling two layer circuit boards and simplified it with a streamlined software workflow. How? Encapsulation.
By delegating more and more of the machine behaviors to software and accepting a variety of common file formats, the resulting machine could be used easily by both novices and experts. As more of us become generalists, encapsulation is key. It helps those of us who aren’t milling every minute of the day to be almost as capable at partmaking as those who mill day in and day out.
With the arrival of their new model, Bantam Tools promises a new set of software tools keen on doing the exact same thing. And features like their 2.5D Auto Cam, which turns 2D SVGs into toolpaths, speak exactly to this principle of user simplicity. I’m confident that their prior experience can take a number of key elements that make cutting aluminum so tricky and simplify them, hiding the complexities and providing a great overall user experience.
An even more Capable Garage, Office, and Hackerspace
As eager onlookers, we’ve had the pleasure of watching Bantam Tools grow their hardware capabilities from the early days of the MTM-Snap prototype, to hearing about the joys and woes of bootstrapping a hardware startup, to hearing early success stories as a PCB Prototyping machine, to their latest name change. I continue to have that same eagerness at seeing new design from a crew that packs giant dreams into tiny machines. But what do you think? Let us know in the comments.
What is this Encapsulation which is supposed to solve all problems? I was really curious, but the whole paragraph is a long-winded way of saying “they threw software at the problem”.
Sorry but this reads like a thinly disguised advertisement….
Yeah, I kept looking around for the “we got paid to review this” disclaimer.
Might as well throw in Software Defined Milling (TM) buzzword. :P
Where is the hack in this? Looks like a cleverly written ad posing as a Hackaday article. Shame.
Great Little Ad, That must be where the hack is hiding.
Zing!
A $200 annual subscription? I think not https://www.bantamtools.com/software-subscription
“Bantam Tools has spent a few years turning classrooms of students into hardware prototypes”
Whoa, that’s some serious Matrix / Supervillain stuff there. No wonder some people don’t like Bre Pettis.
This reeks of the Pettis mantra: Puffery > Utility
Damn, I thought this was going to be about Batman’s Tools! Should read article titles more slowly.
And I thought it was going to be an article about a sequel to a Bantam paperback novel from the famous author PCB Mill,
I thought this was going to be about the new Bantam paperback from the famous author PCB Mill.
but why would his pcp mill need a new sequin?
Well, Bantam did prototype the first Jeep…
http://www.m201.com/bantam.htm
Bre still thinks is 2009 😂😂 200 USD software subscription looool we have prusa and carbide/x-carve GTFO. The next version will probably implement some kind of rfid on each drillbit
I’m sure he’ll find someway to kill the company. Give him time.
Bacon.
(you asked me what I was thinking. Don’t judge!)
A lot of this article did read like an advertisement pulled straight from their “CNC landing page”. Then I saw the subscription model with the selling point “New features unlocked each month”. I feel like this is the exact opposite of what the culture is here but does seem to fall in line with most of what I’ve read about the individual mentioned in the second paragraph.
I like the compact construction. I have a mill with a similar work envelope with steel construction and it’s still pretty flexible during heavy cuts. You can certainly make up for that by taking lots of fast light cuts, if this thing has the feedrate to manage that. The table looks good. You can’t have too many t-slots.
But every single time I see a machine tool that uses end-supported round rail rather than either continuously supported round rail or contoured rail, I wonder why they chose that. The rigidity advantage of having supported ways is simply enormous.
I’d love to know more about the drive system and electronics.
“Let’s be frank. Cutting Aluminum is hard […]”
Afraid I disagree: aluminum is one of the easiest metals to machine. It’s about a third as hard as mild steel, and at least ten times softer than any of the tool steels. It work hardens enough to make good chips if your feed & speed are aggresssive enough, but is extremely forgiving of light cuts. Even if you overload the cutter, you’ll see the aluminum pressure-weld to the edge before things go really bad.
About the only metal friendlier is brass, and that costs about four times as aluminum per unit volume.
Stainless steel is hard to cut. It work hardens enough to cause problems if the cut is too light, the tool speed is wrong, or the cutting edge doesn’t have enough positive rake. It’s ductile before it hardens though, so the tool will dig in if the cut is too deep or the cutting edge has too much positive rake.
Yup, in generally any tool you can use to work wood you can use with aluminum. I have used tablesaes, circular saws, chop saws, and even jointers to work aluminum. The only thing I probably wouldn’t try is a planer. The drive rolls would never get a good enough grip.
Yeesh, there is some salt in this here comments section, haha. CNC folks be salty in general, but especially those that are still holding a grudge against ol’ Bre (rightly so or not).
Personally, I’m excited to see more about this machine and some video reviews! I’ve been in the market for an apartment-friendly(ish) enclosed CNC mill for some time, and I was about to pull the trigger on an Inventables Carvey right before they stopped making them. I want something that can do basic 2.5/3D carving of soft materials without having to spend countless hours fussing with garbage software and constant machine tweaking and maintenance. Its why I prefer my Prusa MK3 over my home-built Mendel i2 any day, and why I would prefer a unit like this over a Shapeoko/X-Carve (which are awesome, just not for my sort of workflow needs).
Mechanically, this looks like something I can rely on for getting jobs done. The software looks pretty slick, and it looks like a paid subscription is not required for basic machine control and G-code sending (would love to know an arbitrary host package like Candle or Mach3 could be used!). Some of the features they are included look super nice too – the workpiece locator, tool length sensor, geometry probe, T-slot bed with (what look to be) low-profile clamps, etc.
Its barely outside of my ideal price range, but the build quality looks outstanding and the “nice to have” features make it a little more palatable. The discount price of $3,600 feels pretty decent, all things considered, but $4,000 is really pushing it to the “investment” territory rather than “hobby tool” for me. I will definitely be considering it!
Seems sort of dumb considering the existence of a 6090CNC. By all means, spend your money on what suits your purpose, but there are cheaper and more capable machines available without the need of a year software subscription. Obviously my take on this isn’t as worded as yours, and maybe this comes down to the right tool for the job, but Bantam’s system seems to be a bit underwhelming for the cost.
IMO, those sorts of CNCs (6090s) are geared towards hardcore CNC enthusiasts who like to spend most of their time tinkering and hacking on the machine itself. The hardware is great, but the documentation, support, and software toolchains are horrific. Some people really enjoy compensating for those gaps by putting in many hours to figure out every single little aspect of the machine, but some people would prefer to spend that time on their project. In other words, some people are CNC enthusiasts and some people are enthusiastic about other things (designers, artists, inventors, etc) and just want to get projects done.
I agree that the cost feels slightly above my comfort zone, but the built-in features they seem to be showing look like they _almost_ justify it. Tool length sensor, workpiece locator, low-profile clamps, etc – other CNCs either break those out into paid add-ons or straight up just don’t support them. I also think that the (assumed) support, documentation quality, and simple, quality host software could help make up a lot of that cost too, if one values those sorts of things.
Also, it doesn’t look like a subscription is required to use the machine – the free “basic” level has all the features I’d be happy with (G-code sending and Fusion 360 support). The main benefits of the subscription seem to be more around support for people who don’t have the skill level needed to do certain tasks manually (like PCB milling or SVG carving). And I mean, $17/mo seems pretty dang reasonable for personalized support and turnkey solutions like that, given how hard CNC is for new users. Maybe consider a “tax” for not taking the time to figure out how to do all these things on your own (which it seems you can avoid by using the basic level if you really want).
> the free “basic” level has all the features I’d be happy with
It’s not free, you pay for it when buying the machine. Please don’t encourage this thought pattern.
> The main benefits of the subscription seem to be more around support for people who don’t have the skill level needed to do certain tasks manually
That’s untrue, given the company statement to date, you unlock ‘new features’ by contributing to this subscription model.
This HaD post is clearly just an advert, from a known scammer.
The bait and switch will not be forgotten, how does the old saying go, ‘fool me once…’?
The comment below by Bob sums up the situation to date:
> Yawn. Another $4K disposable toy. No coolant. Aluminum T-slot table? Get real. A small cast iron table is cheap. Too expensive for hobby. Not good enough for business.
I am not the person you were responding to but I think you went a little too negative here and that some of your logic is flawed.
OP has already stated that he likes the fact that this CNC represents a solution that does not require endless fiddling with free software and open-source solutions. I understand this isn’t your preference, but there is no need to ‘yuck’ his ‘yum’ in this way.
I also disagree with this point you make in your comment with regards to the non-subscription (base) tier software that comes with the machine:
>> the free “basic” level has all the features I’d be happy with
>It’s not free, you pay for it when buying the machine. Please don’t encourage this thought pattern.
This is the same “thought pattern” behind virtually all consumer electronic hardware. If you buy something that uses electronics, you are paying for the software that controls and interacts with those electronics. It’s the same “thought pattern” that leads one to expect an operating system to be loaded on a computer when they buy it from a store. Even if you bought a computer from an OEM who put strictly FOSS on it, you are paying in some part for the software they developed to automatically load that OS onto the machine. It’s why your motherboard ships with a CD including drivers and utilities. Even when you buy boards and cobble something together yourself, you are paying in some part for the firmware on those boards.
Sure, a competent hobbyist can build a machine more cheaply that does not use the software included with this machine, but there is a reason that no respectable professional machine shops use hobbyist CNC machines. It’s not only accuracy; it is peace of mind. For some people and applications, it will never be worth it to build it yourself. I love this site, but commenters here continually bemoan any company selling a machine that could be built at home despite the obvious value proposition intrinsic to a product like this: low mental overhead.
Nine times out of ten a company with a team of software and hardware engineers will produce something far superior and easy to use, and in less time than any hobbyist is going to make in his garage. The tradeoff is that it will usually cost much more than what the hobbyist invests. It’s up to each individual to decide how much work they are willing to put in versus how much work they want to pay someone else to do. It probably won’t be worth it to hardcore DIYers, but the people who decide to buy this machine acknowledge that fact and are probably attracted to this machine specifically because they don’t want to invest the overhead in OSS/Hardware.
What do I think about it? Before you accuse me of being a shill or scammer as you did the author of this article (you have the right idea, this reads like a lightly modified press release), I am not particularly interested in this machine but I like what it represents: a purpose-built device to let less technical users dip their toes into machining. It’s a bike with training wheels, and we shouldn’t make a habit of complaining about children who can’t ride two-wheelers. I am looking forward to seeing what people make with it. If they come out with a version that has better lead screws, repeatability closer to 10um, and a spindle capable of cutting tool steel, I might even decide to buy one.
Well, IF the hardware is any good, somebody will develop a new controller board for this ( or an adaptation kit for the already good boards out there ) , then use this machine with decent software and get free of their “subscription” fees. Without the risk of it getting bricked/unuseful
when they do not pay said fees.
Yawn. Another $4K disposable toy. No coolant. Aluminum T-slot table? Get real. A small cast iron table is cheap. Too expensive for hobby. Not good enough for business.
Damn, 4K is a bit steep when it looks like it was made with itself.
I said the same thing, 4K and for what? a BLDC driven spindle and a yearly subscription requirement for software?
I’m going to be the first to admit I don’t like Bre. His hypetrain tactics drive me up the wall (looking at you glowforge “3D laser printer”). Also I had sour interactions with him back when a bunch of us (including prusa) were hanging out in the reprap IRC.
That out of the way, this new bantam is only mildly better than the HDPE toy they were previously selling.
For less you can get a system from abdi automation. That has a cheap (but proper) spindle, fully supported prismatic linear rails, ballscrews, and a cast epoxy aggregate base. They do have exposed ways which isn’t great, but no different than this mess.
About the only thing going for bantaam is that they are enclosed, but definitely not worth the price to me.
I’m not involved with abdi, I just happened across them. I built my own CNC router and learned a lot but lamented the time.
Man I hate how they call it a printer. It doesn’t print! Printing is ADDING material. A laser REMOVES it. Just call it an engraver already. What a stupid marketing idea.
I completely agree. They just don’t want to be compared to all the other medium format CO2 cutters that can cut twice the size and are compatible with Lightburn for half the price.
Unsupported round linear rail construction? That’s a big nope for me. Round rails are bad enough when there are completely supported, but this…
I dont have a problem with Bre, he is a really funny guy, for instance he tried to tell us a 250$ made in china mill with a couple upgrades was going to sell for 3500 + more than my car note for a subscription in 2020
LOL good one, I see people cutting aluminum on Xcarve’s all the time and they have what a 30 inch travel and still manage to cost a thousand dollars less
No this guy again (Bre), c’mon.
HaD is becoming something strange these days, as somebody mentioned this looks like a paid/poor review and I really don’t like it. HaD should be more careful, don’t underestimate the intelligence of the readers.
Sorry Osgeld, it was not intended to be a reply to your comment.
yea the wordpress commenting system tends to get crap
On the upside, the comment section has been a lot of fun. I keep coming back to see if anyone has left any new jokes.
Plus, if Bre really did pay to have this written, he essentially paid for the opportunity to see people make fun of him, and THAT is icing on the cake.
I feel like there’s a lesson here: If you (attempt to) screw over your customer base, don’t go back into the same market with a different company.
When you can get a stiff 6040 with a 1.5kva spindle and fully supported rails for less than $1500, this thing which isn’t *that* much better than a 3018 which can be had for less than $400 makes absolutely no sense at $3500.
This. I had a ShapeOko 2 (sold it recently due to lack of time to use it) and if I ever get another CNC router it’ll be something significantly beefier than the ShapeOko and certainly won’t be this tiny little thing for $4k.
Tech specs are rater thin, and imperial only. Can’t do metric? Controller? Motor drivers? …
It’s really interesting to see this. When the OtherMill came out for $4000+ it triggered me to build my first pcb mill from lasercut 6mm alu with a standard work area of at least one euro-size board (160mmx100mm) for about $250. Apart from being forced to use hacked together software, the mill did everything I needed to make double sided PCBs.
Later, I designed a new one in 1/4” plywood, which was way simpler and can be cut at home on a K40 china laser and a small 3D printer for under $200 if you don’t count the PROXXON multitool I bought for it.
This new mill looks like all the old things in metal and I’m curious how still the Z-axis will hold up with the seemingly single LM12UU linear bearings. The magic must therefore be in the software.
Keep in mind, it’s a small company with only a few employees working and assembling straight in the San Francisco Bay Area (crazy rent and high salaries because of the cost of living) and that selling only really makes sense with an 8x markup because of all the running cost of such a company. They are not selling millions but rather hundreds or maybe a couple thousand. It’s different for something like a 3040 from China. One factory makes millions and resellers just stick a badge on it. They can sell for cheap. Bantam Tools does not work within the economy of scale.
If you’re a manufacturer who spends too much on rent and salaries due to cost of living and working in a luxurious location, maybe you should move your operation to a more reasonable location. #Just_CEO_talk
But if you need to impress local VCs to continue operation and do good networking… maybe it’s still worth is. I don’t know, I don’t work there. What you say makes sense to me, though.
not in a million years would i ever subscribe to anything
$200 / year buys 10 prototype runs of PCBs from China. That’s just the software cost to do PCBs. $3600 for an aluminium machine with missing specifications (load, deflection, runout etc) not mentioned or glossed is a stretch.
http://www.deskmaster.eu
Better machine for the same money!
We have one at work for small aluminium jobs and the spindle failed with under 200 hours of use. The spindle is not covered by warranty. The replacement costs 25% of the cost of the whole tool to get another unknown amount of life. The original base plate arrived damaged due to insufficient packaging and then got charged a hefty amount of import tax for the replacement. Overall would avoid.